タンガロイ成功事例
ポリゴンカップリングツーリングシステム『TungCap』を活用し、
工具交換時間を大幅削減。
ライン増設でさらなる生産性向上に寄与
ダイナックス工業(株)
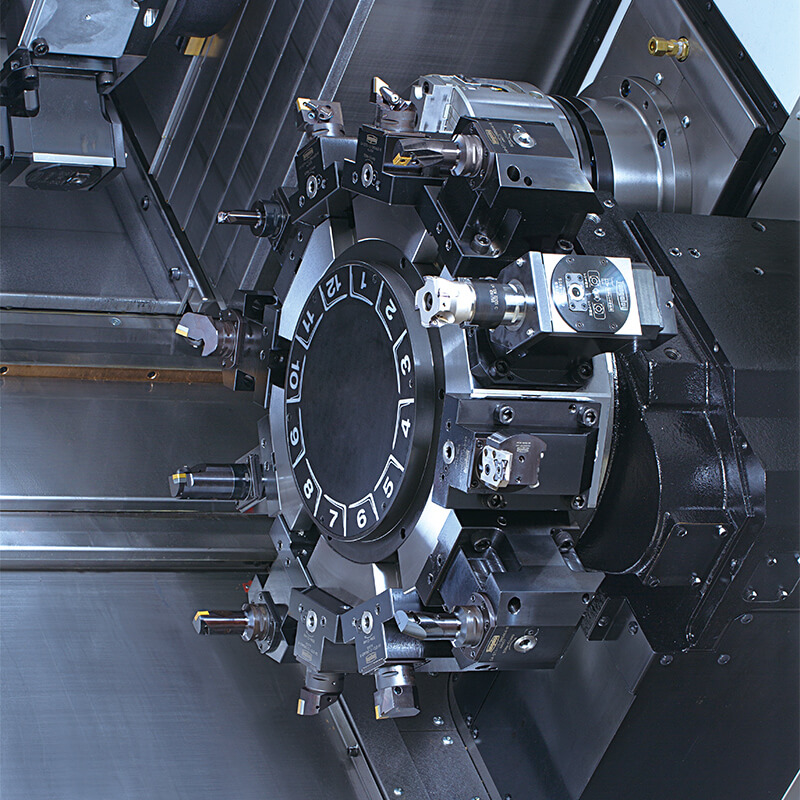
本記事は機械技術2022年5月号掲載分をWeb用に再編集したものです。
高い位置決め精度が求められる切削加工では主軸と工具をつなぐツーリングが重要な役割を担う。特にNC旋盤や複合加工機における高能率化、高精度化の要求が増す中、工具交換を迅速に行い高い繰り返し精度を出すことが大きな課題となっている。部品加工を手掛けるダイナックス工業(株)(兵庫県姫路市)は、NC旋盤に使うツーリングを見直すことでリーマ加工の段取り替えの大幅な効率化を進めている。㈱タンガロイのポリゴンカップリングツーリングシステム『TungCap(タング・キャップ)』を採用し、従来40分かかっていた工具交換を5分以下に短縮。量産化ラインの増設に合わせさらなる生産性向上に取り組んでいる。
鍛造から機械加工の一貫生産体制
ダイナックス工業は1925年に児島鉄工所として創業。100年近い歴史を持つ老舗企業である。熱間鍛造をコア技術に冷間鍛造、切削へと加工領域を広げ、自動車やバイク、農業機械などの部品加工の一貫生産体制を整える。1951年に法人化し、その後、大手電機メーカーとの取引開始を機に業績を拡大してきた。2015年にはタイに合弁会社を設立して海外事業に着手する一方、16年には会社のロゴに使用していた「ダイナックス」を活かしてダイナックス工業㈱に社名を変更して現在に至っている。
同社の特徴は祖業である熱間鍛造を中心に顧客の要望で切削や冷間鍛造といった加工技術を導入し、塑性加工と除去加工の両方を活かした製品提供を行える点にある。近年は自動車電装部品の主軸シャフト、動力を伝達するプーリやEPSカップリングボスを主力にバイク、農機部品なども生産。さらに20年にはプラグインハイブリッド(PHEV)向けのMOTシャフトの自動生産ラインを導入するなど電気自動車(EV)や自動車の電動化に対応した体制強化に乗り出している。
工具交換の効率化が課題
そうした背景の中、この数年急成長しているのがEPSカップリングボスである。電動パワーステアリングに採用される部品で16年から生産に着手。自動車の電動化を背景に量産が進み、現在14ラインが稼働している。ラインはプレス加工された支給材をOP1と呼ぶ外径、内径の切削とOP2での外径の仕上げおよび内径面取りの2工程で加工し、測定検査を経て完成品となる。量産化に向けて検査工程を自動化するなど省人化を図っているものの、大きなネックとなっていたのがOP1でのリーマ加工における工具交換であった。
