タンガロイ成功事例
高生産性ヘッド交換式ドリル「DrillMeister」の採用で、工具費削減、加工タクトの短縮を実現し、設備能力の最大化に貢献
安藤鉄工(株)
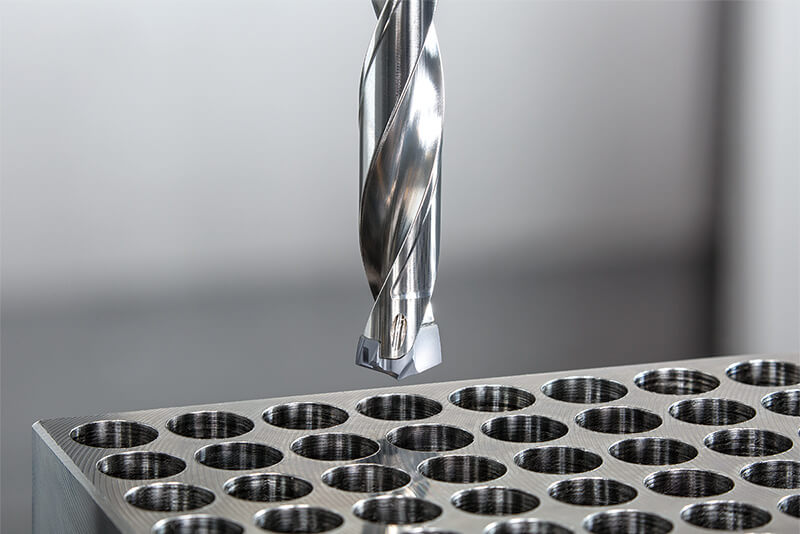
※本記事は機械技術2021年6月号掲載分をWeb用に再編集したものです。
切削加工の代表的な加工法であるドリル加工。穴あけ加工の大半で用いられ、マシニングセンタ(MC)などの機械加工では最も多くの作業時間を要する工程である。そのため穴あけ加工の効率化は生産性向上の大きなポイントとなってくる。岐阜県揖斐郡池田町に本社を置く安藤鉄工㈱は、穴あけ工程のドリル工具を見直し、コスト低減と生産タクト短縮を進めている。従来のソリッドドリルから(株)タンガロイ製ヘッド交換式ドリル「DrillMeister(ドリル・マイスター)」へ置き換えることで、刃具管理の安定化を図り、工具費と工具交換時間を削減。さらに適用範囲を広めることでさらなる高生産性を目指している。
ドリル工具の見直しで再研削から交換式へ
安藤鉄工は産業用ロボットや建設機械向け減速機部品の加工を主力とする金属加工メーカー。国内生産拠点は池田町内に本社、池田、宮地の3工場を持つ。海外では2017年に中国江蘇省常州市に安藤鉄工(常州)精密部件有限公司を設立し、19年から現地向け生産にも着手している。20年は米中貿易摩擦の影響やコロナ感染症の拡大で生産は若干落ち込んだものの、国内外での自動化需要などを背景に20年末ごろからロボット向け減速機部品を中心に回復し、現在は国内、中国ともフル生産状態にある。
「当社の強みは設備力」(金子慎一総務部部長)というように国内3工場では旋盤、MC、ホブ盤など約500台を保有。旋盤2台にロボット1台を組み合わせた旋盤自動化ラインをはじめMC、バリ取り、組立作業の自動化を推進し、顧客の要望に迅速に応えられる「攻めの経営」(同)を推進する。また、「社員に学ぶ意識付けとして技能検定受験を推奨し、社員の5割が技能検定を取得しています」(同)とモノづくりに対するモチベーションの高さも同社の原動力となっている。
