
これは、タンガロイの営業担当がお客様とともに歩んだ成功への道である。
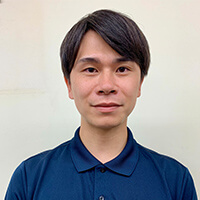
タンガロイ営業担当
谷中 亮太Ryota Yanaka
- 出身
- 愛知県
- 社歴
- 入社2020年
- 趣味など
- スキー、バイク
様々なフライス加工で用いられる事の多いソリッドエンドミル。今回は量産加工で用いられていたソリッドエンドミルでの工具コスト削減事例である。
株式会社オオオカ
愛知県碧南市に拠点を構える株式会社オオオカ様は、エンジンやミッション部品、ブレーキ・足回り部品などの自動車量産部品を製造しており、今年で創立64年を迎える。
そんなオオオカ様の強みは、自動車部品の量産ラインを短期間で構築・稼働できる高い生産技術力である。一般的に鍛造など成形された異形状ワークは、治具の設計やワーク搬送、加工方法の検討など、生産ラインの構築から稼働までは時間を要す場合が多い。しかし、オオオカ様ではこういった異形状部品加工の知識と経験が多く、こういった部品においても短期間でのライン構築・稼働が可能である。また、生産状況に応じてフレキシブルに量産ラインを組み替える事のできる対応力の高さも部品供給先である自動車Tier1,Tier2のお客様から高い評価を頂いている要因の1つである。
新規立上げ部品のツーリングプロジェクト
株式会社オオオカ 大岡正則専務と担当営業である谷中との出会いは「インナー」という新規部品の立上げがスタートしたタイミングであった。前任の担当時から新規部品立上げ案件の話はあったが、その立上げ開始が本格化するタイミングと、谷中への担当変更のタイミングがズバリ重なったのであった。オオオカ様の担当になった最初の仕事がこの重要な新規部品立上げであったため、谷中は身が引き締まる思いであった。
谷中にとって、量産部品でのツーリング選定はほぼ初めての経験であったことや、今回の部品が異形状ワークであることの難しさ(治具やワークとの工具干渉が発生しやすい。部品形状上ワークや治具剛性が弱い部分が存在するなど)より、工具選定にはより配慮が必要で、担当変更直後から難易度の高いプロジェクトを担うことになったなと感じていた。
そんな中でも、大岡専務の要望をお聞きしたり、大岡専務の卓越した加工の知識・経験を聞いたり、時には前営業担当者のアドバイスをもらうなどしながら、一歩一歩工具選定を進めていった。また、オオオカ様の現場担当者の方は、外国人の方も多いことに配慮し、「なるべく現場の方が使いやすいヘッド交換式や刃先交換式の工具を中心に選定する」などの工夫も盛込んでいった。そういった活動を続けながら、工具選定や加工テストを進め、何とかライン立上げまで無事漕ぎつけた。こういった努力の甲斐もあってか、この部品加工で使用する工具の半分がタンガロイ工具で採用頂けたため、オオオカ様での初めての案件を無事完了できたことに対して嬉しく思っていた。
他社ソリッドエンドミルへの切替
