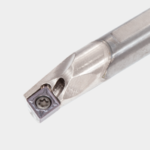
Highly rigid internal toolholder with excellent chip evacuation
Ideal tool geometry has been developed for excellent chip evacuation by extensive structural analysis simulation
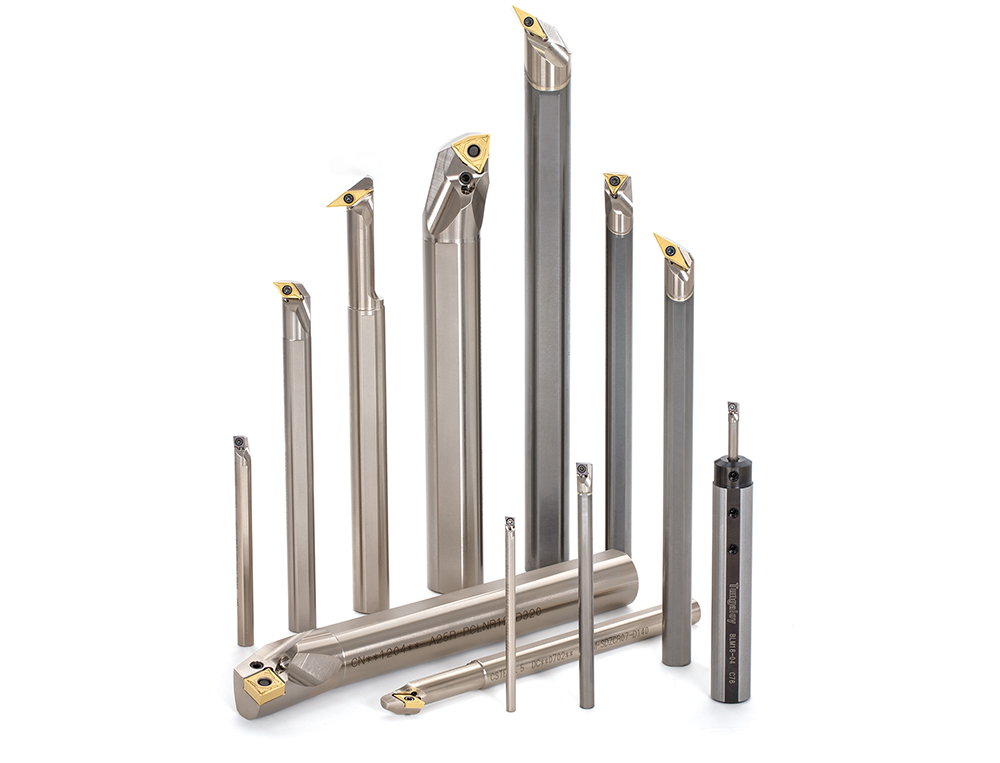
Applications & Features
Applications
Features
Engineered for tool strength and optimal chip evacuation
1. Tool body of special alloy steel, designed to reduce chatter
• Ensures superior surface finish quality over conventional ID turning tools.
• Improved tool life, efficiency, and economy.
