Iwaki, Japan – April, 2025 – Tungaloy Corporation (President: Satoshi Kinoshita, Head Office: Iwaki City, Fukushima Prefecture) announces the expansion of its TungCut series with new 3D chipbreaker-equipped CBN inserts, offering excellent chip control in profiling of hardened steel, featuring wear-resistant BXA10 grade and WavyJoint structure for extended tool life.
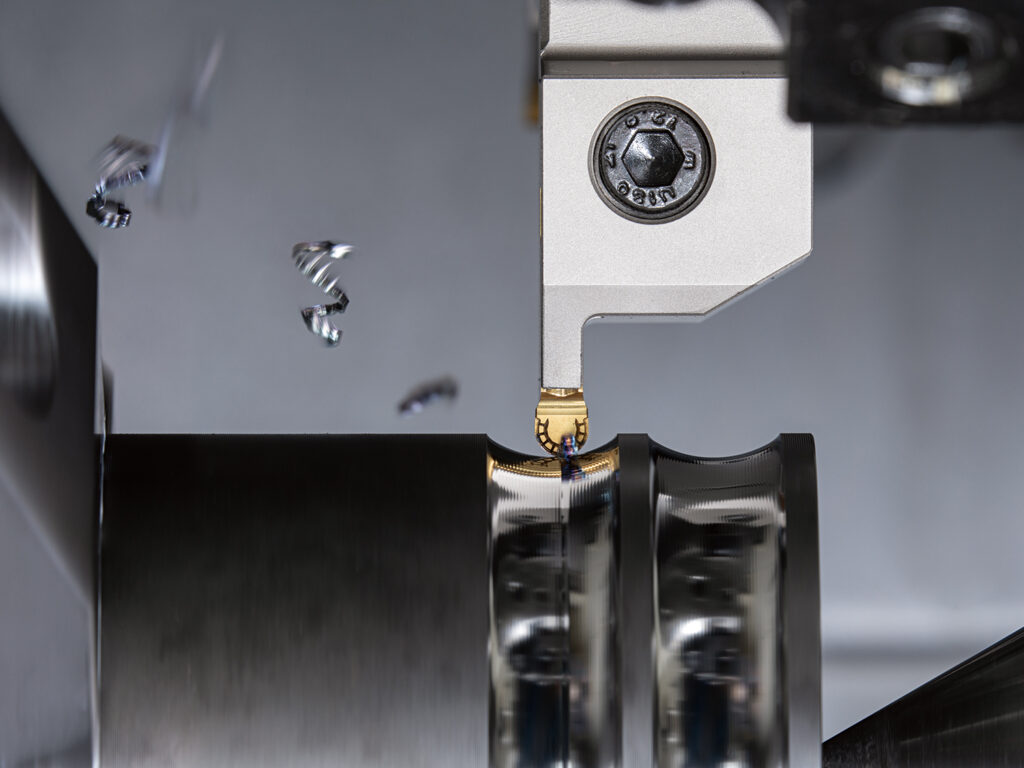
Challenges and Trends
In the finish profiling of hardened steel components such as bearings, rolls, and mold parts, the use of CBN inserts is common. However, conventional CBN inserts lack chip breakers, leading to significant challenges in chip control.
This is especially problematic in profiling with full-radius inserts, where chips tend to entangle with the tool, workpiece, or chuck, causing unexpected machine stoppages, deterioration in surface quality, and sudden insert breakage.
These issues represent major barriers to stable machining and improved productivity.
Product Overview
TungCut is a high-performance tool specialized for grooving and parting-off operations. Its advanced grade selection system enables a wide range of machining applications, while the multifunctional series allows for tool consolidation.
With exceptional insert clamping rigidity and a high-rigidity holder design, TungCut ensures stable tool life and precision. Additionally, its unique breaker geometry enhances chip control and suppresses vibrations.
Featuring a unique insert clamping design, it offers both economic efficiency and high rigidity, delivering outstanding performance in various machining environments.
