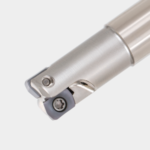
Small-diameter high-feed milling cutter with robust design for stability and efficiency
Indexable high-feed milling cutter, available in as small as ø8 mm diameter, offers free cutting and effective chip control in a wide range of applications
Applications & Features
Applications
Features
1. Built to perform at higher machining conditions
Strong and thick insert corner is designed to withstand fracturing force during high-feed operations.
Thick insert corner Max. 10% thicker than competitors
M2 screws reduce screw neck shears under high cutting forces. A larger screw enhances insert’s fixation and easy handling.
2. Positive inclination angle of the insert provides smooth chip evacuation
The positive cutting edge position contributes to a controlled chip formation and easy chip evacuation when machining next to shoulder and slotting operation.
Positive inclination angle
3. Designed with a small entry angle for chatter stability, TungForceFeed’s insert significantly improves efficiency and tool life even when machining in long reach areas
Inserts & Grades
Inserts
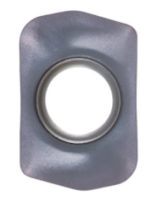
LSMT-HM
- High-feed insert
- Max. depth of cut: 0.5 mm
- Provides machining efficiency in a wide range of applications
- First choice insert for various applications including slotting, pocketing, or long reach areas
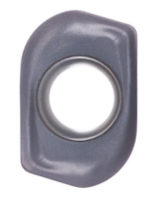
LSMT-MM
- R2 insert
- Max. depth of cut: 2.0 mm
- Full profiling insert design ideal for semi-roughing and semi-finishing of die and mold parts
- Free cutting geometry eliminates chattering and improves surface finish quality
- Built-in side wiper helps reduce burr formation on walls and corners while improving wall accuracy
Grades
AH3225
- Nano multi-layer coating technology with three major properties for optimal cutting edge integrity
- Increased resistance to wear, fracture, oxidation, built-up edge, and delamination
AH8015
- Incorporates a hard coating layer and carbide substrate
- Strong resistance to wear, heat, and built-up edge, ideal for machining hard or difficult materials
Cutter bodies
Practical examples
Example #1
Aerospace Industry
Part: | Turbine blade |
Material: | Inconel 939 |
Cutter: | EXLS02M008C8.0LH16R01 (ø8, CICT = 1) |
Insert: | LSMT0202ZER-HM |
Grade: | AH8015 |
Cutting conditions: | Vc = 30 (m/min) fz = 0.2(mm/t) (Competitor:fz = 0.05) ap = 0.3 (mm) ae = 8 (mm) Application: Grooving Coolant: Dry Machine: Vertical MC, BT50 |