この設備力を最大限に引き出すために取り組んだのがドリル工具の見直しである。18年に発足した製造部の原価低減活動の一環として「工具を見つめ直す」(多和田正芳製造部部長代理)ことから始まった。同社では従来、タップ下穴、きり通し穴を超硬ソリッドドリルで加工し、摩耗したドリルは精度と効率の観点から新品に取り換えるのが慣習となっていた。そこで工具費削減策としてまず着手したのがドリルの再研削だった。
ところが予想したほどの成果が表れてこなかった。「新品に比べて費用は3分の1程度に下げられましたが、再研削ごとに工具長が変わるため交換時のオフセット作業の手間が増えたほか、研削回数によって工具寿命がばらつき、工具管理が難しくなる」(同)といった新たな問題が生じてきた。
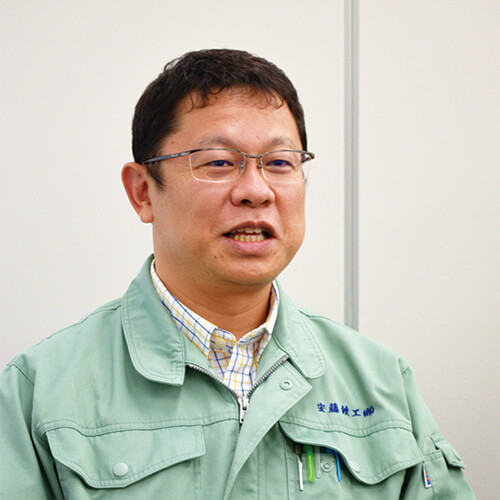
金子 慎一氏
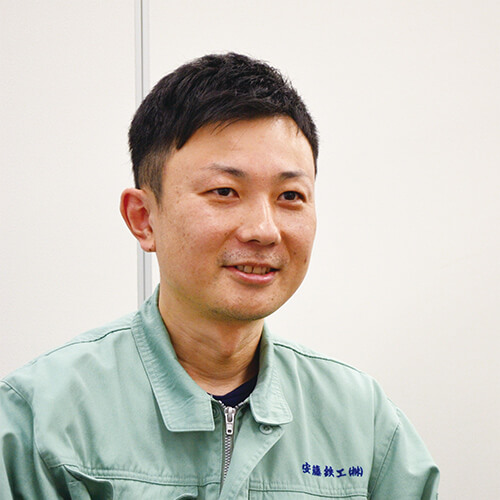
多和田 正芳氏
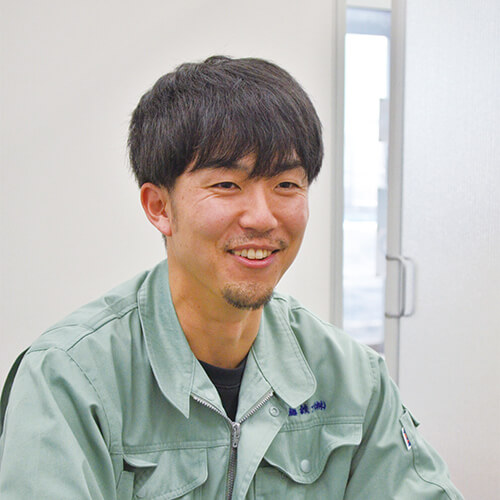
加納 崇善氏
工具交換時間を大幅短縮工具費10%削減
そうした中、ソリッドドリルを購入していたタンガロイの販売代理店を通じて紹介されたのが「DrillMeister」だった。ドリル先端部のヘッド交換のみで工具長の調整などの手間は不要になり、費用も新品のソリッドドリルの半分程度に抑えられることから試験採用することを決めた。
試験導入はロボット向け減速機部品を担当する池田工場で始まった。同工場は全従業員数の約半数にあたる150人が勤務し、2交代で月産12万個を生産する主力工場である。旋盤89台、MC87台が稼働し、3年前からは高周波熱処理の自動化設備も導入。焼入れの内製化によるコスト削減と納期短縮にも取り組んでいる。
「最初はS55C材のタップ下穴の加工に採用し、穴数が1番多いM12を中心にM8、M10、M16、M18と徐々に対象を広げていきました。新品のソリッドドリルと比べても精度や品質に問題なく、ヘッド交換が容易なので再研削に比べて効率は格段に上がりました」(加納崇善製造部第4製造課課長)との成果が得られた。コスト面でもイニシャルコストとしてホルダが必要となるが、ランニングコストが下がったことで4〜5回のヘッド交換で費用は回収でき、工具費削減にも結び付いた。
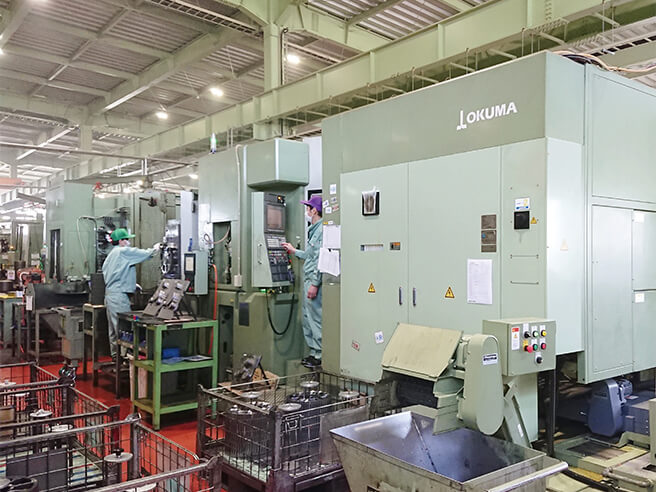
全工場にDrillMeisterを展開今秋には新工場を建設
この結果、タップ下穴に加えて、リーマ加工の下穴、きり通し穴へと適用範囲を広げ、21年4月現在で池田工場でのドリル穴加工の70%をDrillMeisterに切り替え「18年時点に比べて10%の工具費削減を実現」(多和田部長代理)している状況だ。また、DrillMeisterを採用する際に切削条件を見直し、送りを上げることもでき、加工タクトの短縮にも貢献している。
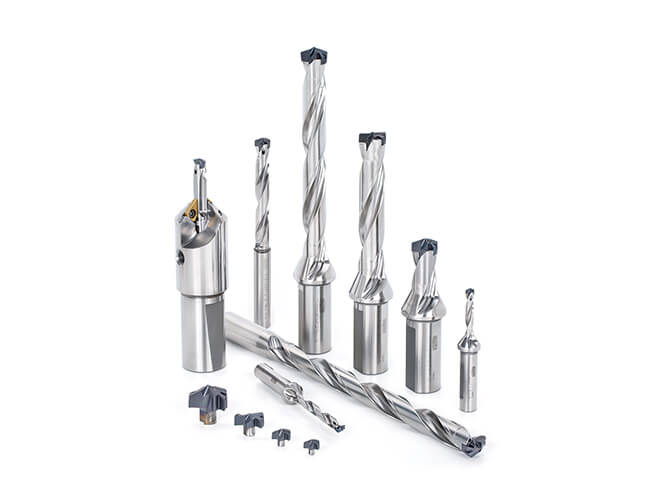
再研削レスで安定長寿命を実現。工具費、工具管理コストを大幅に低減できる。
「減速機部品において穴加工は頻度が高く、池田工場では加工時間全体の50%を占める重要な工程です。当初は浅い穴加工への適用のみを想定していましたが、ヘッドのバリエーションも増えてきたことから深穴加工や素材もFCD材にも適用範囲を広げてコストメリットを上げていきます」(加納課長)とし、他工場へも展開していく計画である。
同社では減速機の需要増を背景に21年秋をめどに本社工場の近隣に新工場を建設する。「池田工場が手狭になってきたため新工場ではロボット向けの減速機部品の生産を行う計画です。具体的な導入設備は今後詰めていきますが、池田工場でのコスト削減の実績を踏まえ、設備に反映していきたいと考えています」(金子部長)。ドリル工具の効率化をばねに設備力を活かし、さらなる「攻めの経営」を展開していく方針だ。