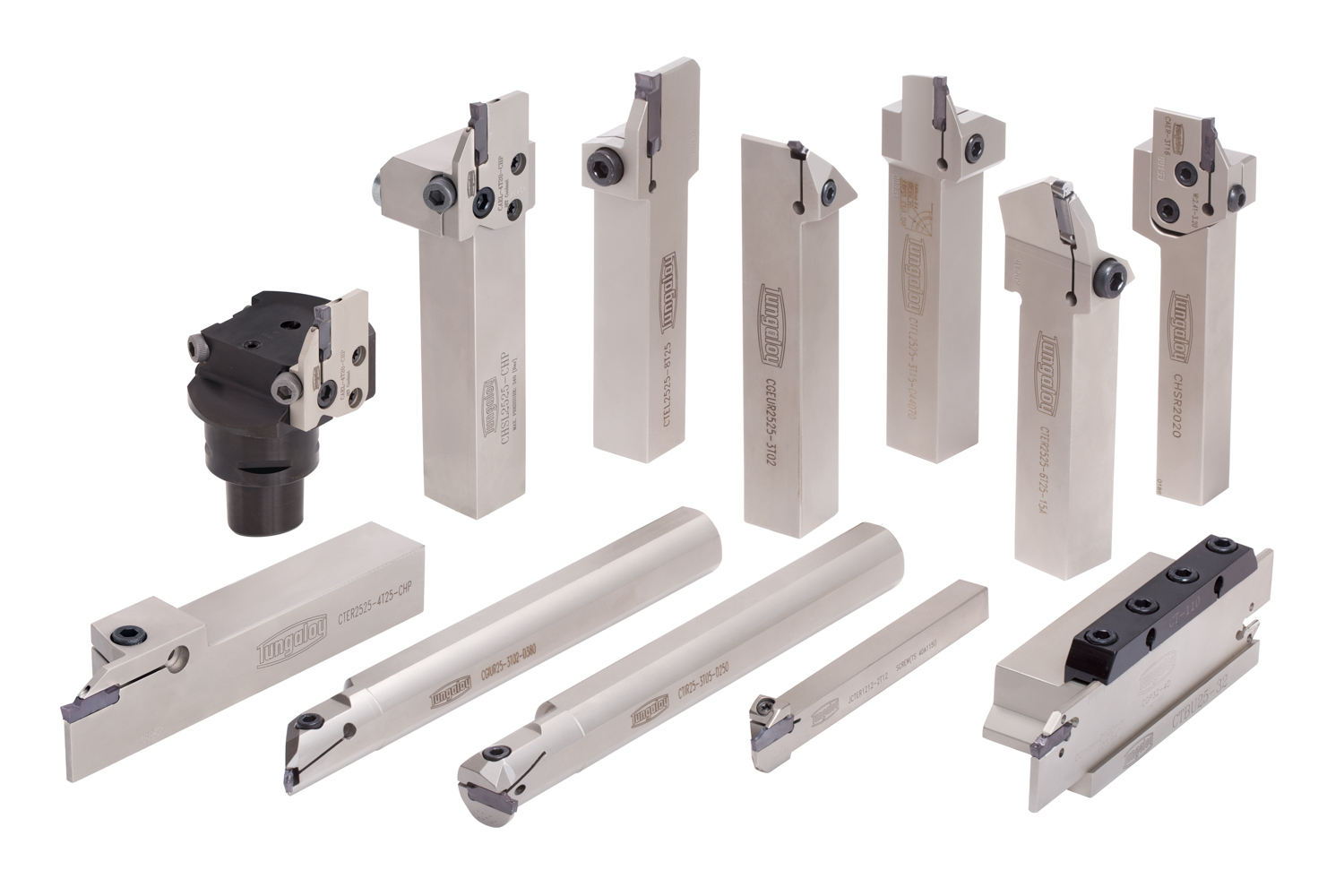
Benefits and Features
Feature 1: 3D Chipbreaker Design Ideal for Copying Applications
The 3D chipbreaker shape controls chips in multiple directions, enabling stable chip evacuation.
Grooves integrated into the breaker promote cutting fluid flow, enhancing cooling performance at the cutting edge.
By suppressing temperature rise at the cutting edge, tool wear is reduced and tool life is extended.
