Die Bedeutung des Tieflochbohrens in der Luft- und Raumfahrt, in der Automobilindustrie und im Die & Formenbau
Tieflochbohren spielt eine entscheidende Rolle in der Luft- und Raumfahrt, im Automobilbau sowie im Werkzeug- und Formenbau und gewährleistet die Präzision und Zuverlässigkeit von Schlüsselkomponenten wie z.B.:
- Flugzeugfahrwerke und Triebwerkskomponenten, die für Sicherheit und Leistung extreme Genauigkeit und Oberflächengüte erfordern.
- Kurbelwellen und Einspritzdüsengehäuse für die Automobilindustrie – anspruchsvolle Präzisionsbohrungen zur Gewährleistung von Haltbarkeit und Effizienz.
- Hydraulische Systeme und Getriebewellen – wo glatte, runde Bohrung für eine optimale Flüssigkeitsbewegung und mechanische Leistung erforderlich sind.
- Werkzeug- und Formenbau – Bohren von harten Materialien mit komplexen Geometrien, Querbohrungen und unterbrochenen Schnitten für Kühlmittelkanäle.

Das genaue und effiziente Tieflochbohren in diesen Anwendungen ist mit verschiedenen Herausforderungen verbunden, wie z.B. der Spanabfuhr, der Ablenkung der Bohrung und der Konsistenz der Bohrungsgenauigkeit. Herkömmliche Rundbohrmethoden führen häufig zu einem Verstopfen der Späne, übermäßigem Werkzeugverschleiß, hohen Bearbeitungskosten und einem komplizierten Nachschleifmanagement. DeepTriDrill Der Wendeschneidplatten-Bohrer von Tungaloy wurde entwickelt, um diese Herausforderungen zu meistern und die Produktivität zu verbessern.
DeepTriDrill: Die Lösung für präzises Tieflochbohren
DeepTriDrill bietet fortschrittliche Funktionen, die die Genauigkeit der Bohrungen, die Kontrolle der Späne und die Standzeit des Werkzeugs verbessern, was sie zur idealen Wahl für Anwendungen in der Luft- und Raumfahrt, der Automobilindustrie und im Werkzeug- und Formenbau macht.
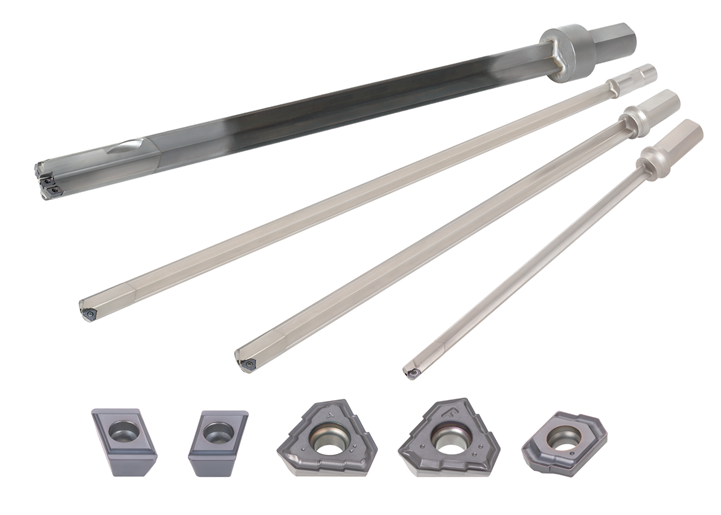
1. Span-Splitter: Optimieren Sie die Evakuierung von Spänen
Eine der größten Herausforderungen beim Tieflochbohren ist die effiziente Span-Absaugung. Eine schlechte Kontrolle der Späne kann zu Verstopfung, erhöhter Spindelbelastung und verkürzter Werkzeugstandzeit führen. Die Wendeschneidplatte des DeepTriDrill ist mit Spanbrechern ausgestattet, die die Späne in kleinere, besser handhabbare Stücke zerteilen. Dadurch wird ein Verstopfen verhindert und stabile Schnittbedingungen werden gewährleistet. Dies führt zu:
- Geringere Schnittkräfte für bessere Bearbeitungsstabilität und längere Werkzeugstandzeiten.