無事初めての案件が1段落してほっとしていたそんなある日、1つ耳の痛い知らせが谷中の元に届いたのであった。1つの溝加工工程で立上げ時からご使用頂いていた当社のヘッド交換式エンドミルに対し、他社のソリッドエンドミルで良好な結果が出たという知らせだった。早速詳細をお聞きしたところ、「現状の設定寿命200台のところ5倍の1,000台まで工具寿命を延長」と大差のある結果であった。元々、この溝加工工程の工具費は、インナーで使用している工具の中でも費用の高い位置づけの工具で改善優先度が高かったことや、オオオカ様は日々の原価低減活動が盛んである自動車量産部品ユーザー様であったことから、立上げ当初からずっと同じ工具をお使い頂けるとは当然思っていなかった。しかし、オオオカ様にてコスト削減が進んだのはいい事と感じつつも、自身でツーリングした思い入れのある工具の転注に対し悔しい気持ちと、必ずお客様からの信頼を取り戻したいという気持ちを抱いた。
リベンジを期した新規工具提案
立上げ当初にヘッド交換式エンドミルを選定した背景としては、「現場使用者が使いやすい工具」を意識した工具選定と、「ソリッド工具は再研・再コート時の流動分の工具在庫が嵩むため、なるべく在庫負担の少ないヘッド交換式や刃先交換式の工具を使用したい」との意向を大岡専務からも聞いていたため、何とかこの2つのご要望に応えられる工具提案が出来ないかと日々思案していた。そんなある日、2つの課題を解決できそうな工具が発売され、この工具でのリベンジを決意し新製品の提案に向かったのであった。
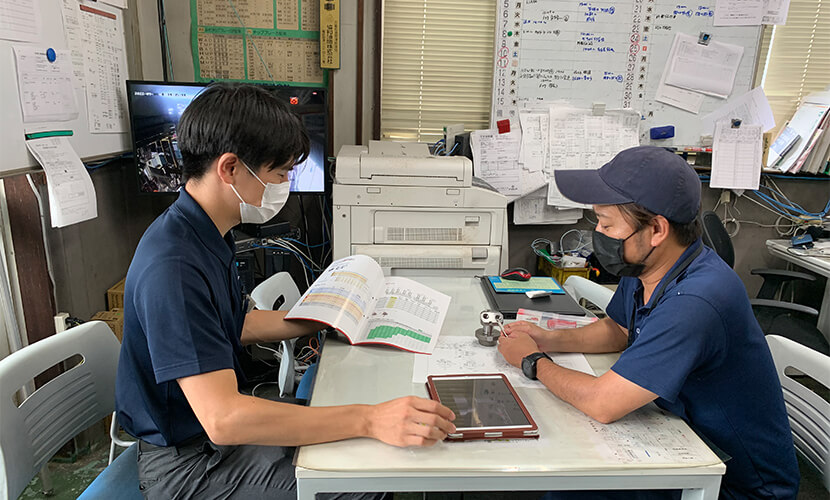
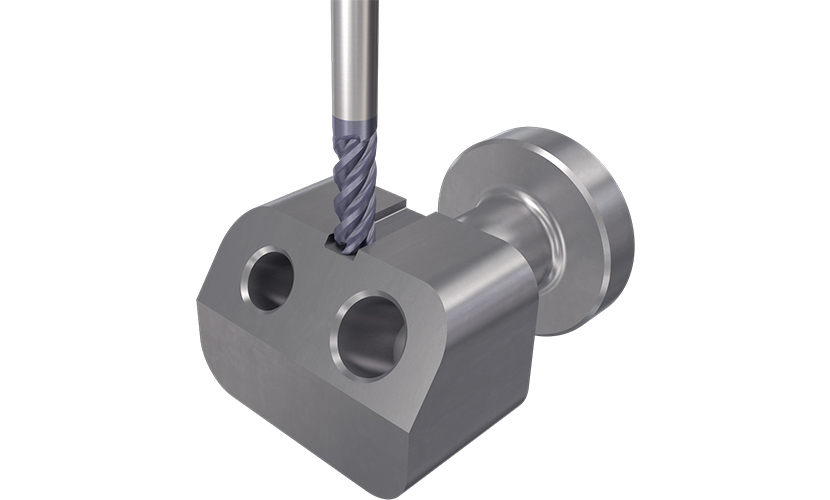
小径刃先交換式エンドミルTungForce-Rec 04サイズ
谷中がリベンジを期して提案した内容は、「小径刃先交換式エンドミルTungForceRec04サイズによる工具費低減と工具管理の手間低減」であった。
『TungForce-Rec』04サイズは、業界最小となる工具径ø6mm、最大切込み4mmに対応する刃先交換式直角肩削りカッタである。インサート底面に施されたV字型形状により、大きな心厚と厚いバックメタルを確保、小径でも高いボディ剛性を実現できる製品である。
ø8 TungForce-Recの高能率溝加工
TungForce-Recの特長
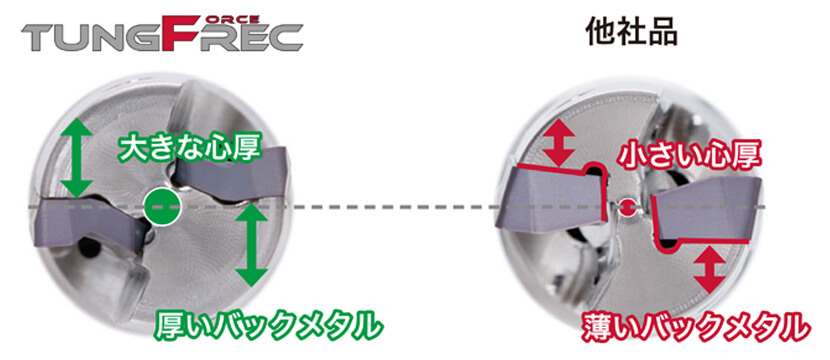
当時使用していた他社ソリッドエンドミルはø8-4枚刃であり、今回谷中が提案した『TungForce-Rec』04サイズのエンドミルはø8-2枚刃であった。いくら工具費が低減できる可能性があっても、加工能率を落とすことは量産部品加工では決して受け入れられない。谷中が焦点と考えていたのは「如何に加工能率をキャッチアップできるか」であった。しかし下記の2つの観点から、十分チャンスがあるのではないかと考えていた。
観点1
生産していたインナーは2機種が存在。それぞれの部品での溝加工の取り代は1機種で2.5mm、もう1機種では3.5mmであったため、この低切込み量であれば切れ刃長の短いTungForce-Rec04でも加工能率をキャッチアップできる可能性があるのではないか?
観点2
通常の小径刃先交換式エンドミルでは負荷の高い溝加工でも、ボディ剛性の高い『TungForce-Rec04』対応可能ではないか?
