
これは、タンガロイの営業担当がお客様とともに歩んだ成功への道である。
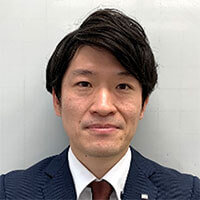
タンガロイ営業担当
中島 淳Shun Nakajima
- 出身
- 群馬県
- 社歴
- 前職計測器メーカにて営業勤務。2016年1月よりタンガロイ入社。以後、高崎営業所にて勤務。
- 趣味など
- スポーツ観戦・ドライブ
タンガロイでは、工具選定の手間を省きつつ、生産性を向上させる工具をお安く購入いただける『新規ツーリングプロモーション』を開催している。今回のストーリーは、量産開始までのリードタイムが短い新規量産部品立上げでの『新規ツーリングプロモーション』活用事例である。
群馬県桐生市に本社を構える株式会社正田製作所様は、主に自動車部品(ステアリング部品、パワートレイン部品、シャシー部品等)を製造し、大手自動車メーカーや自動車Tier1メーカーに供給している。生産拠点としては、群馬県内に2拠点、中国に2拠点と海外進出も進めている。
正田製作所様では『狭い分野でも世界一をめざして、誇り高き技術集団に成長する』をモットーに活動している。鍛造から機械加工・熱処理まで、部品完成までの一連の生産技術を保有している。新規量産部品の立上げ時も、開発試作から量産までを自社内で行うや、プレス機や搬送自動機なども自前で製作する高い生産技術力を要し、ライン構築から量産開始までの一貫生産に対応できることが強みの1つである。また重要保安部品をはじめとする、極めて高い安全性が要求される分野においても、高度な技術と解析力でお客様の信頼に応えている。
前担当営業の撒いた種
中島は2020年から正田製作所様の担当になった。正田製作所様ではタンガロイ工具の採用はほぼ無く、他社工具をメインに使用されていた。そのような状況下であった正田製作所様に対し、前担当が少しずつ改善提案やテストサンプルを提供していた。中島に担当が変わった直後から、それらサンプルでのテスト結果が出始めた。「今まではタンガロイの工具はあまり使用していなかったが、意外と使える」と正田製作所 生産技術担当者様から評価を頂き始め、少しずつタンガロイ工具が正田製作所様の選定候補として認識されていった。そんな中で1つ新規部品のツーリング案件を頂き、弊社工具でのツーリング提案の実施からその後採用を頂いた。
量産開始までのリードタイムが短い新規部品の立上げ
正田製作所様での初めてのツーリング提案と部品立上げが終了し、次の提案を検討していたところ、ある新規量産部品立上げのご相談を頂いた。正田製作所様ではSDGs対応部品の新規受注が決定し、その生産ライン立上げが決まったタイミングであった。中島が量産立上げまでのスケジュールをお聞きしたところ、生産立上げのスケジュールがタイトなプロジェクトであった。
抱えていた課題は「今回の新規部品の立上げは、新規で工作機械を購入しライン構築を行う。量産開始準備完了目標が2022年9月であるが、工作機械の搬入は8月。工作機械や自動化システムの構築、現場オペレーションの教育や稼働などを1か月以内で終了し、量産準備を完了させる必要がある。それら業務を考慮すると、加工確認や加工ネック改善に取り組んでいる時間は無く、工作機械搬入時点で加工確認や加工ネックの潰し込みを終えておきたい」であった。正田製作所様でも工作機械は多くの台数を保有しているが、日々生産活動を行っている中では、テスト実施のための設備や人員の確保を行うことは難しい。そういった量産部品加工ユーザー様の事情を中島も当然知っていた。課題を聞いた中島は「タンガロイテスト設備を使用した事前テストの実施」を提案し、タイトなスケジュールでの立上げ案件のサポートをしていこうとプロジェクトを進めていった。
【新規立上げのスケジュール】
- 新規生産ライン立上げのプロジェクト開始: 2022年5月
- 工作機械の立合い検収:2022年7月
- 工作機械搬入:2022年8月
- 量産準備完了:2022年9月
タンガロイテックセンターでの事前検証
中島は早速タンガロイテックセンターでの、テスト計画と日程調整を進めていった。テストスケジュールは合計1週間を予定し、テストの内訳としては、テスト準備に5日間、お客様の立会い検証に2日間という計画を立てた。正田製作所様から実ワークを支給頂き、弊社内テスト機を使用してこのワークの加工とその評価を行う。テストでは下記の2項目に関して重点的に評価を行う計画を立てた。
