
The Limits of Slot Milling with End Mills
Slot milling with end mills is commonly performed in many workshops. However, due to limitations in tool diameter and rigidity, there are often challenges in achieving machining efficiency and accuracy. Especially with small-diameter end mills, issues such as chatter due to insufficient tool rigidity and short tool life are problematic.
T-slot milling offers a new solution to these challenges. This article details the advantages of T-slot milling over end mills and the secrets to its high efficiency.
Introduction to T-Slot Milling: The New Standard for High-Efficiency Machining
T-slot milling is gaining attention as a high-efficiency slot machining method that can replace end mills. End mills are limited by tool diameter, leading to rigidity issues with small diameter tools. In contrast, T-slot milling overcomes these limitations, offering higher efficiency and longer tool life. Let’s explore why T-slot milling is highly efficient.
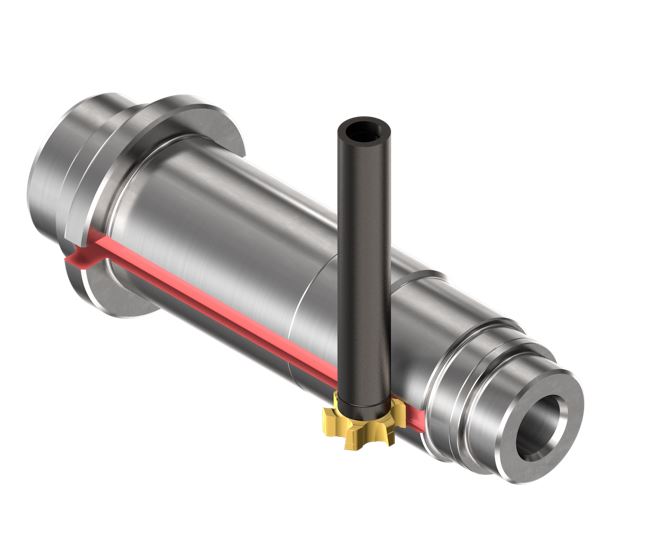
Reasons for High Efficiency
1. Fewer Tool Diameter Limitations
- End mills are limited by tool diameter depending on the slot width, particularly with small-diameter tools, which have low rigidity and restricted machining efficiency.
- T-slot tools are not constrained by slot width, allowing for more flexibility in choosing tool diameter and increasing the number of cutting edges, thereby improving machining efficiency. Additionally, increasing the number of cutting edges contributes to longer tool life.
2. Ability to Use Larger Diameter Shanks
- In T-slot milling, the tool is positioned laterally to the slot, allowing the use of larger diameter shanks (※ requires a change in tool approach direction).
- This allows for the use of larger diameter shanks, enhancing tool rigidity, which suppresses chatter and allows for higher feed rates.
3. Thinner Chip Thickness
-
- End mills have a cutting width equal to the tool diameter (ae/DC=1), making the chip thickness equal to the feed per tooth.
- In T-slot milling, the cutting width ae tends to be smaller compared to the tool diameter DC, resulting in a thinner chip thickness (ae/DC<<1).
- Thinner chip thickness allows for higher feed per tooth, improving machining efficiency.
Potential of T-Slot Heads for Achieving Maximum Efficiency in Slot Milling
Advantages of TungMeister
TungMeister exhibits superior performance in T-slot milling in the following aspects.
1. Economic Benefits of Replaceable Head T-Slot Heads
- Compared to traditional solid carbide T-slot cutters or carbide brazed T-slot cutters, replaceable head T-slot heads require a minimal amount of carbide, reducing tool costs.
- Additionally, regrinding management is unnecessary, allowing for simpler tool management.
2. High Versatility with a Wide Range of Shank Options
- TungMeister offers a wide range of shanks in various diameters and lengths, providing flexible specifications to match machining conditions.
- Shank materials include the most common steel shanks, high-rigidity carbide shanks, and vibration-damping tungsten shanks.
