
これは、タンガロイの営業担当がお客様とともに歩んだ成功への道である。
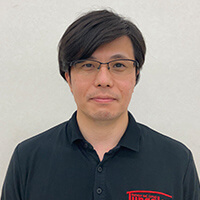
タンガロイ営業担当
石黒 一希Kazuki Ishiguro
- 出身
- 山形県
- 社歴
- 2014年入社
- 趣味など
- 山登り
機内が狭く、工具の段取り替え作業の大変な自動盤。今回は自動盤において、機外段取りに成功したストーリである。
山形県山形市に拠点を構える株式会社鈴木製作所様は、家庭用ロックミシンと横型ピロー包装機を主力事業とする。1968年に工業用ではなく、職人や家庭でも使える小型のロックミシン「ベビーロック」を世界で初めて開発。現在も、ユーザー目線に寄り添った改良を重ね、業界シェアを拡大している。また1977年には、蓄積した技術を応用して、ピロー包装機の開発・販売を開始。独自技術を駆使した、高性能を武器に食品業界をはじめ、医療、農業など幅広い分野に展開、”「山形ブランド」で世界を席巻し続ける開発型企業”を社是に運営をされている。
長きにわたる関係性
担当営業である石黒と鈴木製作所 松田工場長との出会いは2018年であった。松田工場長は、長年タンガロイとの関係を継続頂いており、何と石黒は歴代5人目の鈴木製作所様担当であった。その長年の間には、製品の使用に限らず、発売前試作品のユーザーヒアリングやテストの実施など様々な面でご協力を頂いてきた。
現在の担当営業である石黒とは、特約店であるタルイシ様との同行の際に担当変更のご挨拶に伺った際からの関係である。定期訪問をしながら、セミナーや展示会などのイベントの案内や参加を通じて関係を深めていった。
自動盤ライン機械稼働率のボトルネック
鈴木製作所様では、自社の主力製品であるミシンに使用する小物部品の生産を自社内で行っており、これら部品の加工に自動盤を使用している。自動盤の特性としても、機械稼働率を高めることが生産性向上の鍵であった。しかし、インサート交換や工具の段取り替えに伴う作業時間が長く、この点が機械稼働率向上を阻害していた。
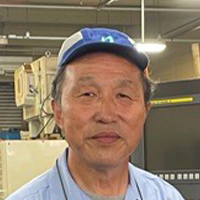
「当社では、小物部品の加工に自動盤を使用しています。インサート交換や工具の段取り作業は、機械内部で行う必要があり、時間がかかる上精度も求められます。特にこの作業は新人オペレーターにとっては難しいものでした。この工具段取り作業の改善が自動盤ラインの長年の課題でした。」
インサート交換と工具の段取り作業
インサートのコーナチェンジ時
- 機内にて交換作業を実施
- ホルダが刃物台に付いた状態で、ねじを緩めてインサートを外す
- 違うコーナに変えて再度ねじを締め直す
インサート交換時及び工具交換時
- バイトを刃物台から一度外して作業を実施
- インサート交換は機外で実施
- 以降下記の刃先位置補正を実施
刃先位置補正方法(径・芯高・ワーク長手方向)
①芯高の補正
- 盤上に基準高さを図る試料を置きダイヤルゲージでゼロ合わせ
- その基準を元に、対象工具の刃先位置をダイヤルゲージで測定し、その差分をY軸の補正に入力
②ワーク長手の補正
- 盤上に基準高さを測る試料を置きダイヤルゲージでゼロ合わせ
- その基準を元に、対象工具の刃先位置をダイヤルゲージで測定し、その差分をZ軸の補正に入力
③径の補正
- 芯高補正をした工具を刃物台に設置
- バー材をブッシュから出し、その外径に切れ刃を接触させる。切れ刃を接触させた状態で、バイトを固定ボルトに締めて締結
