
Gear skiving with Tungaloy´s innovations
How an indexable skiving cutter significantly improved tool life for a gear milling process
Nakazato Haguruma Co., Ltd.are especially skilled in making special gears as well as parts in complicated shapes and handle a wide variety of projects from developing prototypes to manufacturing gears in medium volumes. Recently, Nakazato Haguruma has implemented gear milling processes using a 5-axis machining center (MC) and multitasking machines to build up a flexible production system. In search for further improving their productivity, the company adopted Tungaloy’s indexable skiving cutter to their new power skiving process (Tungaloy´s Gear Milling Solutions).
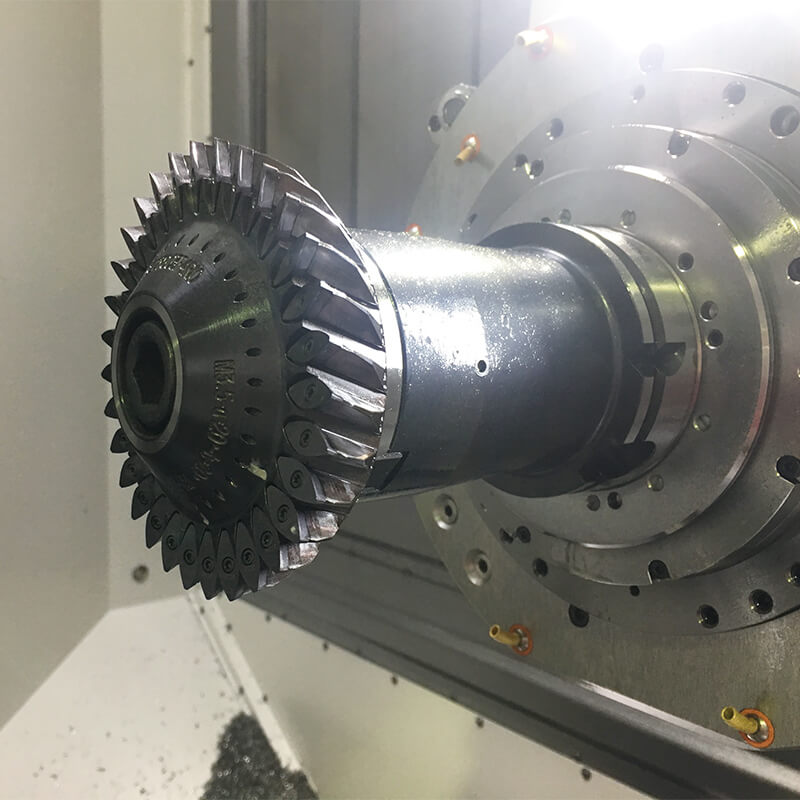
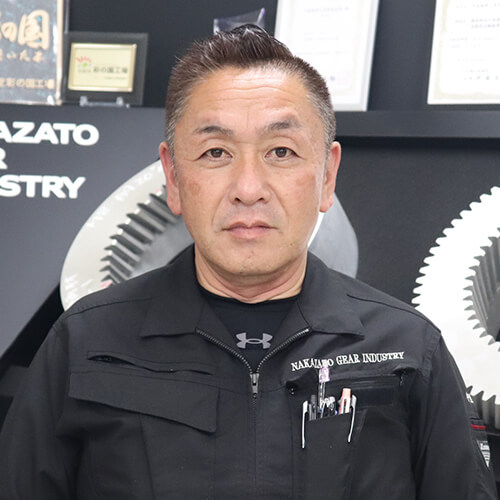
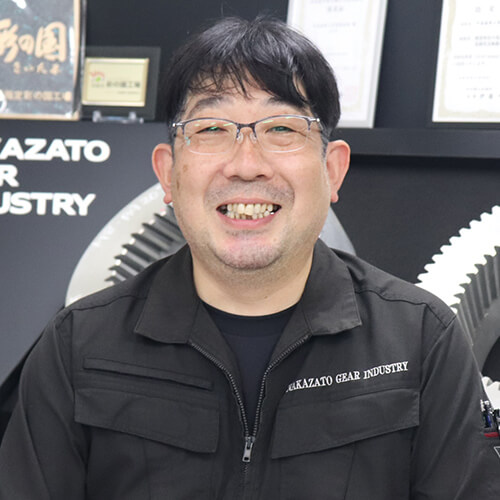
Shinichiro Ogihara
This article has been modified for the web format from the September 2022 issue of Japanese magazine “Kikai Gijyutsu.”
