外部給油ドリル加工の不安解消ガイド~ 成功のポイント
外部給油環境でのドリル加工において、切りくずつまりやドリル折損などのトラブルに悩まされていませんか?内部給油機構を持たない工作機械では、外部給油が唯一の選択肢なりますが、その結果、多くの技術者が加工の安定性に不安を感じています。
この記事では、外部給油環境でのドリル加工に焦点を当て、適切な方法やコツを紹介し、トラブルを抑制するためのポイントを解説します。あなたの不安を解消し、成功への手助けとなる情報を提供します。
ドリル加工の基礎
穴加工は、回転する切れ刃、もしくは回転するワークを切れ刃に接触させることで行う加工方法です。ドリルの刃先が材料に接触し、回転することで削り取られた材料(切りくず)が排出されます。ドリルにはフルートと呼ばれる溝があり、これが切りくずを効率的に排出する役割を果たします。
内部給油では、クーラントがドリルの内部を通り、刃先に直接供給されるため、効率的に冷却と潤滑が行えます。一方、外部給油ではクーラントがドリルの外部から供給されるため、切りくずの排出や冷却効果が劣ることがあります。特に深穴加工や硬い材料の加工では、外部給油の制約が顕著に現れることがあります。
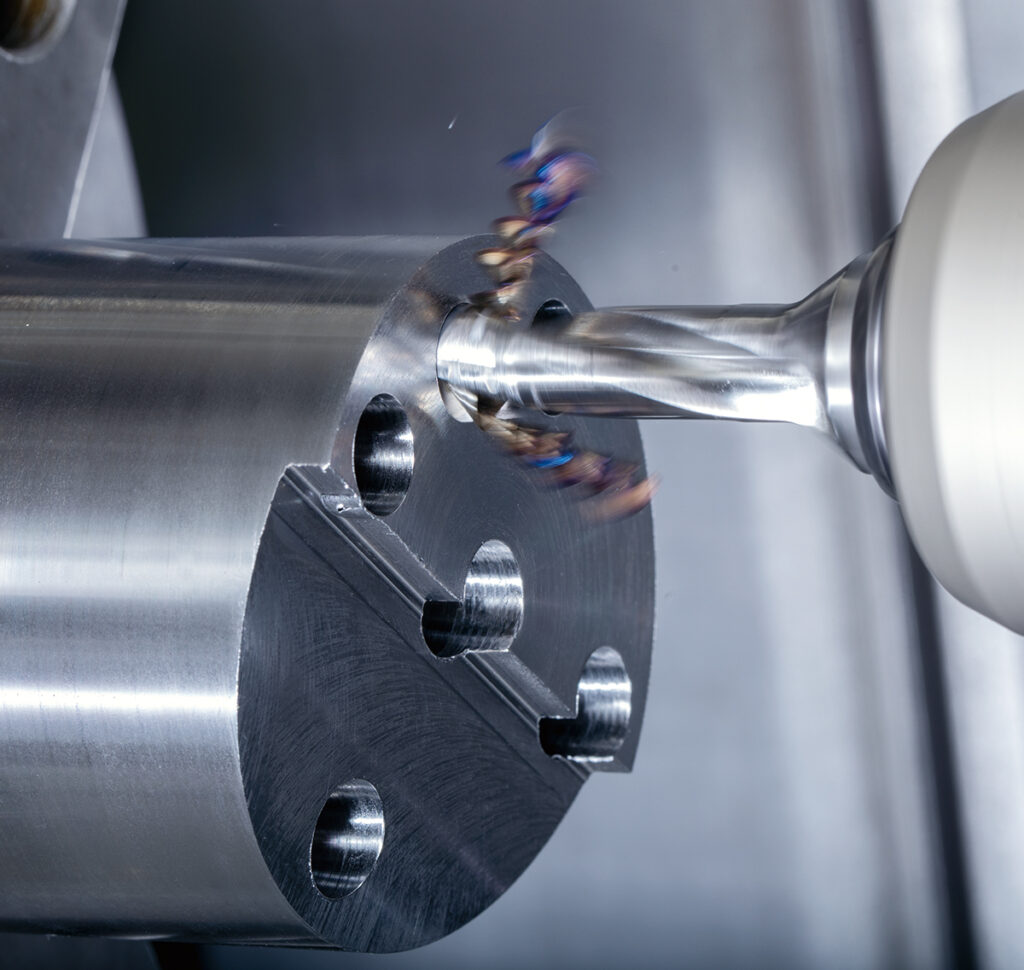
外部給油での重要ポイント
1. 適切な切削速度と送りの選定
外部給油環境では、切削速度と送り速度を適切に設定することが重要です。一般的には、切削速度と送りをカタログの中央値の80%に設定することで安定した加工が可能となります。例えば、ø10程度の2枚刃のドリルの場合、一般的な炭素鋼(S55Cなど)では切削速度40~90m/min、送り0.15~0.2mm/rev程度が安定した切削条件になります。
2. クーラント供給の重要性
クーラントの供給はドリル全体にかかるようにホースの位置を調整し、可能な限り多くのクーラント量を確保することが重要です。特に穴深さが2×Dを超える場合は、切りくず排出促進のために1~3mmごとにドゥエルないしステップ加工を行うことが推奨されます。
3. 刃先の熱管理
刃先の熱を抑えるために切削抵抗の低いドリルが外部給油加工では優位です。例えばヘッド交換式ドリルDrillMeisterの場合は、低抵抗なDMPヘッドを選択し、クーラント濃度をなるべく濃く、例えば10%程度に設定することが有効です。これにより、刃先の冷却と潤滑が適切に行われ、加工の安定性が向上します。
