Challenges in Shaft Keyway Machining
In the automotive industry, shaft groove machining, particularly keyway machining, often uses solid carbide end mills. Grooving is prone to chatter, leading to reduced machining efficiency and shorter tool life, which are significant challenges in the machining process.
To address these issues, Tungaloy proposes TungMeister Series. TungMeister, as a Head exchangeable endmill, offers a wide variety of head and shank combinations. In the shaft groove machining of automotive parts, which requires mass production, it provides a solution that achieves improved machining efficiency and extended tool life.
Challenges of Keyway Machining with Solid End Mills
Keyway machining often uses solid carbide end mills and faces the following challenges:
- Grooving is prone to chatter.
- To suppress chatter, it is necessary to reduce cutting speed and feed rate, which decreases machining efficiency.
- Tool life is short, requiring frequent tool changes, which increases costs.
Innovative Proposal with TungMeister: Square Head with Chamfering Blade
Innovative square head with chamfering edge
This is a multifunctional tool that performs grooving and chamfering simultaneously by attaching a chamfering blade to a square head.
- When only a vertical approach is possible
- When the groove is not through and a corner radius is required
- The adoption of a high-rigidity shank improves tool rigidity and suppresses chatter.
- Designing the head length to be as short as possible enhances tool rigidity.
- The combination blade head with roughing and finishing cutting edges achieves high-level chatter resistance.
- Suppressing the occurrence of vibrations leads to improved machining efficiency and extended tool life.
Innovative T-slot head with chamfering edge
Using a tool with a chamfering edge attached to a T-slot head, grooving and chamfering are performed simultaneously.
- When a horizontal approach is possible
- When the groove machining distance is long
- When the groove is through
- By switching to a high-efficiency T-slot machining process, machining efficiency is dramatically improved.
- A larger tool diameter can be applied compared to a square end mill, allowing for an increased number of flutes.
- Additionally, the thinner chip thickness allows for a higher feed per tooth.Selecting a thicker shank achieves higher tool rigidity, extending tool life.
Both improved machining efficiency and extended tool life can be expected.
Success Story in EV motor shaft
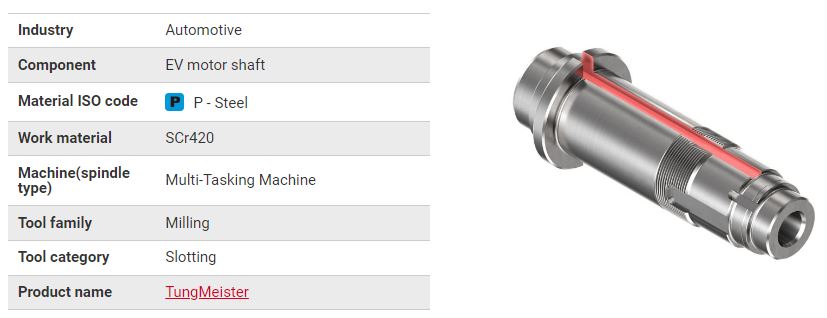
The conventional machining process required three steps using a ø6 end mill for grooving and shoulder milling, facing challenges with efficiency, tool life, and burrs. By switching to TungMeister’s special T-slot head with chamfering edges, the process was streamlined into a single pass, reducing time by 31%. The anti-vibration design and increased shank diameter of the T-slot head significantly suppressed chatter, resulting in a tenfold extension of tool life and improved overall machining efficiency.
Conclusion
The challenges of keyway machining with solid end mills, such as chatter, reduced machining efficiency, and short tool life, can be effectively addressed by Tungaloy’s innovative TungMeister solution. The TungMeister, with its head exchangeable endmill design, offers a variety of head and shank combinations to suit different machining conditions. Its high rigidity and precision help suppress chatter, enhance machining efficiency, and extend tool life.