Iwaki, Japan – January, 2025 – Tungaloy Corporation (President: Satoshi Kinoshita, Head Office: Iwaki City, Fukushima Prefecture) announces the expansion of its TetraForce-Cut series with the addition of three new grades: AH7025 for superior wear and chipping resistance, AH8005 for high-speed machining, and AH6235 for interrupted machining, addressing diverse machining challenges while enhancing tool life and productivity.
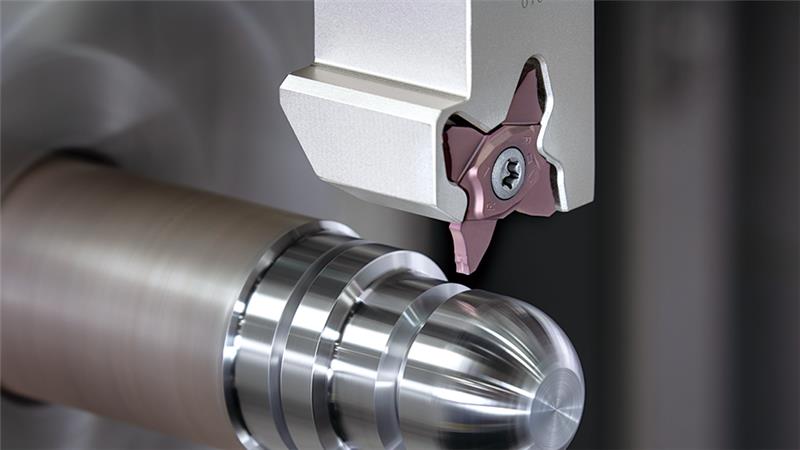
Challenges and Trends
In the automotive industry and small parts machining sectors, there is a growing demand for improving efficiency and reducing costs in grooving and parting-off operations. Specifically, challenges arise in external groove machining of shafts, machining of fuel nozzle components, fittings, and medical parts, where tool life becomes a critical issue. For grooving operations in interrupted cuts, the occurrence of burrs and instability in tool life hinder productivity improvements. Additionally, in parting-off operations, variations in insert lifespan are a significant concern for users. There is a strong demand for solutions that ensure high-quality finishes while controlling the increase in tooling costs. Against this backdrop, expectations are rising for tool grades that offer both enhanced durability and stability.
Product Overview
TetraMini-Cut and TetraForce-Cut are high-performance grooving and cut-off tools offered by Tungaloy. These tools are capable of handling a wide range of materials, including steel, stainless steel, and difficult-to-cut materials. They support groove width 0.3 – 4.0mm and depths of up to 10 mm. With their highly precise cutting edge positioning and cost-efficient 4-corner insert design, they deliver stable performance and excellent cost efficiency.
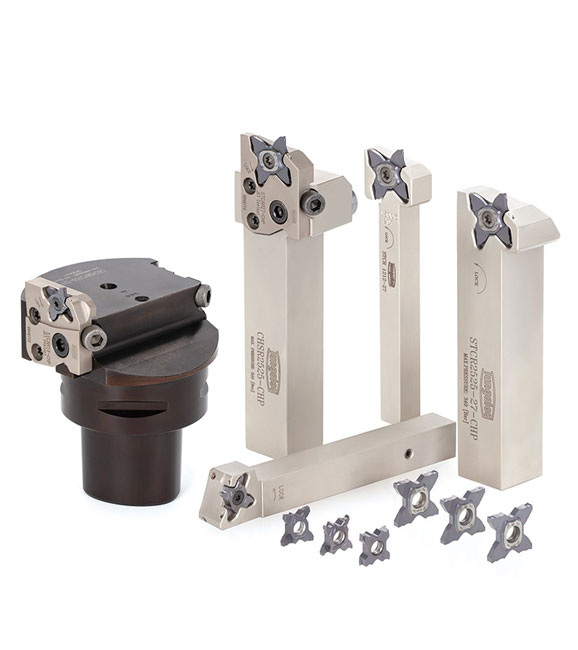
Benefits and Features
Feature 1: AH7025 – Striking a Balance Between Wear Resistance and Chipping Resistance
Utilizes a high-Al nano-layered coating to achieve both wear resistance and chipping resistance.
Employs a well-balanced carbide substrate, delivering stable performance across a wide range of machining conditions.
Highly versatile, suitable for various machining applications, contributing to the efficiency of tool selection.
Feature 2: AH8005 – Optimal Wear Resistance for High-Speed Machining
Features a high-hardness, high-Al coating and a wear-resistant carbide substrate for extended tool life.
Designed for use in high-speed machining and stable machining environments, enhancing productivity.
