Erfolgsgeschichten, die zeigen, wie die Vertriebsmitarbeiter von Tungaloy in enger Zusammenarbeit mit den Kunden zum Erfolg bei der Zerspanung beigetragen haben.
Ein Durchbruch beim Einrichten von Werkzeugen außerhalb der Maschine für Langdrehautomaten steigert die Produktivität beträchtlich
Vorgestelltes UnternehmenSuzuki Manufacturing Co., Ltd.
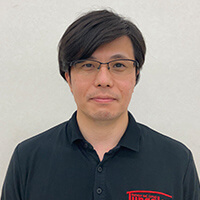
Vertriebsmitarbeiter
Kazuki Ishiguro
- Land
- Japan
Dies ist die Geschichte eines Kunden, der mit der Herausforderung konfrontiert war, Werkzeuge auf dem begrenzten Raum eines Langdrehers einzurichten, und wie eine externe Werkzeugeinrichtung seinem Unternehmen zum Erfolg verhalf. Suzuki Manufacturing Co., Ltd., mit Sitz in der Präfektur Yamagata, Japan, ist bekannt für seine Haushalts-Nähmaschinen und horizontalen Kopfkissenverpackungsmaschinen.
Im Jahr 1968 produzierte das Unternehmen die weltweit erste kompakte Nähmaschine namens “Babylock” für Handwerker und Haushalte. Mit kundenorientierten Geschäftsstrategien verbesserte das Unternehmen kontinuierlich seine Produkte und baute seinen Marktanteil aus. Auf der Grundlage des gesammelten Know-Hows begann das Unternehmen 1977 mit der Entwicklung und dem Verkauf von Verpackungsmaschinen für Kissen. Heute trägt das Unternehmen mit seiner einzigartigen Technologie und seinen leistungsstarken Produkten zu verschiedenen Industriezweigen bei, darunter Lebensmittel, Medizin und Landwirtschaft. Das Unternehmensziel von Suzuki Manufacturing Co., Ltd. ist es, sein Geschäft als “Yamagata-Marke” weltweit auszubauen und sich dabei auf eine kontinuierliche Entwicklung zu konzentrieren.
Inhalt
- Eine langjährige Geschäftsbeziehung
- Das Hindernis bei der Verbesserung der Effizienz eines Langdrehers
- Suche nach einer Lösung zur Bewältigung des Problems
- Möglichkeit der Werkzeugeinrichtung außerhalb der Maschine
- Etablierung des Verfahrens zur Messung der Schneidenposition und zur Durchführung von Korrekturen
- Erfolgreiche Reduzierung der Werkzeugrüstzeit
- Weitere Verbesserungen anstreben
Eine langjährige Geschäftsbeziehung
Herr Ishiguro, ein Tungaloy-Vertreter, und Herr Matsuda, der Werksleiter von Suzuki Manufacturing Co., Ltd., trafen sich zum ersten Mal 2018, als Herr Ishiguro das Unternehmen mit einem Händler, Taruishi, besuchte, um sich vorzustellen. Herr Matsuda unterhält eine langjährige Beziehung zu Tungaloy, und Herr Ishiguro ist bereits der fünfte Vertriebsmitarbeiter von Suzuki Manufacturing Co. Ltd.
Im Laufe der Jahre hat sich ihre Geschäftsbeziehung durch regelmäßige Besuche, Seminare und Ausstellungen vertieft; ihre Zusammenarbeit hat sich über den reinen Produktverkauf hinaus auf das Testen von Prototypen von Schneidwerkzeugen auf den Maschinen des Unternehmens ausgeweitet.
Das Hindernis bei der Verbesserung der Effizienz eines Langdrehers
Bei Suzuki Manufacturing Co. Ltd. werden Kleinteile für das Hauptprodukt, die Nähmaschinen, mit Langdreher im eigenen Haus gefertigt. Bei Langdrehern ist eine höhere Maschinenauslastung entscheidend für die Steigerung der Produktivität. Die zahlreichen Arbeitsschritte und die lange Zeit, die für das Auswechseln von Wendeschneidplatten und das Umrüsten der Werkzeuge benötigt wurde, hinderten das Unternehmen jedoch daran, die Maschinenauslastung zu verbessern.