【テストでの重要確認項目】
-
マシンタイム
予定された生産計画数を1台の工作機械で達成するには、規格のマシンタイムを厳守する事が必達目標であった。このマシンタイムを達成できるような工具選定とツーリングパスの立案と実施が必要であった。
-
溝入れ工程
今回の部品加工で最もネックになると予想していた工程は溝入れ工程であった。今回の部品は溝入れ加工部が強断続になる形状であり、溝の口元には面取り指示がある。正田製作所様では、このような“溝入れ+面取り加工”は、溝入れ加工後に溝入れ工具を使用した倣い加工で面取り加工を実施するのが慣例であった。「今回は加工が断続になるため、倣い加工で面取りを行うと、インサートコーナ部での加工になることからインサートが欠けるリスクが高くなる。またサイクルタイムが厳しい点も考慮して、面取り付き特殊溝入れインサートで、“溝入れ+面取り”一発加工を行いたい」といった要望を頂いていた。
詳細な工具選定や加工方法と加工パスの立案ならびに、テスト準備と実施はマーケティング部 溝入れ担当の比留川とテックセンター 佐藤が担った。
ツーリングの立案を行った比留川は、
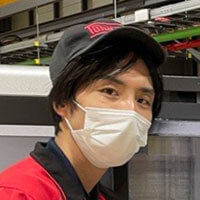
「強断続の溝入れ加工であったことから、溝入れインサートにはクランプ強度の高い『TetraMiniCut』を選定した。クランプ強度を増加させることで、インサート欠損の抑制と、加工中にインサートが動いてしまうことで生じる左右の面取り量がばらつくことの抑制を狙った。また外内径加工では、インサートコストを低減できるよう小型インサートの外径旋削工具『ISO ECO Turn』や、多コーナ内径旋削工具『MiniForce-Turn』を選定しつつ、マシンタイムが最短になるようなツーリングを組みました」
といったツーリングコンセプトを立案した。
テスト機オペレーターである佐藤は、
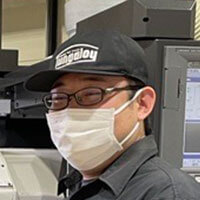
「ワーククランプが内径クランプと、弊社ではクランプに使用できる専用の治具がありませんでした。しかし、社内で保有していたストレートコレットやボルトなどを組み合わせて本番のクランプ治具になるべく近いチャッキングを再現してテスト準備を進めました。」
と、製品担当とオペレーターの二人三脚でテストの準備を進めていった。
①従来工程(溝入れ加工後に面取り加工)
- 通常溝入れ工具での溝入れ加工
- 通常倣い工具での面取り加工
②新工程(特殊面取り付きTetraMiniCutでの溝入れ+面取り一発加工)
- 特殊面取り付きTetraMiniCutでの溝入れ+面取り加工
- 加工部の拡大イメージ
事前テストで見えた新たな課題
テスト準備を進め、お客様の立ち会い日を迎えた。比留川の立案した工具とツールパスでの加工を実施したところ、重要確認項目であったマシンタイムは、テスト加工時点では企画以内での加工時間達成が不可能ではない事に希望を持てた。また懸念された溝入れ加工も「想定以上に何もなくあっさりと加工が行えた」と、生産技術担当者様と比留川の狙い通りの結果となった。
しかし当初想定していた事とは別の新たな課題が見えた。その課題とは、部品外径部に発生したバリであった。バリの懸念事項はもともとあったが、実加工をしてみるとバリの方向や高さ等が後工程に影響を及ぼす予測以上のバリが散見された。サイクルタイム確認と溝入れ加工の検証が早期に終了したことから、残りの1日半をこのバリ対策に充てた。加工方向の変更や様々な切削条件を適用しながら検証を進め、その結果バリ抑制に最適な方法を見つけた。「タンガロイでのテスト終了後すぐに機械メーカーでの立会検収が予定されていた。事前にテストをしておいたおかげで加工上の懸念が事前に潰しこめました。その結果、機械メーカーでの検収立ち合いでは、加工の確認に時間を取られずに機械周りの確認や自動システムの確認に時間を多く割くことが出来ました」(生産技術担当者様)と弊社内の事前テストから機械メーカーでの立会検収を振り返られている。
