Iwaki, Japan – December, 2024 – Tungaloy Corporation (President: Satoshi Kinoshita, Head Office: Iwaki City, Fukushima Prefecture) announces the expansion of its TungForce-Rec shoulder milling cutter series with the addition of new 18-size inserts. These inserts deliver enhanced cutting efficiency and stability through a reverse-positive design and V-bottom structure, ensuring durability, rigidity, and reduced cutting resistance. Combined with versatile breaker options, the expanded lineup offers reliable, cost-effective solutions for diverse machining applications.
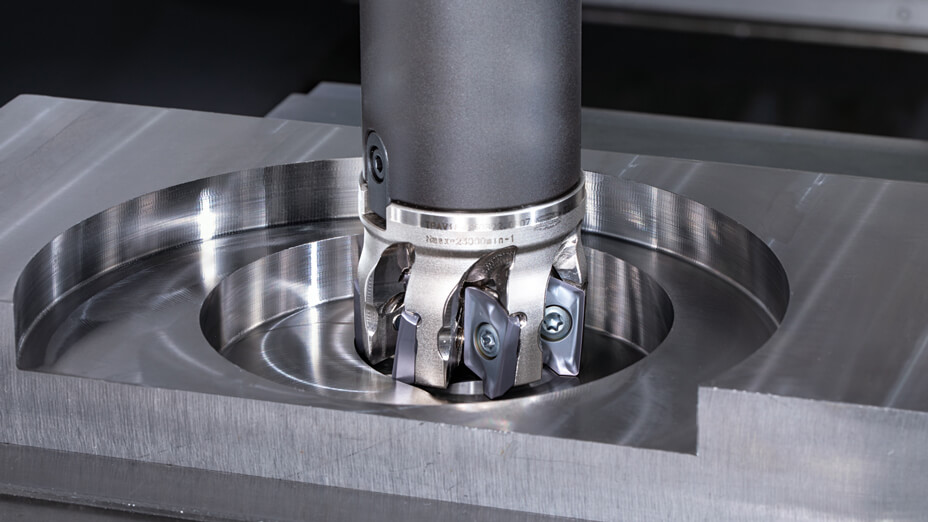
Challenges and Trends
In the field of shoulder milling, particularly in high-load machining involving black scales and cast surfaces, significant challenges arise. Conventional square shoulder end mills with two-corner inserts often lack sufficient cutting edge strength, limiting improvements in machining efficiency. Additionally, in the machining of large components or parts requiring high precision, issues such as tool deflection-induced chatter and cutting edge chipping occur frequently, posing ongoing challenges to machining stability. These Challenges and Market Conditions are common across a wide range of industries, including automotive parts, aerospace, molds, construction machinery, and industrial machinery components. There is a growing demand in the market for new solutions that can deliver higher machining efficiency and reliability, making the development of such products an urgent priority.
Product Overview
TungForce-Rec is a high-precision, high-efficiency cutter specifically designed for square shoulder milling. Featuring a unique V-shaped bottom insert and clamping mechanism, it delivers stable machining performance. It is versatile across various materials and industries. The wear-resistant coating ensures long tool life, contributing to improved productivity and cost savings.
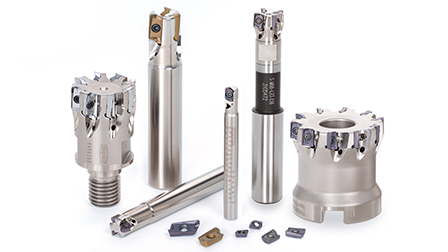
Benefits and Features
Feature 1: High Cutting Edge Strength
Reverse positive insert design ensures a larger insert cross-sectional area, achieving high resistance to chipping.
The large rake angle design reduces cutting resistance, enabling efficient machining.
Offers a choice between the versatile MM breaker and the cutting edge-reinforced MT breaker, providing optimal cutting performance tailored to specific applications.