A shift from the specialized gear machines to the general-purpose milling machines
Nakazato Haguruma had polished its gear machining technology over the years by applying the latest machines, tools, CAD/CAM software, etc. to the experiences and know-how the company had built up since its foundation. President Nakazato especially strived to shorten their delivery time by improving the precision and efficiency of their production processes. Gear machining requires many processes such as material purchase, blanks cutting, normalization, lathe operation, blanks inspection, gear machining and milling operation, carburization treatment, quenching, shaft strain relief, grinding, and finished product inspection. Considering the numerous steps involved in the process, it is common to use specialized machines even for mass production, like NC hobbing machines for gear cutting and gear grinders for grinding teeth.
Since its foundation, the company had also followed this pattern and manufactured gears using specialized machines. However, President Nakazato found limitations in such a machining method. With the increasing requirements for highly precise prototype gears in various quantities, the company had to constantly order tools for the specialized machines, which prolonged their production times. Using specialized machines for mass production also required a long time to change tool setups. This is when he decided to adapt 5-axis MCs and multitasking machines in their production floor. With general-purpose machines, he was certain the company will be more flexible in tool exchange and other functions and be able to improve the overall productivity.
Shortening the production time with power skiving
While working on spiral bevel gears and gears with parallel axes using 5-axis MCs and multitasking machines, President Nakazato put his eyes on the power skiving technology. This is a method where gears are created by synchronizing the workpiece and the tool, rotating them at high speed while scraping off the grooves of the teeth (skive). It has many advantages, such as excellent processing speed and accuracy, easy tooth trace correction and high degree of processing freedom, and shortened production time. In addition, the ability to use multi-tasking machines eliminates the need for multiple specialized machines, making it possible to consolidate production processes. Looking back, President Nakazato recalls, “About 10 years ago, I saw a video of a power skiving process on the Internet, and I was shocked. Since then, we had used the method with trial and error.”
The biggest bottleneck was the tool life. The high-speed rotation made the machining speed more than 10 times faster than that of the hobbing machine, and tools quickly wore out. Shinichiro Ogiwara, Engineering Manager and Deputy Factory Manager who managed the production floor, said, “I will never forget the moment when our staff excitedly gathered around the machine for its first demonstration and the tool immediately broke. They all returned to their posts quietly with disappointments in their faces.” It was a very difficult start for the company.