担当営業の中島は、
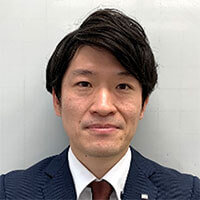
「今回の案件については時間軸がタイトであったので、客先との連携がキーになると思いレスポンスをなるべく早くすることを心掛けました。また、お客様と弊社の間で意思疎通の齟齬がなるべく出ないように間に入り、やりとりが円滑に進むよう気を付けていました。多くの方のご協力があったおかげで、試作品の製作やテストを実施することが出来ました」
と当時を振り返っている。
機械敷設後の垂直立上げに成功
無事タンガロイ内のテストと機械メーカーでの立会い検収テストを終えて、正田製作所様に工作機械が施設された。実機での加工でもタンガロイ内でのテストとほぼ同様な結果が得られたため、加工に関してはトラブルなく量産立上げが行えた。「生産ライン立上げ前に加工検証を行えることは非常に助かる。今後も新規部品の立上げは続くが、その際もタンガロイに声を掛けていきたい」と生産技術担当者様からは高評価を頂いている。
担当営業である中島は、
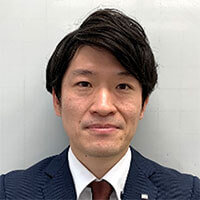
「立上げて終わりではなく、量産開始後の改善活動も工具メーカーにとって大事な役割だと認識している。生産で使用されたインサートの損傷状態を確認しながら、材種やインサートのノーズRなどの細かな変更とその評価を進めて、よりお客様の加工に最適なチューニングを継続しています」
と量産開始後も更なるランニングコスト低減活動をお客様と共に取り組んでいる。
今回の改善ポイント
-
タンガロイテスト設備で事前検証を実施。事前に加工検証と対策を実施しておくことでスムーズな生産立上げをサポート
早い段階での課題の洗出しと対策を実施。試削りと評価が柔軟に行いやすい工具メーカー設備を使用して加工を検証
-
課題に沿った工具提案と最新工具を用いた特殊品の適用
工具特性をよく理解した専門家だからこその工具選定や加工方法の立案。失敗の少ない工具選定&ツーリングが可能に
-
新規ツーリングプロモーションでお得に工具をご購入
プロモーションへの参加申込により、普段よりも工具をお得にご購入
省人化と複雑形状部品への取り組み
生産技術担当者様が考える今後の課題は「省人化」だそうだ。少子高齢化が進む環境下では人材確保が難しくなっている。また、少子高齢社会の日本にとっていかに作業負荷を下げ、今後、日本の労働力不足や世界情勢にあったワークスタイルを確立していくことが重要だと考える。「正田プロダクションシステム=SPS」を基本とした、人にやさしい最適なライン構築を目指し、今後も自動化を選択肢の一つとして進めていく予定である。また、近年の部品形状は軽量化ニーズ及び複数機能保有による部品能力統合の関係からより複雑化が進んでおり、従来の汎用的な旋盤やマシニングセンタでは加工が難しく、逆に治具金額・管理工数増によりコストUPする可能性が高い部品が増加していると感じている。「QCDで最適な工法を見出し、対他競争力のあるライン構築を見出していきたい」と目標を述べられている。
今後、工具メーカーに求める次世代工具は、切粉排出性を極限まで高めた切削工具・1つの刃物で穴あけ、外径等多様的に加工のできるマルチ工具だそうだ。「軽量化の観点から完成された製品の内径部をさらに加工して欲しいというニーズが今後増えていくと考えている。長尺の内径加工はビレとともに切粉の対策が永遠のテーマだと考えている。そこに対応できる工具が出来たら嬉しい。マルチ工具に関しては、設備選定時と同様に切削時間の低減、刃物管理工数の低減という直結的な生産性に起因するため、期待しています」といった要望を頂いている。弊社としても加工環境の変化に対応できるような工具開発を今後も進めていきたい。
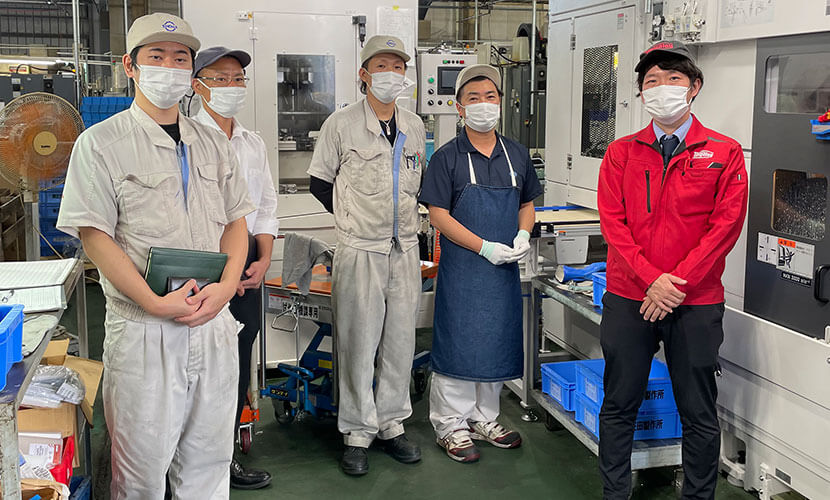
今回ご紹介した製品はこちら
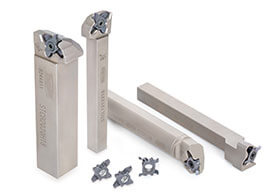
独自の3点クランプシステムで信頼性に優れ、4コーナで経済的
TetraMiniCut(テトラ・ミニ・カット)
インサート切れ刃は高精度加工に適した研削級独自のポケット形状により、繰り返し刃先位置精度とクランプ剛性に優れる