Overcoming Tool Wear Challenges in High-Resistance Material Milling
Background and Current Situation:
In milling difficult-to-cut materials and high hardness steels, end mills are a very common choice. However, these materials have high specific cutting resistance and elevated tool tip temperatures, which significantly impact tool life. Particularly when machining stainless steels, super alloys and high hardness steels, the tool tip temperature of end mills rises sharply, frequently causing premature wear and chipping. This leads to increased tool costs and higher machining expenses.
Challenges in the Field:
Under such conditions, many machining sites are facing the limits of tool life, requiring frequent tool changes. This results in decreased operational efficiency and increased production costs. For users who primarily select end mills, this issue is a daily headache, increasing the need to seek new solutions.
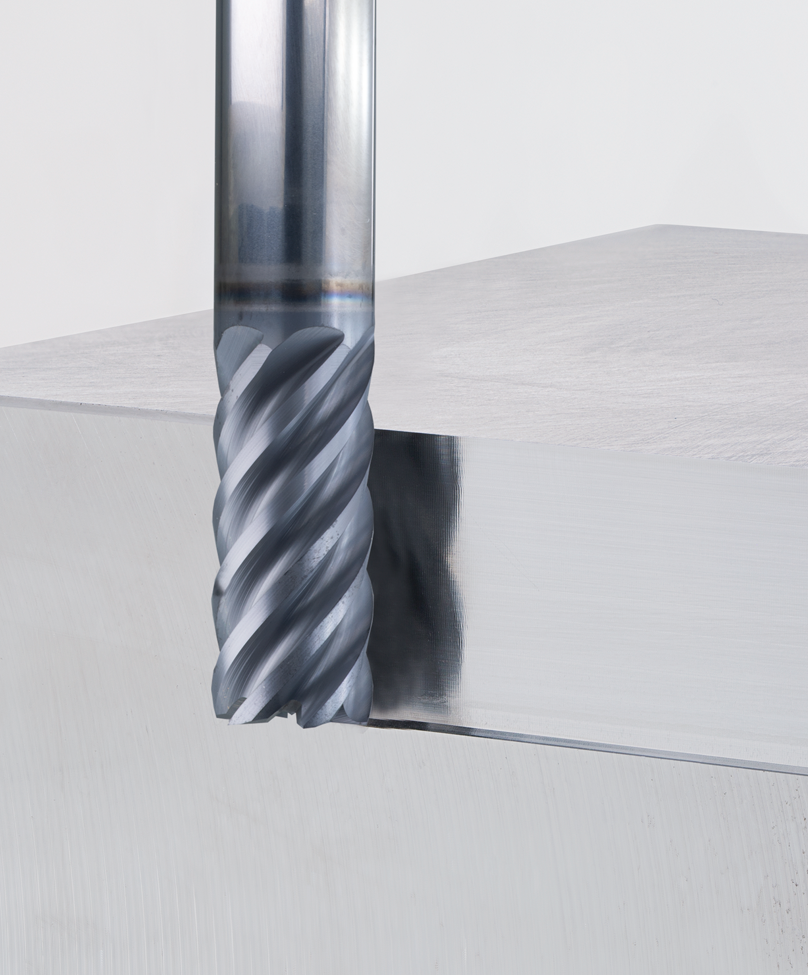
Innovative Technology of High Feed Cutters
Advantages and Theory of High Feed Blade Types:
High feed cutters have an advantage over end mills in rough machining of difficult-to-cut materials and high hardness steels. This advantage lies in the smallness of the cutting angle.
In the case of AddDoFeed, the cutting angle is 17°, which allows the cutting thickness to be reduced. When the cutting angle is 17°, the cutting thickness can be made approximately one-third as thin as that of an end mill with a 90° cutting angle. This helps suppress the rise in tool tip temperature and extend tool life.
