
これは、タンガロイの営業担当がお客様とともに歩んだ成功への道である。
長突き出しが必要な金型キャップボルト座加工の課題を解決!
取材協力株式会社P・A・Sアシスト
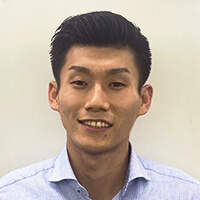
タンガロイ営業担当
伊藤 遼Ryo Itoh
- 出身
- 東京都葛飾区
- 社歴
- 入社2019年 社歴4年
- 趣味など
- サッカー、スポーツ観戦
今回は部品加工に意外と多い“座繰り加工”にまつわるストーリーである。
愛知県みよし市に拠点を構える株式会社P・A・Sアシスト様は、先代の社長が静岡県で創業し、プレス金型やダイキャスト金型の製造、レース向け自動車部品加工を行ってきた。みよし市に拠点を移した現在は、自動車プレス金型加工をメインに様々な業種の金型加工を行っている。
そんなP・A・Sアシスト様の強みは、3DCADを用いた金型設計やCAMを活用した高い技術力である。会社創業時から一早くCAMを導入したため、CAMを用いた加工の経験や知見が豊富である。また、3D CADを活用した開発・設計業務も対応できるため、金型の設計から加工まで一貫して対応できる点も強みの1つである。
現場で学んだ経験を活かした提案活動
担当の伊藤は2019年にタンガロイ入社後、名古屋営業所に赴任となった。
名古屋営業所に赴任してからは、お客様の実際の加工現場から学ぶことが多かった。切削の理論については研修で一通り学んで理解していたが、実際の加工現場で起こりうる課題や改善点は理論だけでは解決できないことも多かった。しかしながら泥臭くお客様に足を運んで提案をしながら、実際の加工を見ることで自分自身の引き出しが多くなり、切削理論と現場の経験を掛け合わせることで、少しずつ提案の質も上がっていった。今では提案する量だけでなく質にもこだわって営業活動を行っている。
今回のストーリーであるP・A・Sアシスト秋山社長と出会ったのは、そんながむしゃらに提案活動をしている頃の話だ。それまではP・A・Sアシスト様に訪問しても秋山社長に直接提案をする機会はなかった。そんなある日、現場ではなく事務所に顔を出させてもらった際に、たまたま秋山社長にご挨拶をすることができ、製品を直接PRさせて頂いた。
そこから定期的に工具を提案する関係がスタート。様々な工具提案をしていくなかで、お付き合いが深くなっていったそんな折、秋山社長から穴加工に関する課題のご相談を受けた。
長突き出しが必要なキャップボルト座加工
P・A・Sアシスト様では、大物金型の受注が近年増加傾向であり、今まではL/D=5で足りていた穴加工に、L/D=8や10の穴加工への対応も必要になってきた。その中でも、特に課題であった工程としては「長付き出しが必要なキャップボルト座」の加工であった。
ボルト座の穴深さ自体はL/D=3程度であるが、加工部近くに干渉があるなど、必要な穴深さを加工するためにはL/D=8ドリルを使用する必要があった。この工程に他社のヘッド交換式ドリルを使用していたが、下記のような課題が存在した。
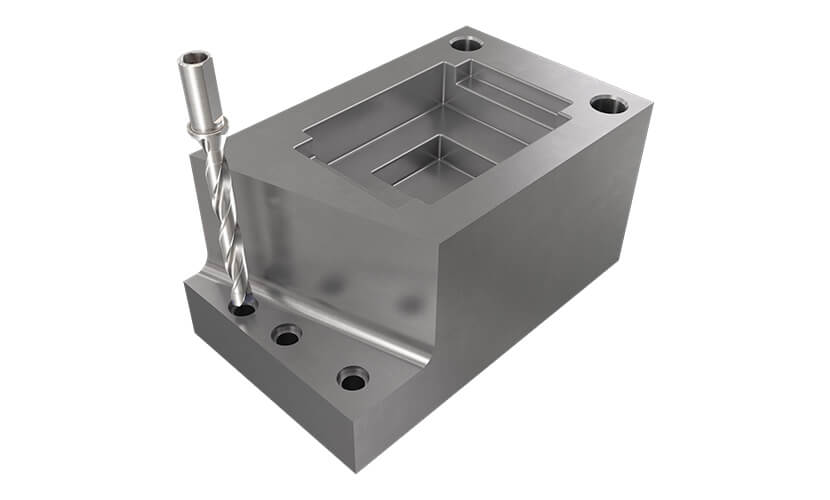
課題1:加工に3つの工具の使用が必要
他社のヘッド交換式ドリルでは、フラットタイプのヘッドを用いたL/D=8加工は安定的に行えなかったため、手間のかかる3工程での加工が必要であった。
工程詳細
- 工程1:「L/D=5ドリル + フラッドタイプヘッド」を使用して、ガイド穴を加工
- 工程2:「L/D=8ドリル + 先端角140°タイプヘッド」を使用して、必要穴深さ手前まで加工
- 工程3:「L/D=8ドリル + フラッドタイプヘッド」を使用して、穴底をフラットに修正
- 工程1:
- 工程2:
- 工程3:
課題2:工具本数が増加し、ツールポッドの工具搭載数を圧迫。夜間の無人運転ができない
P・A・Sアシスト様では加工の自動化を進めており、夜間に無人運転で加工を進めることを基本としている。しかし、穴加工工程での工具本数がかさばり、加工途中で工作機械のツールポッドの工具入れ替えが必要で夜間の無人運転が行えない課題があり、生産性をおとす大きな要因になっていた。
課題3:加工時間が長い
前述の課題よりも深刻度は低かったが、1つのキャップボルト座加工に2分の加工時間を要しており、本点も生産上の課題になっていた。
ヘッド交換式ドリルDrillMeister DMF型を使用したL/D=8一発加工
その課題を受けて、伊藤が行った提案は「ヘッド交換式ドリルDrillMeisterフラットヘッドDMF型を使用したL/D=8一発加工」である。DMFヘッドを用いたL/D=8の加工はカタログでも推奨されているが、伊藤にとっては始めての経験であったため、加工難易度の高いこの加工への不安はあった。しかし、他社のフラットタイプヘッドは、切れ刃全体が完全にフラットであったのに対し、DMFヘッドは切れ刃中心部に食いつき性を高めるパイロットエッジが備えられている。他社のフラットヘッドでは難しかった加工も、食いつき性の改善により、他社よりも優位な結果が得られるだろうと考えこの提案を行ったのである。
この提案を受けた秋山社長も提案を受けた当初は、苦労してきた過去の経験から「一発加工は難しいのではないか?」と半信半疑であった。しかし、以前より伊藤が行ってきた提案は効果が出るケースが多く、今回も伊藤を信じ、テストの実施を決断した。
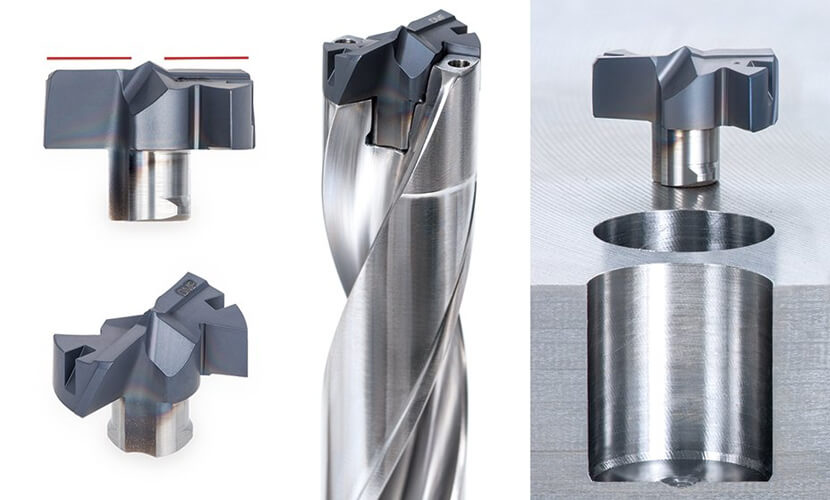
工具・工程集約に成功!生産性を大きく改善!
初回の加工テストでは、カタログ推奨の中央値である切削速度Vc=90m/min,f=0.25mm/revでトライアルを行った。この条件ではびびりが発生し、ヘッドに欠けが生じたため寿命目標である加工長9mは達成できなかった。
そこで再度切削条件を見直し、送りをf=0.15mm/revまで低下させたところ、加工が安定。加工長25mまで寿命延長が行えることが確認できた。
このテスト結果を受けてDrillMeisterの正式採用を決めた。採用後の実生産では下記のような効果が得られ、伊藤の提案が生産性と工具費改善に大きく貢献したのである。
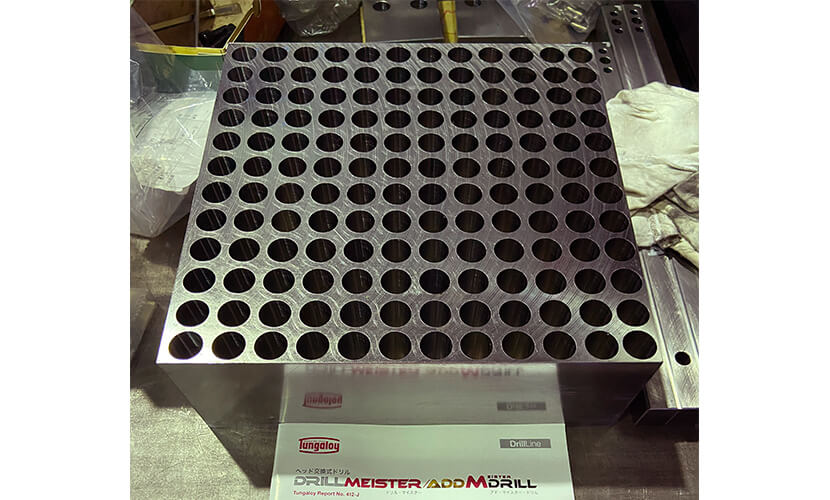
今回の改善ポイント
-
3本必要であった工具が1本に集約できた。ツールポッドの工具本数が圧縮でき、夜間での無人運転が可能になった
-
以前は2~3分要していた加工が20秒にまで短縮
-
工具集約により工具本数が減ったため、予備工具の在庫金額が削減できた
更なる高性能工具開発への期待
秋山社長は、金型の開発・製作工程の改善プロジェクトを自動車Tier1メーカーと協業し取り組まれている。金型の開発工程では、一度試し打ちをした後に設計変更を行うプロセスがあり、その際には修正部を溶接で肉盛りし再加工を行うことが一般的だそうだ。しかし、溶接のリードタイムやコスト削減のために、予め金型修正を盛り込んだ厚さの鋼材を準備しておき、その厚さ増分を設計変更時の再加工に利用するといった工法を検討中である。
この工法を達成するためには、穴深さはより深くなり、L/D=12や15の加工を行う必要がある。前述した機械ツールポッド数の制限があるため、秋山社長はL/D=12や15を一発で加工できるドリルを要望されている。
また、加工後に焼入れをする金型もあることから、座繰り隅部のクラック対策として、隅部に0.5~1.0Rを形成できる座繰りヘッドのラインナップや、焼入れ後の形状加工に用いる刃先中心部が強いボール形状のミーリングインサートの開発も要望されている。
タンガロイとしては、これら金型加工現場の要望に応えられる製品開発と提案ができる体制を今後も強化していきたい。
今回ご紹介した製品はこちら
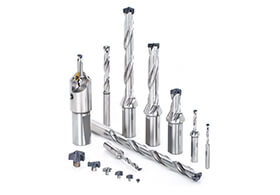