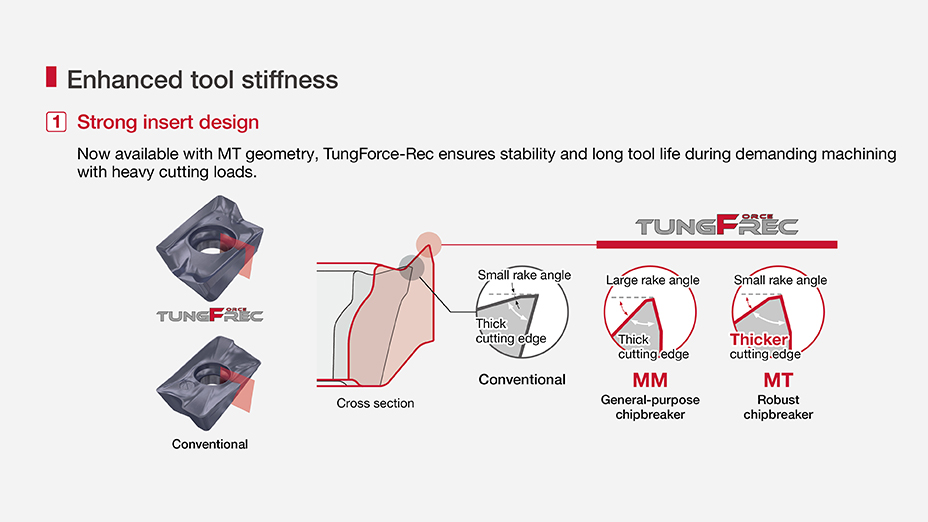
Feature 2: Improved Reliability
V-bottom insert design secures a larger core thickness and thicker back metal, enhancing the rigidity of the cutter body.
Utilizes larger screw sizes compared to competitors, strengthening the reliability of the insert clamping system. This ensures stable performance even under demanding machining conditions.
High-rigidity design minimizes vibration during machining, contributing to improved surface finish quality.
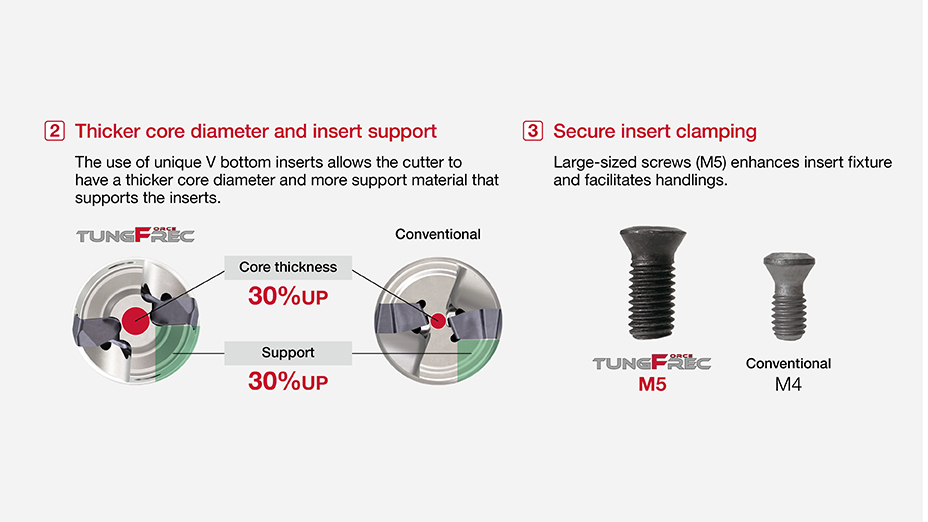
Cutting Performance
Tool Life Comparison: S55C / C55
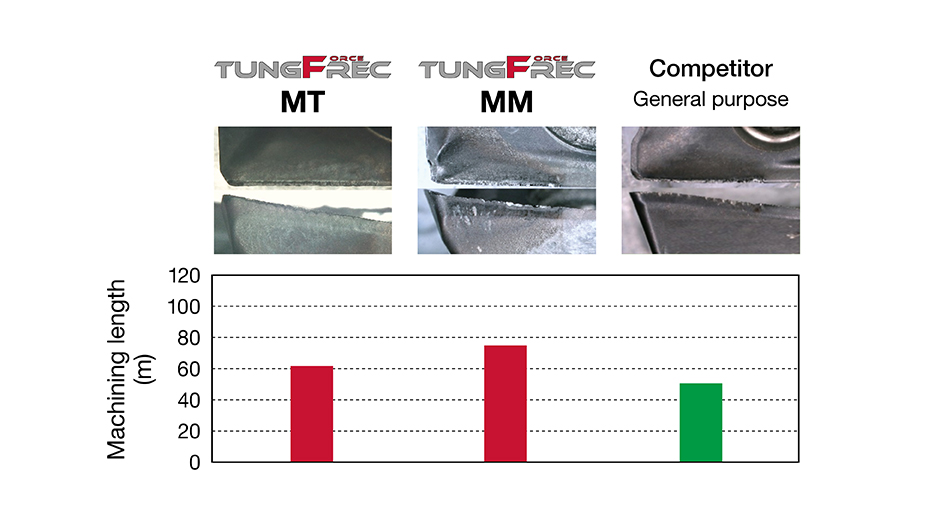
Cutter | TPAV18M050B22.0R05 (φ50 mm, z = 5) |
Insert | AVMT180708PDER-MM AH3225 / AVMT180708PDER-MT AH3225 |
Workpiece material | S55C / C55 |
