Iwaki, Japan – March, 2025 – Tungaloy Corporation (President: Satoshi Kinoshita, Head Office: Iwaki City, Fukushima Prefecture) announces the expansion of its TungShortCut series with new 0.8 mm and 1.0 mm insert widths and a dedicated ModuMiniTurn head.
Designed for small-diameter part cut-off operations, this expansion offers enhanced machining stability and material savings. Compatible with 10 mm and 12 mm square shank holders, the ModuMiniTurn head enables easy replacement, reducing downtime and improving efficiency.
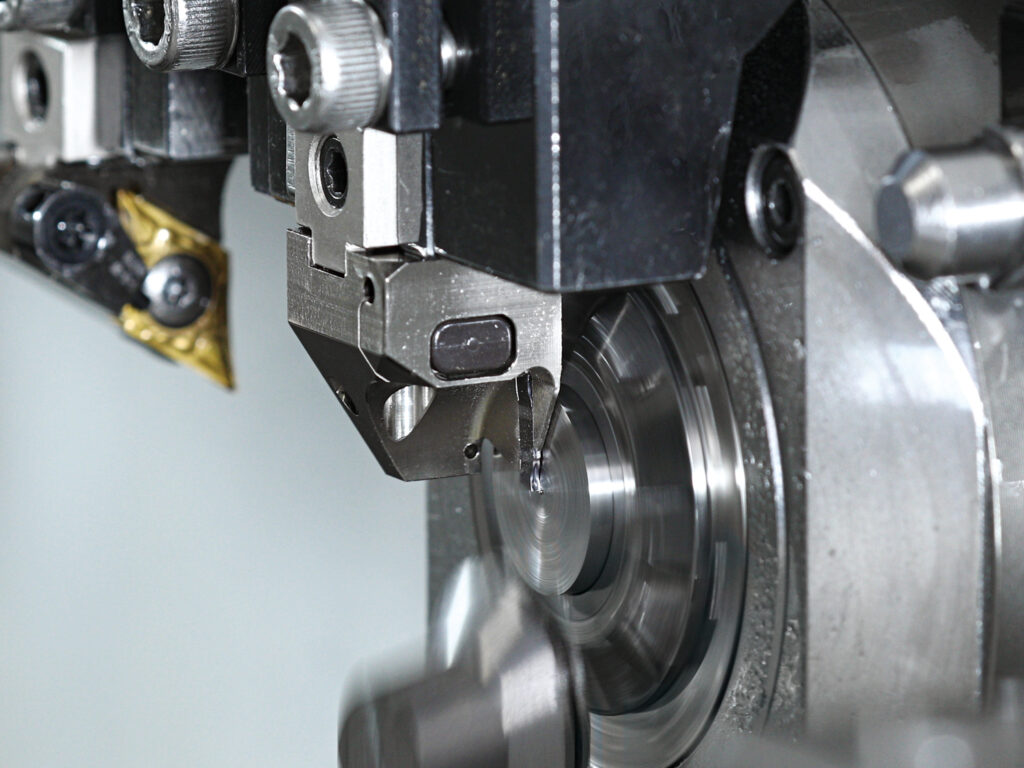
Challenges and Trends
In cutoff machining using automatic lathes, reducing material costs is a top priority, and there is a growing demand for inserts with narrow groove widths. This is particularly crucial in small-diameter component machining, where even a slight reduction in material usage can significantly contribute to cost savings. However, using inserts with narrow groove widths makes chip control more difficult, increasing the risk of deteriorating surface quality.
Furthermore, conventional screw-clamp inserts tend to have a longer overall length, leading to increased tool overhang. This results in a higher likelihood of chatter and stability issues during machining. To address these market needs, a new solution is required that enables higher precision and more stable machining.
Product Overview
TungCut is a high-performance tool specialized for grooving and parting-off operations. Its advanced grade selection system enables a wide range of machining applications, while the multifunctional series allows for tool consolidation. With exceptional insert clamping rigidity and a high-rigidity holder design, TungCut ensures stable tool life and precision. Additionally, its unique breaker geometry enhances chip control and suppresses vibrations. Featuring a unique insert clamping design, it offers both economic efficiency and high rigidity, delivering outstanding performance in various machining environments.
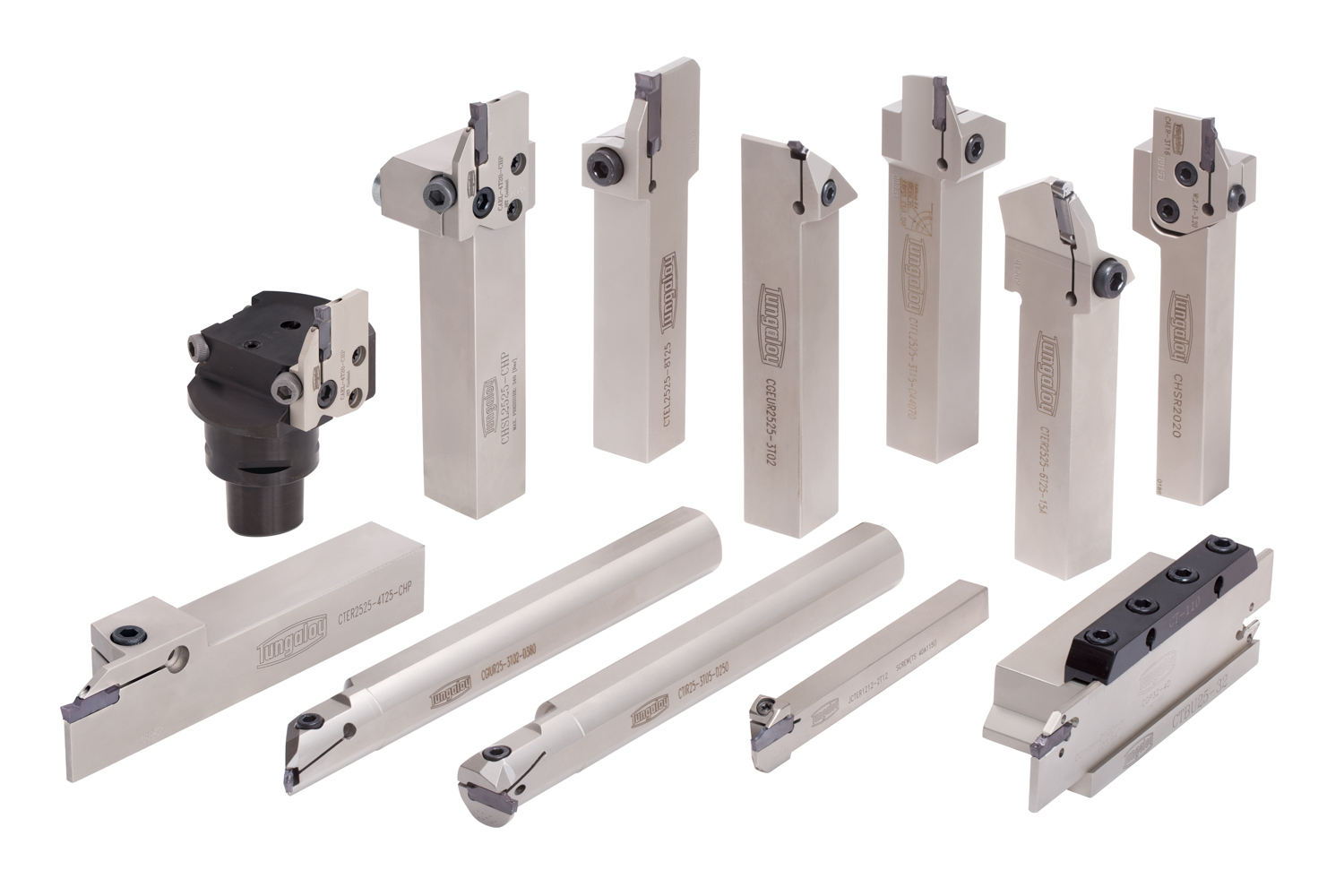
Benefits and Features
Feature 1: High-Precision Machining with 0.8mm and 1.0mm Insert Widths
Narrow insert width reduces material waste and lowers costs
Minimizes cutting resistance, preventing workpiece deformation and ensuring high precision
DGS chipbreaker design prevents chip entanglement, enabling stable chip control
Feature 2: Vibration Suppression with TungShortCut Combination
Short insert length minimizes tool overhang, reducing vibration
Higher rigidity compared to screw-clamp systems, ensuring stable machining
Compatible with current shank holders, ideal for small automatic lathes
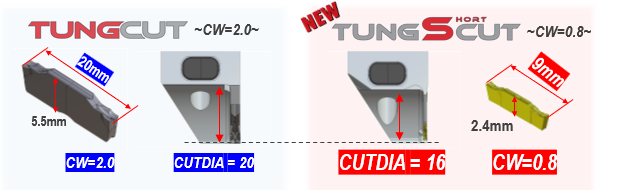
Feature 3: Improved Work Efficiency with ModuMiniTurn Head
Easy head replacement reduces tool change time and machine downtime
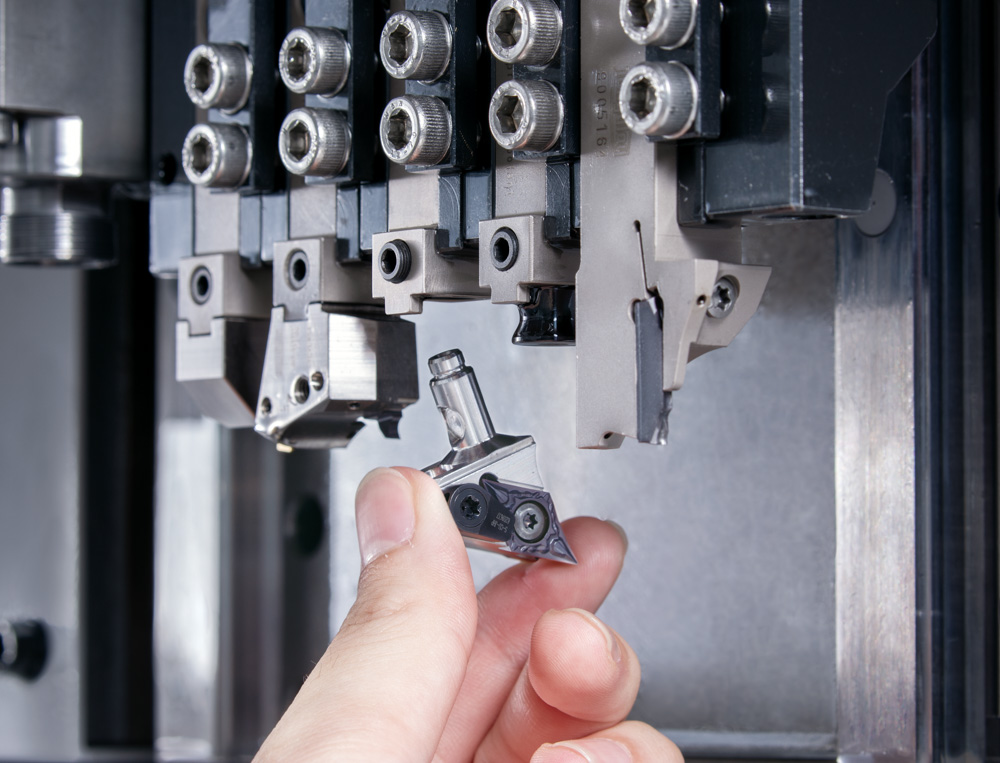
Success Stories
REDUCTION OF MATERIAL COSTS
Previously, parting-off was performed using a 1.5 mm width insert.
After switching to a 1.0 mm width TungShortCut insert, stable machining was achieved without issues such as chip evacuation problems or insert breakage.
By changing to a 1.0 mm width insert, a reduction in material costs became possible.
Industry | Engineering |
Component | Shaft Parts |
Material ISO code | M – Stainless steel |
Work material | SUS430 |
Machine(spindle type) | Swiss Lathe |
Tool family | Grooving |
Tool category | Parting off |
Product name | TungShortCut |
TSR No. | 5181T |
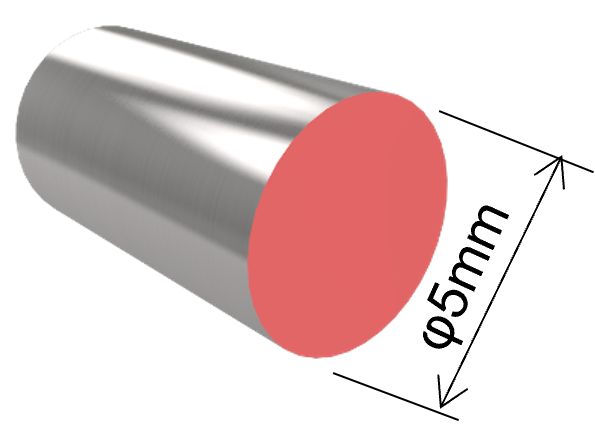
REDUCTION OF MATERIAL COSTS
Previously, parting-off was performed using a 1.2 mm width insert.
After switching to a 1.0 mm width TungShortCut insert, stable machining was achieved without issues such as chip evacuation problems or insert breakage.
By changing to a 1.0 mm width insert, a reduction in material costs became possible.
Industry | Automotive |
Component | Shaft |
Material ISO code | M – Stainless steel |
Work material | SUS430 |
Machine(spindle type) | Swiss Lathe |
Tool family | Grooving |
Tool category | Parting off |
Product name | TungShortCut |
TSR No. | 5182T |
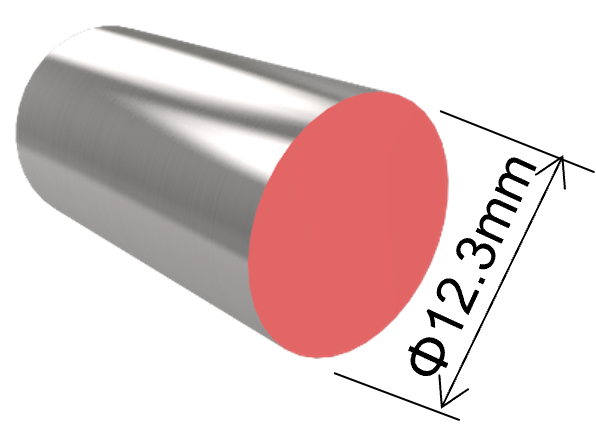