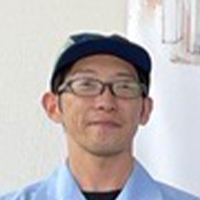
「インサートの交換や工具の段取り替えには、多くの作業や注意すべきポイントがあります。自動盤は機内スペースが狭いため、単純にインサートやホルダを交換するだけでもやりにくい作業です。また、刃物台もコンパクトであるため、隣接工具間のスペースや、ブッシュ最近傍の工具とブッシュ間とのスペースが狭いことも作業を難しくする要因でした。
こういった理由から、インサート交換時にインサートやねじを落としてしまうなどの不具合が生じていました。一度落としてしまったインサートやねじを探すのにも時間がかかります。場合によっては見つからないことも多く、時間とお金を浪費してしまうため、管理者としては頭の痛い問題でした。」
狭い機内でのインサート交換/工具交換作業
ネック事項解決策の模索
担当営業である石黒は、日々定期訪問を重ねている中で、鈴木製作所様が抱える課題解決策がないかを模索していた。そんな中、課題解決に繋がりそうなある製品、自動盤用ヘッド交換式工具『ModuMini-Turn』が発売になった。
『ModuMini-Turn』は、抜群の工具操作性と加工精度を実現したヘッド交換式工具で、シャンクを刃物台に設置したまま、ヘッド交換のみでインサートを交換できる。また独自のカップリング機構で、ヘッドを確実にクランプでき、優れた刃先位置精度を実現可能な製品である。
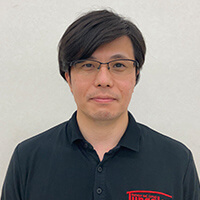
「自動盤の工具交換作業の課題解決に貢献できそうなModuMini-Turnが2021年9月に発売されました。この製品を知った時、まさに鈴木製作所様の抱えられる課題解決に繋がりそうであったため、真っ先に提案に伺いました。」
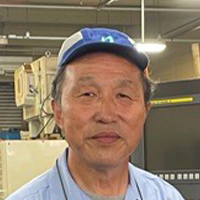
「石黒さんからこの工具の紹介を受けた際には、課題解決の可能性を感じました。この工具のコンセプトを最大限利用するには、“機外でインサートを交換し、刃先位置測定/補正無しで工具をクイックチェンジする運用”がベストと考え、この運用が行えるかのトライアル実施に向けて動き始めました。」
機外段取り替えの可能性
松田工場長はこのアイデアならネックになっていた課題を解決できる可能性があるとトライアルを進めていった。最初の目論見としては、
- ヘッドを機内でシャンクから外す。(シャンクは刃物台に取り付けたまま)
- 予めインサートを装着した別ヘッドを機外に用意
- この別ヘッドを機内のシャンクに取付け加工を行う
ことを目指した。
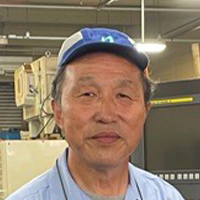
「この運用を行う上での、懸念事項としては刃先位置精度(芯高/径/ワーク長手方向)でした。刃先位置精度のばらつきを把握するために、ModuMini-Turnのシャンクと様々な種類のヘッドを数個準備し、それらを組み合わせながらインサートを交換すると、どのくらいの刃先精度にばらつきが発生するかの検証を行ってみました。
結果としては、求められる精度を満足するような範囲に納まらず、特に型押し成形品であるM級インサートでは0.1を超えるような刃先位置のばらつきがあったため、この方法は断念しました。」
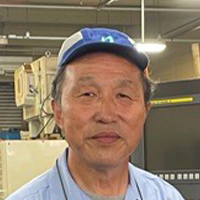
