
Tungaloy’s Guide to Drilling Fundamentals: Understanding Chip Characteristics and Hole Development
Welcome to our comprehensive guide on drilling fundamentals. In this article, we will meticulously examine chip characteristics and hole development, shedding light on critical aspects of drilling operations. Join us as we analyze the distinctions between 2-flute and single-flute drills, scrutinize the influence of cutting conditions on chip formation, and delve into the considerations surrounding hole expansion with drills. Prepare to deepen your understanding of drilling techniques as we embark on this insightful exploration together.
Table of Contents
1. 2-Flute Drill Chips
- Chip shape of 2-flute drills
- Effect of cutting conditions on chips
2. Single-Flute Drill Chips
- Chip shape of single-flute drills
- Effect of cutting conditions on chips
3. Hole Expansion
- Exploring techniques and precautions
Chip shape of 2-flute drills
During the drilling process with a 2-blade drill, chips of distinct shapes are produced at various stages: upon entry, within the middle section, and upon exit. At the entry point, chips form a “continuous spiral,” transitioning to “finely divided chips” within the middle, and culminating in “undivided elongated chips” at the exit. Additionally, umbrella-shaped chips are expelled as drilling progresses.
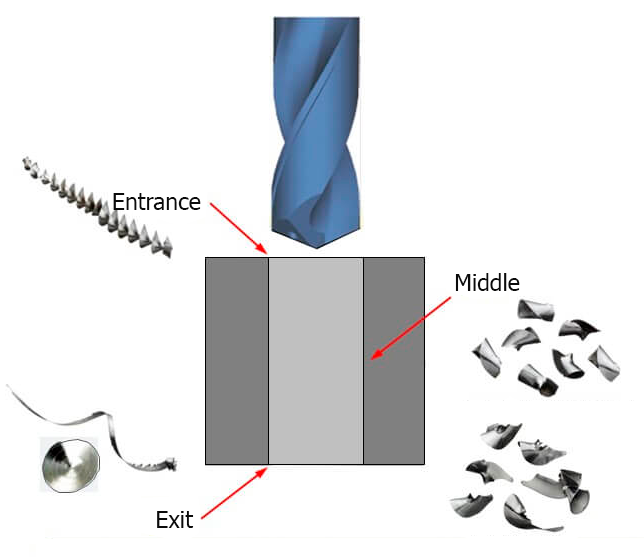
Impact of Cutting Conditions on Chip Formation
In the case of a two-flute drill, altering cutting parameters yields noticeable changes in chip characteristics. Elevating cutting speed results in thinner chips with a larger curl radius, while increasing the feed rate generates thicker chips. Optimal feed adjustment, tailored to prevent chip congestion, enhances chip fragmentation, facilitating smoother chip evacuation across a variety of work materials.
Cutting Speed increase | Chip thickness: thinner
Curl radius: larger |
Feed increase | Chip thickness: thicker |
Carbon steel, alloy steel, cast iron, low carbon steel (sticky material), stainless steel
Adjusting the feed rate plays a critical role in chip formation during drilling operations. Increasing the feed rate not only affects the thickness of the chips produced but also influences the ease of chip fragmentation. It’s important to note that this effect is contingent upon preventing chip clogging, as excessive buildup can impede the machining process. By strategically adjusting the feed rate to maintain an optimal balance, chips are more readily broken up, enhancing chip evacuation efficiency. This nuanced approach ensures smoother drilling operations and improves overall machining performance.
Tungaloy´s 2-Flutes Drills Lineup
DrillMeister / AddMeisterDrill
High productive head-changeable drill
ø4.0 – ø25.9 mm – (L/D): 1.5, 3, 3,5, 5, 6, 8, 12
SolidDrill (DSW, DSM)
Coated solid carbide drill for excellent stability
DSW: ø3 – ø12 mm – (L/D): 3, 5DSM: ø0.1 – ø3 mm – (L/D): 5 – 15
In this section, we’ll delve into the distinct characteristics of chips generated when drilling through holes using a single-flute drill, also known as an indexable drill.
Single-Flute Drill Tip Shape
Similar to two-flute drills, single-flute drills produce continuous spiral chips at the inlet and umbrella-shaped chips at the exit. However, in the middle section, the varying speeds between the central and outer circumferential sides lead to the formation of different chip shapes. Chips such as “continuous coiled chips” emerge from the central side, while “curled and divided chips” are ejected from the outer circumference. This variability is a defining feature of single-flute drill chips.
Center Blade Side:
Chips curl due to the difference in speed between the center and outer edges, forming a continuous coil without breaking up.
Peripheral Blade Side:
Chips curl and break up due to the difference in speed between the center and outer periphery.
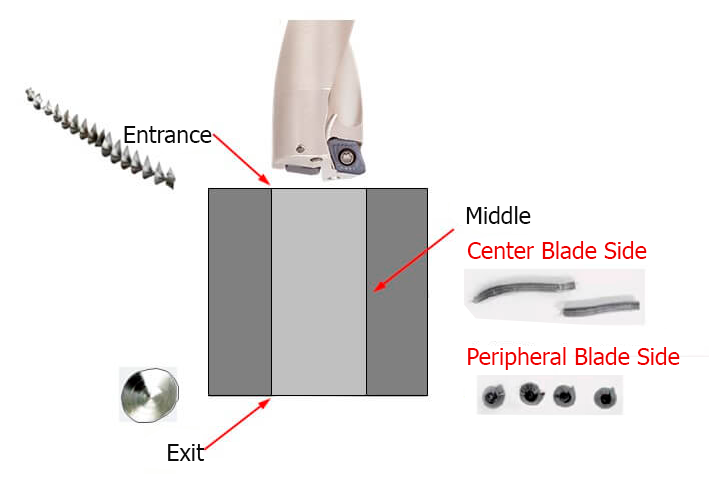
Effect of Cutting Conditions on Chips
Adjusting the cutting speed of a single-flute drill influences chip thickness and curl radius. Higher cutting speeds result in thinner chips with a larger curl radius, whereas increasing the feed rate yields thicker chips. Proper chip control varies depending on the workpiece material, necessitating tailored machining approaches for optimal results.
Cutting Speed increase | Chip thickness: thinner
Curl radius: increase |
Feed increase | Chip thickness: thicker |
For carbon steel, alloy steel, and cast iron
By increasing the feed rate and thickening the chips, the chips become easier to break up.
For low carbon steel/stainless steel
If the chip thickness is too thick, the strength of the chip will be high and it will be difficult to break it, so make sure the chip thickness is appropriate depending on the workpiece material.
For machines with covers, it is also effective to increase the rotation speed and use centrifugal force to separate the parts.
Tungaloy´s Single-Flute Drills Lineup
TungSix-Drill
Indexable drill with economical 6 cutting edges insert
ø20 – ø80 mm – (L/D): 2, 2.5, 3, 4
TungDrillTwisted
A wide range of indexable drills for various applications
ø12.5 – ø80 mm – (L/D): 2, 2.5, 3, 4, 5
The feasibility of hole drilling largely hinges on the presence of a breaker. Attempting to enlarge holes using a 2-blade drill without a breaker is discouraged due to challenges in chip control.
In contrast, single-flute drills are equipped with breakers, enabling effective chip disposal and facilitating hole enlargement based on cutting conditions.
NC lathes offer a similar capability to expand inner diameters akin to boring tools. By consolidating tools, machining efficiency can be significantly enhanced.”
2-Flute Drills:
Chip disposal is challenging without a breaker on the cutting edge. While machining may be feasible with a pre-cut hole and uniform thickness, it’s generally not recommended.
Single-Flute Drills:
Equipped with a breaker, single-flute drills enable effective chip disposal, contingent on cutting conditions. They can handle uneven thickness, such as cast holes, with ease.
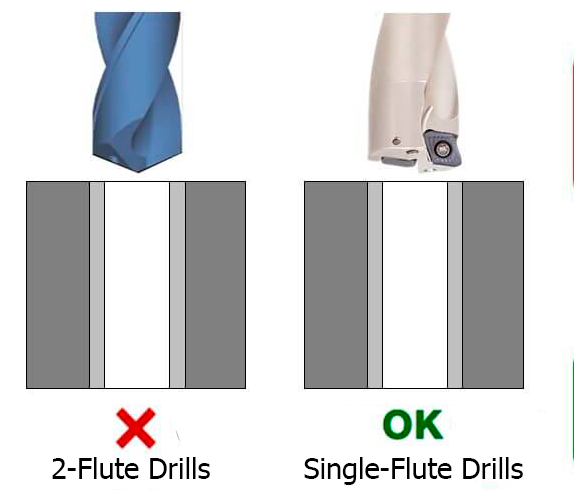