タンガロイ成功事例
工具管理・コスト低減システム
「MATRIX」を導入し、
チップ交換時間を大幅に短縮
(株)石井機械製作所
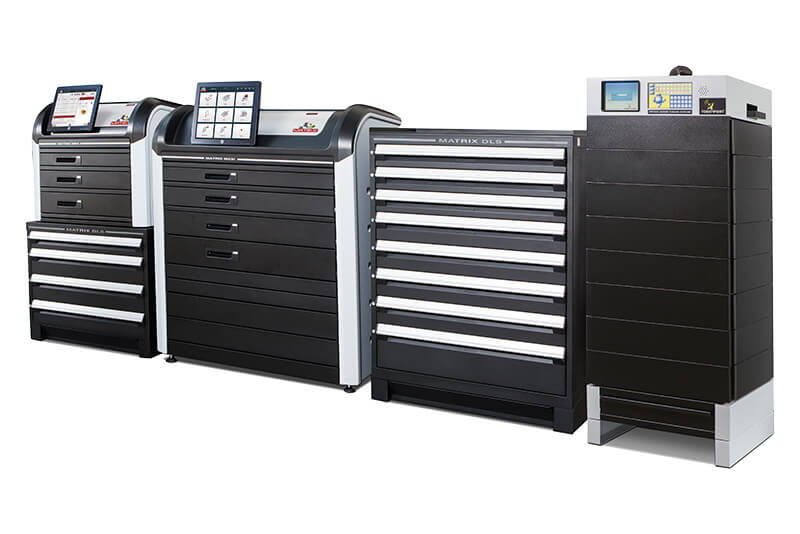
※本記事は型技術2022年3月号掲載分をWeb用に再編集したものです。
製造現場において工具管理の重要性が改めて見直されている。工具の整理整頓による交換時間の短縮、使用履歴を踏まえた適正な在庫管理など生産性向上とコスト削減に大きく寄与するためだ。自動車や医療機器などの部品加工や治具製作などを主力に展開する(株)石井機械製作所(栃木県足利市)は、(株)タンガロイの工具管理・コスト低減システム「MATRIX(マトリックス)」を導入し、段取り時間の削減に大きな成果を上げている。工具の保管場所を特定して常に在庫状況を把握することで、工具を探し回ることなく、迅速な工具出庫を実現。活用工具の見直しや原価改善にも寄与しつつある。
創業134年の老舗企業
石井機械製作所の創業は1888年。織機用木製部品の加工からスタートし、自動車や産業機械、航空機、医療機器などへと業容を広げてきた134年の歴史を誇る足利市屈指の老舗企業である。
試作品をはじめとする単品物を得意とし、部品加工だけでなく顧客の要望に沿った部材や治工具の設計も手掛け、図面の作成から切削、組立までの一貫生産体制を構築。汎用フライス、中小型マシニングセンタ(MC)、門型5軸MCなどを揃え、手のひらサイズから大物製品まで対応できる設備を整える。近年は単品物に加え量産物の比重を高め、電気自動車(EV)向けのユニット装置や医療機器のリピート品などが好調に推移。コロナ禍での航空機分野などの落ち込みをカバーし、堅調に業績をキープしている。
同社の5代目となる石井大洋社長は「当社の強みは自前で工具をつくれる熟練の技とチャレンジ精神。お客様の要望にとことん寄り添い『ここに任せればやってくれる』という信頼関係が今につながっています」と時代に応じた課題への挑戦の積み重ねが幅広い市場で顧客を獲得し、その結果、景気に左右されにくい事業基盤をつくりあげてきたと自負する。
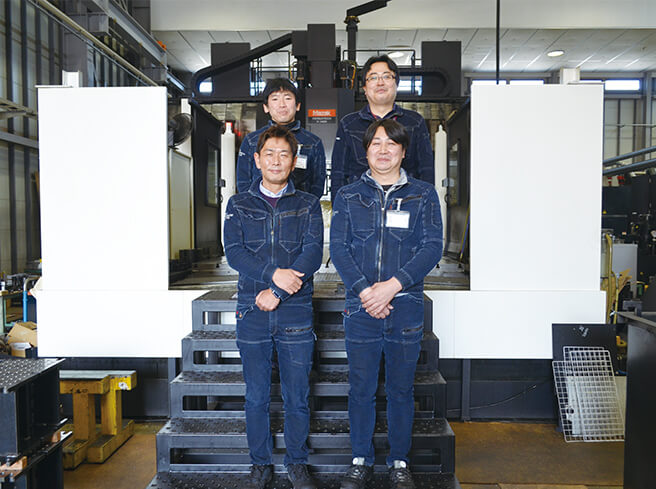
MATRIXの導入で5Sを深化
ベテラン、若手のモチベーションを引き出すユニークな取り組みも目立つ。その1つが「オーケストラファクトリー」である。自社のモノづくりを合奏になぞらえ「大勢の観客に感動を与えるオーケストラのように飛躍し続けるために」との思いが込められている。そしてその基礎となるのが「足利流5S」活動である。「整理・清掃・(整列)・整頓・清潔・しつけ」による改善活動を通じて同社のモノづくりを常に見直し、労働環境改善、地域社会の貢献にも結び付けていく取り組みだ。
タンガロイの工具管理・コスト低減システム「MATRIX」の導入もこうした改善活動の一環として始まった。「従来は工場内の整備などマクロ的な5Sが中心でした。さらに成果をだすためにミクロな5Sを徹底する必要があると判断しました」と石井社長は振り返る。その第1弾として着目したのが工具管理だった。
それまで同社では工具管理は作業者各自に任されていたため、工具の置き場所や在庫量の情報が共有されず、必要な工具を探し回ったり、発注し忘れたりといったケースが度々あった。改善の課題として挙がっていたものの「本社工場だけで何千種類もあり、手つかずになっていた」(田中茂則生産技術Gr・航空宇宙Grリーダー ピアノグループ)のが実情であった。
そこで注目したのがMATRIXだった。MATRIXは工具を収納するキャビネットと工具管理システムのハードとソフトで構成。現場での工具出庫作業と在庫管理業務を自動化し、各種履歴データを業務改善にも活かせる工具管理システムである。キャビネットの引き出し(トレイ)に工具1つひとつの所定地を設定。出庫の際はタッチパネルでアイテムや数量を打ち込むか、バーコードを読み取らせると該当するトレイが光って施錠が解除される。トレイを引くと内部収納コンテナから指定したアイテムのみが取り出せる仕組みである。
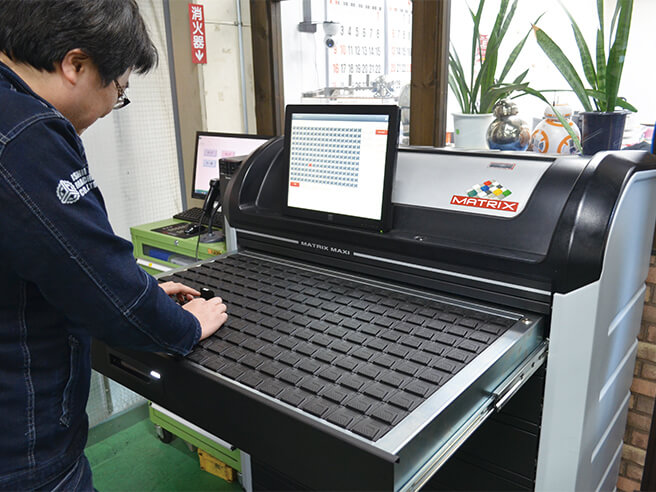
「数社のシステムと比較して格納庫にロック機能があることが検討の決め手となりました」(同)。日頃付き合いのあるタンガロイの代理店㈱かなめ商工(栃木県足利市)に相談し、ショールームでの実機を見学したのち、本社工場を対象に現場アンケート(18人)を実施。そこで1日あたりの工具探し/出庫に要する時間が平均530分との試算結果が出された。これを1カ月の稼働日数(20日)として1年で127,200分。仮に時給1,000円で換算したとして、2,120,000円のロスが発生する計算となり、「当社で導入すればさらに効果がでる」(同)と確信した。
在庫管理による工具量の最適化に期待
この試算結果を踏まえ石井社長からもMATRIXの導入を了承。3カ月の準備期間を経て2021年6月から運用を始めた。最初はチップのみを対象にして作業者の机の引き出しに入っている工具を選別して約600種類をMATRIXに登録した。運用を始めると現場からの評判も良かった。「工場では以前からバーコードリーダーを活用していたので、MATRIXにも抵抗なく移行できました。工具を探し回ることもなくなり、欠品もゼロとなりました」(田所達也製造本部技術Gr・ピアノグループ)と早くも手ごたえを感じている。すでにチップに加え、エンドミルにも適用を広げ、在庫が一定量減ると自動的に発注メールを送信する自動発注機能も活用し始めた。具体的な成果については22年3月末をめどに報告書をまとめる。
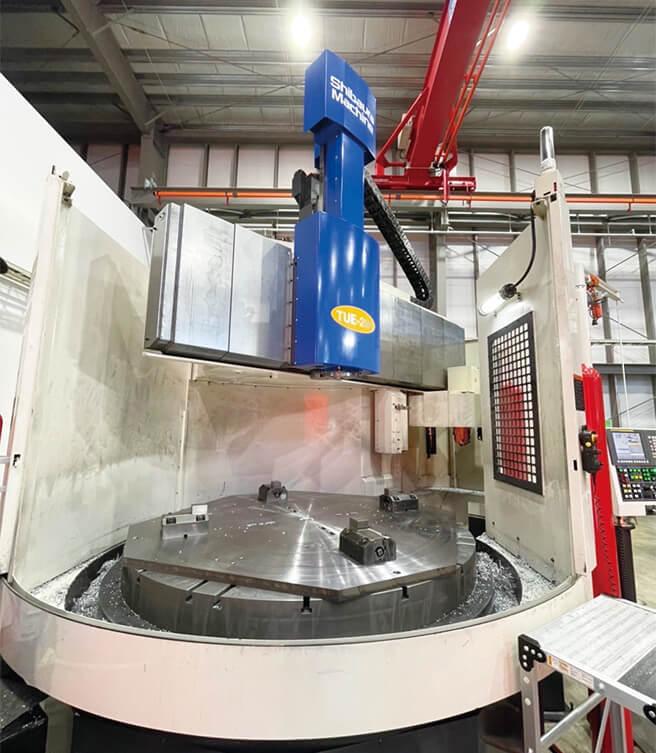
工場を統括する新藤浩光取締役製造本部長生産管理グループリーダー コンサートマスターは、「探す時間の短縮に加え、工具の使用量把握できる効果が大きい。当社は多品種少量品が多いため工具の種類も増えていく傾向にあり、適正在庫の指標として活用したいと考えています」と期待する。
MATRIXによる生産性の向上が、さらなるハイエンドのモノづくりへと導く。