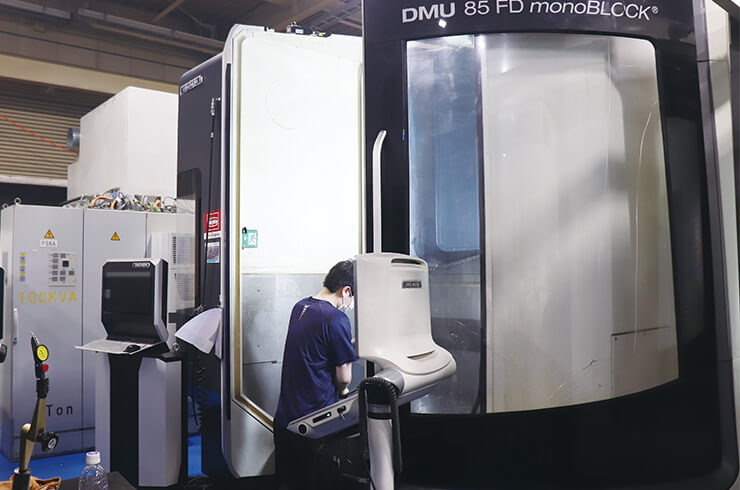
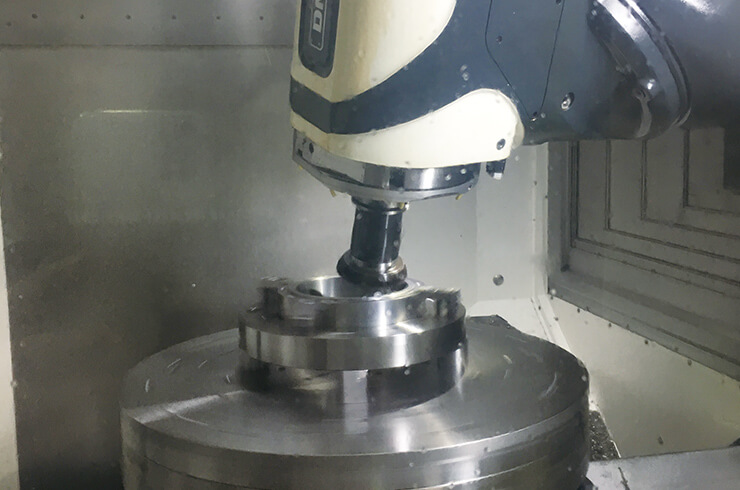
Tripled tool life with Tungaloy´s unique gear skiving technology
After the discouraging incident, Nakazato Haguruma repeated trial and error with machine and tool manufacturers using the help of public subsidies. Finally in 2018, the company succeeded to put power skiving technology into practical use. It began to lead business expansion as it helped Nakazato Haruguma receive orders for complicated projects, like processing helical internal gears. An indexable skiving cutter was the key to solving the problem of tool life, and it was offered by Tungaloy.
“At first, we used a solid high-speed-steel cutter from roughing to finishing processes, but the tool life was especially short in the roughing operation. Regrinding cost was also high. When Tungaloy, well-known for its carbide tools, proposed us an indexable skiving cutter, we decided to go for it,” said Ogihara, the Engineering Manager and Deputy Plant Manager.
The target gear component was a module 5-size, made of cast iron FCD450 material with high hardness. In response to Nakazato Haguruma’s request, Tungaloy added improvements to its cutter to allow higher sliding speed during the machining process, and the team succeeded to extend the tool life by three times the original tool. In addition, switching to carbide tools improved the cutting cycle time by 15%, yielding an “unexpected benefit” as Engineering Manager and Deputy Plant Manager Ogihara put it.
Tungaloy´s innovative gear skiving solution