Cutting speed / Feed per tooth | Vc = 160 m/min, fz = 0.2 mm/t |
Depth / Width of cut | ap = 2 mm, ae = 35 mm |
Coolant | Dry |
※Performed with only one insert on the cutter
MM chipbreaker provided 1.5x tool life increase, MT 1.2x.
Tool Life Comparison: Inconel 718 (38 HRC)
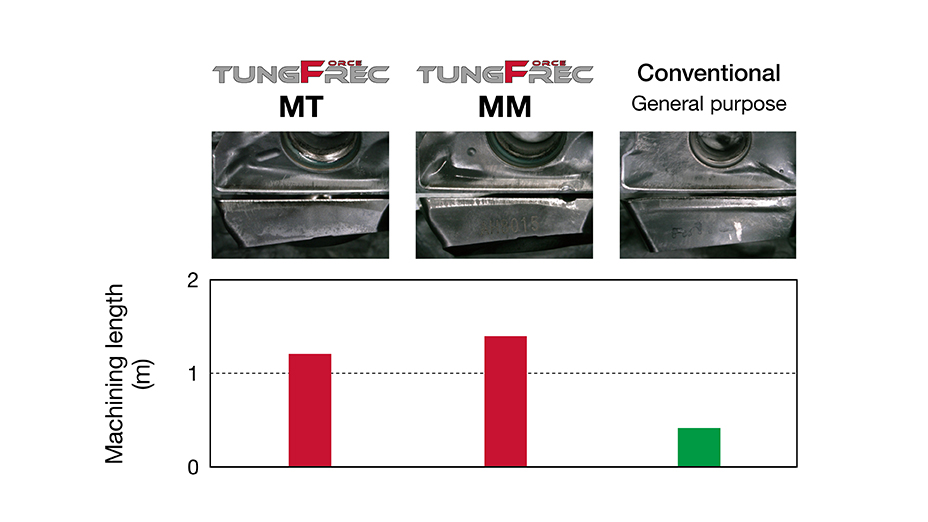
Cutter | TPAV18M050B22.0R05 (φ50 mm, z = 5) |
Insert | AVMT180708PDER-MM AH8015 / AVMT180708PDER-MT AH8015 |
Workpiece material | Inconel 718 (38 HRC) |
Cutting speed / Feed per tooth | Vc = 15 m/min, fz = 0.08 mm/t |
Depth / Width of cut | ap = 15 mm, ae = 10 mm |
Coolant | Wet (Performed with only one insert on the cutter) |
※Performed with only one insert on the cutter
MM chipbreaker provided 3.5x tool life increase, MT 3.0x.