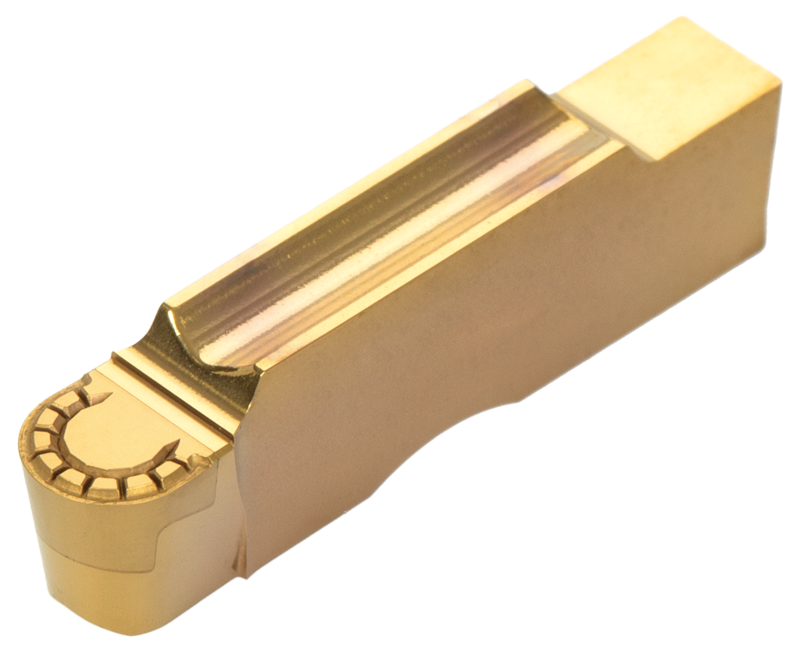
Feature 2: Long Tool Life with High Wear-Resistant BXA10 Grade
Utilizes BXA10, a highly wear-resistant CBN substrate, significantly improving tool life in hardened steel machining.
Delivers stable cutting performance even on high-hardness materials, ensuring machining reliability.
Maintains dimensional accuracy during extended continuous machining, reducing tool change frequency.
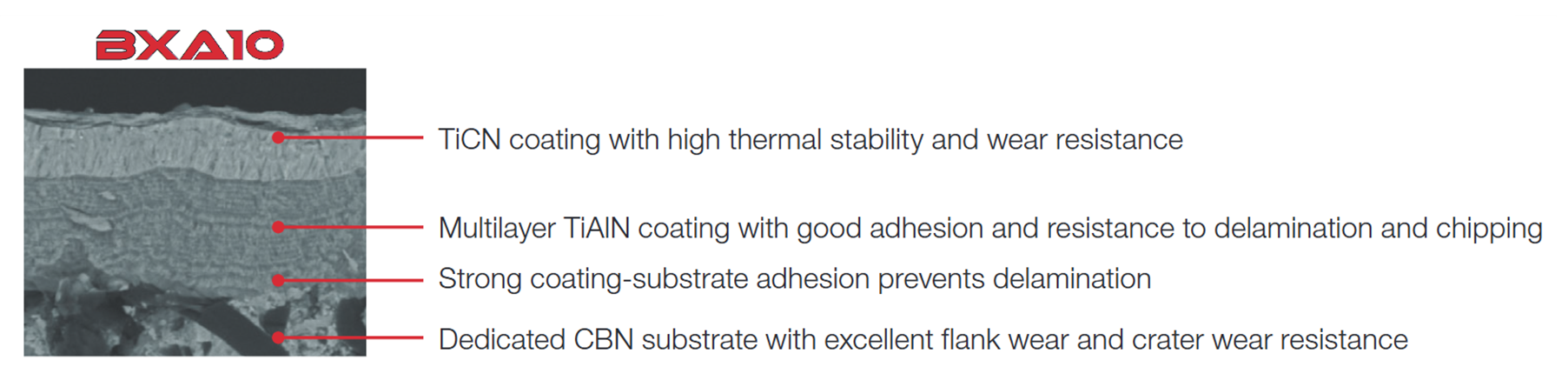
Feature 3: High-Strength CBN Brazing Technology with WavyJoint
Proprietary brazing technology “WavyJoint” maximizes the bonding area of the CBN tip.
Improved joint strength and thermal conductivity reduce breakage risk during high-load machining.
Enhanced heat dissipation minimizes thermal damage during cutting, ensuring both stability and long tool life.
Cutting performance
CHIP CONTROL IMPROVEMENT
STR-type inserts with chip breakers provide more stable chip control compared to inserts without chip breakers.