加工トラブルの対策
1. 切りくず詰まりの防止方法
外部給油環境での切りくず詰まりは、ドリル加工における主要なトラブルの一つです。これを防ぐためには、切削速度と送り速度の適切な設定が重要です。さらに、ドリルのフルートに切りくずが効率よく排出されるように、クーラントの供給量を増やし、ホースの位置を調整してドリル全体に均等にクーラントが行き渡るようにする必要があります。
3. 加工プログラムの使い分け
外部給油環境でのドリル加工において、適切な加工プログラムを選択することは非常に重要です。以下に、代表的な加工プログラムの概要を示します。
- G81: 通常の穴あけ加工に使用される基本的なドリルサイクル。
- G83: ステップ加工を行うサイクルで、一定の深さごとにドリルを引き戻し、切りくずを排出。
- G73: 高効率ステップ加工サイクルで、引き戻し量が小さく、効率的な加工が可能。
G81, G83, G73の詳細とメリット・デメリット
1. G81の詳細とメリット・デメリット
詳細: G81は直線的に穴をあけるサイクルで、切りくずの排出を考慮しない。
メリット: シンプルで高速な加工が可能。
デメリット: 深穴加工や切りくず詰まりのリスクがある場合には不向き。
2. G83の詳細とメリット・デメリット
詳細: G83は一定の深さごとにドリルを引き戻し、切りくずを排出する。
メリット: 切りくず詰まりを防ぎ、深穴加工に適している。
デメリット: 加工時間が長くなる場合がある。
3. G73の詳細とメリット・デメリット
詳細: G73は小さな引き戻し量でステップ加工を行う。
メリット: 効率的な切りくず排出と高速加工が可能。
デメリット: 材料や加工条件によっては、G83ほどの効果が得られない場合がある。
ステップサイクルとドゥエルサイクルの適用
1. ステップサイクルの詳細とメリット・デメリット
詳細: 一定の深さごとにドリルを引き戻し、切りくずを排出する方法。
メリット: 切りくず詰まりを防ぎ、深穴加工で効果的。刃先の冷却効果が高い。
デメリット: 加工時間が長くなり、効率が低下する場合がある。引き戻し時に切りくずが嚙み込むリスクがある。
2. ドゥエルサイクルの詳細とメリット・デメリット
詳細: ドリルを一時停止させ、刃先の冷却を行う方法。
メリット: 刃先の冷却が効果的で、特に縦型マシニングセンターで有効。
