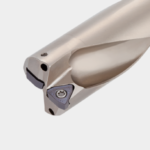
Gazdaságos fúrószerszám 6 vágóélű lapkákkal
6 élű lapkák kimagasló teljesítménnyel és költséghatékonysággal
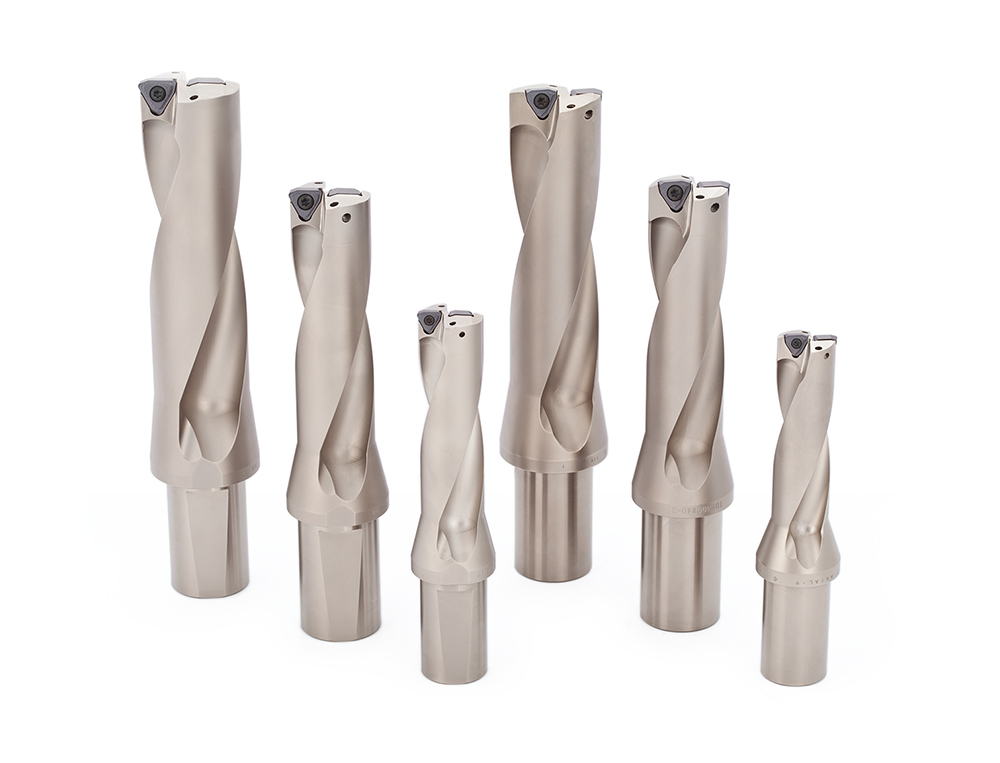
Alkalmazhatóság és jellemzők
Alkalmazhatóság
Jellemzők
1. Kétoldalas lapka 6 vágóéllel
• TungSixDrill is the first indexable drill in the world to adapt double-sided inserts with 6-cutting edges, reducing the insert consumption for the customers.
2. Low cutting force even with double sided insert
• The cutting forces are almost equal to competitors positive single sided inserts, especially at higher feed rates, thus complementing higher productivity.
3. Enhanced corner of central insert
• The central corner is strengthened by an obtuse angle relief thus increasing the corner strength and reliability.
4. TungDrillBig
Drill body with adjustable cartridge covers hole diameter ranges from: øDc: ø55 mm – ø80 mm, L/D = 2.5
-
Highly rigid body and optimized insert position
Provides well balanced cutting forces and stable machining conditions for highly accurate hole making.
-
Adjustable tool diameter
TungDrillBig features 5 drill body sizes that can accommodate a range of setting plates covering a diameter range from ø55 mm – ø80 mm.
-
Variety of design options
TungDrillTwisted and TungDrill-Six type cartridges can be affixed to the same body.