「内径の寸法精度が同軸度3μm以内の指定があり、導入当初から課題になっていました。機械設置当初のチャンピオンデータでは精度を出せても工具を交換するたびに測定しながら調整する必要があり、腕の良いベテランでも30分以上かかる。実際、別の部署から配属されたばかりの私自身の体験では主軸の芯だしに4時間以上かかりました」と北野典明第一製造部次長(兼)部品工作課課長は振り返る。北野次長は21年10月に品質保証課から現在の部署に異動してきた。「ホルダーの締め込みなどの誤差がすべて先端に現れてくる」ことを実感したという。主軸の振れによって不良品が生じるほか、うまく加工できたとしても工具の接触位置の偏りが工具寿命を半減することにもつながる。
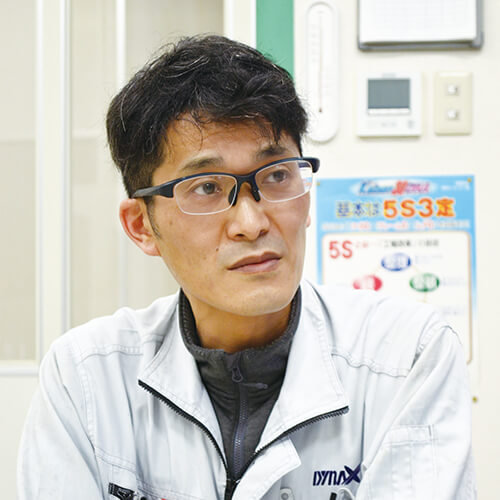
(兼)部品工作課課長北野 典明氏
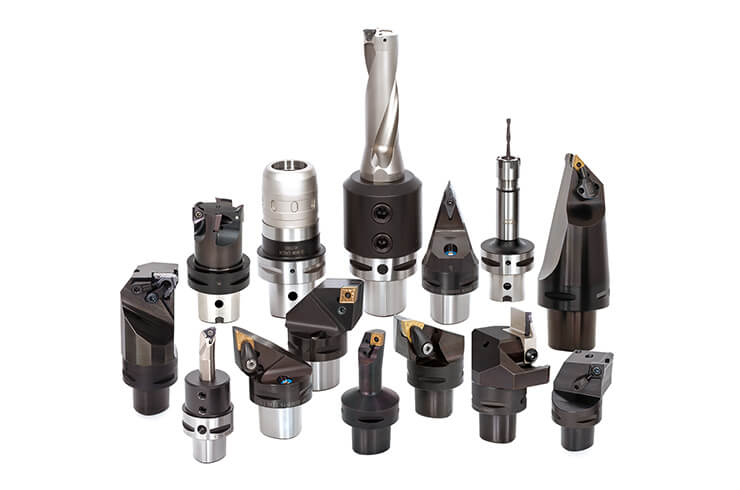
MTBのサポートで特殊仕様にも迅速に対応
『TungCap』はポリゴンテーパとフランジ端面の2面拘束により高クランプ剛性を実現したツーリングシステムである。ポリゴン形状により切削トルクが均等配分され、センタリング機能を向上。同一工具交換時の繰り返し刃先位置精度は±2μm 以内を実現している。誰でも容易に工具の取り外しが行え、工具交換時間の大幅な短縮を可能にする。
採用の決め手となったのが、タンガロイと高松機械工業の迅速な対応であった。タンガロイでは工作機械や周辺機器メーカーと連携し、顧客の課題解決を展開するMTB(マシンツールビルダーズ)を12年から組織。今回もダイナックス工業から要望があった「芯高調整」の特殊仕様についてMTBと高松機械工業が密に連絡を取り、約3カ月の短納期で対応できたことが評価された。
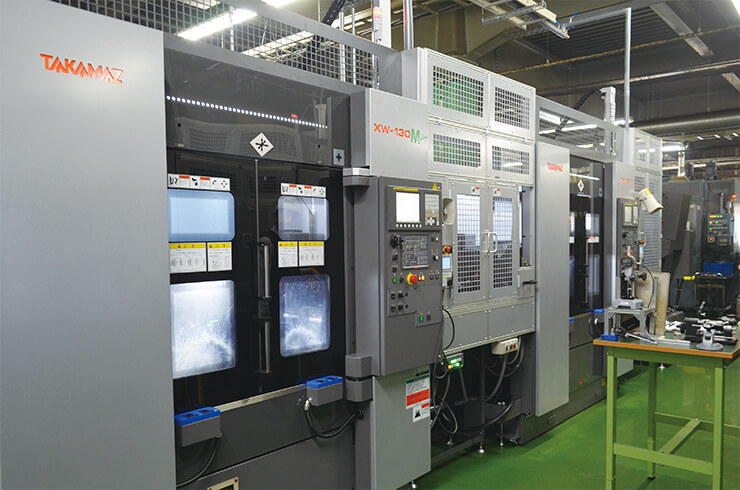
同社とMTBグループの密な連携で、特殊仕様にも迅速に対応。
21年7月に納入したところ繰り返し精度に問題がなく、工具交換時間は数分で行えるようになった。実際、16ラインで試算した場合、月間の稼働日数21日で計算するとツール交換間隔2.8日に1回として工具交換調整作業が1回40分だったものが5分に短縮することで、月間の交換時間は70時間短縮でき、生産台数では6212台アップすることがわかった。
同社では21年7月に2機に搭載したのをはじめ既存のラインへの後付けを進める一方、22年2月に導入した新ラインでは装着済みの機械を購入。今後、バリ取り工程を集約した複合加工機を導入していく予定で、高松機械工業からダイナックス工業仕様として納入されることになる。
「計画では現在の14ライン月産50万台から来年初旬までに18ライン月産65万台体制に増設する予定で、年内には既存ラインのすべてに『TungCap』を導入します。工具交換を平準化することで初心者とベテランとのばらつきがなくなり、不良の心配がなくなりました。ラインの増加に伴い初心者の作業員も増える中、効果はさらに大きくなると見ています」(北野次長)。高精度、高効率なモノづくりに意欲を示す。