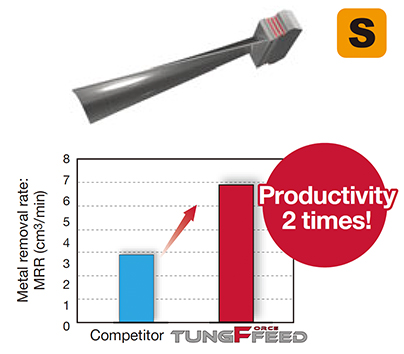
Example #2
Die and Mold Industry
Part: | Stamping die part |
Material: | SKD11 (before hardening) |
Cutter: | HXLS02M010M06R02 (ø10, CICT = 2) |
Insert: | LSMT0202ZER-HM |
Grade: | AH3225 |
Cutting conditions: | Vc = 120 (m/min) fz = 0.6 (mm/t) ap = 0.3 (mm) ae = 5 (mm) Application: Pocketing Coolant: Dry Machine: Vertical MC, BT40 |
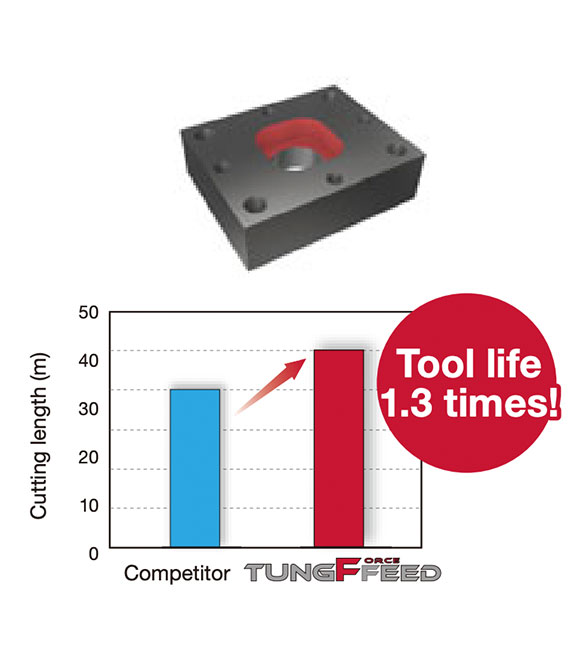
Example #3
Die and Mold Industry
Part: | Stamping die part |
Material: | SKD61 (45HRC) |
Cutter: | EXLS02M012C12.0LH50R02 (ø12, CICT = 2) |
Insert: | LSMT0202ZER-HM |
Grade: | AH3225 |
Cutting conditions: | Vc = 113 (m/min) fz = 0.5 (Competitor:fz = 0.1) (mm/t) ap = 0.3 (mm) ae = 12 (mm) Application: Face milling Coolant: Air Machine: Vertical MC, BT50 |
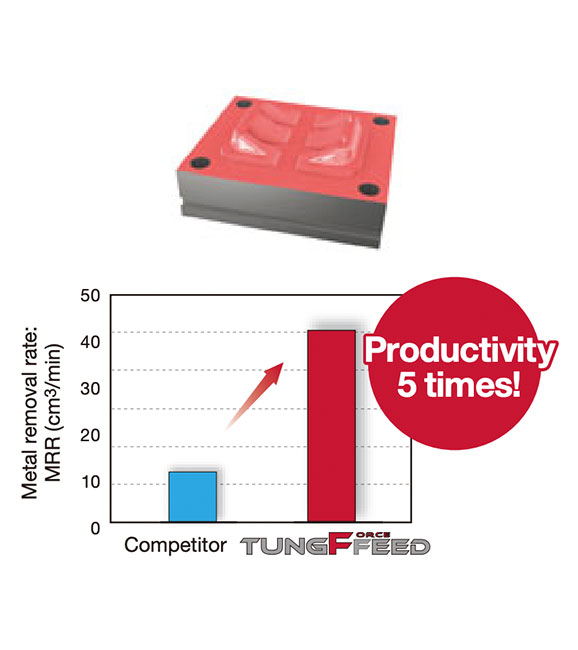
Standard cutting conditions
ISO | Workpiece materials | Hardness | Priority | Grades | Cutting speed Vc (m/min) |
Feed per tooth fz (mm/t) |
Tool dia.: øDc (mm), Number of revolutions: n (min-1), Feed speed: Vf (mm/min), Max. depth of cut: ap = 0.5 mm, Number of teeth: CICT | ||||||||||||||||
---|---|---|---|---|---|---|---|---|---|---|---|---|---|---|---|---|---|---|---|---|---|---|---|
ø8, CICT = 1 | ø10, CICT = 2 | ø12 | ø16 | ø20 | ø25 | ||||||||||||||||||
n | Vf | n | Vf | n | Vf | n | Vf | n | Vf | n | Vf | ||||||||||||
CICT = 2 | CICT = 3 | CICT = 3 | CICT = 5 | CICT = 5 | CICT = 6 | CICT = 6 | CICT = 8 | ||||||||||||||||
![]() |
Carbon steels (S45C / C45, S55C / C55, etc) |
– 300HB | First choice | AH3225 | 100 – 300 | 0.2 – 0.8 | 7,960 | 3,980 | 6,370 | 6,370 | 5,310 | 5,310 | 7,970 | 3,980 | 5,970 | 9,950 | 3,180 | 7,950 | 9,540 | 2,550 | 7,650 | 10,200 | |
– 300HB | For wear resistance | AH8015 | 100 – 300 | 0.2 – 0.8 | Vc = 200 m/min, fz = 0.5 mm/t | ||||||||||||||||||
Alloy steels (SCM440 / 42CrMo4, etc) |
– 300HB | First choice | AH3225 | 100 – 300 | 0.2 – 0.8 | 7,960 | 3,980 | 6,370 | 6,370 | 5,310 | 5,310 | 7,970 | 3,980 | 5,970 | 9,950 | 3,180 | 7,950 | 9,540 | 2,550 | 7,650 | 10,200 | ||
– 300HB | For wear resistance | AH8015 | 100 – 300 | 0.2 – 0.8 | Vc = 200 m/min, fz = 0.5 mm/t | ||||||||||||||||||
Prehardened steels (NAK80, PX5, etc) |
30 – 40HRC | First choice | AH8015 | 100 – 200 | 0.2 – 0.5 | 5,970 | 2,390 | 4,780 | 3,820 | 3,980 | 3,180 | 4,780 | 2,990 | 3,590 | 5,980 | 2,390 | 4,780 | 5,740 | 1,910 | 4,590 | 6,120 | ||