- Minimiertes Risiko von Spanverstopfungen, geringere Stillstandzeiten und höhere Produktivität.
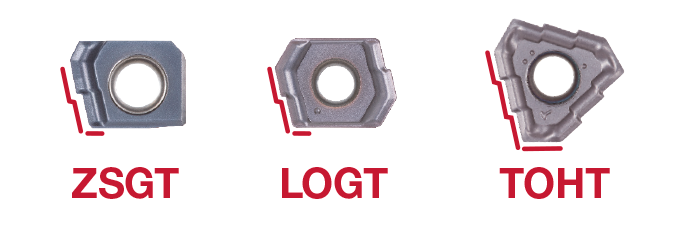
Außerdem hat jede TOHT-Wendeschneidplatte 3 Schneidkanten, und jede Kante ist mit einem Abstreifer ausgestattet, um die Oberflächengüte und die Geradheit der Bohrung zu verbessern.
2. Führungspads: Sicherstellung von Lochgenauigkeit und Stabilität
Die Aufrechterhaltung der Geradheit und Rundheit von Bohrungen ist für hochpräzise Komponenten in der Luft- und Raumfahrt, im Automobilbau und im Werkzeug- und Formenbau von entscheidender Bedeutung. DeepTriDrill ist mit Präzisionsführungsleisten ausgestattet, die das Werkzeug beim Bohren unterstützen, die Durchbiegung der Bohrung reduzieren und die Genauigkeit der Bohrung verbessern. Die wichtigsten Vorteile sind:
- Hervorragende Rundheit und Geradheit der Bohrungen, wodurch die Notwendigkeit eines zweiten Arbeitsgangs minimiert wird.
- Stabile Führung, auch bei hohen Vorschüben und Tiefen.
- Verbesserte Oberflächenqualität, unerlässlich für Anwendungen, die enge Toleranzen erfordern.
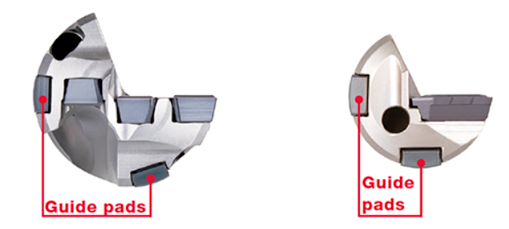
Um die Effizienz weiter zu steigern, haben alle Führungsleisten zwei nutzbare Seiten und sind mit einem doppelten Anfasen ausgestattet, um einen reibungslosen Eintritt in das Werkstück zu gewährleisten. Jede Führungsleistengröße ist in drei verschiedenen Hartmetallsorten erhältlich, die Flexibilität für verschiedene Materialien und Bearbeitungsbedingungen bieten.
3. Reduzierung der Schnittkraft & optimierte Spanbildung
Tieflochbohren erfordert eine präzise Kontrolle der Schnittkräfte, um eine stabile Bearbeitung und eine lange Standzeit der Werkzeuge zu gewährleisten. Jede wendeschneidplatte ist mit einem Spanformer ausgestattet, der beim Bohren kurze, überschaubare Späne bildet.
DeepTriDrillDas Standardsortiment umfasst zwei Arten von Spanformern für jede wendeschneidplatte:
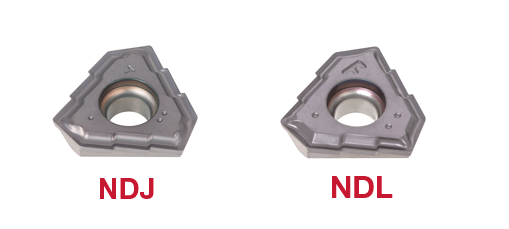
Diese Vielseitigkeit stellt sicher, dass die Hersteller den besten Spanformer für ihre spezielle Anwendung auswählen können, um die Effizienz und die Standzeit der Werkzeuge zu erhöhen.
4. Vordere Kühlmittelzufuhr: Verbesserung der Standzeit der Werkzeuge und der Spanabfuhr
Die Zufuhr von Kühlmitteln ist beim Tieflochbohren von entscheidender Bedeutung, um Überhitzung zu vermeiden, die Standzeit des Werkzeugs zu verlängern und eine effiziente Spanabfuhr zu gewährleisten. DeepTriDrill verfügt über innere Kühlmittelzufuhren an der Vorderseite, die eine ordnungsgemäße Kühlung, Spanabfuhr und konstante Leistung gewährleisten. Das Ergebnis ist:
- Verlängerte Standzeit der Werkzeuge durch Reduzierung der Wärmeentwicklung.
- Verbesserte Span-Absaugung für unterbrechungsfreies Bohren.
- Höhere Stabilität beim Bohren für hochpräzise Anwendungen.
5. Hochleistungs-Wendeschneidplatten-Sorten für vielseitige Anwendungen
DeepTriDrill ist in zwei Standardsorten erhältlich, um eine breite Palette von Bearbeitungsanforderungen zu erfüllen:
- AH9130 – Hohe Verschleißfestigkeit, entwickelt zum Bohren verschiedener Materialien.
- AH725 – Gutes Gleichgewicht zwischen Verschleiß- und Zerspanungsfestigkeit, geeignet für die Bearbeitung von Stahl und rostfreiem Stahl unter allgemeinen Zerspanungsbedingungen.
Diese Sorten gewährleisten eine optimale Leistung in verschiedenen Anwendungen und bieten zuverlässige Verschleißfestigkeit und Langlebigkeit.
Bewährte Leistung in der Branche
DeepTriDrill wurde erfolgreich in verschiedenen Anwendungen in der Luft- und Raumfahrt, im Automobilbau und im Werkzeug- und Formenbau eingesetzt und hat dabei die Effizienz der Bearbeitung, die Standzeit der Werkzeuge, die Präzision der Bohrungen und die Kostenreduzierung im Werkzeugmanagement verbessert. Nachfolgend finden Sie echte Fallbeispiele, die die Auswirkungen auf die Produktionsleistung zeigen:
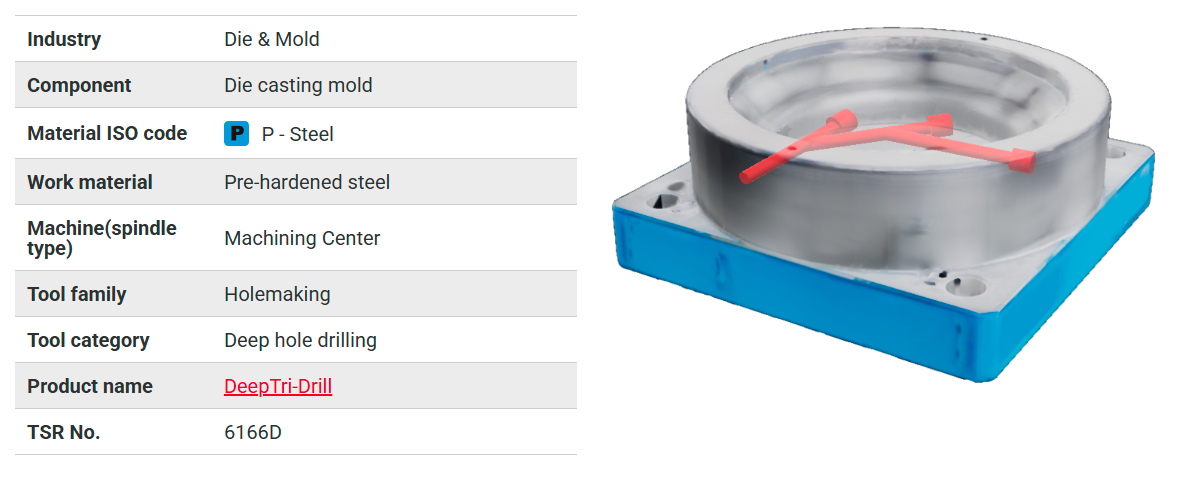
Durch das Ersetzen eines herkömmlichen Spatenbohrers durch DeepTriDrill mit doppelten Führungsleisten konnte ein Kunde erfolgreich Probleme bei einer schwierigen Querbohrung lösen. Das Upgrade führte zu einer 3,5-fachen Produktivitätssteigerung sowie zu einer deutlichen Reduzierung der Zykluszeit, des Werkzeugbruchs und der Maschinenstillstandszeiten.