谷中から提案を受けた大岡専務が工具の実物を見た際に抱いた印象は、「こんな小さな工具で本当に削れるの?」であった。しかし、上手くいけば工具低減に繋がる可能性を持った提案であったことから、まずは味見の加工テストを行ってみた。その結果、「印象よりも普通に削れる」といった評価だったため、実際の切替可否確認のテストに進んでいった。
工具費低減を目指した検証テスト
切替可否確認のテストでは、下記のポイントを焦点にテストを進めていった。
検証ポイント1:加工能率を保ちつつ安定的に加工できる切削条件の探索
このポイントを見極めるために様々な条件を振りながら『TungForce-Rec』の加工領域を探っていった。加工能率のキャッチアップ策としては、刃当たり送りは現状と同じに保ちつつ、刃数減少分2倍の切削速度を適用であった。この条件が加工能率を保ちつつ、安定性が確保できるを切削条件だと判明した。
今回の切削条件選定の最大の焦点は切込み量であった。溝加工はびびりやすい加工で、特に切込み量が最も効いてくるファクターである。取り代が2.5mmのワークはソリッドエンドミルと同様に1パスでの加工が行えたため、ソリッドエンドミルと同等の能率を達成できた。もう1機種取り代が3.5mmのワークでは、量産を踏まえた上での安定性の点では1パス加工は不可能であったが、1.75mmずつ2パスであれば加工が十分成り立つことが判明した。上述した切削速度の増加を適用することで、加工タクトの増加は1秒以内と、量産を行う上でも許容範囲内に何とか収めることに成功した。
検証ポイント2:バリ
2つ目の検証ポイントはバリであった。一般的にソリッドエンドミルは刃先にホーニングを取っていないシャープな切れ刃を持つのに対し、刃先交換式では刃先にホーニングを取っている。刃先交換式にすることでバリの大きさや強度が増加し、後工程にあるバリ取り工程に影響を及ぼす懸念があった。実際加工を行いバリの程度を確認してみたところ、ソリッドエンドミルでの加工時よりも「TungForce-Rec」で発生するバリは若干大きくはあるが、後工程のバリ取り工程には何ら影響を及ぼさない程度であることが判明した。
検証ポイント3:工具寿命
前述した2つの検証を行った後に、今回の最大の焦点である工具費に影響する工具寿命の確認を進めていった。刃数が4枚→2枚に減少することや切削速度が増加していることから、まずは現状ソリッドエンドミルの半分の500台を目標に評価を進めた。500台加工しても刃先の損傷が小さかったことから更に寿命延長を行っていき、最終的には1,000台まで加工が可能なことが分かった。刃先交換式に変更するだけでも工具費低減には効果が出ることは予め想定していたが、「ソリッドエンドミルと同等寿命まで達成できるとは予想外の結果だった」(大岡専務)と嬉しい誤算が得られたのであった。
最終的に得られた工具費の低減効果としては、「台当たり7円、年間削減額にして約200万円」という大きな効果が得られたのであった。
今回の改善ポイント
-
切込みの小さい溝加工に使用していたソリッドエンドミルに対し刃先交換式エンドミルを適用
現状同等の加工能率と工具寿命を達成。ランニングコストの低い刃先交換式に変更したことで、台当たり7円工具費を低減、年間削減額としては約200万円と大きな工具費低減につながった。
-
現場使用者が使いやすい工具
再研削が必要なソリッドエンドミルでは、工具交換時の突出し長の調整が必要で、突出し長のミスが発生する可能性がある。ホルダから外す必要の無い刃先交換式工具では突出し長調整が不要で、突出し長設定ミスや工具オフセット設定ミスの発生を抑制することが可能になった。
-
再研・再コート流動在庫の圧縮
再研・再コートを実施するソリッド工具では、再研・再コートに出す間のリードタイムが必要なため、使用量以上に再研流動分の工具在庫が必要になる。特に単価の高いソリッド工具はこの在庫金額負担が大きい。再研・再コートが不要な刃先交換式工具に変更できたため、流動在庫金額が削減でき工具への投資負担が減少した。
今後の工具メーカーに期待すること
大岡専務が今後の工具メーカーに期待することは「ヘッド交換式や刃先交換式工具の更なる小径化とラインナップの強化」だそうだ。前述した「工具管理」や「流動在庫負担」の観点からこれら負担を減らせる工具の開発強化を要望されている。「加工用途や部品精度を見極めながら、今後もソリッド工具からヘッド交換式や刃先交換式工具への切替えを進めていきたい」とおっしゃっている。当社としても「現場作業者」「生産技術者」「経営者」の3方良しにつながるこういった工具の開発を今後も進めていきたい。
お客様に寄り添った提案活動
谷中としては、大幅なコストダウンに喜んでいただけたこと、何より信頼を取り戻せたことが非常に嬉しかった。谷中の営業ポリシーとしては「お客様に喜んでいただける提案をすること」であり、そのためには、まずお客様の現状把握をすることが大事だと考えている。お客様の真の課題をお聞きするには「時にはプライベートな雑談も交えながら、まずは人として信頼されることを大事にしている」と、今後もお客様に寄り添った営業活動を続けていきたい。
今回ご紹介した製品はこちら
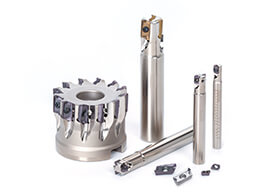