
これは、タンガロイの営業担当がお客様とともに歩んだ成功への道である。
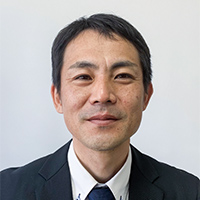
タンガロイ営業担当
平川 浩志Koji Hirakawa
- 出身
- 静岡県
- 社歴
- 12年(入社2010年)
- 趣味など
- スポーツ(野球)
今回は新たな加工方法に挑戦した生産性改善のストーリーである。
大弥精機株式会社
静岡県磐田市に拠点を構える大弥精機株式会社様は、工作機械部品とスピンドルの製造を専門とし、スピンドルの開発・設計から加工・組み立てまで対応可能なエンジニアリング会社である。自動車業界・電子機器業界・電子部品業界など多種多様なスピンドルを製造してきており、その累計出荷本数は10,000本を超える。まさにスピンドル製造のスペシャリスト集団である。
そんな大弥精機株式会社様の強みは、スピンドル製造のための豊富な経験とノウハウに基づく高い技術力である。「ハンドメイドによる1本からの最高品質」をキャッチフレーズに、OEMからオリジナル品までお客様のニーズに合った様々な製品の製作実績がある。また従業員の平均年齢が34歳と若い力を原動力に、「スピンドル技術の頂点を目指す!」を掲げて更なる技術開発と品質向上に日々取り組まれている。
大弥精機株式会社 会社紹介Movie
新規顧客開拓での出会い
大弥精機株式会社 萩田グループリーダーと担当営業の平川の出会いは約6年前の事であった。その当時平川は、多くの加工業者様が拠点を構え、大弥精機様も拠点を構える工業団地に定期訪問し、これら会社に工具提案を行うことを日課としていた。中でも社屋と看板が一際目立つ大弥精機様に何かご提案が出来ないかと考えていた。その当時は、大弥精機様との取引は少なかったので、心機一転、大弥精機様に飛び込んでいったのであった。そこで萩田グループリーダーと出会い、そこから足繁く通う中で様々な加工や改善のご相談を頂くようになった。「気がつけば、いつの間にか横にいた」と萩田グループリーダーは平川に対しての印象を述べられている。
スピンドル軸製造のボトルネック工程
大弥精機様の主力部品であるスピンドル軸の加工には大きなボトルネック工程があった。スピンドル軸はその形状上、1部品の中に外径が大きな箇所と小さな箇所が混在している。外径が小さな箇所は素材からの取り代が多いため、この外径荒加工工程での加工時間の長さがスピンドル軸加工におけるボトルネックになっていた。また、この外径旋削を担っている工作機械はその他にも内径加工やねじ切りなど多種の加工も担っており、外径旋削工程の加工時間の長さが他工程の仕事を圧迫していた。「新規設備導入も多額の投資が必要になるため、この外径荒加工工程の加工時間を短縮することが本加工ライン改善のキーポイント」と萩田グループリーダーは考えていた。
スピンドル軸加工のイメージ
- 加工前素材:
- 加工後のワーク形状:
多⽅向旋削加⼯⽤工具AddMultiTurn(アド・マルチ・ターン)による後挽き・高送り加工への挑戦
萩田グループリーダーからスピンドル軸加工の課題を聞いた平川は、『多⽅向旋削加⼯⽤工具 AddMultiTurn』を使用した後挽き・高送り加工がこの課題解決に役立てるのではないかと考えた。
『AddMultiTurn』は、外径加工、端面加工、倣い加工及び後挽き加工等、あらゆる方向に加工可能な新発想の旋削加工用工具シリーズである。『AddMultiTurn』の最大の売りは、後挽きによる高送り加工である。『AddMultiTurn』は独自の切れ刃形状を有しており、後挽きで使用する側の切れ刃の切込み角が21.5°と浅い高送り刃型になっている。切込み角を小さくすることで、生成される切りくずの厚みを薄く出来るため、一般的なISO形状のインサートを使用した旋削工具(CNMG,WNMG,TNMG,DNMGなど)よりも200%以上高い送りの適用が可能な工具である。平川が提示した提案内容は「AddMultiTurnにより後挽き加工を行い、現状倍以上の高送りを狙う」であった。
平川からこの挑戦的な提案を受けた萩田グループリーダーは、後挽きによる外径旋削加工の経験がそれまで無かった事や、何より「現状倍以上の送りの適用」という非常に高い送りの適用と高送りによる切削負荷の増加に多少の不安を覚えた。
しかし、萩田グループリーダーは新しいものや革新的なものにはどんどん挑戦することを信条にしており、今回の平川の提案も「考える前にやってみろ!」の精神でトライアルの実施を決めたのであった。
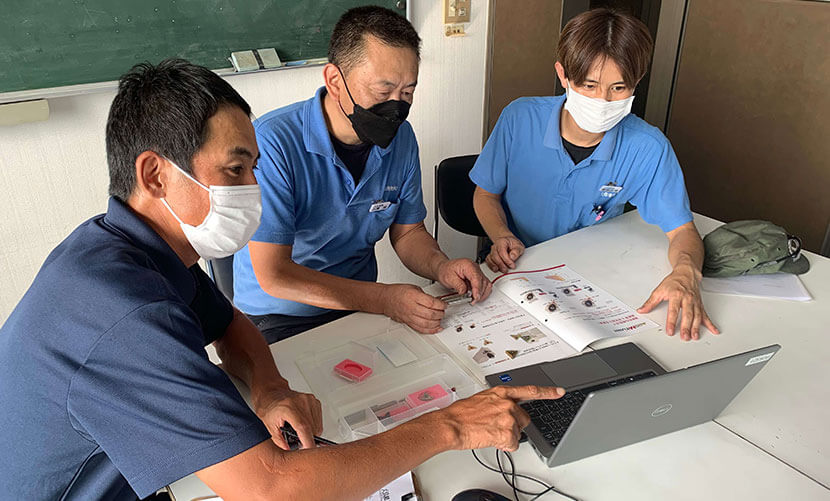
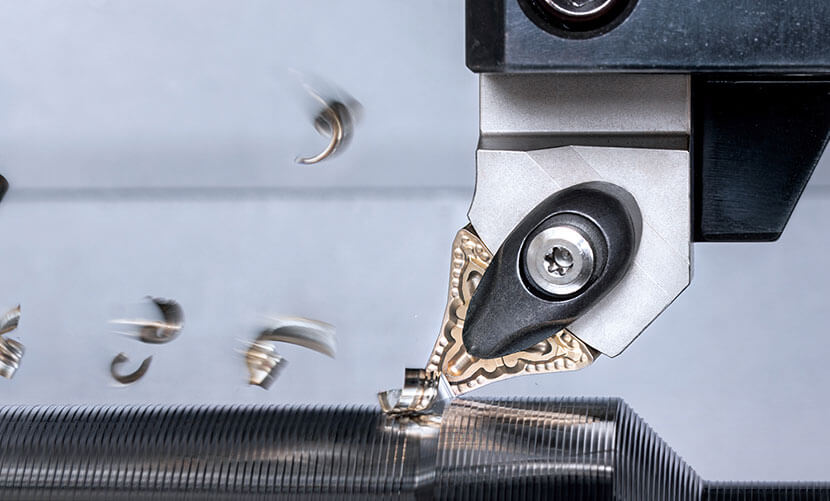
加工時間1/3の短縮に成功!
