
Unlocking the Future: Machining 3D Printed Metal Components
In the evolving landscape of manufacturing, 3D printing has emerged as a transformative technology, especially for metal components. The ability to create complex geometries and internal structures directly from digital designs has opened new frontiers in various industries, including aerospace, medical, and automotive. However, while 3D printing offers incredible advantages, the journey from a printed part to a functional component often requires an essential finishing touch: machining. This article delves into the crucial role of machining in refining 3D printed metal parts, exploring the challenges faced and the specialized approaches required to overcome them.
Reasons for Machining 3D Printed Metal Components
- Surface Finish: As-printed surfaces often have a rough finish. Machining processes like grinding and polishing improve the surface texture, making parts suitable for both functional and aesthetic purposes.
- Dimensional Accuracy: While 3D printing provides good accuracy, machining refines parts to meet the exacting tolerances required for critical applications, ensuring parts fit together precisely in assemblies.
- Removal of Support Structures: Support structures are often necessary during the printing process but must be removed for the part to function correctly. Machining removes these supports and smooths the resultant surfaces.
- Mechanical Properties: Machining can relieve residual stresses induced during printing, enhancing the overall mechanical properties and performance of the part.
- Assembly Fit: Ensuring that parts fit together correctly in assemblies is crucial for the functionality of complex systems. Machining ensures precise fits and smooth interfaces.
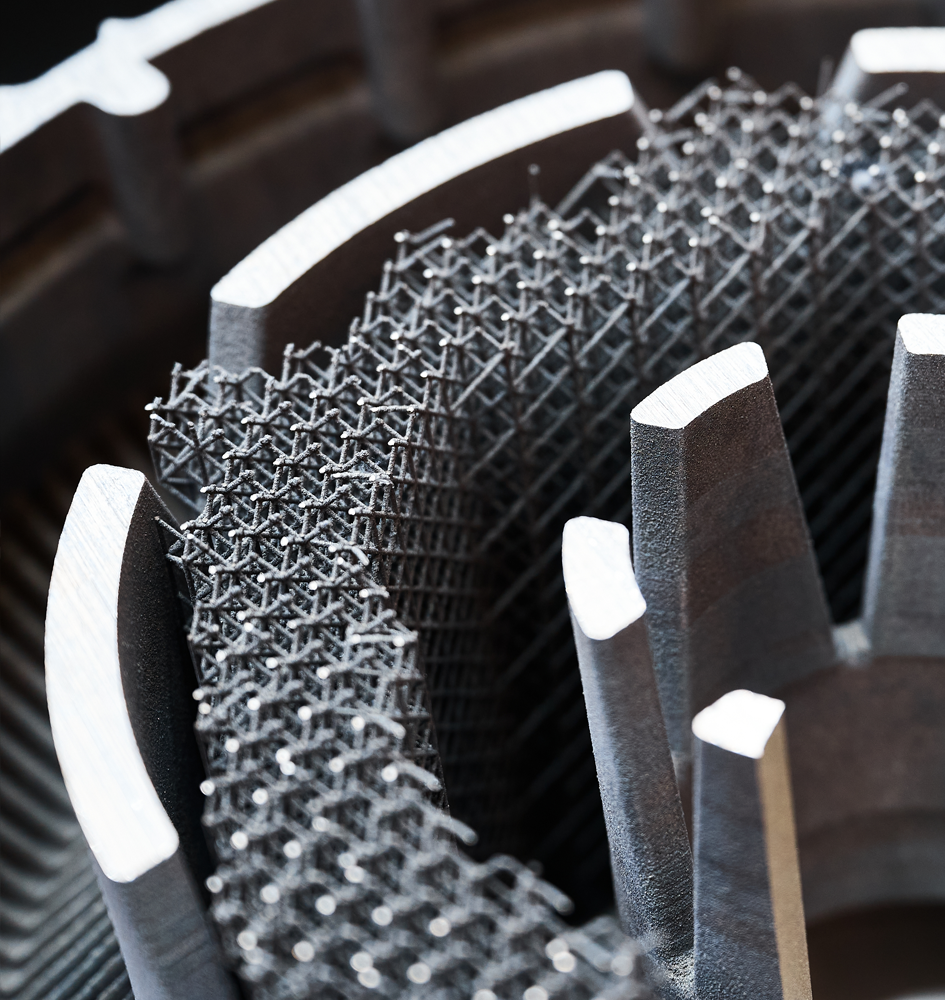
3D-printed component with internal mesh supports
Industries Leveraging Machining of 3D Printed Metal Components
Aerospace: The aerospace sector demands lightweight, high-strength components with intricate designs. 3D printing facilitates these needs by producing parts that are challenging to create through traditional means. Post-processing through machining ensures these parts meet the stringent tolerance and surface finish requirements necessary for aerospace applications. The use of titanium is increasing due to its high strength-to-weight ratio and corrosion resistance.