Lapkák és minőségek
Lapkák
Fő minőségek
AH7020
- Wear-resistant grade that enables high speed machining in steel and cast iron. Improved machining efficiency with no compromise on tool life.
AH7030
- First-choice grade in all material groups. Extremely fracture resistant, the grade provides predictability in unstable drilling applications that might, otherwise, induce edge chipping.
AH3135
- P30 – P40 / M30 – M40
-
High fracture resistance
-
Suitable for machining steel and stainless steel under general cutting conditions
AH9030
- P15 – P35 / K10 – K25
- High wear resistance
- Suitable for drilling steel and cast iron at high speed
AH6030
- M25 – M35 / S15 – S30
- High fracture resistance
- Suitable for drilling stainless steel and heat-resistant alloy under general cutting conditions
Fúrószárak és kapcsolódó szerszámok
Practical examples
Example #1
Automotive Industry
Part: | Connecting rod |
Material: | S55C / C55 |
Drill: | TDS200F25-2, øDc = 20 mm |
Insert: | WWMU05X205R-DJ |
Grade: | AH9030 |
Cutting conditions: | Vc = 200 (m/min) f = 0.15 (mm/rev) Vf = 477 (mm/min) H = 30 (mm) Coolant: Wet Machine: Vertical M/C, BT40 |
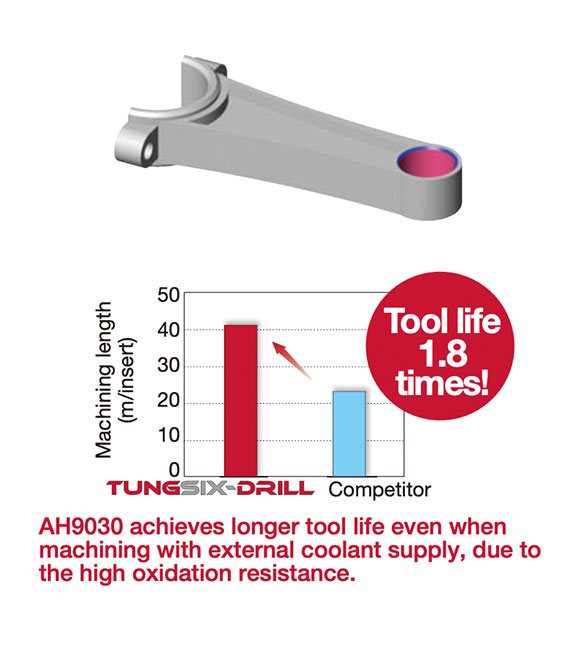
Example #2
General Engineering
Part: | Housing |
Material: | FCD450 / GGG45 |
Drill: | TDS420F40-2, øDc = 42 mm |
Insert: | WWMU11X512R-DJ |
Grade: | AH9030 |
Cutting conditions: | Vc = 120 (m/min) f = 0.2 (mm/rev) Vf = 180 (mm/min) H = 80 (mm) Coolant: Wet Machine: NC lathe |
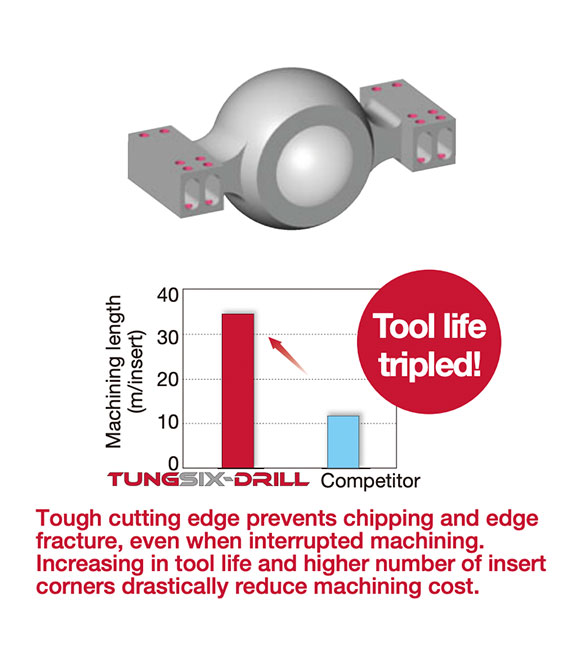
Example #3
Automotive Industry
Part: | Knuckle |
Material: | SCM440 / 42CrMo4 |
Drill: | TDS500F40-3, øDc = 50 mm |
Insert: | WWMU13X512R-DJ |
Grade: | AH9030 |
Cutting conditions: | Vc = 160 (m/min) f = 0.11 (mm/rev) Vf = 112 (mm/min) H = 80, 65 (mm) Coolant: Wet Machine: Horizontal M/C, BT50 |
