タンガロイ成功事例
刃先交換式
スカイビングカッタの採用で、
パワースカイビング加工の
工具寿命を大幅改善
中里歯車工業(有)
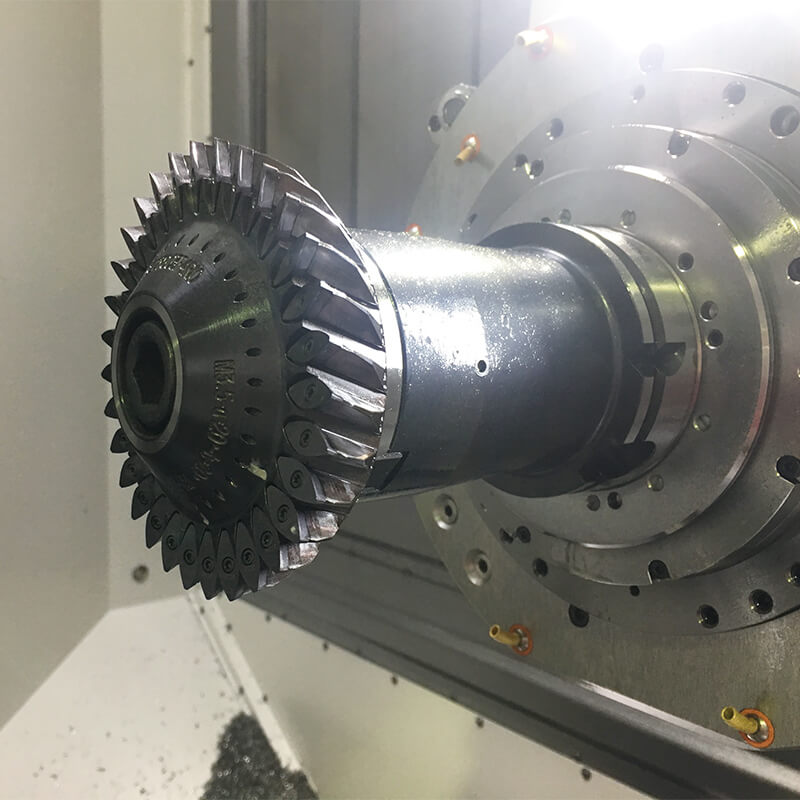
本記事は機械技術2022年9月号掲載分をWeb用に再編集したものです。
歯車のスペシャリストである中里歯車工業㈲(埼玉県川口市)。精密歯車の試作開発から中量生産までを手掛け、特殊歯車や複雑形状部品を得意とする。近年は5軸マシニングセンタ(MC)や複合加工機を活用した歯車加工に取り組み、柔軟な生産体制を構築。新たに導入したパワースカイビング加工では㈱タンガロイ(福島県いわき市)とのコラボレーションによる刃先交換式スカイビングカッタの採用で、生産性向上による短納期化に成功するなど歯車加工の可能性を追求している。
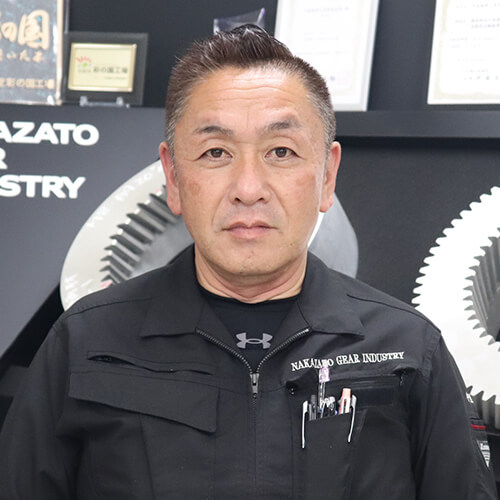
中里 昭宏氏
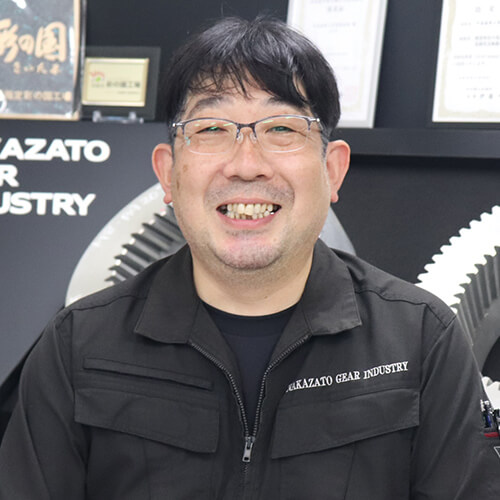
荻原 慎一郎氏
専用機から汎用機へシフト
同社の基盤技術である歯車加工は創業以来の経験、ノウハウをベースに最新の工作機械、工具、CAD/CAMなどのツールを活用し、進化してきた。特に中里社長がこだわってきたのが、製品の高精度化と高能率化による納期短縮である。歯車加工は材料購入から切断、焼きならし、旋盤加工、ブランク検査、歯切り加工、切削加工、防炭処理、焼入れ、シャフトひずみ取り、研削工程、完成品検査と多数の工程が必要となる。歯切りにNCホブ盤、歯の研削には歯車研削盤など専用の工作機械を使い量産に対応するのが一般的だ。
同社も創業以来、専用機を用いた歯車製造に取り組んできたが「高精度歯車の試作ニーズが増える中、専用機では工具の発注などで納期が延びてしまう。そこで納期を短縮するために着手したのが5軸MCや複合加工機を使った歯車生産へのシフト」(中里社長)であった。量産を前提とした専用機では段取り替えにも時間がかかり、試作をはじめ多品種変量への対応が難しい。汎用機によって工具交換などのフレキシビリティを向上し、付加価値の高いモノづくりを実現することが狙いだ。
パワースカイビングによる短納期化に着手
5軸MCや複合加工機でスパイラルベベルギヤや平行軸を持つ歯車などを手掛けていく中、次に同社が着目したのがパワースカイビング加工だった。同加工はワークと工具を同期して高速回転させながら歯の溝をそぎ取る(Skive)ようにして歯車を創成する工法である。加工速度、精度ともに優れ、歯すじ修正が容易で加工自由度が高いなど利点が多く、納期短縮が期待できる。また、複合加工機を活用できるので複数の専用機が不要で工程集約を図れることも大きな魅力だ。中里社長は「10年ほど前にインターネットの動画を観て衝撃を受け、そこから手探り状態で始めました」と振り返る。