By improving chip control, it is possible to significantly enhance machining reliability.
Success Stories
IMPROVED PRODUCTIVITY AND TOOL LIFE
Ceramic inserts were previously used for the outer diameter profiling of rolls. However, since ceramic inserts lack chip breakers, chip evacuation was unstable. By switching to STR-type inserts with chip breakers, chip control was significantly improved.
As a result, even when the cutting speed was increased by more than two times, the TungCut STR-type CBN insert achieved more than 4 times longer tool life. This led to a significant improvement in both machining efficiency and tool life.
Industry | Engineering |
Component | Roll |
Material ISO code | H – Hardened material |
Work material | SKD11/1.2379 |
Material hardness | 62~64HRC |
Machine(spindle type) | CNC Lathe |
Tool family | Turning |
Tool category | External grooving & turning |
Product name | TungCut |
TSR No. | 5209T |
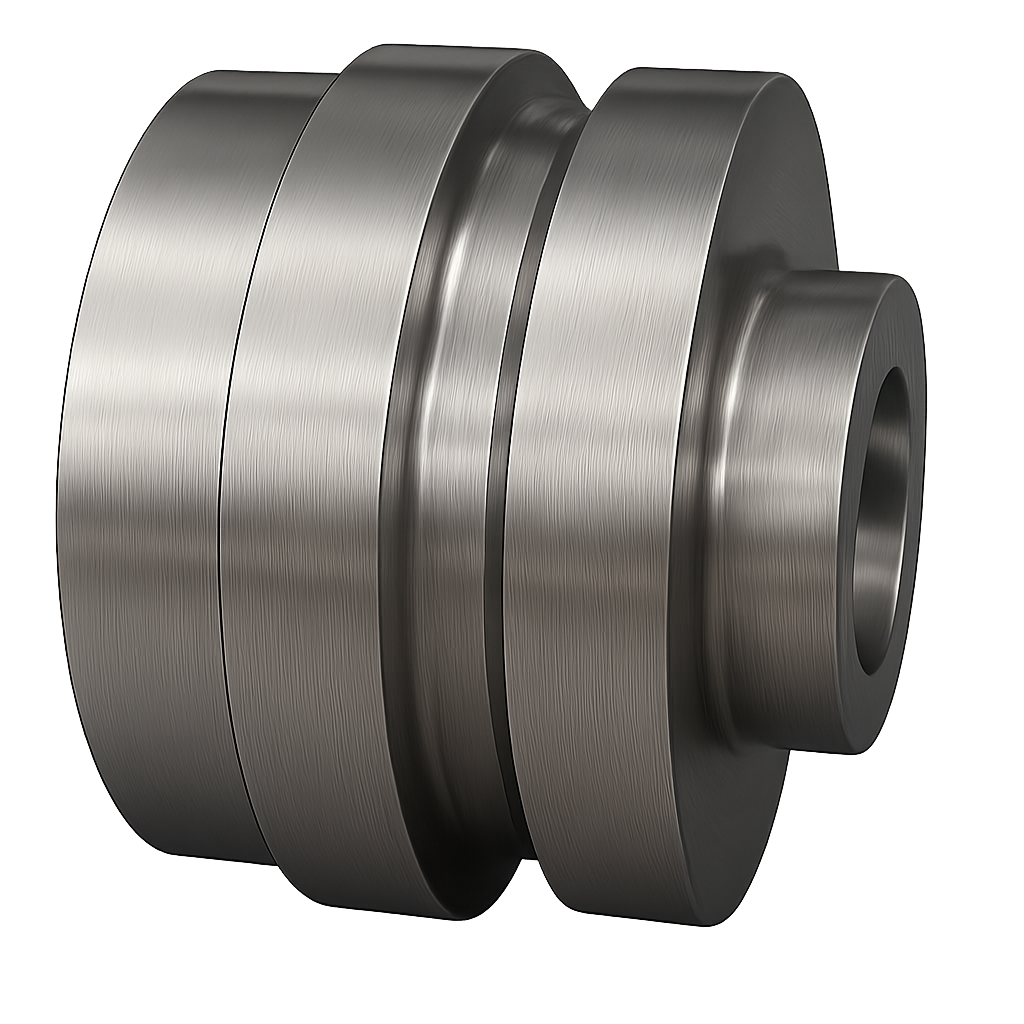
IMPROVED PRODUCTIVITY AND RELIABILITY
A full-radius CBN insert was used for the outer diameter profiling in crush cutting applications.
