
Ever since the industrial revolution, the human race has constantly worked on productivity improvements. And, creative engineering has made a lot of progress in developing machinery with multiple axes. Y-axis tooling solutions is a sample of this progress.
From a 2 axes CNC lathe tool to a multi axes turn-mill or mill-turn center, the development has continued to progress, from common X-axis tooling solutions to the latest Y-axis tooling solutions.
One operation at a time to multi-tasking has become a state-of-the-art manufacturing process.
Let’s understand the various axes on a basic Turn-Mill center –
X axis – This carries the turret and feeds the tool radially to take the required DOC.
Z axis – This is the component axis.
C axis – This is the rotary axis or the head stock rotation axis, when used in conjunction with a radial or axial live tool on X-Axis. By itself, it cannot be counted as an effective axis.
Y axis – This is an axis perpendicular to the X-Axis. It can either carry a live tool or can take a NRT tool and feed into the component for turning, grooving or parting off.
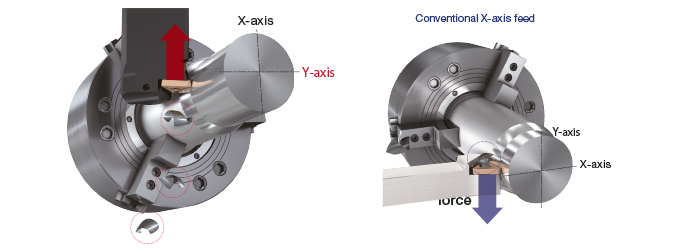
We are already aware of tooling solutions for X-Axis and also for rotary tools which can be used on the live tools for simple operations to be performed on the component.
In this article, we are going to explore Tungaloy’s tooling solutions for Y-Axis and the advantages of using Y-Axis for turning and grooving applications.
Tungaloy has emerged as a leading metal cutting solution provider, with exchangeable head tools, for building stronger Automotive, Aerospace, Equipment and general engineering, infrastructure and railway industries.
Undoubtedly there are many that ask why to use Y-Axis for turning and parting when the processes are already proven with X-Axis. For any change, there are always challenges and when the challenges are met, there are many advantages.
Y-axis Tooling Solutions Advantages:
#1: The First advantage as we can see from the previous image, Y-Axis turning is a more stable operation compared to conventional X-Axis machining. Two major forces acting on the tool are those due to cutting speed and feed. The rotational forces are much higher compared to feed forces. The resultant of these two forces tends to be perpendicular to the tool in X-Axis turning, resulting in deflection while forcing us to reduce the tool overhang. However, in Y-Axis turning, the forces tend to be mostly parallel to the tool’s axis without any tool’s deflection thus resulting in a much more stable machining process.
#2: Y-Axis tools’ premium performance is constant regardless of the overhang since there is no deflection.
#3: The advantage of this stable machining leads to using higher feeds and depth of cuts. Hence, higher productivity is gained with stable tool life.
#4: Chip disposal. Due to the design feature of the Y-Axis tool, the chips are always pushed to the care of gravity. Hence, no chip entangling and no downtime due to machine / automation stoppage.
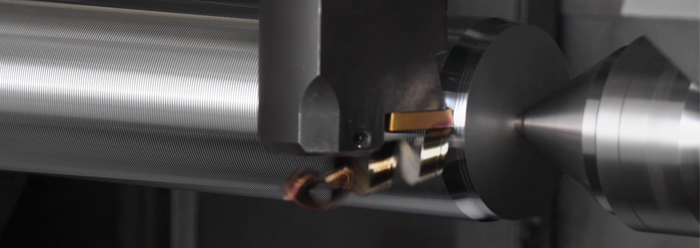
With clever programming of various orientations of the Y-Axis tool, it can be used to complete all the turning operations of a component.
This unique tool, which is very stable even at extended tool lengths, offers you multiple advantages of – high productivity, unmatched chip evacuation and eliminates several tools to complete most of the operations with just one tool.
Tungaloy has designated these innovative tools called AddYAxisTurn.
AddYAxisTurn is the best solution to turn components like shafts with various diameters, undercuts and profiles. Utilizing it for high feed reverse turning and moderate feed forward turning helps in productive machining of such components.
All AddYAxisTurn tools are equipped with TungCap connection for high stability with premium performance.