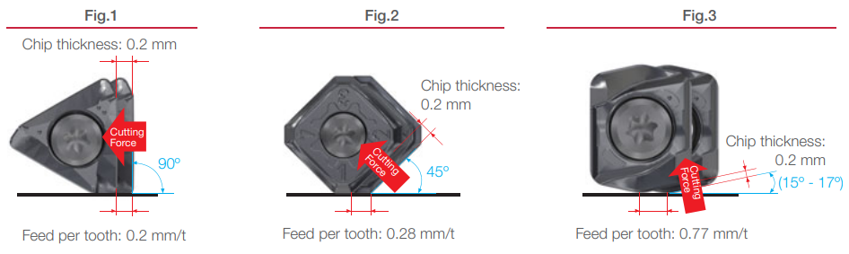
Challenges and Countermeasures of High Feed Cutters::
High feed cutters offer unique advantages but also come with disadvantages. While they allow for thin cutting thickness, achieving a large cutting depth (ap) like that of an end mill is challenging. Many users prioritize both tool life and machining efficiency, making this aspect crucial.
When machining difficult-to-cut materials and high hardness steels, end mills often chip due to high specific cutting resistance. This typically leads to reduced cutting depth (ap) or smaller cutting widths (ae) and lower feed rates, even with a larger ap.
For high feed cutters like AddDoFeed, which operate at small cutting depths, improving overall efficiency can be achieved by increasing the feed per tooth. By doing so while maintaining a shallow depth, users can attain machining efficiency equal to or greater than that of end mills.
Thus, AddDoFeed not only extends tool life but also enhances machining efficiency.
Extension of Tool Life:
Due to the small cutting angle, tool tip temperature is suppressed, resulting in less wear. Additionally, choosing to increase the feed rate beyond the current levels can reduce wear by decreasing the number of contacts between the cutting edge and the workpiece per pass.
Improvement of Machining Efficiency:
Even with a small cutting depth, increasing the feed rate allows machining efficiency to catch up, resulting in more efficient processing.
Cost Reduction:
By using high feed cutters, it is possible to reduce overall machining costs through “reduction of insert usage,” “decrease in tool costs by switching from solid tools to insert-type tools,” and “reduction in tool change frequency.”
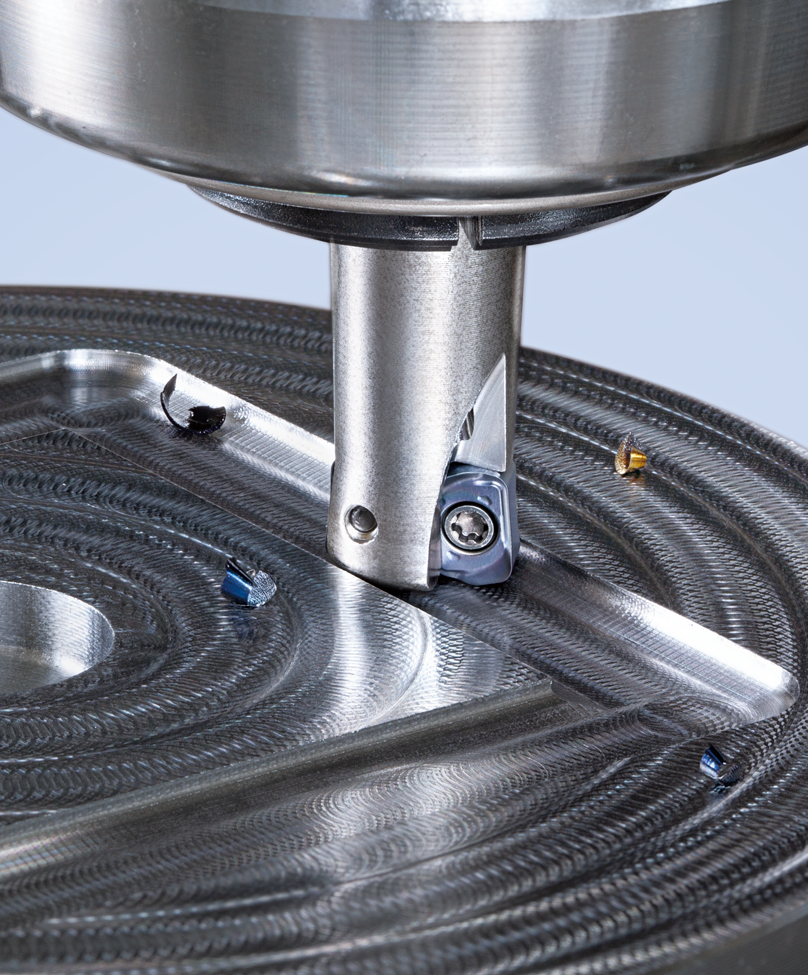
Advantages of AddDoFeed
Processing Efficiency with AddDoFeed
AddDoFeed’s unique 17° cutting angle minimizes chip thickness, reducing cutting resistance and improving efficiency. This design manages tool tip temperatures and wear, extending tool life for stable machining.