2. Optimal holder design assures low cutting load and high performance in the smallest bore diameters
3. Easy to use
Marking specifications
Inserts & Grades
Inserts
Main Grades
T9215
- P10 – P20
- Well-balanced between wear and chipping resistance
- First choice for steel
- High versatility for a wide range of applications
T6130
- P15 – P30 / M15 – M30
- High wear resistance in cutting at medium to high speed
- First choice for stainless steel
AH8015
- M01 – M20 / S10 – S20
- Good balance between wear and fracture resistance
- First choice for machining heat-resistant alloy under general cutting conditions
Toolholders
Internal turning
StreamJetBar Toolholders
Highly rigid internal toolholder with excellent chip evacuation
Practical examples
Example #1
General Engineering
Part: | Machine parts |
Material: | S35C (C35) |
Toolholder: | E20S-SDUCR11-D270 |
Insert: | DCMT11T304-PS |
Grade: | T9215 |
Cutting conditions: | Vc = 70 – 160 (m/min) f = 0.12 – 0.2 (mm/rev) ap = 1.0 (mm) Coolant: Wet |
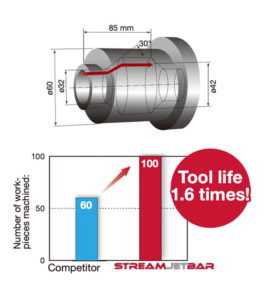
Example #2
Automotive Industry
Part: | Automotive parts |
Material: | S45C (C45) |
Toolholder: | A12M-SDUPL07-D180-P |
Insert: | DPMT070204-PS |
Grade: | T9215 |
Cutting conditions: | Vc = 130 (m/min) f = 0.1 (mm/rev) ap = 1.5 (mm) Coolant: Wet |
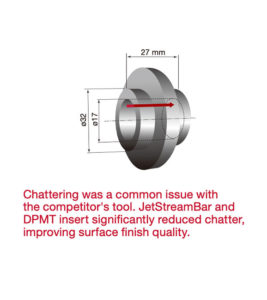
Standard cutting conditions
ISO | Operation | Work condition | Chip-breaker | Grade | Depth of cut ap (mm) |
Feed f (mm/rev) |
Cutting speed: Vc (m/min) | ||
---|---|---|---|---|---|---|---|---|---|
Low carbon steels, Alloy steels |
Medium carbon steels, Alloy steels |
High carbon steels, Alloy steels |
|||||||
![]() |
Precision finishing |
Continuous | 01 | NS9530 | 0.05 – 0.5 | 0.03 – 0.15 | 150 – 250 | 80 – 220 | 80 – 180 |
Light interrupted | 01 | NS9530 | 0.05 – 0.5 | 0.03 – 0.15 | 150 – 250 | 80 – 220 | 80 – 180 | ||
Finishing | Continuous | PSS | NS9530 | 0.1 – 0.5 | 0.05 – 0.3 | 150 – 250 | 80 – 220 | 80 – 180 | |
Light interrupted | PSS | NS9530 | 0.1 – 0.5 | 0.05 – 0.3 | 150 – 250 | 80 – 220 | 80 – 180 | ||
Heavy interrupted | PSS | NS9530 | 0.1 – 0.5 | 0.05 – 0.3 | 150 – 250 | 80 – 220 | 80 – 180 | ||
Finishing to light cutting |
Continuous | PS | NS9530 | 0.3 – 2.0 | 0.08 – 0.3 | 150 – 250 | 80 – 220 | 80 – 180 | |
Light interrupted | PS | NS9530 | 0.3 – 2.0 | 0.08 – 0.3 | 150 – 250 | 80 – 220 | 80 – 180 | ||
Heavy interrupted | PS | NS9530 | 0.3 – 2.0 | 0.08 – 0.3 | 150 – 250 | 80 – 220 | 80 – 180 | ||
Finishing to Medium cutting |
Continuous to Heavy interrupted |
PS | T9215 | 0.5 – 2.5 | 0.08 – 0.3 | 120 – 300 | 100 – 300 | 80 – 250 | |
PS | T9125 | 0.5 – 2.5 | 0.08 – 0.3 | 120 – 250 | 80 – 180 | 80 – 120 | |||
Medium cutting | Continuous to Heavy interrupted |
PM | T9215 | 1.0 – 3.0 | 0.15 – 0.3 | 120 – 300 | 100 – 300 | 80 – 250 | |
PM | T9125 | 1.0 – 3.0 | 0.15 – 0.3 | 120 – 250 | 80 – 180 | 80 – 120 |
Low carbon steels, Alloy steels: S10C, SCM415, SS400, SCr420H, etc. C10, 18CrMo4, E275A, 20Cr4, etc. Medium carbon steels, Alloy steels: S45C, SCM440, etc. C45, 42CrMo4, etc. Hi carbon steels, Alloy steels: SNCM439, etc. 41CrNiMo2, etc.