The conventional insert lacked a chip breaker, resulting in unstable chip control.
By switching to the STR-type insert with a 3D chip breaker, chip evacuation became stable, improving the reliability of the machining process.
As a result, both machining reliability and productivity were improved, achieving a 1.8-fold increase in machining efficiency.
Industry | Engineering |
Component | Crush Cutting Knife |
Material ISO code | H – Hardened material |
Work material | 100Cr6 |
Material hardness | 61HRC |
Machine(spindle type) | Dedicated Machine |
Tool family | Turning |
Tool category | External grooving & turning |
Product name | TungCut |
TSR No. | 5210T |
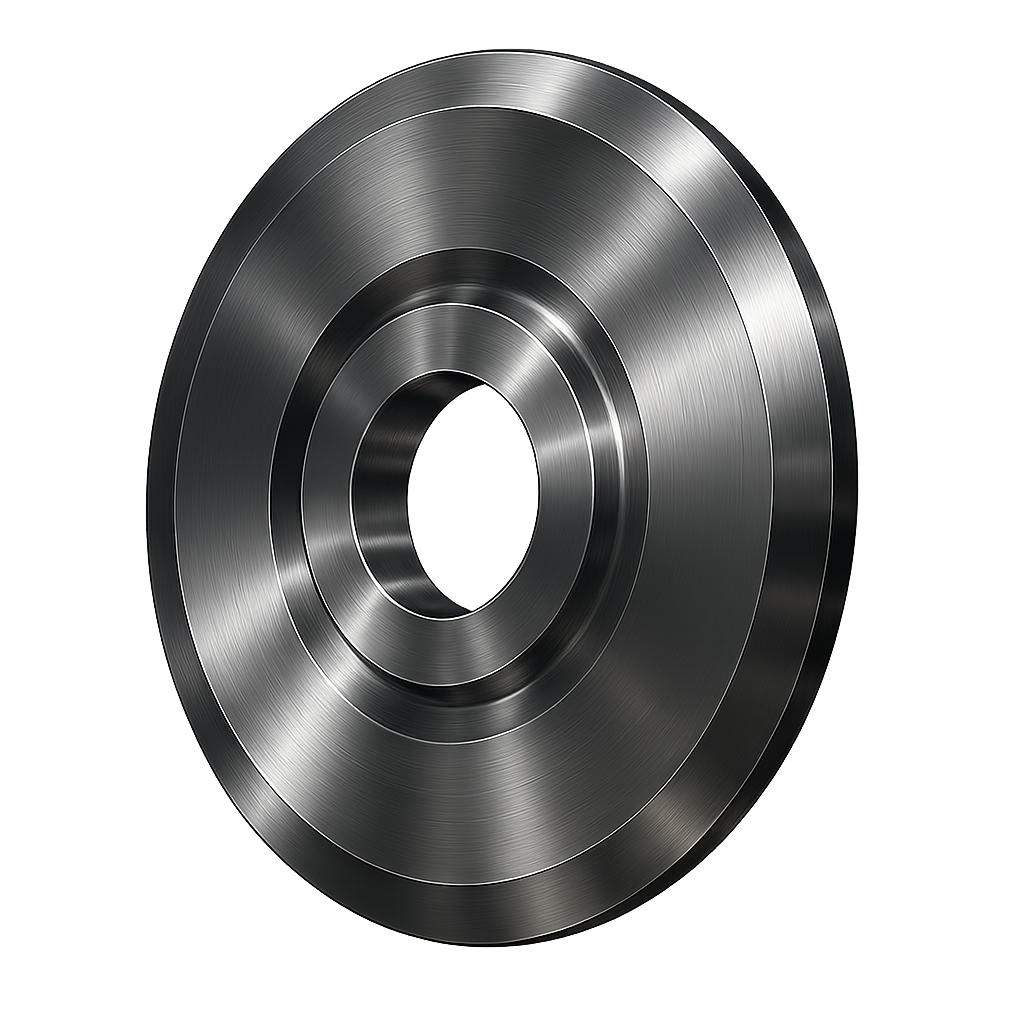