萩田グループリーダーは工具の味見を行う初回テストに臨んだ。初回のデモ加工では送りをあげても問題なく加工が行えたため、工具の味見としては好感触を覚えた。しかし実生産では加工能率とともに当然高い安定性が求められる。その中で様々な切削条件での検証を進め、タンガロイとしても、切削条件の検証テスト時には、技術サポートエンジニアによる立会を行いながら、切削音や切りくずのチェックやインサート損傷の確認を一歩ずつ進めていった。その結果、実生産でも安定性に優れる最適条件が見つかった。その最適条件での得られた成果としては、
- 従来約40分を要していた加工が約13分と加工時間を1/3まで短縮
- 従来の設定工具寿命が2本/コーナであったところ、3本/コーナと1.5倍に工具寿命を延長
と加工能率と工具寿命の両面での改善という大きな成果が得られたのであった。
旋削工程の加工時間の短縮により、短縮分の時間を他工程の加工に振り分ける事が出来るため、工作機械を新規導入する事なくラインの業務負荷を低減することが出来たことが最も大きな成果であった。
今回の改善ポイント
-
AddMultiTurn後挽き加工の適用により加工能率を改善
被削材:S45C ,ap=2.0mmの加工。切削速度Vc=200m/min(従来比130%up)、送りf=0.6mm/rev(従来比200%up)を適用することで加工時間を従来比1/3まで短縮
-
高送りの適用で工具寿命を1.5倍まで改善
送りの増加で擦過距離が減少。インサート摩耗が抑制され工具寿命が改善
-
ボトルネック工程の加工改善によりラインの業務負荷を低減
外径旋削工程の改善により空いた時間で他工程の仕事をこなせるようになった。新規設備導入をせずにラインの生産能力が向上
更なる改善への挑戦
失敗を恐れず新しい事に果敢に挑戦することが大弥精機様の社風であり、萩田グループリーダーとしても今後も革新的な加工方法への挑戦を継続していくようだ。そんな中、現在トライアルを進めているのは、スピンドル軸のフランジ部に存在する幅が約90mmと大きな取り代がある溝部の加工改善である。本工程は現状、左右勝手の外径バイトを使用した倣い加工で加工しており、約90分の加工時間を要している。この工程に弊社の溝入れ工具『AddForceCut』の高剛性TungFeedBladeタイプホルダでの加工テストを進めて頂いている。「高送り溝加工による突落としに加工方法を変更することで、加工時間を約20分程度まで短縮できそう」とのお言葉を頂いている。
工具メーカーに対する今後の要望は、「おっと!思わせる効果が大きそうな革新的な工具の開発」だそうだ。弊社としても加工の常識を覆せるような革新的な工具の開発に今後も挑戦していきたい。
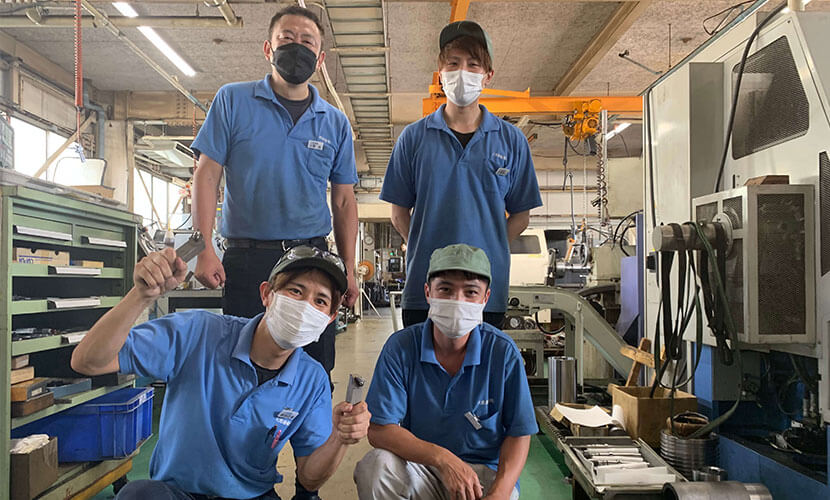
後列左より 小澤さん、江塚さん
前列左より 萩田さん、タンさん
今回ご紹介した製品はこちら
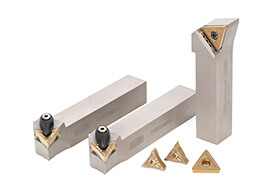
高能率加工を実現する汎用性および経済性の高い6コーナインサート
AddMultiTurn(アド・マルチ・ターン)
1つのホルダで前挽き、後挽き、倣い、端面加工まで幅広い旋削加工に対応