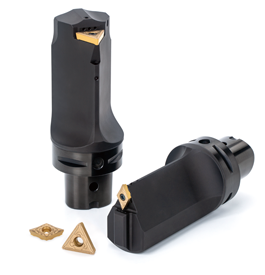
Medium Cutting – 3C-TCMT
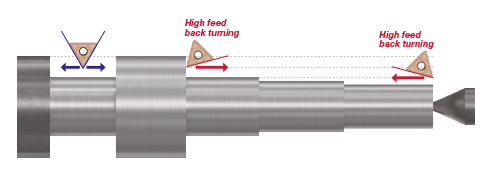
Finishing/Profiling – 2D-DCMT
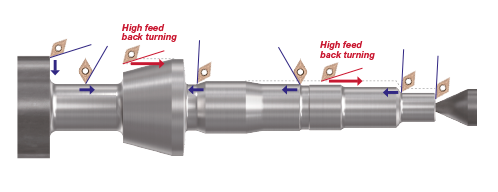
Both inserts are securely placed in their respective pockets to ensure reliable performance in multi-directional turning.
– Y-PRISM’s safe lock design has a rail on the toolholder and matching slot on the insert for tight interlocking and secure clamping.
– Prevents the cutting forces from affecting the insert position in any direction and ensures high stability.
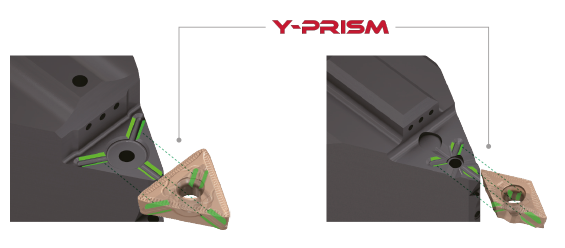
Finally, to ensure predictable tool life on various material, the tool has a high pressure thru coolant nozzle, delivering coolant right at the cutting zone.
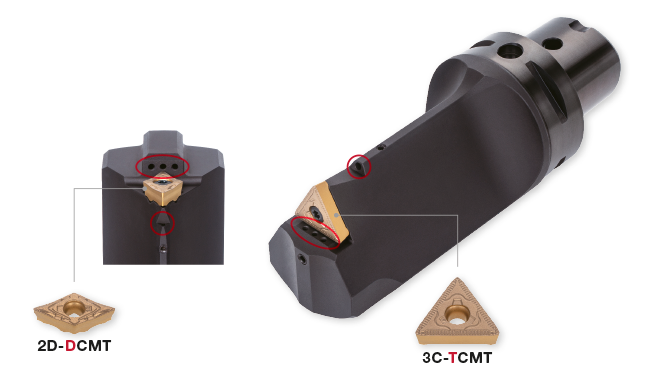
Now you know all about using the Y-Axis tooling solutions on a big multi-tasking machine. How about applying the same principles for compact sliding head machines and smaller turn-mill centers? Yes, Tungaloy has a solution for this too.
- Modular for faster changeover and high machine utilization
- High pressure thru coolant jet for optimal chip formation and tool life
- Economical multi-corner inserts
- Precise inserts and tool shanks
- Unlimited cutting edge geometry and grade combinations for various applications.
ModuMiniTurn featuring Y-Axis tooling solutions are available from Tungaloy.
The benefits remain the same as with AddYAxisTurn tool but with additional flexibility in terms of modular heads. One tool shank can take multiple heads for turning, grooving, parting and profiling. QC12 and QC16 covers two sizes of holding system – 12×12 and 16×16 shanks.
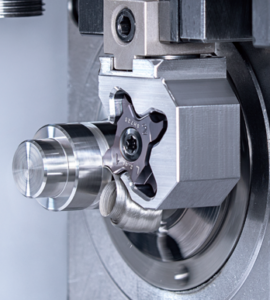
External Turning
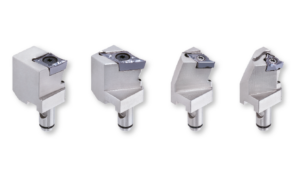
Grooving and Threading
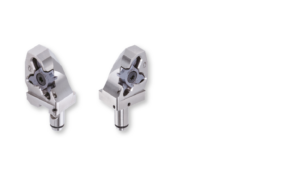
Refer to the user and setting manual in Tungaloy’s catalogue for more information on applications of use of these tools for maximum benefits.
To summarize, Y-Axis tooling solutions for turning is a great option in today’s competitive world for optimizing machine utilization. Investments on these tools have long term benefits to our customers. Contact Tungaloy to discuss switching to the Y-Axis tooling solution. We can provide your return on investment based on the number of tools required for a component and the production volume.