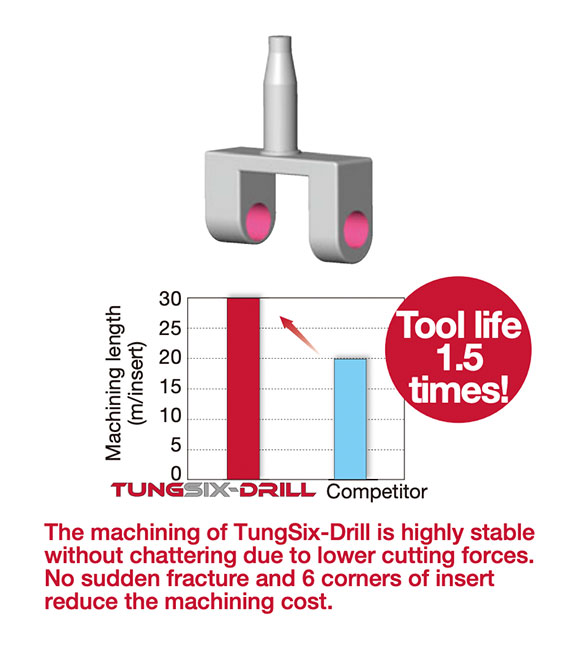
Standard cutting conditions
Recommended insert
ISO | Workpiece material | First choice | Wear resistance | Chip control |
---|---|---|---|---|
![]() |
Low carbon steel (C ≤ 0.3%) | DS AH7030 | DS AH7020 | DJ AH3135 |
Carbon steel (C > 0.3%), Low alloy steel, Alloy steel |
DJ AH7030 | DJ AH7020 | DJ AH3135 | |
Low alloy steel | DS AH7030 | DS AH7020 | DJ AH3135 | |
Alloy steel | DJ AH7030 | DJ AH7020 | DJ AH3135 | |
![]() |
Stainless steel | DS AH7030 | DS AH7020 | DJ AH3135 |
![]() |
Grey cast irons | DJ AH7030 | DJ AH7020 | – |
Ductile cast irons | DJ AH7020 | – | DJ AH7030 | |
![]() |
Aluminium alloy | DS AH7030 | – | – |
![]() |
Heat-resistant alloys | DS AH7020 | – | DJ AH7020 |
Titanium alloys | DS AH7030 | DS AH7020 | DJ AH3135 | |
![]() |
Hardened steel | DJ AH7020 | – | DJ AH7030 |
Standard cutting conditions
ISO | Workpiece material | Hardness | Cutting speed Vc (m/min) |
Series L/D |
Feed: f (mm/rev) | ||
---|---|---|---|---|---|---|---|
ø20 – ø27.5 | ø28 – ø38 | ø39 – ø54 | |||||
![]() |
Low carbon steels (C < 0.3) SS400, SM490, S25C, etc. st42-1, St52-3, C25, etc. |
– 200 HB | 160 – 320 | 2D, 3D | 0.04 – 0.1 | 0.04 – 0.1 | 0.04 – 0.1 |
4D | 0.04 – 0.1 | 0.04 – 0.1 | 0.04 – 0.1 | ||||
Carbon steels (C > 0.3) S45C, S55C, etc. C45, C55, etc. |
– 300 HB | 80 – 250 | 2D, 3D | 0.06 – 0.15 | 0.06 – 0.16 | 0.08 – 0.18 | |
4D | 0.06 – 0.15 | 0.06 – 0.15 | 0.06 – 0.17 | ||||
Low alloy steels SCM415, etc. |
– 200 HB | 160 – 250 | 2D, 3D | 0.06 – 0.12 | 0.06 – 0.12 | 0.06 – 0.14 | |
4D | 0.06 – 0.12 | 0.06 – 0.12 | 0.06 – 0.14 | ||||
Alloy steels SCM440, SCr420, etc. 42CrMo4, 20Cr4, etc. |
– 300 HB | 80 – 200 | 2D, 3D | 0.06 – 0.13 | 0.06 – 0.15 | 0.08 – 0.18 | |