「当初の目論見は達成できませんでしたが、ヘッド交換の容易さや機外でのインサート交換作業には大きな可能性を感じていため、何とかこのModuMini-Turnのシステムを使用した機外段取りは達成したい意向がありました。」
そこでこの運用を達成するために、生産課 田崎様に機外段取り運用達成の白羽の矢が立ったのであった。
刃先位置測定/補正方法の確立
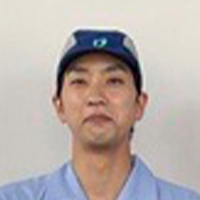
「工具の機外段取り替えの達成は、大きな生産性向上ができる手段だと可能性を感じていたため、何とか刃先位置測定と補正量の計測が出来る方法を確立させたいと考えました。
と言うのも、インサートやねじを落としてしまう小さなトラブルの他に、工具を刃物台に正しく取り付けられずに斜めに装着してしまい、加工不良品が発生するトラブルや、工具交換作業中の工具移動位置指定時の入力ミスによる、ワークやブッシュと工具の接触トラブルも発生していました。こういったトラブルが起きると、精度確認などの復旧作業に多くの時間を割いてしまい、それに伴い生産スケジュールが大きく遅延するケースもあります。
そういった影響度の高いトラブルを避ける意味でも、機外段取り化は重要なミッションであると感じ、運用構築を進めていきました。」
と思考錯誤と、様々なトライアルを重ねる中で下記のような方法を考案し、運用を開始した。
専用治具とマスターシャンク/マスターヘッドを使った刃先位置の機外計測と補正の方法
インサートのコーナチェンジ時
- 計測用の専用治具を準備
- 測定の基準となるマスターシャンクとヘッドを定義し、これらを補正入力の基準にする
刃先位置補正方法(径・芯高・ワーク長手方向)
- 機内に取り付けるシャンクにマスターヘッドを付けて、マスターシャンクと機内取付けシャンクの芯高と径、ワーク長手方向の差分を使用するシャンク毎に計測
- 測定後、これらシャンクを機内に設置
- 機内で使用するヘッドにインサートを取付け、そのヘッドを計測用治具に取り付ける
- 取り付けた状態で芯高・径・ワーク長手方向の位置を測定
- 計測した測定値とマスターシャンク間の補正を足し合わせることで、最終的に必要な補正量を定義し、NCプログラムにこれらの補正量を入力
工具交換作業時間削減と作業の平準化を達成
新しい運用に変えてみたところ、劇的にインサート交換時間と段取り替え時間が短縮された。熟練オペレーターの従来作業時間が8分だったところ、2.7分まで削減された。
また作業練度の低い新人オペレーターでは、従来作業時間が19分だったところ、3分と更に改善効果の大きくなる結果が得られたのであった。交換時間の削減にとどまらず、オペレーターの熟練度によらない工具交換作業が達成できたことも効果の大きい成果であった
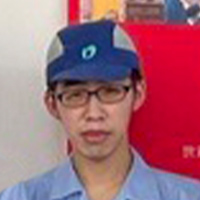
「ベテランの方に比べると、どうしても作業時間が長くかかってしまうことが以前より気になっていました。早くやろうとは心掛けていましたが、早くやろうとすると、その分確認の精度や慎重さがどうしても犠牲になってしまうため、時間短縮と作業の精度の両立が何より課題でした。新しい交換方法は短時間で作業を終えることが出来ます。空いた時間を他の作業に費やせるため、作業全体の効率化及び精度向上に大きな効果が出ました。」
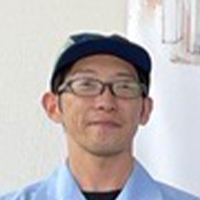