Proven Results and Tool Life
AddDoFeed optimizes cutting conditions and increases feed rates for challenging materials and high hardness steels. Available in tool diameters Φ8–16 mm with a 4-corner insert, it reduces tool usage and costs while minimizing frequent tool changes.
Visit Tungaloy’s eCat to explore the complete lineup of AddDoFeed
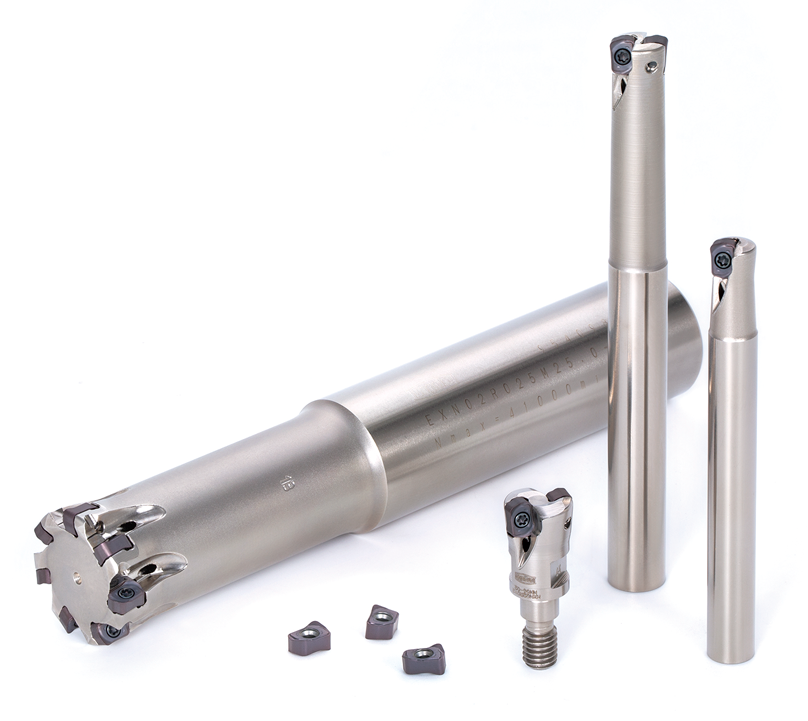
AddDoFeed Vs. Solid Endmill with 4 teeth for SUS304
2.7 times the machining efficiency
1.8 times the tool life
Tool cost estimation shows a 80% reduction in tool costs
Product Name | AddDoFeed | Φ10 Solid End Mill |
---|---|---|
Insert Price (¥) *Reference price listed on a certain e-commerce site |
10 | 30 |
Number of Corners | 4 | 1 |
Number of Cutting Edges | 4 | 4 |
Chip Removal Volume Until End of Life (cc) | 180 | 108 |
Running Tool Cost per Set (¥) *Excluding the cutter body |
100 | 300 |
Tool Cost per cc of Chip Removal ($/cc) | 0.06 | 0.28 |
AddDoFeed Success Reports from the Shop Floor
Successful Case in Turbine Blade Machining
High feed machining with AddDoFeed replaced traditional solid end mills, resulting in a 2.9 times increase in machining efficiency. Tool life was extended by 7.5 times, thanks to the excellent wear and heat resistance of AH8015 material and effective internal lubrication for tool tip cooling.
Successful Case in Inconel Shafts Machining
Traditionally used solid end mills. AddDoFeed generates thin chips with a small cutting angle, distributing cutting loads mainly to the tool tips. As a result, tool life doubled, and efficiency increased by 2.2 times.
Interested in How AddDoFeed Can Improve Your Processes?
Interact with our AddDoFeed chatbot to estimate the benefits of introducing AddDoFeed. By providing the parameters related to how your current end mill is being used our specialist chatbot will provide you with tailored recommendations and specific advantages.