4D | 0.06 – 0.1 | 0.06 – 0.12 | 0.08 – 0.14 | ||||
![]() |
Stainless steels (Austenitic) SUS304, SUS316, etc. X5CrNi18-9, X5CrNiMo17-12-2, etc. |
– 200 HB | 100 – 200 | 2D, 3D | 0.04 – 0.1 | 0.04 – 0.12 | 0.04 – 0.12 |
4D | 0.04 – 0.1 | 0.04 – 0.12 | 0.04 – 0.12 | ||||
Stainless steels (Martensitic and ferritic) SUS430, SUS416, etc. X6Cr17, X20Cr13, etc. |
– 200 HB | 100 – 220 | 2D, 3D | 0.04 – 0.1 | 0.04 – 0.12 | 0.04 – 0.12 | |
4D | 0.04 – 0.1 | 0.04 – 0.12 | 0.04 – 0.12 | ||||
Stainless steels (Precipitation hardening) SUS630, etc. X5CrNiCuNb16-4, etc. |
– | 80 – 120 | 2D, 3D | 0.04 – 0.08 | 0.04 – 0.1 | 0.06 – 0.1 | |
4D | 0.04 – 0.08 | 0.04 – 0.1 | 0.06 – 0.1 | ||||
![]() |
Grey cast irons FC250, etc., 250, etc. |
150 – 250 HB | 80 – 250 | 2D, 3D | 0.06 – 0.15 | 0.06 – 0.18 | 0.08 – 0.2 |
4D | 0.06 – 0.12 | 0.06 – 0.14 | 0.08 – 0.16 | ||||
Ductile cast irons FCD700, etc., 600-3, etc. |
150 – 250 HB | 80 – 200 | 2D, 3D | 0.06 – 0.15 | 0.06 – 0.18 | 0.08 – 0.2 | |
4D | 0.06 – 0.12 | 0.06 – 0.14 | 0.08 – 0.16 | ||||
![]() |
Aluminium alloy A2017, ADC12, etc. AlCu4SiMg, AlSi11Cu3, etc. |
– | 200 – 400 | 2D, 3D | 0.15 – 0.2 | 0.15 – 0.2 | 0.15 – 0.25 |
4D | 0.12 – 0.16 | 0.12 – 0.16 | 0.12 – 0.2 | ||||
![]() |
Heat-resistant alloys Inconel 718, etc. |
– 40 HRC | 20 – 60 | 2D, 3D | 0.04 – 0.1 | 0.04 – 0.1 | 0.04 – 0.1 |
4D | 0.04 – 0.1 | 0.04 – 0.1 | 0.04 – 0.1 | ||||
Titanium alloys Ti-6Al-4V, etc. |
– 40 HRC | 40 – 120 | 2D, 3D | 0.06 – 0.12 | 0.06 – 0.12 | 0.06 – 0.12 | |
4D | 0.06 – 0.1 | 0.06 – 0.1 | 0.06 – 0.1 | ||||
![]() |
Hardened steel | – 50 HRC | 40 – 100 | 2D, 3D | 0.04 – 0.1 | 0.04 – 0.1 | 0.04 – 0.1 |
4D | 0.04 – 0.08 | 0.04 – 0.08 | 0.04 – 0.08 |
For more information about this product, visit our online e-catalog or download the product report: