深孔钻削在航空航天、汽车及模具制造中的重要性
深孔钻削在航空航天、汽车及模具制造中发挥着关键作用,确保以下关键部件的精度和可靠性:
- 飞机起落架和发动机部件——需要极高的精度和表面光洁度,以确保安全性和性能。
- 汽车曲轴和喷油器体——要求精密钻孔,以保证耐用性和燃油效率。
- 液压系统和传动轴——需要光滑、圆整的孔,以实现最佳的流体流动和机械性能。
- 模具——涉及硬质材料钻孔,具有复杂几何形状、交叉孔和断续切削,用于冷却液通道加工。

在这些应用中实现精准高效的深孔钻削面临诸多挑战,包括排屑、孔偏斜以及孔精度的一致性。传统枪钻工艺常导致切屑堵塞、刀具过度磨损、加工成本高昂以及复杂的刀具重磨管理。东芝泰珂洛的可转位深孔钻DeepTriDrill正是为应对这些挑战并提升生产效率而设计。
DeepTriDrill:精密深孔钻削的解决方案
DeepTriDrill 凭借其提升钻孔精度、优化排屑表现及延长刀具寿命的先进技术特性,成为航空航天、汽车制造及模具加工领域的理想解决方案。
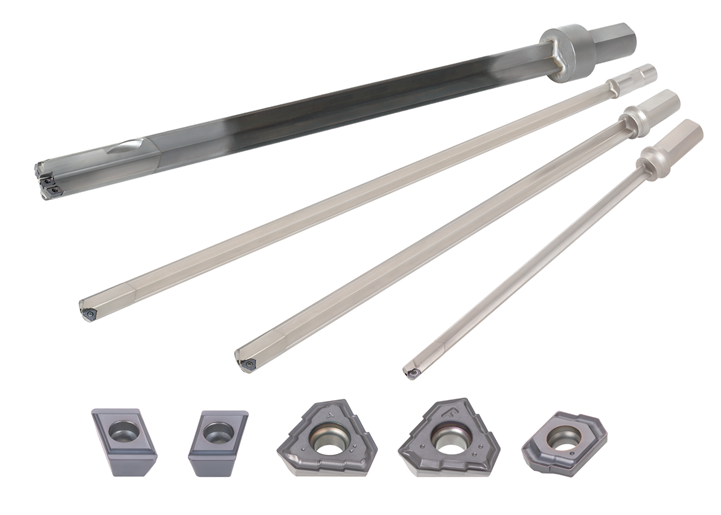
1. 断屑槽设计:优化排屑效率
深孔钻削的核心挑战在于高效排屑。若切屑控制不佳,易导致堵塞、主轴负荷增大及刀具寿命缩短。DeepTriDrill采用可转位刀片设计,其断屑槽结构能将切屑破碎为更小、更易处理的尺寸,从而有效防止堵塞并确保切削稳定性。这带来以下优势:
- 更低的切削力带来更高的加工稳定性及更长的刀具寿命
- 有效避免切屑堵塞,减少停机时间并提升生产效率
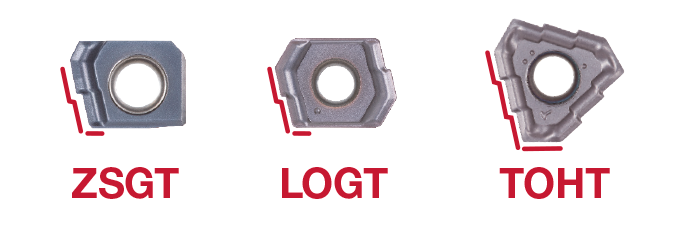
此外,每片TOHT刀片配备3个切削刃,且每个切削刃均带有修光刃,可提升表面光洁度与孔直线度。
2. 导向条设计:保障钻孔精度与稳定性
精准钻孔直线度与圆度控制对航空航天、汽车及模具高精密部件至关重要。DeepTriDrill配备高精度导向支撑条,在钻孔过程中提供刀具稳定支撑,有效抑制孔偏斜并提升加工精度,其核心优势包括:
- 优异的孔圆度和直线度,最大限度减少二次精加工需求。
- 即使在高进给和大深度下也能保持稳定导向。
- 提升表面质量,对高公差要求的应用至关重要。
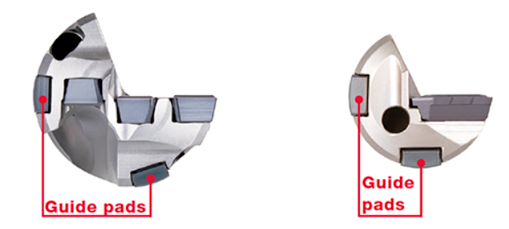
为进一步提升效率,所有导向条均设有两个可用侧面,并采用双倒角设计以实现平稳进入工件。每种规格的导向条均提供三种不同硬质合金材质可选,以适应各种材料和加工条件。
4. 前冷却液供给:提升刀具寿命与排屑性能
冷却液供给对深孔钻削至关重要,可防止过热、延长刀具寿命并保持高效排屑。 DeepTriDrill采用前冷却液孔设计,确保充分冷却、有效排屑和稳定性能。这带来以下优势:
- 延长刀具寿命,减少热量积聚。
- 改善排屑效果,实现连续钻孔。
- 增强钻孔稳定性,满足高精度应用需求。
5. H高性能刀片材质,适用于多种加工场景
DeepTriDrill 提供两种标准材质以满足广泛的加工需求:
- AH9130 –高耐磨性,专为钻削多种材料设计。
- AH725 – 在耐磨性和抗崩刃性之间取得良好平衡,适用于一般切削条件下的钢和不锈钢加工。
这些材质确保在各种应用中实现最佳性能,提供可靠的耐磨性和耐用性。
行业验证性能
DeepTriDrill 已在航空航天、汽车及模具制造领域成功应用,显著提升了加工效率、刀具寿命、孔加工精度并降低了刀具管理成本。以下是展示其对生产性能影响的实际案例:
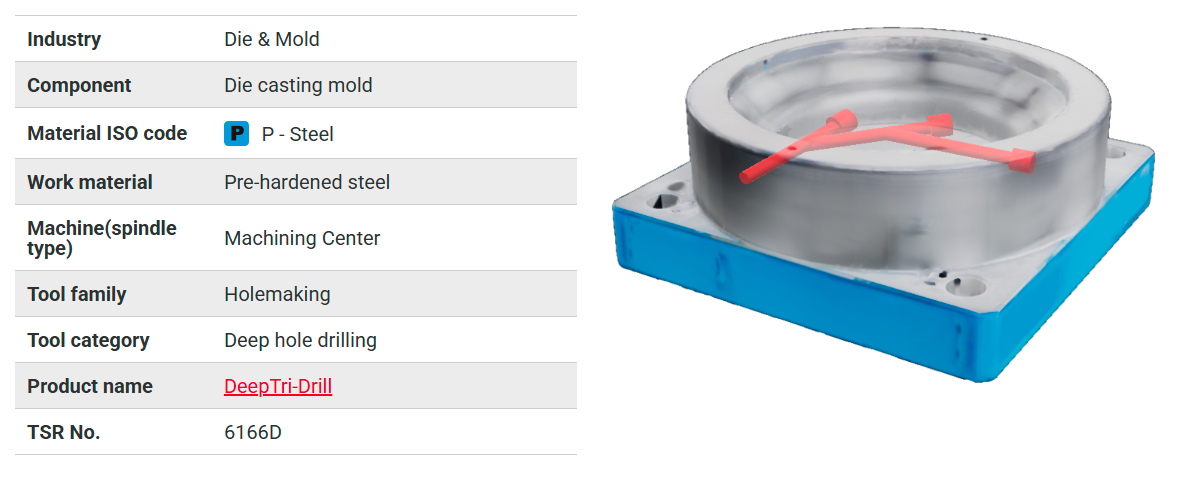
某客户采用配备双导向条的DeepTriDrill 替代传统扁钻,成功解决了交叉孔加工难题。此次升级使生产效率提升3.5倍,同时显著缩短了循环时间、降低了刀具破损率和设备停机率。
.通过优化切削参数(主轴转速1200 RPM 、切削速度54mm/min、进给速度 mm/min),DeepTriDrill展现出卓越的加工性能和工艺稳定性,成为压铸模具预硬钢材料加工的理想解决方案。
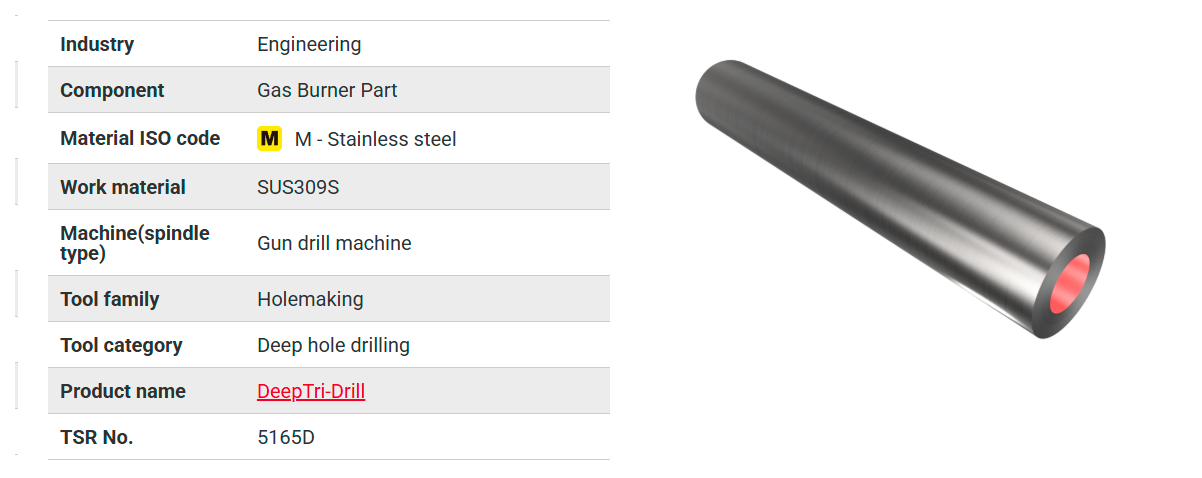
在SUS309S燃气燃烧器部件的加工中,用DeepTriDrill替代传统钎焊钻头使钻孔效率提升3倍。通过将进给量提高到 0.03 mm/rev,显著改善了进给速度,加工出清洁的孔、短小的切屑和极小的切削噪音。优化的排屑进一步提升了工艺稳定性和效率,实现了更安静、更清洁、更可靠的操作。
制造商选择DeepTriDrill的原因
随着对精度、效率和成本效益要求的不断提高,DeepTriDrill通过以下优势提供竞争优势:
✅ 优化的深孔钻削切屑控制
✅ 采用可更换刀片延长刀具寿命,降低加工成本
✅ 优异的圆度和直线度,减少返工并提升零件质量
随着航空航天、汽车和模具行业持续追求更高精度和生产力,DeepTriDrill是制造商提升深孔钻削工艺的理想解决方案。
立即体验 DeepTriDrill ,提升效率、精度并节省成本。