ISO | Operation | Work condition | Chip-breaker | Grade | Depth of cut ap (mm) |
Feed f (mm/rev) |
Cutting speed: Vc (m/min) |
---|---|---|---|---|---|---|---|
![]() |
Precision finishing | Continuous | Whh | GH330 | 0.05 – 2.0 | 0.03 – 0.2 | 100 – 150 |
Finishing | Continuous | PSF | AH725 | 0.1 – 0.5 | 0.05 – 0.3 | 50 – 150 | |
Light interrupted | PSF | AH725 | 0.1 – 0.5 | 0.05 – 0.3 | 50 – 150 | ||
Heavy interrupted | PSF | AH725 | 0.1 – 0.5 | 0.05 – 0.3 | 50 – 120 | ||
Finishing to light cutting |
Continuous | PSS | AH630 | 0.3 – 2.0 | 0.08 – 0.3 | 90 – 190 | |
Light interrupted | PSS | AH630 | 0.3 – 2.0 | 0.08 – 0.3 | 90 – 190 | ||
Heavy interrupted | PSS | AH630 | 0.3 – 2.0 | 0.08 – 0.3 | 90 – 190 | ||
Finishing to medium cutting |
Continuous | PS | T6130 | 0.5 – 2.5 | 0.08 – 0.3 | 100 – 200 | |
Light interrupted | PS | AH630 | 0.5 – 2.5 | 0.08 – 0.3 | 90 – 190 | ||
Heavy interrupted | PS | AH630 | 0.5 – 2.5 | 0.08 – 0.3 | 90 – 190 | ||
Medium cutting | Continuous | PM | T6130 | 1.0 – 3.0* | 0.15 – 0.3 | 90 – 190 | |
Light interrupted | PM | AH630 | 1.0 – 3.0* | 0.15 – 0.3 | 90 – 190 | ||
Heavy interrupted | PM | AH630 | 1.0 – 3.0* | 0.15 – 0.3 | 90 – 190 |
* For CCMT0602 and DCMT0702 type inserts, a p = 0.5 – 2.5
Stainless steels: SUS304, SUS316, etc. X5CrNi18-9, X5CrNiMo17-12-3, etc.
ISO | Operation | Work condition | Chip-breaker | Grade | Depth of cut ap (mm) |
Feed f (mm/rev) |
Cutting speed: Vc (m/min) | |
---|---|---|---|---|---|---|---|---|
Grey cast irons | Ductile cast irons | |||||||
![]() |
Finishing | Continuous | CM | T515 | 0.05 – 2.0 | 0.05 – 0.3 | 150 – 700 | 150 – 300 |
Heavy interrupted | CM | T515 | 0.05 – 2.0 | 0.05 – 0.3 | 100 – 200 | 100 – 200 | ||
Medium cutting | Light interrupted | CM | T515 | 0.05 – 2.0 | 0.05 – 0.3 | 100 – 300 | 100 – 250 |
Grey cast irons: FC250, etc. 250, etc.
Ductile cast irons: FCD450, etc. 450-10S, etc.
ISO | Operation | Work condition | Chip-breaker | Grade | Depth of cut ap (mm) |
Feed f (mm/rev) |
Cutting speed: Vc (m/min) | |
---|---|---|---|---|---|---|---|---|
Titanium alloys | Ni-base alloys | |||||||
![]() |
Finishing | Continuous | PSS | AH8015 | 0.3 – 2.0 | 0.02 – 0.3 | 20 – 150 | 20 – 100 |
Light interrupted | PSS | AH8015 | 0.3 – 2.0 | 0.02 – 0.3 | 20 – 150 | 20 – 100 | ||
Finishing to medium cutting |
Continuous | PS | AH8015 | 0.5 – 2.5 | 0.02 – 0.3 | 20 – 150 | 20 – 100 | |
Light interrupted | PS | AH8015 | 0.5 – 2.5 | 0.02 – 0.3 | 20 – 150 | 20 – 100 |
Ni-base alloys: INCONEL718 etc.
Titanium alloys: Ti – 6Al – 4V etc.
For more information about this product, visit our online e-catalog or download the product report: