Unveiling Cutting-Edge CBN Machining Knowledge with Tungaloy´s CBN Premium Products
Dive into the world of CBN machining with Tungaloy’s premium turning products. This article explains the fundamentals of Cubic Boron Nitride (CBN), showcasing the technical intricacies shaping tool performance, and offers Tungaloy´s insights on selecting the right CBN solutions. Discover the latest trends in CBN technology, for higher performance and productivity.
Table of Contents
-
-
-
What is CBN?
-
Physical properties of CBN and its characteristics as a tool material
- CBN Properties and their Effects
- CBN Content and its Relationship to Wear and Fracture Resistance
-
Enhancing machining performance with Tungaloy’s latest tool shapes
- Unique Brazing Technology: Wavy Joint
- Edge Preparation (Honing)
- Tungaloy´s Hardbreaker Series
- Tungaloy’s Unique Periphery Geometry Inserts: GNGA/FNGA/YNGA
- MiniForce-Turn CBN Series for Internal Turning
-
Tungaloy’s CBN Grades and their properties
-
Questions or doubts about CBN Machining?
-
-
What is CBN?
Advances in technology across various industries such as automotive, aerospace, oil & gas, and medical, have led to the development of materials with superior heat resistance and wear resistance. Such cutting-edge materials enhance material durability but also present greater challenges for machining.
Generally, cutting tools require a hardness three times more than that of the material being cut. Thus, when machining high-hardness steel around 700Hv, the cutting tool must have a hardness of at least 2100Hv. Common hard cutting tools and inserts have a hardness of 1500Hv, which is insufficient for such high-hardness materials.
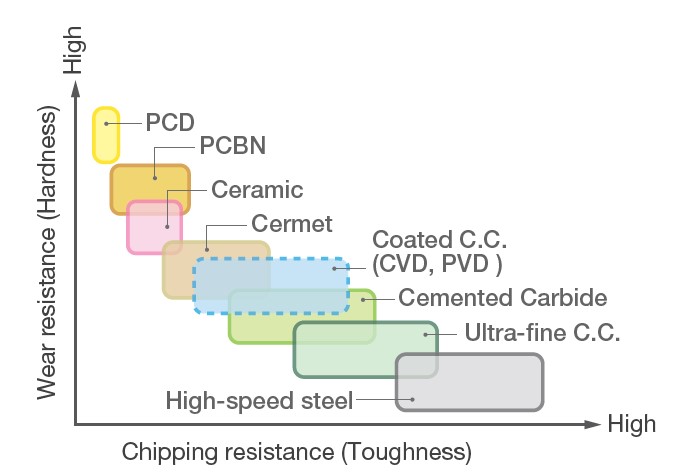
Tungaloy is one of the few companies that can manufacture sintered CBN (Cubic Boron Nitride), also known as cubic crystal boron nitride, in-house. This material is formed by compressing a compound of boron and nitrogen at very high pressure and temperature along with other bonding materials. It is the second hardest material known to humanity, surpassed only by diamond, with a hardness exceeding 7000Hv and very high thermal conductivity. CBN plays a crucial role in the high-speed machining of high-hardness steel, sintered materials, cast iron, and Inconel.
Physical Properties and Characteristics of CBN as a Tool Material
CBN Properties and their Effects
Property |
Effect |
---|---|
Second only to diamond in hardness | Excellent wear resistance, suitable for high-speed machining of hardened steel over 58HRc. Also suitable for cast iron and sintered materials containing abrasive particles, extending tool life compared to hard metals. |
Superior heat resistance – high thermal conductivity | The high thermal conductivity ensures effective heat dissipation from the cutting edge, crucial for machining hard materials like hardened steel and Inconel. |
Excellent chemical stability at high temperatures | Significantly reduces crater wear due to chemical reactions at high temperatures |
CBN Content and its Relationship to Wear and Fracture Resistance
CBN content (vol. %) plays a significant role in tool performance characteristics. CBN grades are produced by mixing CBN particles with ceramic or carbide binders. Tungaloy offers a range of CBN grades with CBN content ranging from 45% to 95%.
Selection Criteria:
- Lower CBN content improves wear resistance
- Higher CBN content improves fracture resistance
The lower the CBN content is, the more wear resistant the grade will be, and the higher the CBN content is, the more fracture resistant the grade will be when turning hardened steel.