デメリット: 切りくずがフルートに残留しやすく、切りくず処理に工夫が必要。嚙み込みリスクが低いが、冷却効果がステップサイクルに劣る場合がある。
具体的な加工事例
お客様での活用事例
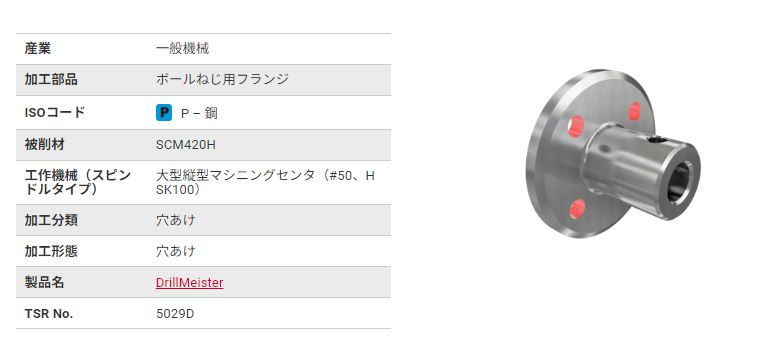
機械がセンタースルーが使えないため、これまでヘッド交換式ドリルの使用を控えていた。
経済性に優れるDrillMeisterの外部給油ボディを使用した結果、ハイスドリルと比較して条件を改善し、工具寿命を延ばすことができたため、DrillMeisterの採用に至りました。
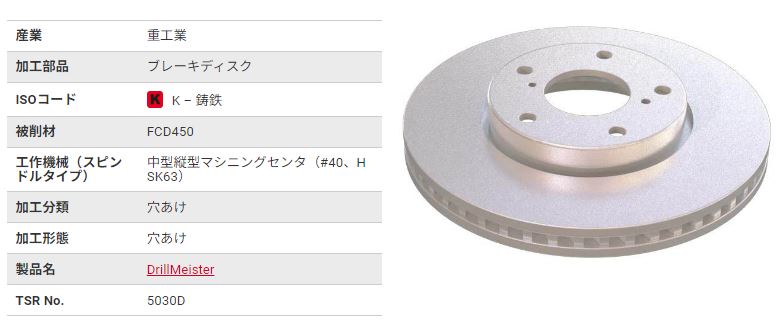
現在、ディスクの穴あけにはハイスドリルを使用していた。 加工効率の向上と段取り時間の短縮のために、DrillMeisterが提案されました。 外部給油のため条件を上げることはできなかったが、ハイスドリルに比べて加工能率は3倍、工具寿命は5倍に向上し、DrillMeisterへの切り替えにつながった。
効果的なドリル選定とその結果
成功事例からもわかるように、適切なドリルと加工条件を選定することで、外部給油環境でも高い加工品質を維持することが可能です。特に、刃先の冷却と切りくずの排出が重要なポイントとなります。
まとめ
外部給油環境でのドリル加工は、多くの技術者にとって課題となることが多いですが、適切な方法やコツを理解することで、トラブルを最小限に抑え、安定した加工が可能となります。本記事では、外部給油環境でのドリル加工の基礎知識、重要なポイント、加工トラブルの対策、適切な加工プログラムの選択、具体的な成功事例を紹介しました。これらの情報を基に、外部給油環境でのドリル加工に自信を持って取り組んでいただければ幸いです。成功の鍵は、適切な準備と継続的な改善にあります。
さらなる情報
オンラインセミナーはこちら
タンガロイでは技術テーマ別のオンラインセミナーアーカイブを配信しています。
お申込みいただければ、無料でいつでもどこでも視聴ができます。
オンラインセミナーアーカイブ配信
「穴あけ加工の基礎!穴あけ工具の選定と上手な使い方をご紹介」
・1枚刃ドリルの切削メカニズム
・工具選定時の確認事項
・穴精度(径精度・真円度/円筒度・真直度・位置度)
・切り屑処理のコツ
・旋盤で使用する際の芯高確認と調整
・外部給油加工時で気を付けるポイント