タンガロイ成功事例
外径旋削用工具「AddMultiTurn(アド・マルチ・ターン)」の採用で加工時間短縮と生産数3割アップを実現
㈱大林テクノ
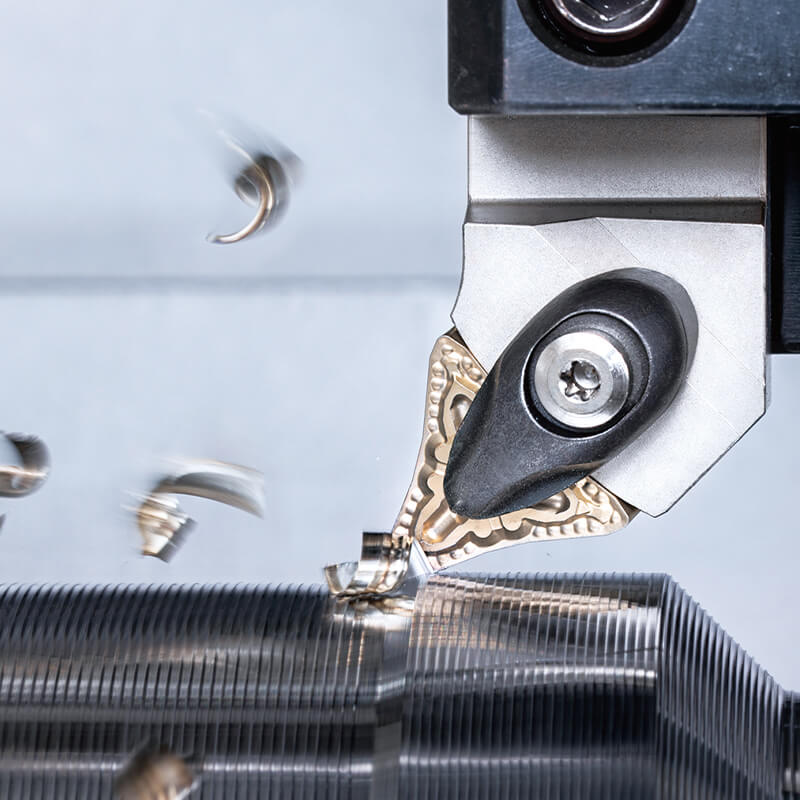
本記事は機械技術2024年3月号掲載分をWeb用に再編集したものです。
1個当たりの加工時間をいかに縮めるかが問われる金属部品の量産現場。寸法精度や表面品質を維持しつつ加工時間を短縮するには、適切な工具選定や加工プログラムの作成などさまざまなノウハウが必要になる。自動車部品の旋削加工を主力とする大林テクノ(愛知県安城市)は、安定して精度を出しにくい部品やコスト削減が求められる部品など、難易度の高い量産加工を積極的に受注する。新たに立ち上げたトランスミッションのリング形状部品では、タンガロイの外径旋削用工具「AddMultiTurn(アド・マルチ・ターン)」を採用。高送り加工への切替えや突発的な工具欠損の撲滅により、加工時間の大幅な短縮と生産数3割アップを成し遂げた。好調な受注を背景に新工場の建設も視野に入れている。
安定した部品量産に強み
さらに独特なのが池田社長の経歴だ。創業者である祖父の死去に伴い、大学卒業と同時に大林テクノに入社したものの、経営学部出身の池田社長にとって製造業はまったく畑違いの職場だった。ところが、事務員として工具メーカーより頼まれたトライアルを社内へ展開していくうち、次第に切削工具に興味を持つようになり、「この工具で成果が上がったなら、次はこのラインで使ってみて」と工具の選定を自分なりに始める。助言が功を奏すると、次は工具に合った切削条件に興味を持ち始め、機械メーカーのカタログを参考に「機械剛性×工具」に合った加工プログラムを独学で作成。初めて作ったプログラムがマシンタイム半減、工具寿命3倍の成果を出し現場スタッフの信頼を獲得。その後製造部長や専務を経て2019年に社長に就任した。
技術者として頭角を現した池田社長のもとにはさまざまな仕事が舞い込むようになる。祖父の時代に主力だったシャフトに加え、丸物や薄物が増加。加工形状の変化に合わせて、加工設備にマシニングセンタや複合加工機を加えた。
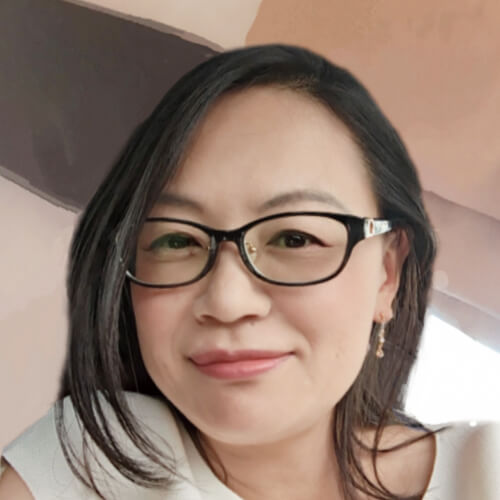
池田 奈々子氏
加工時間の長さが課題
そうした中、新規で受注したトランスミッション部品で頭の痛い事態が発生した。1個当たりの加工時間が長く、現状の加工設備では顧客の求める数量を確保できないという問題である。設備を増設したくても、工場のスペースがひっ迫していて増やせず、1台当たりで加工できる数量を増やすしかない状況だった。
問題になったのは「リアプラネタリリング」と呼ばれる段付きのリング形状部品。熱間鍛造された鉄製のブランク材を、ガントリーローダーの付いた2スピンドルタイプのCNC旋盤を使い、荒加工(1工程目)、荒・仕上げ加工(2工程目)、仕上げ加工(3工程目)の順に削っていく。当初の予測では、1台で加工できるのは月産7,000個。これを月産10,000個以上に引き上げる目標が掲げられた。改善のターゲットになったのは1工程の荒加工。2・3工程目に比べて25秒ほど長く、ボトルネックとなっていた。特に鍛造粗材には型ずれや形状のダレがあり、硬い黒皮を削るため工具欠損も多く、安全を見るため余計に時間がかかっていた。
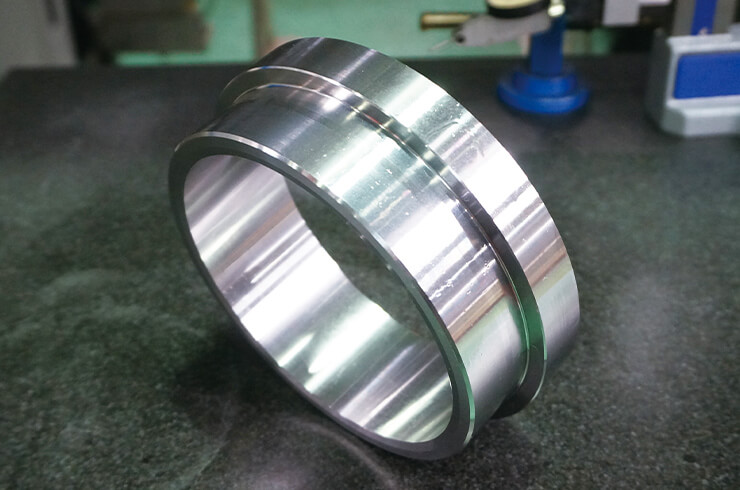
往復パスの導入が可能に
課題解決のため、池田社長は「高能率・長寿命工具」に着目。加工時間短縮に役立つ高能率工具にもいろいろあるが、「今回は鍛造端面へも切り込み可能な高送り工具が必要不可欠だった」(池田社長)。そこでクランプ剛性も高く、高送りが可能なタンガロイの外径旋削用工具「AddMultiTurn」でテスト加工を実施した。
2022年に発売されたAddMultiTurnは、1つのホルダで前挽き、後挽き、倣い、端面の加工が可能な新発想の外径旋削用工具である。旋削では前挽き加工(押し加工)が一般的で、ツールパスは押して→元の位置に戻り→また押して、を繰り返す。一方、AddMultiTurnは前挽き加工と後挽き加工(引き加工)の両方が可能で、押し・引きを繰り返す往復のツールパスを使える。しかも、後挽き加工は前挽き加工に比べてさらなる高送りが可能。通常のインサートに比べて厚みがあり欠損に強いのも特徴である。
効果ははっきりと現れた。当初は3工程との差をなくすため、1工程の加工時間を25秒縮めるのが目標だった。それを大きく上回る40秒近い短縮に成功。全体で生産量の3割アップを実現した。3工程目の方が逆に長くなってしまったため、「今度は3工程目の短縮に取り組まなければ」と池田社長は苦笑する。
テスト結果を受け、リアプラネタリリングの量産にAddMultiTurnが採用された。取り代の多い端面を加工する際、切りくずが長く伸びて工具に絡まる問題も、往復のツールパスを採用したことで切りくずを短く分断できるようになり解決。鍛造品のブランク材は形状にばらつきがあり、同じ条件で加工しても突然工具が欠損することがあったが、AddMultiTurnの採用後は発生していない。
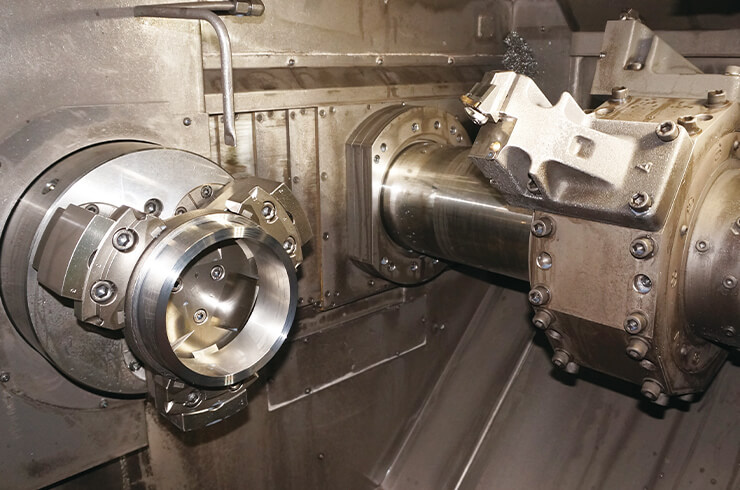
自動車部品に加え電動工具部品の量産を開始するなど受注が好調で、2年後には新工場への移転を予定する同社。「オリジナルの自動車カスタムパーツの製造にも参入したい」と話す池田社長は、将来への明確なビジョンを描いているようだ。