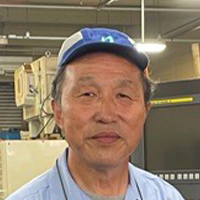
“Wir mussten Wendeschneidplatten wechseln und Werkzeuge in der Maschine einrichten. Das kostete Zeit und erforderte Präzision, so dass diese Aufgabe eine besondere Herausforderung für die neuen Maschinenbediener darstellte. Die Verbesserung des Werkzeugwechselprozesses in unseren Langdrehmaschinen war schon lange eine große Herausforderung für uns.”
Erforderliche Schritte zum Auswechseln der Wendeschneidplatten und Einrichten der Werkzeuge
So wechseln Sie die Schneide:
- Der Bediener setzt die Wendeschneidplatte wieder in die Maschine ein.
- Der Bediener löst die Schraube und entfernt die Wendeschneidplatte, während der Halter noch an der Werkzeugsäule befestigt ist.
- Der Bediener wechselt die Schneide und zieht die Schraube wieder an.
So wechseln Sie die Wendeschneidplatte und das Werkzeug:
- Der Bediener nimmt den Werkzeughalter von der Werkzeugsäule ab.
- Der Werkzeughalter wird aus der Maschine genommen, und der Bediener wechselt die Wendeschneidplatte aus.
- Der Bediener korrigiert die Position der Werkzeugspitze mit der unten beschriebenen Methode.
Methode zur Korrektur der Position der Werkzeugspitze
1. Einstellen der Kantenhöhe (Y-Achse)
- Legen Sie das Höhenreferenzmuster auf das Maschinenbett und stellen Sie die Messuhr auf Null.
- Messen Sie die Position der Werkzeugspitze des neuen Werkzeugs mit der Messuhr.
- Geben Sie die Differenz der Messung als Werkzeugkorrektur in der Y-Achse ein.
2. Einstellen der Längsmessung des Werkstücks (Z-Achse)
- Legen Sie das Höhenreferenzmuster auf das Maschinenbett und stellen Sie die Messuhr auf Null.
- Messen Sie die Position der Werkzeugspitze des neuen Werkzeugs mit der Messuhr.
- Geben Sie die Differenz der Messung als Werkzeugkorrektur in der Z-Achse ein.
3. Einstellen des Durchmessers (X-Achse)
- Setzen Sie das neue Werkzeug auf den Werkzeughalter.
- Ziehen Sie die Stange aus der Buchse heraus und lassen Sie die Schneide den Außendurchmesser berühren.
- Während die Schneide den Außendurchmesser berührt, ziehen Sie das Werkzeug mit einer Befestigungsschraube an und sichern es.
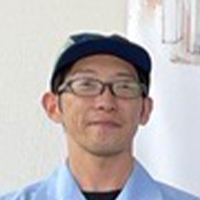
“Das Wechseln von Wendeschneidplatten und das Einrichten von Werkzeugen erforderte viele Schritte, und wir mussten aufpassen, dass wir keinen Fehler machten. Der begrenzte Platz im Inneren des Langdrehers machte selbst einfache Aufgaben wie das Wechseln von Wendeschneidplatten oder Haltern zu einer Herausforderung. Die kompakte Werkzeugsäule und der begrenzte Platz zwischen benachbarten Werkzeugen und in der Nähe der Buchse machten den Prozess ebenfalls komplizierter. Dies führte dazu, dass die Bediener häufig Wendeschneidplatten und Schrauben in der Maschine fallen ließen. Es war zeitaufwändig, sie zu suchen, und wir fanden einige von ihnen nie. Wie Sie sehen können, verschwendeten wir unsere Zeit und unser Geld. Dieser Zustand war schon lange ein großes Problem für uns.