最大のネックは工具寿命だった。高速回転で加工速度はホブ盤の10倍以上となる一方、工具摩耗が激しい。現場で陣頭指揮を執る荻原慎一郎技術部長/副工場長は「最初に現場で披露したときは一瞬で工具が壊れ、興味津々に集まった社員が静かに持ち場に帰っていった姿は忘れません」と多難なスタートだったと打ち明ける。
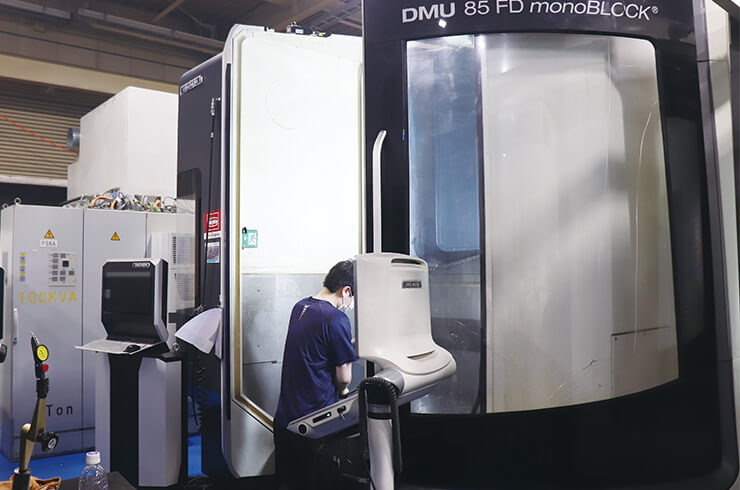
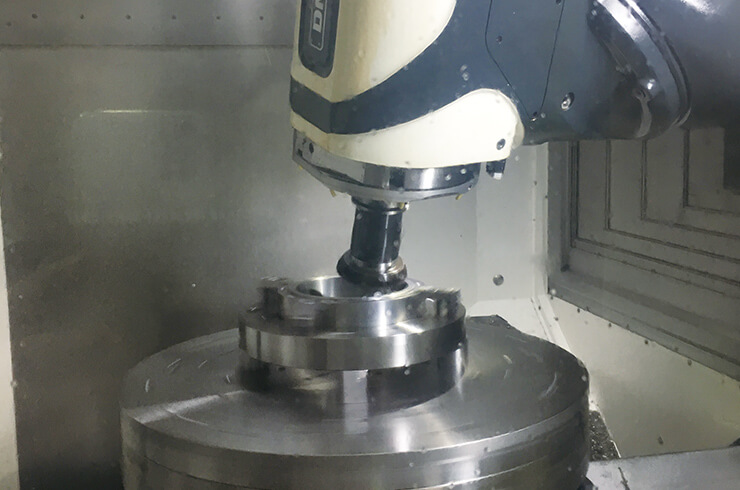
荒加工工程での工具寿命を3倍に
その後はサポインなど公的補助金を活用し、工作機械メーカーや工具メーカーも交えて試行錯誤を繰り返し、18年にパワースカイビング加工の実用化にこぎつけた。難易度が高かったヘリカルインターナルギヤの加工を受注するなど業容拡大にも結び付き始めた。課題であった工具寿命に寄与したのがタンガロイとのコラボレーションから採用した刃先交換式スカイビングカッタだった。
「当初は荒加工から仕上げまでソリッドのハイスカッタを使っていましたが、特に荒加工での工具寿命が短く、再研削費用も高い。そこで超硬工具を扱うタンガロイから提案されたインサート式スカイビングカッタが決め手となりました」(荻原技術部長)。
対象となったギヤはモジュール5の大型サイズで鋳鉄のFCD450という高硬度の削りにくい素材だった。タンガロイでは中里歯車工業の要望を受け、加工時の滑り速度をアップさせるための改良を加えた結果、最終的に工具寿命を3倍に延長することに成功した。加えて、超硬工具に切り替えたことで切削のサイクルタイムが15%改善し、「予期せぬ効果」(荻原技術部長)も得られた。
三位一体のものづくり
「すでにモジュールのバージョンを増やしており、鋼の調質した製品でも荒加工~仕上げという形をとれば十分加工できるとみています。次の目標としてはウォームホイルへの適用です。従来、ホブ盤でしかできなかった加工もMCでモデルをつくれば可能」(荻原技術部長)とし、タンガロイとの連携による工具開発を進めているところだ。
中里社長は「つくり手と工具メーカーが一体となることで相乗効果が得られるという、いい経験をさせてもらっています。使い手、工具、機械が三位一体となれば専用機を追い越せる確信が持てました。製造業が変革期を迎える中、これからが正念場。歯車加工を柱に周辺部品にも事業領域を広げていきます」と歯車加工を核とした技術革新への挑戦に意欲を示す。