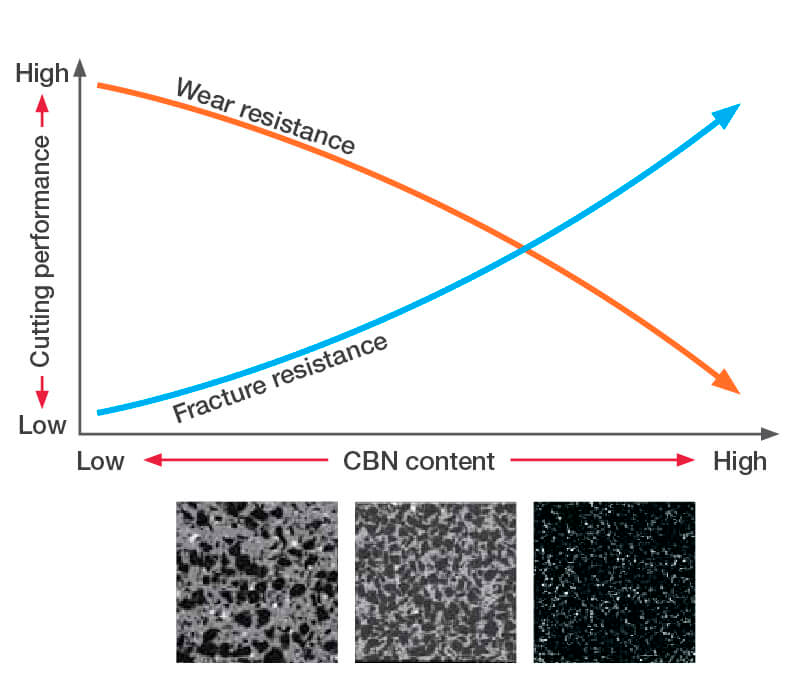
Enhancing Machining Performance with Tungaloy’s Latest Tool Shapes
While the performance of the CBN grade itself is important, Tungaloy also focuses on the development of the shape of CBN tools. Understanding the benefits of these latest technologies and selecting the right tool for each machining process can extend tool life, reduce tool costs, and improve machining efficiency.
Unique Brazing Technology: Wavy Joint
CBN inserts are manufactured by brazing CBN tips onto a tungsten carbide substrate. Given the high cutting resistance of hardened steel and heat-resistant alloy machining, it is crucial to join the brazing sections in a robust and highly heat-conductive manner to ensure longevity and stability.
Tungaloy uses a unique brazing technology known as the “Wavy Joint“. This technique increases the surface area of the joint by forming the joining part into a unique wavy shape. This not only increases the strength of the joint compared to traditional flat brazing methods but also enhances the heat dissipation due to the increased volume of CBN used, which is crucial for machining environments where cutting heat is significant.
Key Points of Tungaloy´s Wavy Joint
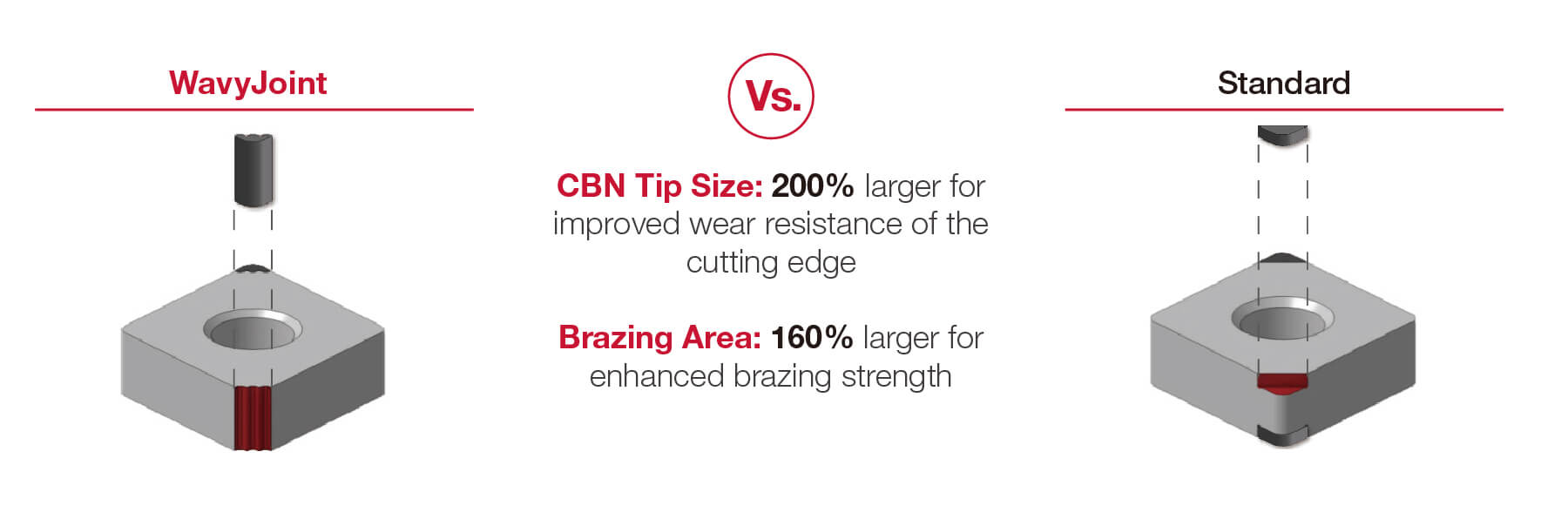
1. High Joining Strength
The conventional brazing method for CBN tips joins the bottom and side faces of a flat-formed tip. In contrast, the “Wavy Joint” technique creates a wave-shaped form, doubling the brazing area and resulting in a stronger bond.