Die Bediener mussten Wendeschneidplatten und Werkzeuge auf engem Raum in der Maschine wechseln.
Die Suche nach einer Problem-Lösung
Herr Ishiguro, Vertriebsmitarbeiter von Tungaloy, suchte nach einer Lösung für die Herausforderung, vor der Suzuki Manufacturing Co. Ltd. stand. Zu diesem Zeitpunkt wurde das neue Produkt ModuMini-Turn, das für Langdrehautomaten entwickelt wurde, auf den Markt gebracht. Das Werkzeug mit austauschbarem Kopf bietet hervorragende Bedienbarkeit und Bearbeitungspräzision. Es erlaubt dem Bediener, die Wendeschneidplatten zu wechseln, während der Schaft auf der Werkzeugsäule installiert bleibt. Sein einzigartiger Kupplungsmechanismus sorgt dafür, dass der Kopf sicher geklemmt wird, was eine hohe Präzision bei der Positionierung der Werkzeugspitze ermöglicht.
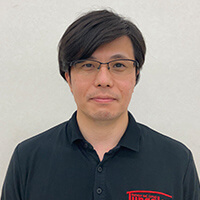
“Ich hatte eine Ahnung, dass ModuMini-Turn die Herausforderungen des Werkzeugwechsels bei Langdrehern lösen würde. Es wurde im September 2021 auf den Markt gebracht, und ich habe es sofort bei Suzuki Manufacturing Co. eingeführt”.
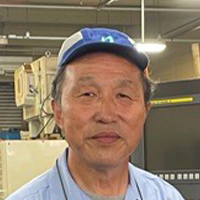
“Als ich von Herrn Ishiguro von diesem Werkzeug hörte, hatte ich auch das Gefühl, dass es unser Problem lösen würde. Um die Eigenschaften des Produkts zu nutzen, dachten wir, der beste Ansatz wäre das Wechseln der Wendeschneidplatten außerhalb der Maschine zum schnellen Wechseln der Werkzeuge, ohne dass die Position der Werkzeugspitze gemessen oder eingestellt werden muss.”
Möglichkeit der Werkzeugeinrichtung außerhalb der Maschine
Herr Matsuda war davon überzeugt, dass diese Idee ihre Engpässe lösen könnte, und begann, das Produkt zu testen. Der ursprüngliche Plan sah wie folgt aus:
- Entfernen des Kopfs vom Schaft in der Maschine (wobei der Schaft am Werkzeughalter befestigt bleibt).
- Vorbereiten des Ersatzkopfs mit einer bereits außerhalb der Maschine installierten Wendeschneidplatte.
- Befestigen dieses Ersatzkopfs auf dem Schaft in der Maschine und fortführen mit dem Bearbeitungsprozess.
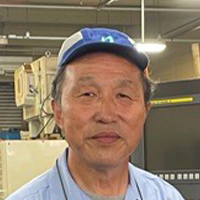
“Mein Hauptanliegen bei dieser Operation war die Präzision der Werkzeugspitzenposition (Spitzenhöhe, Durchmesser und Längsrichtung des Werkstücks). Wir bereiteten mehrere Kombinationen von ModuMini-Turn-Schäften und -Köpfen vor und maßen die Variabilität der Präzision der Werkzeugspitze. Leider lagen die Abweichungen nicht im geforderten Präzisionsbereich, insbesondere bei Wendeschneidplatten der Klasse M, die beim Pressformen verwendet werden und eine Abweichung von mehr als 0,1 mm aufwiesen. Wir haben diese Methode widerwillig aufgegeben.”
