Vibrationen beim Schaftfräsen verstehen
Das Schaftfräsen wird häufig zur Herstellung von Präzisionsbauteilen eingesetzt, doch Vibrationen während der Bearbeitung können zu unregelmäßigen Oberflächenmustern führen, die die Maßgenauigkeit und die Gesamtqualität beeinträchtigen. Dieser Artikel befasst sich mit praktischen Techniken zur Unterdrückung von Vibrationen und zur Verbesserung der Bearbeitungsstabilität.
Identifikation von Vibrationen bei der Bearbeitung
Bemerken Sie unregelmäßige Muster auf Ihren bearbeiteten Oberflächen? Das sind Anzeichen für eine Vibration, die sich negativ auf Oberflächengüte und Genauigkeit auswirkt.
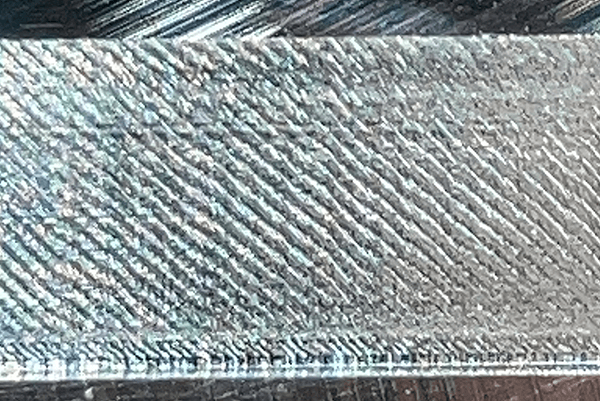
Was verursacht Vibrationen?
Die Hauptursache für Vibrationen ist die Werkzeugablenkung. Wie im Diagramm gezeigt, wird das Werkzeug bei aufgebrachter Kraft von einer Seite in die entgegengesetzte Richtung abgelenkt, wodurch Vibrationen entstehen, die zu Vibrationen führen.
Eine effektive Möglichkeit, Werkzeugvibrationen und Ablenkung zu reduzieren, ist die Verwendung von Schruppfräsern mit geringem Schneidwiderstand.
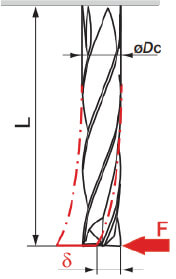
Schruppfräser vs. Schulterfräser: Vor- und Nachteile
Während Schruppfräser aufgrund ihrer gezahnten Schneidkanten die Vibrationen verringern, führen sie oft zu einer raueren Oberflächenqualität. Schulterfräser hingegen ermöglichen eine glattere Oberfläche, sind aber anfälliger für Vibrationen.
Schruppfräser | Schulterfräser | |
Schneidkanten |
gezahnte Schneidkanten
|
gerade Schneidkanten
|
Vibrationen | geringe Schwingungsneigung | Schwingungsneigung |
Anwendung | Schruppen | Schlichten |
Oberfläche |
Raue(Ra 1.5)
![]() |
Gut(Ra 0.3)
![]() |
Kombinierte Schaftfräser: Das Beste aus beiden Welten
Schruppfräser | Kombinationsfräser | Schulterfräser | |
Schneidkanten |
gezahnte Schneidkanten
|
gezahnte Schneidkanten+gerade Schneidkanten
|
gerade Schneidkanten
|
Vibrationen | geringe Schwingungsneigung | geringe Schwingungsneigung | Schwingungsneigung |
Anwendung | Schruppen | Schruppen+Schlichten | Schlichten |
Schnitttiefe |
Höher(ae=0.3D)
![]() |
Höher(ae=0.3D)
![]() |
geringe(ae=0.1D)
![]() |
Oberfläche |
Raue
(Ra 1.5)
![]() |
Gut
(Ra 0.3)
![]() |
Gut
(Ra 0.3)
![]() |
Kosten |
Hoch
|
Hoch
|
Mitte
|
Wie man mit einem Schulterfräser eine glatte Oberfläche ohne Vibrationen erzielen kann
Der Schlüssel liegt in der Werkzeugkonstruktion. Bei Kombinationsfräsern sind die geraden Schneidkanten leicht versetzt, was eine saubere Oberflächenqualität gewährleistet und gleichzeitig die Stabilität bewahrt.
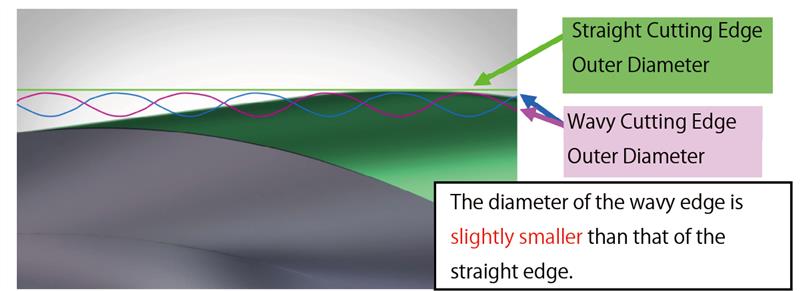
Praktisches Beispiel: Verbesserte Effizienz mit einem Kombischaftfräser
Traditionell erfordern Schruppen und Schlichten separate Werkzeuge. Durch den Wechsel zu einem Kombinationsfräser konnte jedoch die Bearbeitungszeit um 53 % reduziert werden, während eine ausgezeichnete Oberflächenqualität beibehalten wurde.
Werkstückmaterial: Titanlegierung, Werkzeug-Durchmesser: 16 mm, ap = 24 mm
Kombination: Vc= 45m/min fz= 0.03mm/Z ae= 6mm Konventionelle Bearbeitung: Schruppen (4z): Vc= 35m/min, fz= 0.03mm/Z, ae= 5.7mm Schlichten (6z): Vc= 45m/min, fz= 0.03mm/Z, ae= 0.3mm |
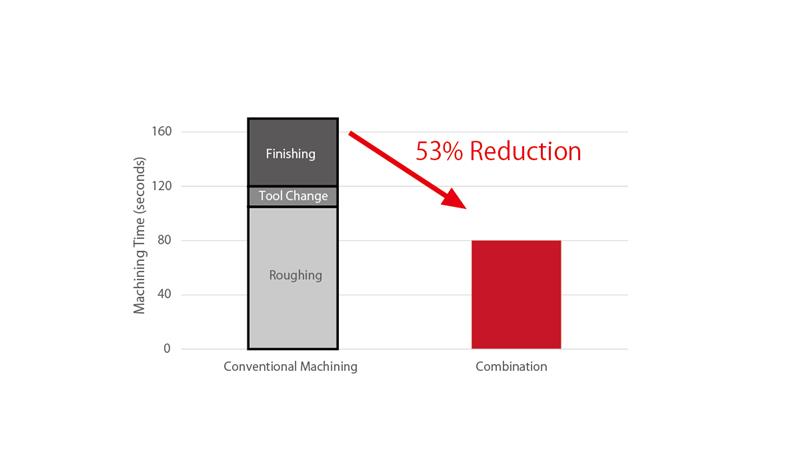
Im Vergleich zu einem Schulterfräser eines Wettbewerbers lieferte der Kombinationsfräser eine deutlich bessere Oberflächenrauheit (Ra, Rz) aufgrund geringerer Vibrationen.
Schulterfräser | Kombinierter Schaftfräser | |
Oberfläche |
Vibrationen
|
Gut
|
Oberflächenrauhigkeit |
Ra 1.394 μm
Rz 5.323 μm
![]() |
Ra 0.349 μm
Rz 1.947 μm
![]() |
Werkstückmaterial: S50C
Werkzeugdurchmesser: 6mm
ap= 6mm, Vc= 130m/min, fz= 0.03mm/Z, ae= 0.3mm
Benutzer-Feedback
Testbenutzer berichteten über die wichtigsten Vorteile:
- Reduzierte Werkzeugwechsel: „Früher haben wir getrennte Schrupp- und Schlichtwerkzeuge verwendet. Jetzt, mit einem Kombifräser, hat sich die Bearbeitungszeit erheblich verkürzt.“
- Verlängerte Standzeit: „Bei anderen Schulter- oder Radiusfräsern traten nach der Bearbeitung einiger Dutzend Teile Vibrationen und Gratbildung auf, sodass sie häufig ausgetauscht werden mussten. Dieses Werkzeug sorgt für Stabilität und verlängert die Standzeit.“
- Reibungslose Leistung: „Der Test verlief reibungslos ohne größere Probleme. Ich glaube, dass die Werkzeuglebensdauer die Erwartungen übertreffen wird.“
Fallstudie: FinishMeister in der Praxis
Herkömmliche Schaftfräser hatten beim Schruppen mit starken Vibrationen zu kämpfen, was die Produktivität einschränkte. Der FinishMeister-Schaftfräser mit seinem einzigartigen Schneidkanten-Design hat diese Herausforderung erfolgreich gemeistert, indem er:
✅ Ermöglicht 6× tiefere Schnitte
✅ Erhöhung der Vorschubgeschwindigkeit um das 1,5-fache
✅ Verdopplung der Anzahl der Schneidkanten
Das Ergebnis: Die Produktivität wurde im Vergleich zu herkömmlichen Methoden um das 14-fache gesteigert.
Wenn Sie mit Vibrationen kämpfen, probieren Sie einen Kombinationsfräser aus.
Der Wechsel zu einem Kombinationsfräser kann Schruppen und Schlichten in einem einzigen Werkzeug vereinen und so die Effizienz steigern und die Kosten senken.
Tungaloy bietet sowohl Vollhartmetall- als auch Wechselkopfversionen an – weitere Details finden Sie unter den untenstehenden Links!