「工具交換作業時間の短縮と作業の平準化が行えたことは、生産ライン全体の生産性向上に大きく貢献しました。新しい運用方法では、工具交換時に刃物台を動かさなくてよくなります。次に動かすときは加工開始になるため、接触トラブルを防止できます。トラブルの種を抑制できたことは、ラインの安定稼働に繋がるため、ライン管理の責任者としては安心です。」
と今回の改善を振り返っている。
今回の改善ポイント
-
工具交換時間の削減により機械稼働率が向上
従来10~20分要していた工具交換時間が約3分まで削減。機械稼働率の向上に貢献
-
熟練度に頼らない作業の平準化
従来方法では、熟練者と新人では作業時間に大きな隔たりがあった。ModuMini-Turnを使用した機外段取りに変更したところ作業時間が同等になり、工具交換作業の平準化が行えた。
-
ミス発生のリスクを低減し、大きなトラブルを抑制。ラインの安定稼働に貢献。
機外段取りのため交換作業中の機械操作が最小限に抑制され、入力ミスなどで生じる接触事故発生などの致命的なトラブルを抑制。生産計画に狂いを起こさない安定的な生産が可能になった。
更なる改善へ向けて
今回の改善活動の成果は松田工場長も大きな成果であったと感じている。
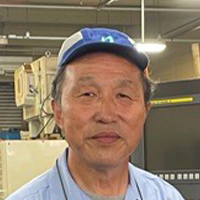
「交換時間の削減、作業の平準化、ならびにトラブルの抑制は、工場を統括する立場としても非常に良い改善であったと思っています。ものづくりを営む同業者として、このリクエストは難しい事は理解していますが、タンガロイさんには当初の狙いであった補正なしの一発加工が行える工具への改良を引き続き期待しています。
ものづくりの現場では常に改善が求められます。今回の改善で満足することなく、より生産性の高い現場を目指し、更なる自動化や無人化への取組も継続していきたいと思っています。こういった自動化/無人化が進むと、工具にもより高い性能が求められます。トラブルレスな稼働のための安定した切りくず処理、稼働率向上のための工具寿命の更なる延長を工具メーカーには期待しています。」
と今後の展望と期待を頂いている。
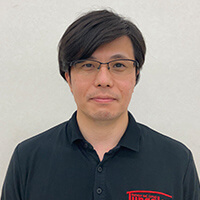
「ModuMini-Turnの提案は私から行わせて頂きましたが、ModuMini-Turnの更なる活用方法を鈴木製作所様から教えて頂けた貴重な体験でした。鈴木製作所様の活用方法は、メーカーとしても目から鱗が落ちるような活用の仕方で、社内の技術者の間でも話題にあがるほどでした。
今回の事例のように、メーカーがユーザー様から学ぶ機会は多いと感じており、そのような機会を頂けた鈴木製作所の方々には感謝しています。
今回の案件を振り返ってみると、営業がユーザー様からのアドバイスやご意見を拾い、それらを会社にしっかりと伝え、製品に反映させる事の重要性に改めて気づかされました。今後もしっかりとユーザー様の声が会社に届けられるように、お客様に近いところで営業活動を行っていきたいと思います。」
と今回の案件を振り返っている。
タンガロイとしても、ただ製品を開発・販売するだけでなく、お客様現場でのユースケースまで考えた製品を開発・提案し、お客様の生産性向上に貢献していきたい。
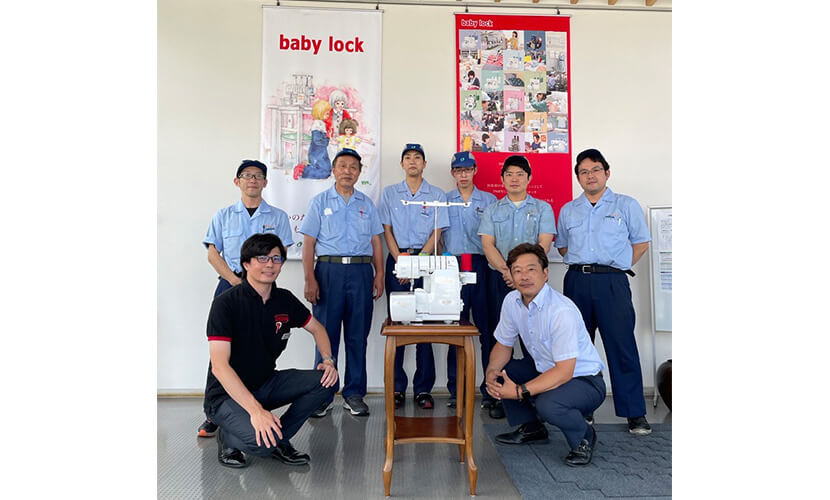
今回ご紹介した製品はこちら
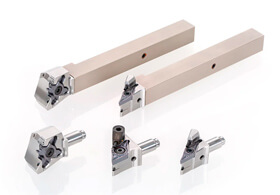