Auch wenn der ursprüngliche Plan nicht aufging, schienen dem Unternehmen die Einfachheit des Kopfwechsels und die Möglichkeit des Wechselns von Wendeschneidplatten außerhalb der Maschine attraktiv zu sein. Herr Matsuda sagt: “Wir wollten irgendwie einen Weg finden, um mit ModuMini-Turn Werkzeuge außerhalb der Maschine einzurichten.” Um dieses Ziel zu erreichen, beauftragte Herr Matsuda Herrn Tasaki aus der Produktionsabteilung mit der Leitung des Projekts.
Etablierung des Verfahrens zur Messung der Schneidenposition und zur Durchführung von Korrekturen
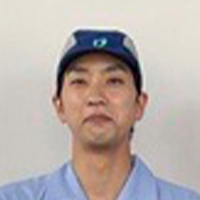
“Ich war mir sicher, dass sich unsere Produktivität erheblich verbessern würde, wenn wir eine Möglichkeit zum Einrichten von Werkzeugen außerhalb der Maschine sowie zum Messen und Korrigieren der Werkzeugspitzenpositionen schaffen könnten. Neben kleineren Problemen, wie dem Fallenlassen von Wendeschneidplatten und Schrauben innerhalb der Maschine, können die Werkzeuge in einem falschen Winkel montiert werden, was zu fehlerhaften Teilen führt. Wir hatten auch Fälle, in denen Werkzeuge aufgrund falscher Werte für die Werkzeugkorrektur in das Werkstückmaterial oder in die Buchse gerieten. Diese Probleme konnten zu erheblichen Verzögerungen im Produktionsplan führen, da die Zeit für die erneute Überprüfung der Präzision benötigt wurde. Um solche schwerwiegenden Probleme zu vermeiden, war ich bestrebt, eine Lösung für unsere Werkzeugeinrichtungsprozesse zu finden.”
Nach vielen Analysen und Tests findet Herr Tasaki schließlich den richtigen Weg.
Methode zur Korrektur der Position der Werkzeugspitze außerhalb der Maschine mit Hilfe von speziellen Vorrichtungen und Masterschaft/Masterkopf
So wechseln Sie die Schneide:
- Bereiten Sie eine spezielle Messschablone vor.
- Definieren Sie einen Master-Schaft und einen Master-Kopf, die als Standard für die Messung dienen, und verwenden Sie sie als Referenz für Eingabekorrekturen.
So korrigieren Sie die Position der Werkzeugspitze (X-, Y-, und Z-Achse):
- Befestigen Sie den Master-Kopf an dem Schaft, der in der Maschine installiert werden soll. Messen Sie dann die Unterschiede in der Spitzenhöhe (Y-Achse), im Durchmesser (X-Achse) und in der Längsrichtung des Werkstücks (Z-Achse) für jeden zu verwendenden Schaft im Vergleich zu den Werten der Kombination aus Master-Schaft und -Kopf.
- Nach der Messung installieren Sie den Schaft in der Maschine.
- Befestigen Sie die Wendeschneidplatte an dem Kopf, der in der Maschine verwendet werden soll, und montieren Sie diesen Kopf dann auf der Messvorrichtung.
- Mit dieser Einstellung messen Sie die Spitzenhöhe, den Durchmesser und die Längsposition entlang der Werkstückrichtung.
- Durch Addition der gemessenen Werte und der Differenzen zum Hauptschaft können Sie die endgültigen Korrekturwerte für die Eingabe der Werkzeugkorrektur berechnen.
Erfolgreiche Reduzierung der Werkzeugrüstzeit
Nach der Einführung des neuen Verfahrens verringerte sich die Zeit, die der Bediener für den Wechsel der Wendeschneidplatte und das Einrichten der Werkzeuge benötigte, drastisch. Der Prozess, für den ein erfahrener Bediener 8 Minuten benötigte, konnte auf 2,7 Minuten reduziert werden. Noch beeindruckender war die Veränderung für die neuen Bediener, die mit den alten Schritten 19 Minuten für die Arbeit benötigten. Mit dem neuen Verfahren benötigten sie nur noch 3 Minuten, was dem Zeitaufwand der erfahrenen Bediener sehr nahe kam. Die Einführung des neuen Werkzeugwechselverfahrens hat nicht nur die Umrüstzeit verkürzt, sondern auch dazu beigetragen, dass alle Bediener die Arbeit unabhängig von ihren Fähigkeiten erfolgreich durchführen konnten.