Medical and Dental: In the medical field, precision and biocompatibility are paramount. 3D printing is utilized to create custom implants, dental restorations, and surgical instruments. Machining enhances surface finishes and ensures precise fits, which are critical for patient safety and comfort. Stainless steel and cobalt-chrome alloys are commonly used for their biocompatibility and durability.
Automotive: Automotive manufacturers use 3D printing for prototyping and producing performance-critical components like engine parts and heat exchangers. Machining refines these parts to meet the exacting specifications required for high-performance applications. Aluminum and titanium alloys are frequently used for their lightweight and high strength.
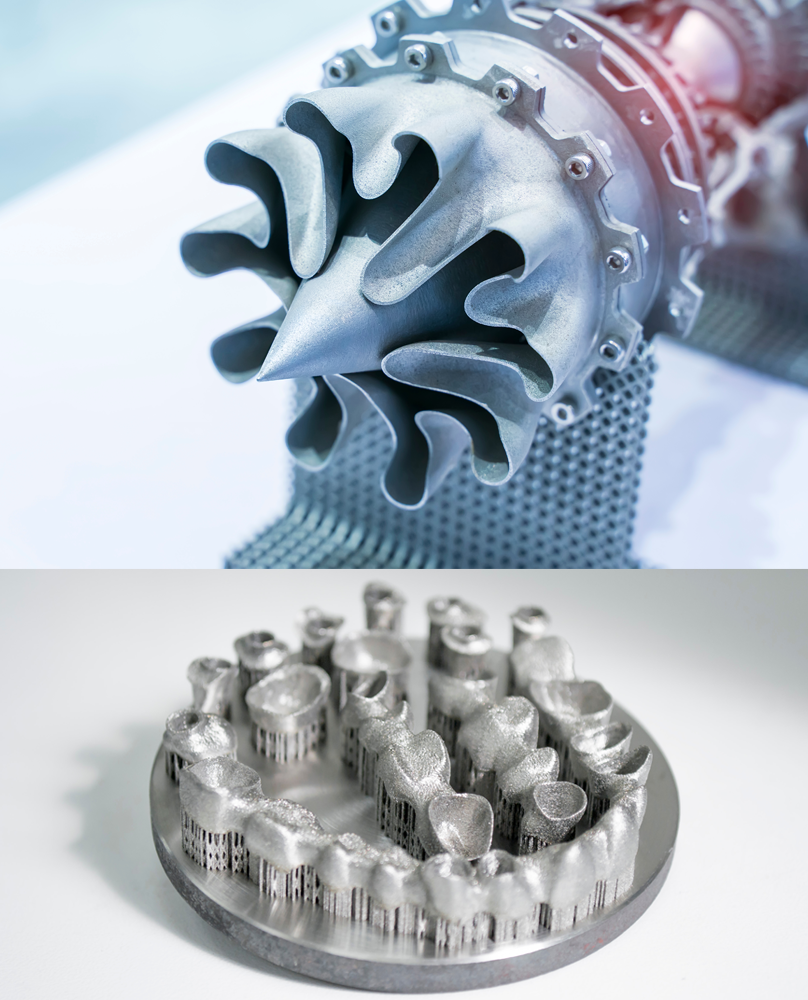
Aerospace jet engine 3D printed and 3D printed dental crowns
Tool and Die: Tooling components, including molds and dies, benefit significantly from 3D printing’s ability to create complex shapes and internal cooling channels. Machining these parts is essential to achieve the durability and precision needed for tooling applications. High-speed steel and carbide materials are often utilized for their toughness and wear resistance.
Oil and Gas: In the oil and gas industry, components such as impellers and housings are 3D printed for bespoke applications. Machining ensures these parts can withstand the harsh operational environments they will encounter. Materials like Inconel and stainless steel are used due to their excellent corrosion resistance and mechanical properties.
Changes Brought by 3D Printing to Machining
Increased Complexity of Component Shapes: 3D printing enables the manufacturing of shapes that were difficult or impossible to produce with traditional manufacturing processes, reducing design constraints and increasing design freedom. This leads to more complex component shapes, which in turn increases the need for profile machining in cutting processes. The machining of complex-shaped components also impacts the machine tools used. To process these complex shapes, multi-axis machine tools such as 5-axis machining centers and multi-tasking machines are increasingly required.
Impact of Increased Complexity on Cutting Tools: Increased profile machining and reduced allowance mean that the share of finishing processes in total machining time increases, necessitating high-productivity finishing methods.
Tool Material and Design Considerations
Tungaloy offers a wide variety of cutting tool materials and coatings to address the diverse needs of different industries. For example:
- Coating Technologies:
- TiAlN (Titanium Aluminum Nitride): Offers high wear resistance and oxidation resistance, ideal for high-speed machining.
- Diamond Coatings: Used for non-ferrous materials and composites, offering exceptional wear resistance.
Advancements and Innovations in Machining 3D Printed Components
The field of machining 3D printed components is evolving with several key advancements:
High-Precision Machining:
3D printed parts require high-precision cutting tools for final finishing, as 3D printing alone can’t achieve the desired surface finish and accuracy.
Handling Complex Shapes:
Multi-axis and five-axis machining centers are essential for handling complex structures. Cutting tools must be multifunctional to execute precise, three-dimensional machining.
Reduced Workpiece and Fixture Rigidity:
As 3D printed parts become more intricate, both workpiece and fixture rigidity decrease. Low-resistance cutting tools are necessary to minimize vibrations and maintain stability during machining.
Machining High-Hardness Materials:
3D printing often results in high-hardness materials, increasing tool wear. Cutting tools must have a long tool life to handle these challenging materials effectively.
Tungaloy Cutting Tools to Address Changes Brought by 3D Printing
To address the changes and challenges brought by 3D printing in metal components, Tungaloy offers a range of cutting tools and technologies designed to meet the demands of modern machining.
Miniaturization of Inserts:
With 3D printing reducing the material left for machining, Tungaloy is focusing on smaller insert-exchangeable tools. This miniaturization fits reduced material allowances and increases the number of cutting edges, enhancing efficiency. Tools like the TungForceRec, TungTri, AddDoFeed, and TungForceFeed exemplify this approach.
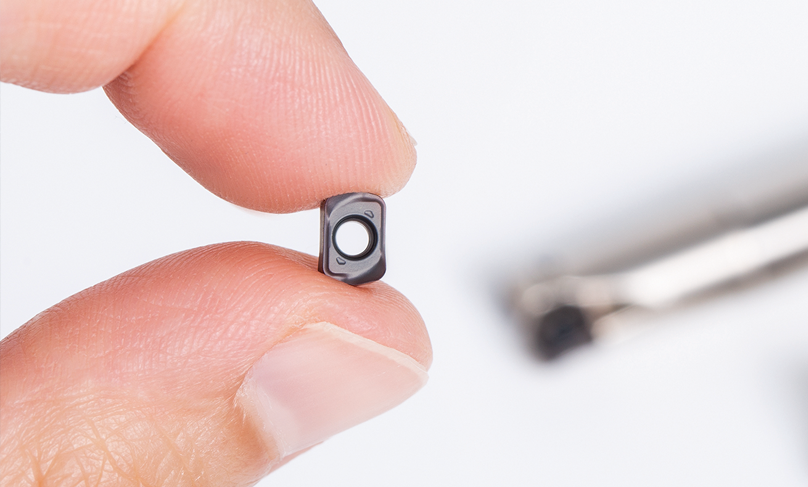
Solutions for Long Overhang Machining
When machining parts with complex shapes, there can be interference between the workpiece and the tool. To prevent this, tools are often extended further from the machine, which can lead to vibration (chatter). Tungaloy suggests two main solutions to address this:
High-Feed Tools: These tools have low resistance in the vertical direction, which reduces vibration and deflection. They’re especially useful for machining with long tool overhangs, where chatter is more likely. Tungaloy has a wide selection of high-feed tools designed for various machining needs.
Exchangeable Head Tools: For long overhangs, it’s important to use tools that provide maximum rigidity. Tungaloy’s TungMeister series offers a variety of head shapes and shank options, allowing you to customize the tool setup for optimal rigidity and performance in long overhang machining.

Improving Machining Efficiency in Finishing:
As near-net shaping reduces rough machining, efficient finishing becomes more crucial. Tungaloy’s barrel tools, with specialized cutting edges, replace conventional ball end mills to reduce finishing passes and save time. The range includes solid tools, TungMeister exchangeable heads, and AddForceBarrel insert tools.
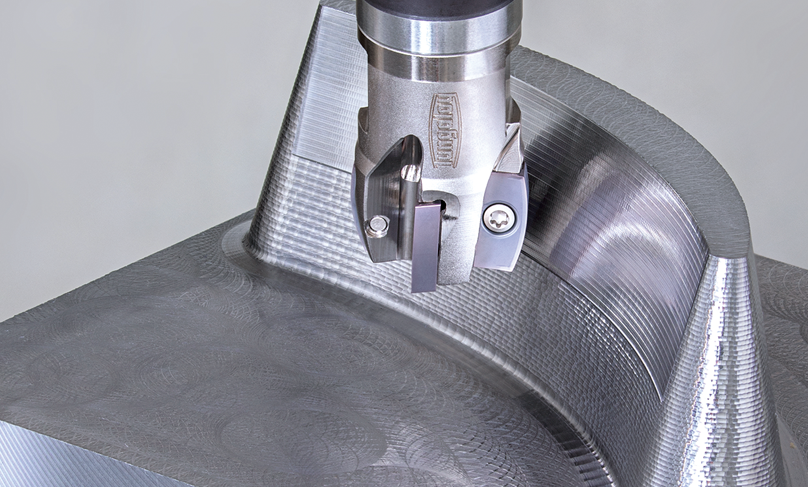
Insert Grades for High-Hardness and Difficult-to-Cut Materials:
Tungaloy’s AH8000 series is tailored for machining high-hardness and difficult-to-cut materials. This PVD grade features a TiAlN coating with high aluminum content for increased hardness and nano-layered films for improved chipping resistance.
Integration of 3D Printing in Tungaloy’s Production Processes
In addition to its expertise in machining 3D printed metal components, Tungaloy is at the forefront of utilizing 3D printing technology in its production processes. This cutting-edge approach is exemplified by the manufacture of drill bodies for the DrillMeister line, where 3D printing allows for the creation of complex geometries and internal cooling channels that enhance tool performance. By integrating 3D printing across its production lines, Tungaloy can produce highly customized and precise components with reduced material waste and shorter lead times. This synergy between additive and subtractive manufacturing processes not only enhances efficiency but also reduces the overall environmental footprint.
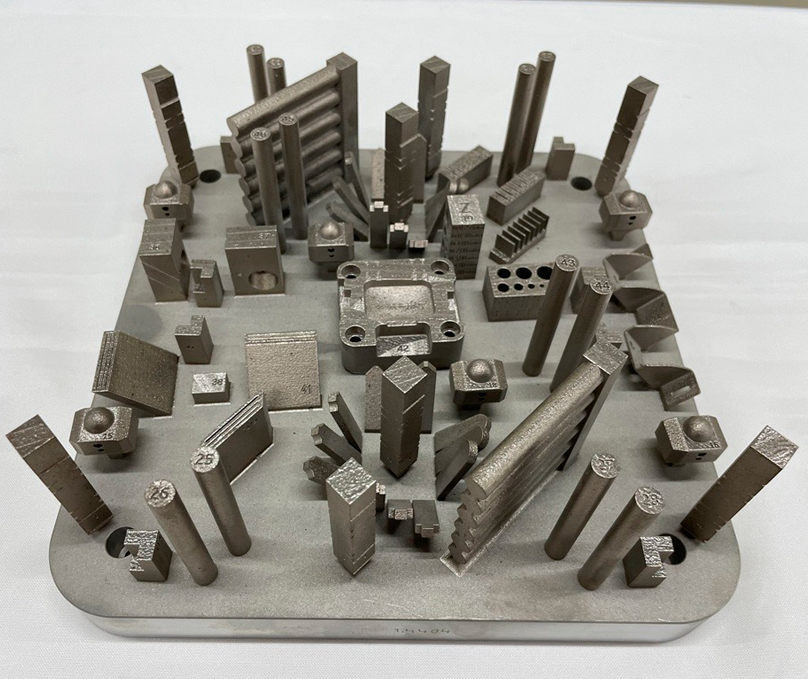
Tungaloy 3D printed components
Challenges and Considerations
Machining 3D printed metal components presents several challenges. These include dealing with the directional properties (anisotropy) and internal stresses found in printed metals, managing tool wear due to the hardness and abrasiveness of certain materials, ensuring effective heat management to maintain part integrity, and securely fixing complex-shaped components during machining. Successfully addressing these challenges demands meticulous tool selection, precise machining parameters, and the application of advanced machining techniques.
Conclusion
Machining 3D printed metal components is an indispensable step in transforming printed parts into functional, high-performance components. By focusing on semi-finishing and finishing operations, manufacturers can enhance surface quality, achieve precise dimensional tolerances, and ensure mechanical integrity. This synergy between additive manufacturing and traditional machining unlocks the full potential of 3D printed metals, driving innovation and efficiency across various industries.
Tungaloy exemplifies this integration, not only with its expertise in machining 3D printed products but also through its pioneering use of 3D printing technology in production. This approach, as showcased by the drill bodies of the DrillMeister line, showcases Tungaloy’s ability to produce complex and precise components with reduced material waste and shorter lead times. Tungaloy’s dual mastery of additive and subtractive manufacturing techniques positions it at the forefront of the industry, providing advanced solutions to meet the rigorous standards of modern applications. By leveraging cutting-edge tools and technologies, Tungaloy continues to lead in transforming 3D printed metal components into high-performance, reliable parts for a wide range of industries.