Surface finishing
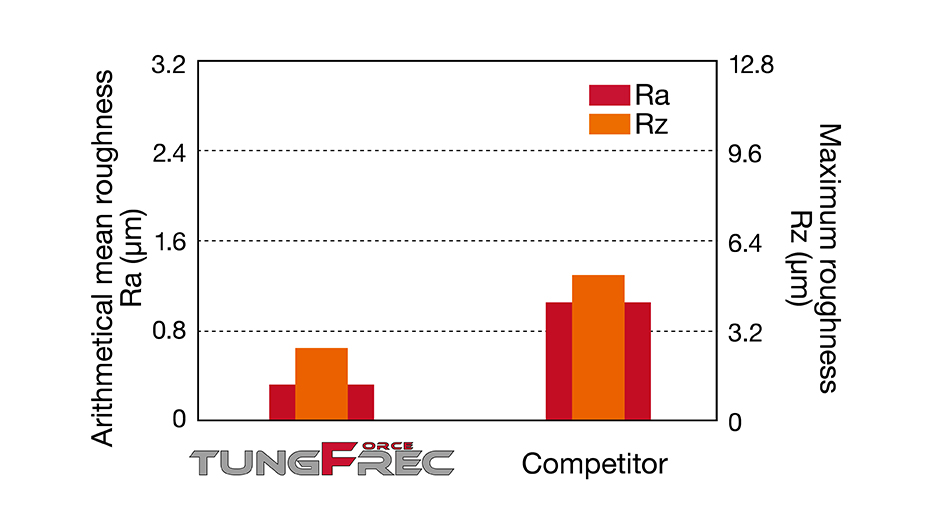
Face milling
Cutter | TPAV18M050B22.0R05 (φ50 mm, z = 5) |
Insert | AVMT180708PDER-MM AH3225 |
Workpiece material | S55C / C55 |
Cutting speed / Feed per tooth | Vc = 120 m/min, fz = 0.15 mm/t |
Depth / Width of cut | ap = 15 mm, ae = 20 mm |
Coolant | Dry |
Better surface quality vs the competitor.
Wall finishing
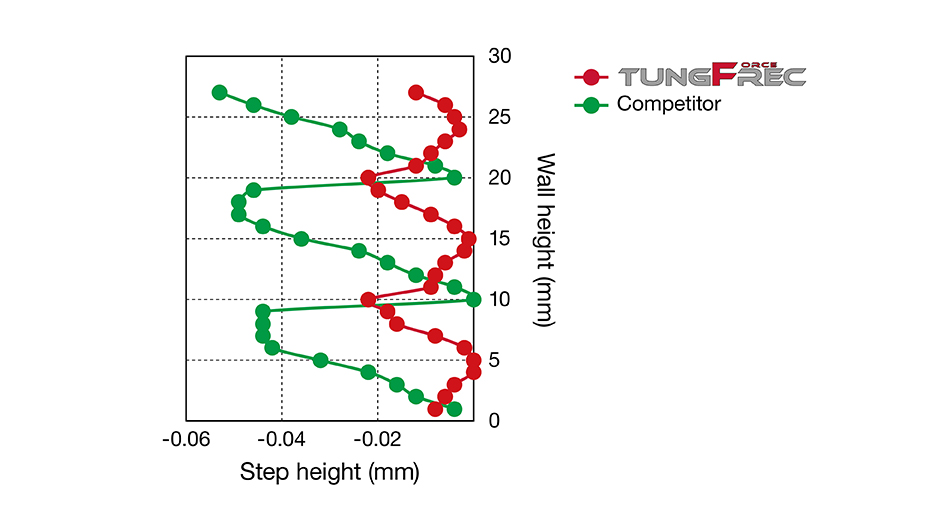
Shoulder milling
Cutter | TPAV18M050B22.0R05 (φ50 mm, z = 5) |
Insert | AVMT180708PDER-MM AH3225 |
Workpiece material | S55C / C55 |
Cutting speed / Feed per tooth | Vc = 120 m/min, fz = 0.15 mm/t |
Depth / Width of cut | ap = 15 mm, ae = 20 mm |
Coolant | Dry |
Better wall step than the competitor.
Success Stories
IMPROVED TOOL LIFE
The TungForceRec18 achieved stable machining without chipping thanks to its high edge strength.
Industry | Heavy |
Component | Construction machine part |
Material ISO code | P – Steel |
Work material | High alloyed steel |
Machine(Spindle type) | Vertical Machining Center Large (#50, HSK100) |
Tool family | Milling |
Tool category | Shoulder milling |
Product name | TungForce-Rec |
TSR No. | 5071M |
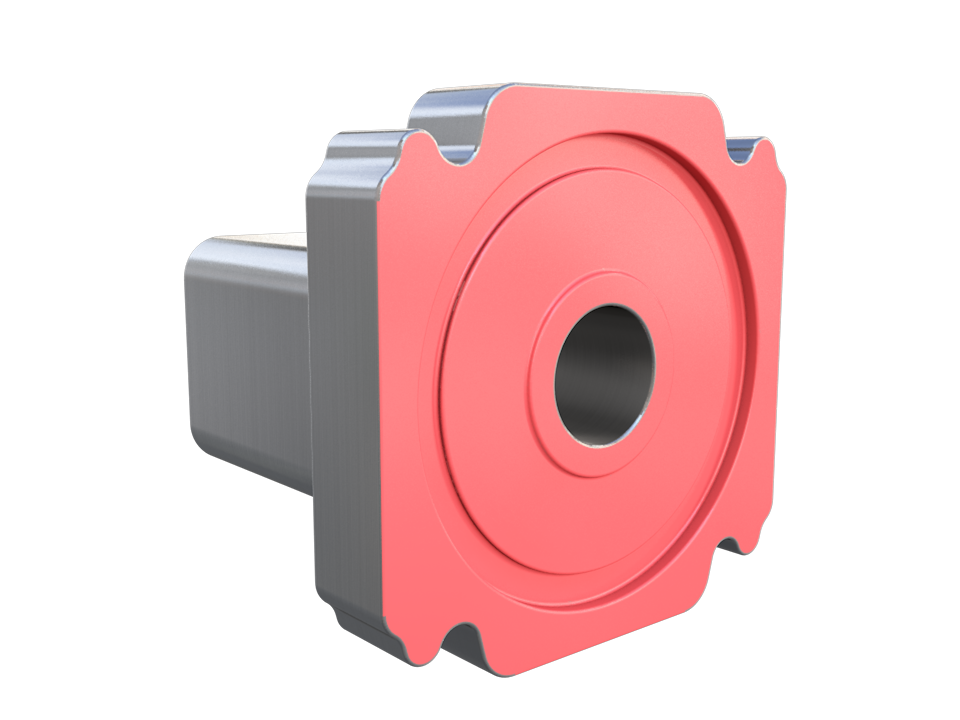
IMPROVED TOOL LIFE
The TungForceRec18, combined with the robust cutting edge and AH3225 grade, increased the number of machined parts from 7 to 10, achieving a 1.4 times improvement in tool life.
Industry | Engineering |
Component | Bracket |
Material ISO code | P – Steel |
Work material | SKD11 |
Machine(Spindle type) | Vertical Machining Center Middle(#40, HSK63) |
Tool family | Milling |
Tool category | Shoulder milling |
Product name | TungForce-Rec |
TSR No. | 5073M |
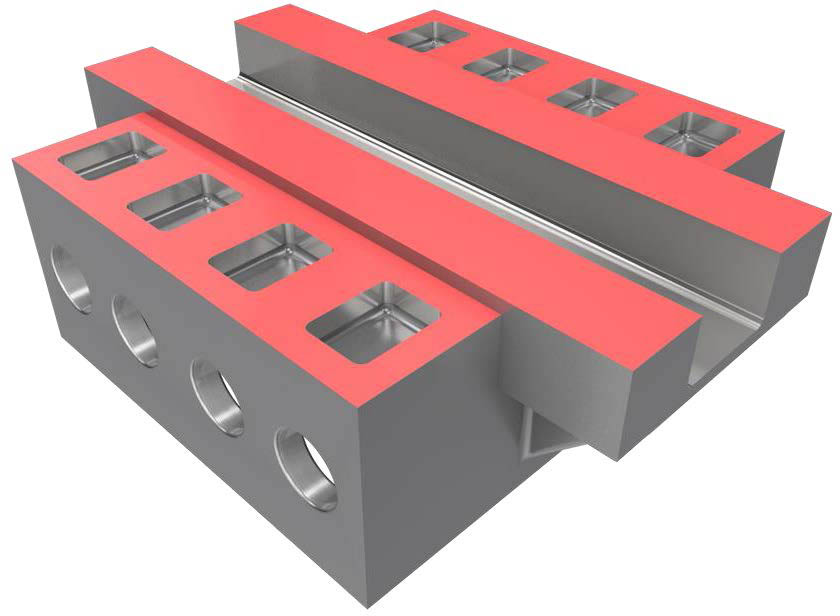
IMPROVED TOOL LIFE
The TungForceRec18, with its low-resistance MM breaker, suppressed chatter and achieved a 2.1 times improvement in machining efficiency through an increase in the number of teeth and feed rate.