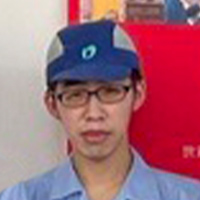
“Ich war immer besorgt darüber, dass ich für einen Werkzeugwechsel viel länger brauchte als meine älteren Kollegen. Wenn ich versuchte, es schneller zu machen, war die Wahrscheinlichkeit größer, dass ich Fehler machte. Die größte Herausforderung bestand darin, die Zeiteffizienz mit der Präzision der Arbeit in Einklang zu bringen, und mit der neuen Methode konnte ich die Aufgaben schnell und präzise erledigen. Außerdem konnte ich dadurch einen Teil meiner Zeit für andere Aufgaben nutzen und meine Arbeitseffizienz und -genauigkeit insgesamt verbessern.”
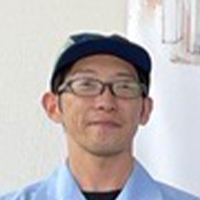
“Die Verkürzung der Werkzeugwechselzeit und die Standardisierung des Prozesses trugen erheblich zur Gesamtproduktivität der Produktionslinie bei. Durch die neue Arbeitsmethode ist es nicht mehr erforderlich, den Werkzeughalter während des Werkzeugwechsels zu bewegen, was dazu beiträgt, Kontaktprobleme zu vermeiden, da die nächste Bewegung der Bearbeitung dient. Zweifelsohne hat die Verringerung potenzieller Probleme zu einem stabileren Betrieb der Fertigungslinie geführt und meine Kopfschmerzen als Leiter der Fertigungslinie verringert.”
Entscheidende Verbesserungen
-
Erhöhte Maschinenauslastung durch reduzierte Werkzeugwechselzeit
Die Zeit für den Werkzeugwechsel, die zuvor 10-20 Minuten betrug, konnte auf etwa 3 Minuten reduziert werden, was zu einer besseren Maschinenauslastung beiträgt.
-
Standardisierung der Arbeitsabläufe für alle Bediener
Mit dem alten Verfahren gab es einen erheblichen Zeitunterschied zwischen den erfahrenen Mitarbeitern und den neuen Bedienern, um die Arbeit abzuschließen. Mit der Umstellung auf die externe Werkzeugbestückung mit ModuMini-Turn wurde der Prozess standardisiert, und die benötigte Zeit wurde unabhängig vom Qualifikationsniveau der Mitarbeiter.
-
Reduziertes Risiko von Fehlern und größeren Störungen und trägt zu einem stabilen Betrieb der Anlage bei.
Die externe Einrichtung minimierte den Maschinenbetrieb während des Werkzeugwechsels und reduzierte kritische Fehler, wie z. B. Kontaktunfälle, die durch die Eingabe falscher Werkzeugkorrekturwerte verursacht wurden. Dies half dem Unternehmen, seine Produktionslinien ohne Unterbrechung zu betreiben.
Weitere Verbesserungen sind geplant
Herr Matsuda, der Betriebsleiter, ist ebenfalls der Meinung, dass die Ergebnisse dieser Verbesserung dem Unternehmen erhebliche Veränderungen gebracht haben.
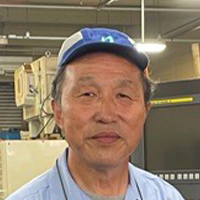
“Die Verkürzung der Werkzeugwechselzeit, die Standardisierung der Arbeitsabläufe und die Vermeidung von Störungen sind allesamt sehr wichtige Verbesserungen für die Fabrik. Ich möchte Tungaloy bitten, Werkzeuge zu entwickeln, die eine Bearbeitung ermöglichen, ohne dass die Position der Werkzeugspitze angepasst werden muss. Als Hersteller-Kollege verstehe ich, dass das eine Herausforderung ist, aber das war mein ursprüngliches Ziel und würde unseren Produktionsprozessen weiter helfen. In der Welt der Fertigung ist immer eine kontinuierliche Verbesserung erforderlich. Wir geben uns nicht mit dieser Verbesserung zufrieden, sondern wollen unsere Abläufe weiter automatisieren, um unsere Produktivität zu steigern. Mit der Automatisierung kommt der Bedarf an leistungsfähigeren Werkzeugen, wie z. B. Produkte mit einer stabilen Spanabfuhr für einen störungsfreien Betrieb und einer verlängerten Werkzeuglebensdauer für höhere Bearbeitungsraten.”
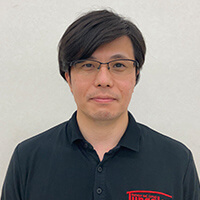
“Ich schlug der Suzuki Manufacturing Co. den ModuMini-Turn vor, aber sie zeigten mir, wie das Produkt über unsere Erwartungen hinaus eingesetzt werden kann. Ihre Strategie war selbst für unsere Ingenieure bei Tungaloy augenöffnend. Hersteller von Zerspanungswerkzeugen lernen oft wichtige Lektionen und finden neue Ideen durch die Endverbraucher, und ich bin dankbar, dass ich bei diesem Projekt mit Suzuki Manufacturing Co. zusammenarbeiten konnte. Diese Erfahrung hat mir gezeigt, wie wichtig es ist, auf das Feedback unserer Endkunden zu hören, es mit unseren Ingenieuren zu teilen und es in unsere Produktentwicklungen einfließen zu lassen. Ich möchte weiterhin eng mit meinen Kunden zusammenarbeiten und sicherstellen, dass ihre Stimmen in Tungaloy gehört werden.”
Bei Tungaloy engagieren sich alle Mitglieder für die Entwicklung und Lieferung von innovativen Schneidwerkzeugen, die unseren Kunden helfen, ihre Produktivität zu steigern.
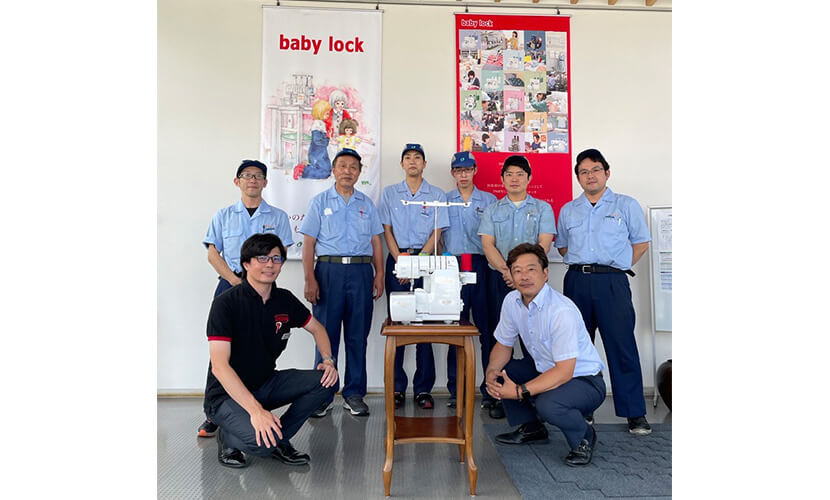
Vorgestelltes Produkt
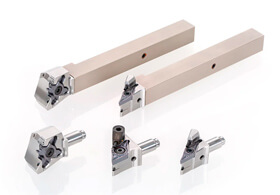
Drehhaltersystem mit modularen Köpfen für Langdreher
ModuMini-Turn
Erhebliche Reduzierung der Maschinenstillstandszeiten durch Werkzeug- und Einrichtungswechsel