- Indexable skiving cutter for rough gear milling operations
- Indexable inserts for easy tool management, no grinding required
- Economically efficient 2-cornered insert
- Adopts an insert peripheral shape that optimizes the machining allowance for finishing operations
- Longer tool life than HSS skiving cutters because of carbide-coated inserts
- Even higher efficiency achieved with increase in the rotation speed of the workpiece
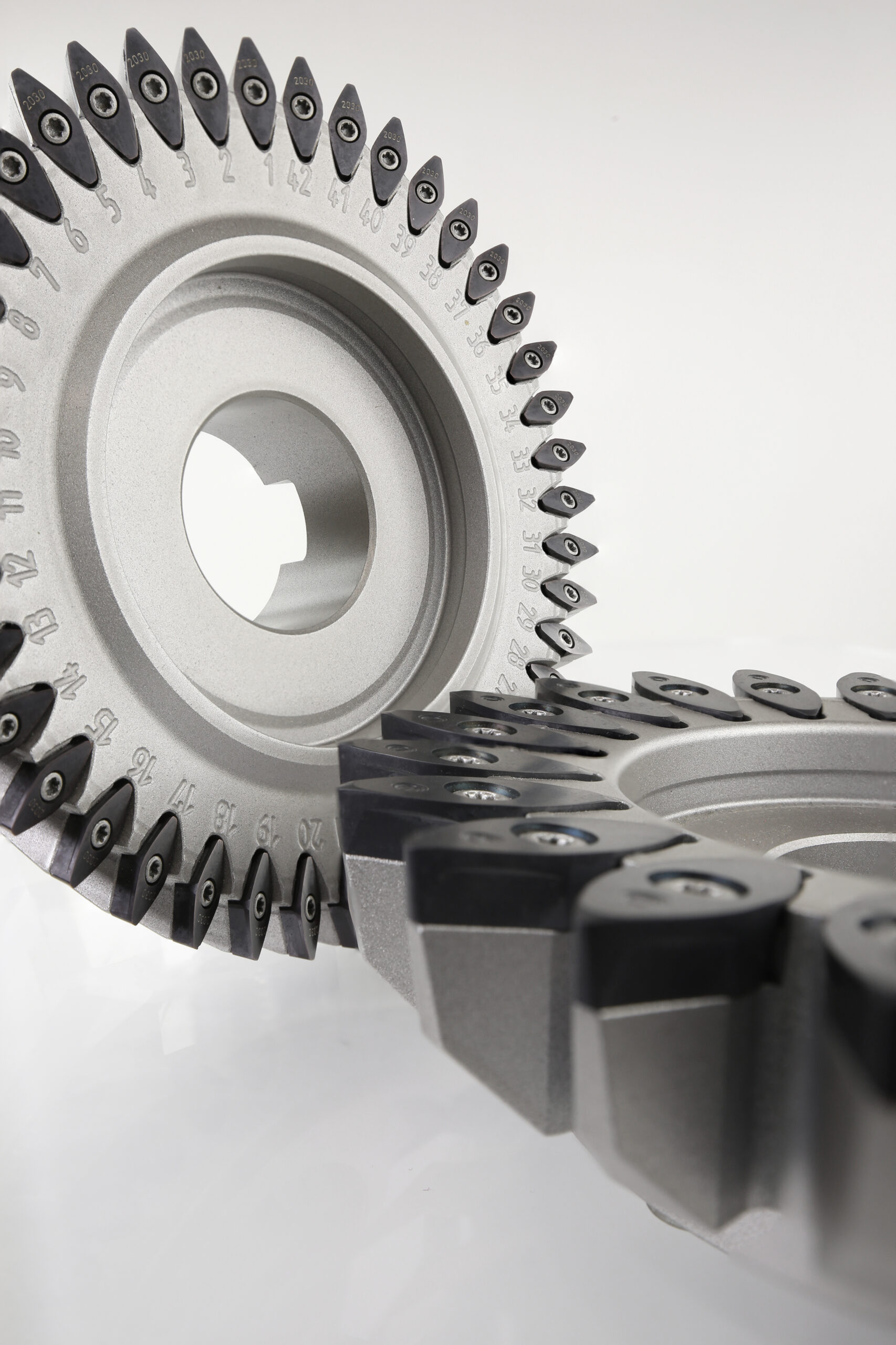
Synergy among the producer, tool manufacturer, and machine manufacturer
“We have already increased the number of module versions and believe that we can even machine products made of steel with roughing to finishing operations. Our next target is applying it to worm wheels. Machining worm wheels could only be done with hob machines in the past, but a MC can do it if we create a 3-D model,” said Ogihara, and Tungaloy is currently working with the company on developing a tool that meets their requirements.
President Nakazato said, “There is a big synergy going on between Tungaloy and us, and I am very happy I realized it. I am convinced that if the producer, the tool manufacturer, and the machine manufacturer work together, then we can outperform specialized machines. Adaptability is the key to success in today’s rapidly changing manufacturing industry, and we will continue polishing our gear processing techniques and also expanding our business operations to include machining peripheral parts.” Nakazato Haguruma is ready to take on the challenge to advancing their gear machining technologies.