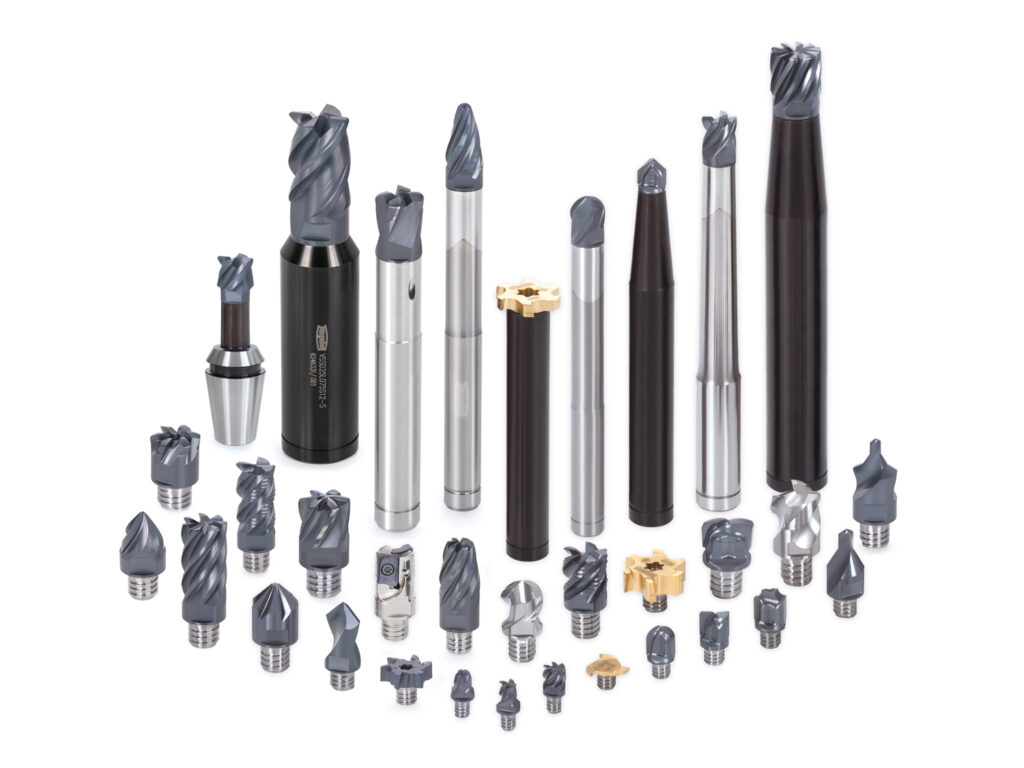
Case Study: Utilizing TungMeister T-Slot Heads
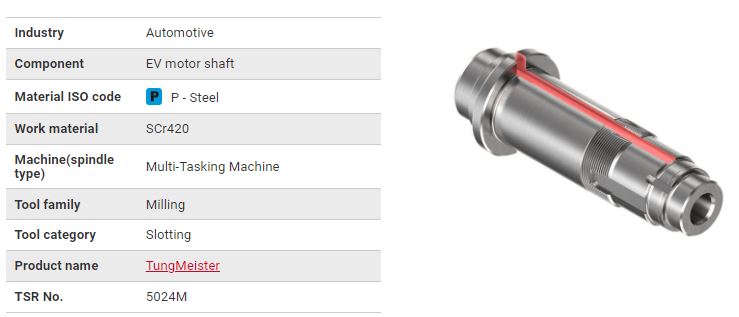
TungMeister’s T-slot heads have proven effective in many workshops. For example, in an automotive parts manufacturing site, switching from end mills to T-slot heads improved machining speed and significantly extended tool life.
In a specific success case, a process that previously required three passes with end mills was reduced to one pass with T-slot milling. As a result, machining time was reduced by 31%, and tool life increased tenfold. This led to reduced process time and cost savings.
Learn More About TungMeister Here
TungMeister T-Slot Head Line up
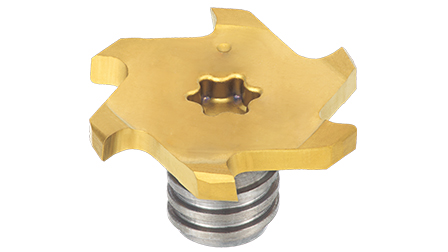
Tungaloy offers a lineup of T-slot heads that accommodate various slot widths and diameters.