Excels under specific machining conditions, such as side cutting, supporting machining efficiency.
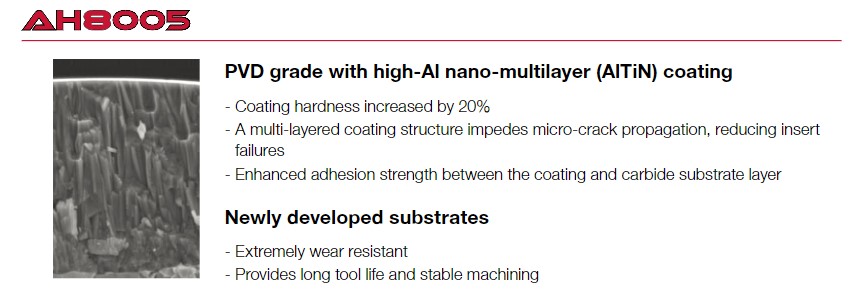
Feature 3: AH6235 – Enhanced Chipping Resistance
Incorporates a high-Ti nano-layered coating designed to suppress crack propagation.
Utilizes a high-toughness substrate to ensure stable tool life under harsh machining conditions, such as interrupted cutting or grooving.
Improves reliability in challenging machining scenarios, reducing machining costs.
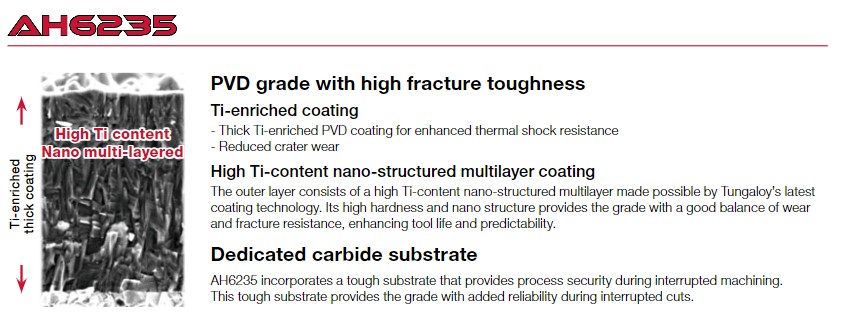
Success Stories
IMPROVED TOOL LIFE AND PRODUCTIVITY
Using a two-corner grooving tool for shaft components, the TetraForce-Cut was applied to this machining process.
Thanks to its high-rigidity clamping mechanism, cutting speed and feed rates were improved, achieving double the machining efficiency.
Additionally, tool life doubled compared to the previous tool, and with the increase to four corners per insert, tool life per insert was extended by four times.
The TCS breaker ensured stable chip control, enhancing machining reliability.
Industry | Automotive |
Component | Shaft |
Material ISO code | P – Steel |
Work material | SCM415 |
Machine(spindle type) | CNC Lathe |
Tool family | Grooving |
Tool category | External grooving |
Product name | TetraForce-Cut |
TSR No. | 5106T |
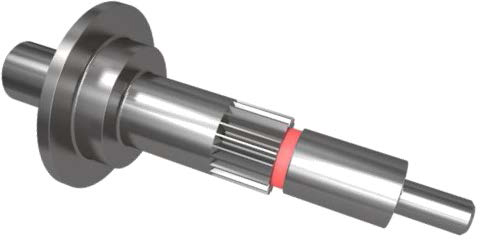
IMPROVED TOOL LIFE
A three-corner insert was previously used for machining brake covers on construction machinery. We proposed the TetraForce-Cut instead.
The workpiece material is FC250, and to improve tool life, the wear-resistant AH8005 grade was applied.
The latest AH8005 grade enhanced tool life by 1.5 times, and switching from the conventional three-corner insert to the four-corner TetraForce-Cut significantly improved tool life per insert.
Additionally, cutting speed was increased, contributing to higher machining efficiency.
Industry | Heavy |
Component | Brake cover |
Material ISO code | K – Cast iron |
Work material | FC250 |
Machine(Spindle type) | CNC Lathe |
Tool family | Grooving |
Tool category | External grooving |
Product name | TetraForce-Cut |
TSR No. | 5107T |
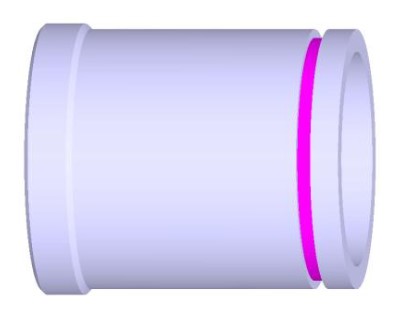