Benefits of Increased Joining Strength:
- Improved stability during high-depth cutting operations
- Enhanced durability during interrupted machining processes, which typically involve repeated stress
2. High Thermal Conductivity
To manage the high heat from machining hardened steel, CBN inserts need efficient cooling. CBN’s high thermal conductivity, four times greater than hard metals, is key. The “Wavy Joint” technique doubles the CBN volume compared to conventional methods, enhancing heat dissipation. This is vital for reducing wear and extending tool life during high-speed, deep cutting.
Benefits of Improved Heat Dissipation:
- Efficiently dissipates cutting heat generated during high-speed machining, reducing crater wear and extending tool life.
- Increased joint strength also contributes to improved stability under high-speed and high-depth cutting conditions, enhancing machining efficiency.
Edge Preparation (Honing)
Honing on CBN inserts plays a crucial role in enhancing cutting performance and durability. By creating a blunt face near the cutting edge, known as a negative land, honing strengthens the edge, a process sometimes termed “edge killing.” Despite CBN’s high hardness, it is more prone to chipping than cemented carbides due to inferior fracture resistance. To counter this, larger honing is often applied compared to cemented carbide inserts. Tungaloy offers a range of honing specifications, including varying widths and angles of the negative land, tailored to specific machining needs, ensuring optimal performance.
Advancements in machining, particularly laser processing of hard materials, now allow for complex 3D chip breaker geometries on CBN inserts. These breakers enhance chip control and achieve angles previously challenging with CBN. Effective in processes prone to machine stops or vibration due to poor chip control or low workpiece rigidity, CBN inserts with chip breakers are recommended for such scenarios.
CBN inserts are commonly used for machining hardened steel components, such as automotive transmission parts. However, chips can get trapped between the insert and the workpiece, leading to potential damage and insert failures, especially near flanges or on end-face operations. To address this, Tungaloy offers inserts with a reduced corner radius, increasing clearance and reducing the risk of chip entrapment.
Features of the GNGA/FNGA/YNGA Inserts:
- Inserts with a unique corner angle smaller than standard ISO geometries
- Small corner angle ensures greater clearance between the cutting edge and the work material, reducing chip entrapment
- Despite their unique standards, these inserts are compatible with existing holders (CNGA/DNGA/VNGA), eliminating the need for holder replacement
- Effective solutions for sudden surface damage or short lifespan of inserts caused by chip entrapment
GNGA inserts allow smooth chip flow, preventing chip packing, enhancing surface finish, and minimizing cutting edge chipping.