Industry | Heavy |
Component | Casing |
Material ISO code | P – Steel |
Work material | SS400 |
Machine(Spindle type) | Vertical Machining Center Large(#50, HSK100) |
Tool family | Milling |
Tool category | Shoulder milling |
Product name | TungForce-Rec |
TSR No. | 5074M |
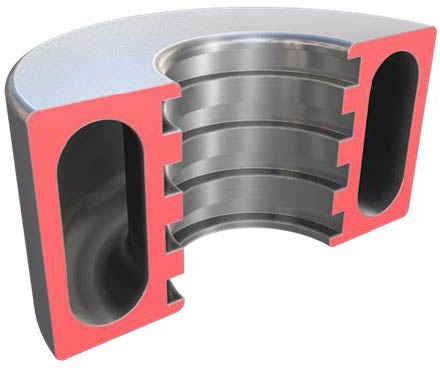
IMPROVED PRODUCTIVITY
The TungForceRec18, with more cutting edges compared to competitors, enabled stable machining without chatter.
As a result, a 1.3 times improvement in machining efficiency was achieved.
Industry | Heavy |
Component | Machine Base |
Material ISO code | P – Steel |
Work material | SS400 |
Machine(Spindle type) | Vertical Machining Center Large(#50, HSK100) |
Tool family | Milling |
Tool category | Helical interpolation |
Product name | TungForce-Rec |
TSR No. | 5076M |
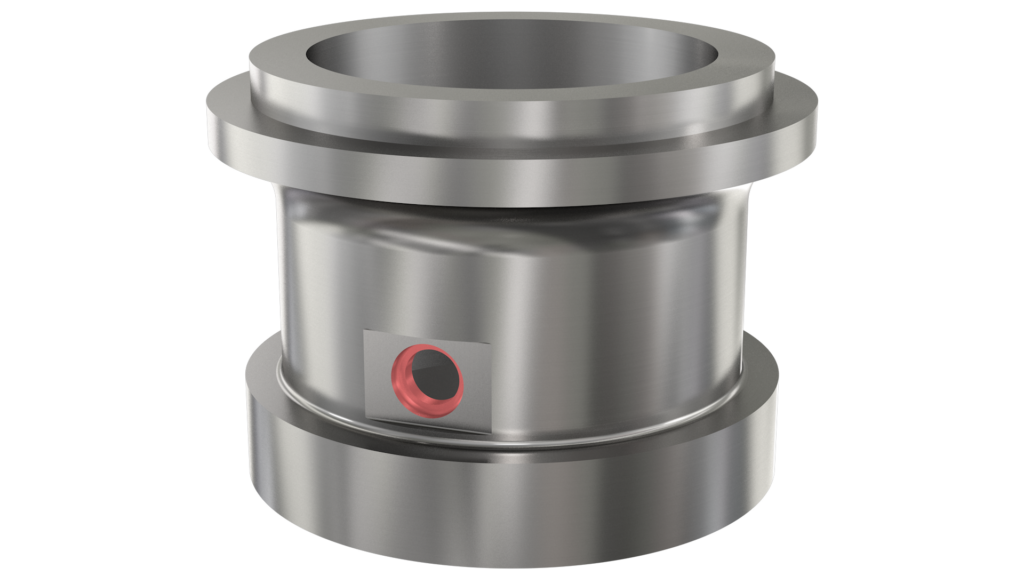