Mit optimierten Schnittbedingungen – 1200U/min Spindeldrehzahl, 54 mm/min Schnitttiefe und 70 mm/min Vorschub –hatDeepTriDrill hervorragende Leistung und Prozessstabilität bewiesen. Das macht sie zu einer idealen Lösung für die Bearbeitung von vorgehärtetem Stahl bei Anwendungen in Druckgussformen.
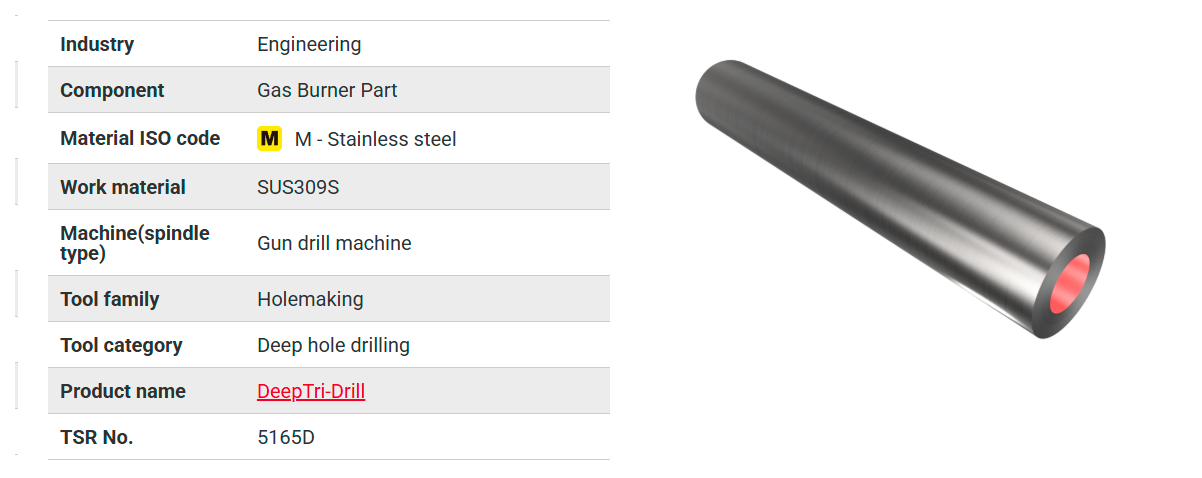
Bei der Bearbeitung von SUS309S-Gasbrennerteilen führte der Wechsel von einem herkömmlichen gelöteten Bohrer zu DeepTriDrill zu einer 3-fachen Steigerung der Produktivität beim Bohren geführt. Durch die Erhöhung des Vorschubs auf 0,03 mm/U konnte die Vorschubgeschwindigkeit deutlich verbessert werden, was zu sauberen Löchern, kurzen Spänen und minimalen Schnittgeräuschen führte. Die verbesserte Spanabfuhr trug weiter zur Prozessstabilität und Effizienz bei und führte zu einem leiseren, saubereren und zuverlässigeren Betrieb.
Warum Hersteller wählen DeepTriDrill
Mit steigenden Anforderungen an Präzision, Effizienz und Kosteneffizienz, DeepTriDrill einen Wettbewerbsvorteil, indem es Folgendes bietet: ✅ Optimierte Span-Kontrolle beim Tieflochbohren. ✅ Längere Standzeiten durch austauschbare wendeschneidplatten, die die Bearbeitungskosten senken. ✅ Hervorragende Rundheit und Geradheit, minimiert die Nacharbeit und verbessert die Qualität der Teile.
Die Luft- und Raumfahrt, die Automobilindustrie und der Werkzeug- und Formenbau streben nach immer höherer Präzision und Produktivität, DeepTriDrill ist die ideale Lösung für Hersteller, die Tieflochbohren verbessern möchten.
Entdecken Sie DeepTriDrill noch heute und erleben Sie mehr Effizienz, Genauigkeit und Kosteneinsparungen.