Chip Control in Interrupted Face Turning
GNGA type – Corner angle: 70°
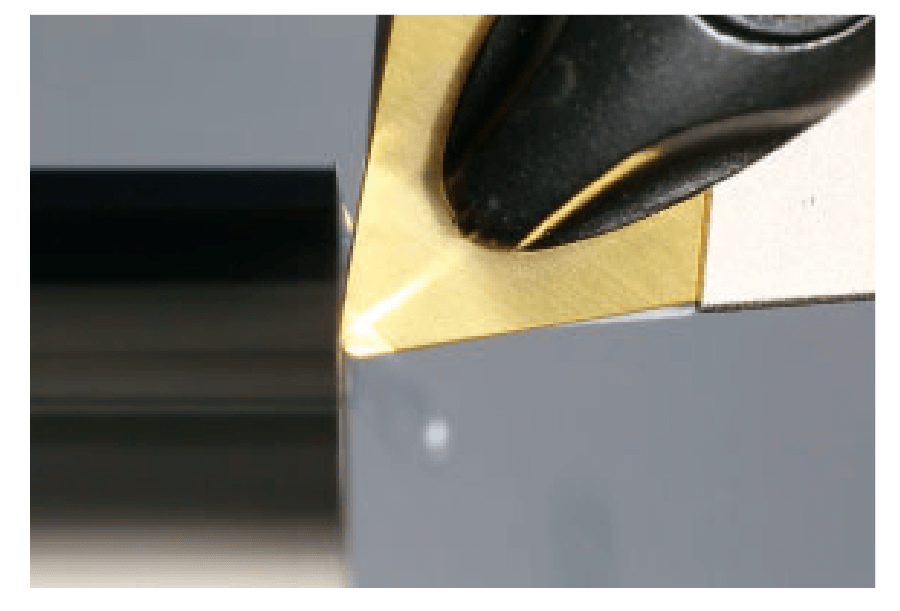
CNGA type – Corner angle: 80°
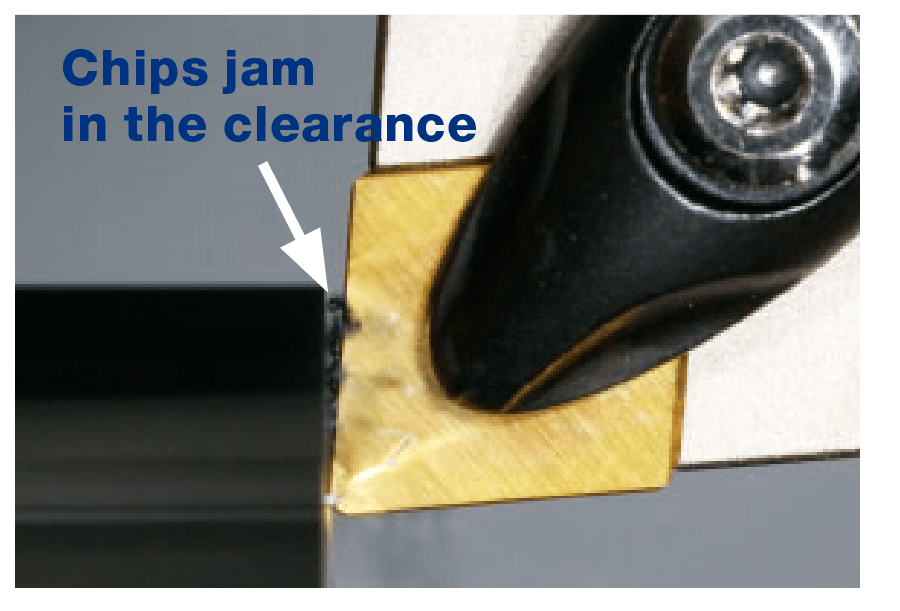
Comparison of Insert Damage Between GNGA (70°) and CNGA (80°) Inserts
- Reducing chip entanglement helps to minimize abnormal insert wear
MiniForce-Turn, is Tungaloy specialized series of internal turning tools distinguished by their unique insert designs. Within the MiniForce-Turn lineup, CBN inserts are integrated, enabling the utilization of multi-corner benefits in CBN machining applications. These tools feature exclusive insert shapes tailored for internal turning operations, offering double-sided six-corner inserts that excel in cost efficiency. Despite their double-sided configuration, the inserts boast a design and arrangement that ensures cutting resistance comparable to single-sided counterparts. Notably, transitioning from commonly used single-sided inserts can lead to significant cost savings. Furthermore, inserts equipped with breakers are strategically engineered to mitigate vibration during extended overhang operations on hardened steel, thereby reducing the occurrence of disruptive vibrations.
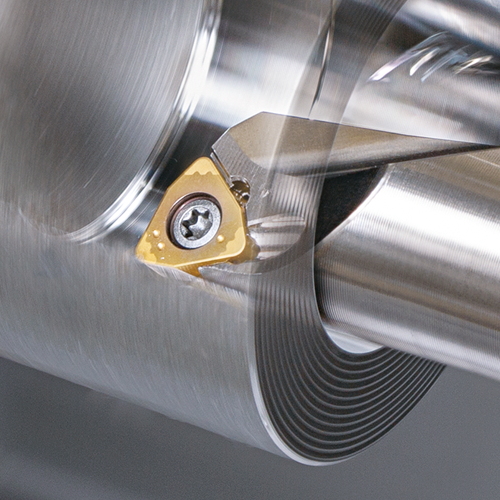
Tungaloy’s CBN Grades and their properties
Click on the below link to see the wide lineup of Tungaloy´s CBN Grades
Questions or doubts about CBN Machining?
Contact us through the below form and our experts will contact you to solve any inquiry that you may have.