TungMeister Special T-Slot Head Auto Drawing System
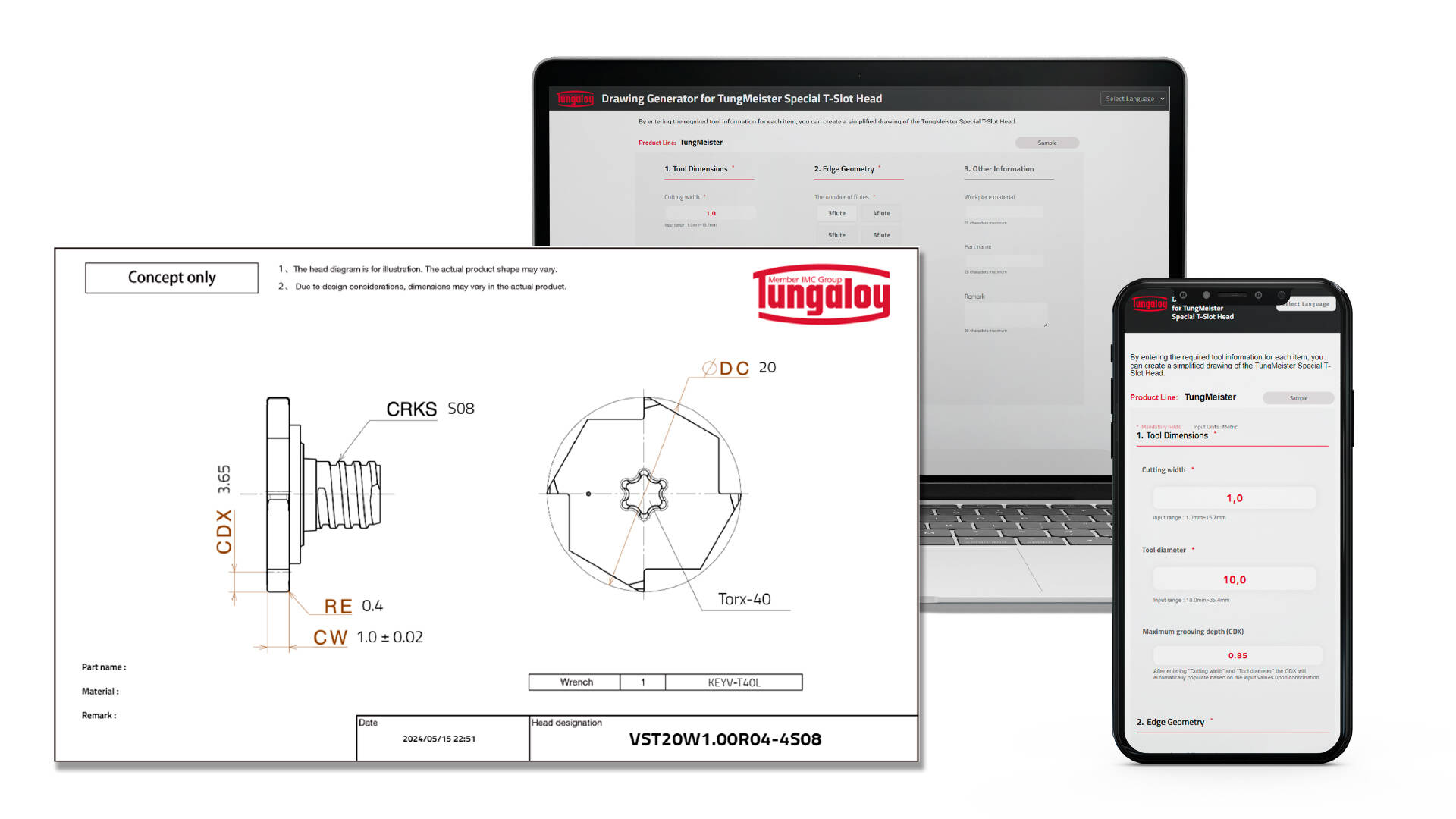
Try our automatic drawing system for designing special T-slot heads quickly and easily.