30 – 40HRC | For impact resistance | AH3225 | 100 – 200 | 0.2 – 0.5 | Vc = 150 m/min, fz = 0.4 mm/t | ||||||||||||||||||
![]() |
Stainless steels (SUS304 / X5CrNi18-9, (SUS304 / X5CrNi18-9, SUS316 / X5CrNiMo17-12-3, etc) |
– 200HB | First choice | AH3225 | 100 – 150 | 0.2 – 0.5 | 4,780 | 1,910 | 3,820 | 3,060 | 3,190 | 2,550 | 3,830 | 2,390 | 2,870 | 4,780 | 1,910 | 3,820 | 4,590 | 1,530 | 3,680 | 4,900 | |
Vc = 120 m/min, fz = 0.4 mm/t | |||||||||||||||||||||||
![]() |
Gray cast irons (FC250 / 250 / GG25, (FC250 / 250 / GG25, FC300 / 300 / GG30, etc) |
150 – 250HB | First choice | AH8015 | 100 – 300 | 0.2 – 0.8 | 7,960 | 3,980 | 6,370 | 6,370 | 5,310 | 5,310 | 7,970 | 3,980 | 5,970 | 9,950 | 3,180 | 7,950 | 9,540 | 2,550 | 7,650 | 10,200 | |
150 – 250HB | For impact resistance | AH3225 | 100 – 300 | 0.2 – 0.8 | Vc = 200 m/min, fz = 0.5 mm/t | ||||||||||||||||||
Ductile cast irons (FCD600 / 600-3 / GGG60, etc) |
150 – 250HB | First choice | AH8015 | 80 – 200 | 0.2 – 0.8 | 5,970 | 2,990 | 4,780 | 4,780 | 3,980 | 3,980 | 5,970 | 2,990 | 4,490 | 7,480 | 2,390 | 5,980 | 7,170 | 1,530 | 4,590 | 6,120 | ||
150 – 250HB | For impact resistance | AH3225 | 80 – 200 | 0.2 – 0.8 | Vc = 150 m/min, fz = 0.5 mm/t | ||||||||||||||||||
![]() |
Titanium alloy (Ti-6Al-4V, etc) |
– 40HRC | First choice | AH3225 | 30 – 60 | 0.1 – 0.3 | 1,590 | 320 | 1,270 | 510 | 1,060 | 420 | 640 | 800 | 480 | 800 | 640 | 640 | 770 | 510 | 620 | 820 | |
– 40HRC | For wear resistance | AH8015 | 30 – 60 | 0.1 – 0.3 | Vc = 40 m/min, fz = 0.2 mm/t | ||||||||||||||||||
Heat resistance alloy (Inconel, Hastelloy, etc) |
– 40HRC | First choice | AH8015 | 20 – 50 | 0.1 – 0.3 | 1,190 | 240 | 1,000 | 400 | 800 | 320 | 480 | 600 | 360 | 600 | 480 | 480 | 580 | 380 | 460 | 460 | ||
– 40HRC | For impact resistance | AH3225 | 20 – 50 | 0.1 – 0.3 | Vc = 30 m/min, fz = 0.2 mm/t | ||||||||||||||||||
![]() |
Hardened steel | SKD61 / X40CrMoV5-1, etc | 40 – 50HRC | First choice | AH8015 | 80 – 150 | 0.1 – 0.5 | 4,780 | 1,430 | 3,820 | 2,290 | 3,190 | 1,910 | 2,870 | 2,390 | 2,150 | 3,590 | 1,910 | 2,870 | 3,440 | 1,530 | 2,760 | 3,680 |
Vc = 120 m/min, fz = 0.3 mm/t | |||||||||||||||||||||||
SKD11 / X153CrMoV12, etc | 50~60HRC | First choice | AH8015 | 50 – 70 | 0.1 – 0.3 | 2,390 | 480 | 1,910 | 760 | 1,590 | 640 | 950 | 1,190 | 710 | 1,190 | 950 | 950 | 1,140 | 760 | 920 | 1,220 | ||
Vc = 60 m/min, fz = 0.2 mm/t |
For more information about this product, visit our online e-catalog or download the product report: