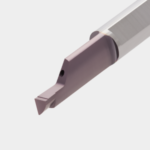
Solid carbide boring bar for small-diameter turning
Extra-fine cutting edge offers high-precision machining for a wide range of internal applications
Applications & Features
Applications
Features
1. Strong cutting edge
Optimized geometry and coating surface.
2. Enhanced lineup for a variety of turning operations of small-diameter holes
Full lineup with 146 items of solid carbide boring bars – Minimum boring diameter : øDm = 0.6 mm
3. High precision collet chuck sleeves
Functional TinyMiniTurn sleeves ensure stability in boring of small-diameter holes.
Solid Carbide Boring Bars & Grades
Solid Carbide Boring Bars
Grades
SH730
- P20 – P35 / M20 – M35 / S05 – S15
- High wear resistance
- Designed for machining steel, stainless steel, and difficult-to-cut material
SH725
- P20 – P30 / M20 – M30
- High wear resistance
- Designed for machining steel and stainless steel
BX310
- H01 – H10
- High wear resistance
- Designed for high-speed continuous cutting of hardened steel
Inserts & Grades
Inserts
Main Grades
SH7025
- P20 – P30 / M20 – M30
- The latest grade with sharp cutting edge designed for small part machining.
- A combination of a columnar-structured TiCN coating and multilayered TiAlN coating provides superior surface quality and process security.
SH725
- P20 – P30 / M20 – M30
- High wear resistance
- Designed for machining steel and stainless steel
SH730
- P20 – P35 / M20 – M35 / S05 – S15
- High wear resistance
- Designed for machining steel, stainless steel, and difficult-to-cut material
GH110
- P10 – P20 / M10 – M20 / K10 – K25 / N05 – N15 / S10 – S20
- High wear resistance
J740
- Ultra-fi ne-grain cemented carbide coated with TiN-based compoundF
GT9530
- High wear resistance
- Excellent surface quality in finishing
NS9530
- High fracture resistance
- Suitable for finishing to medium cutting of steel
TH10
- P10 / M10 / K10 / N10
- Uncoated Cemented Carbide
BX310
- H01 – H10
- High wear resistance
- Designed for high-speed continuous cutting of hardened steel
BX470
- Excellent sharpness
- Suitable for ferrous sintered metal
DX140
- High wear resistance
- Designed for machining non-ferrous metal and nonmetal
Indexable Toolholders
Sleeves
Practical Examples
Standard cutting conditions
Boring, profi ling, chamfering, back boring
ISO | Workpiece materials | Grade | Cutting speed Vc (m/min) | Feed f (mm/rev) |
---|---|---|---|---|
![]() |
Low carbon steels S15C, S25C, etc. C15E, C15E4, etc. |
SH725 | 40 – 140 | 0.01 – 0.08 |
Carbon steels, Alloy steels S55C, SCM440, etc. C55, 42CrMo4, etc. |
SH725 | 40 – 140 | 0.01 – 0.08 | |
Prehardened steels NAK80, PX5, etc. |
SH725 | 40 – 140 | 0.01 – 0.08 | |
![]() |
Stainless steels SUS304, SUS316, etc. X5CrNi18-9, X5CrNiMo17-12-3, etc. |
SH725 | 40 – 140 | 0.01 – 0.08 |
![]() |
Grey cast irons FC250, FCD300, etc. GG25, 250, GG30, 300, etc. |
SH725 | 30 – 100 | 0.01 – 0.08 |
Ductile cast irons FC450, FCD600, etc. GGG60, 600-3, etc. |
SH725 | 30 – 100 | 0.01 – 0.08 | |
![]() |
Aluminium alloys, Copper alloys Si < 12% |
SH725 | 90 – 200 | 0.01 – 0.08 |
![]() |
Titanium alloys Ti-6AI-4V, etc. |
SH725 | 30 – 100 | 0.01 – 0.08 |
Superalloys Inconel718, etc. |
SH725 | 30 – 100 | 0.01 – 0.08 | |
![]() |
Hardened steel | BX310 | 15 – 100 | 0.01 – 0.1 * |
* Set the D.O.C. and feed according to the tool’s corner radius (RE).
Threading (metric thread)
ISO | Workpiece materials | Grade | Cutting speed Vc (m/min) |
Number of passes Pitch (mm) |
||||
---|---|---|---|---|---|---|---|---|
0.5 | 0.75 | 1 | 1.25 | 1.5 | ||||
![]() |
Low carbon steels S15C, S25C, etc. C15E, C15E4, etc. |
SH725 | 40 – 140 | 6 – 8 | 8 – 10 | 10 – 12 | 12 – 15 | 15 – 18 |
Carbon steels, Alloy steels S55C, SCM440, etc. C55, 42CrMo4, etc. |
SH725 | 40 – 140 | 6 – 8 | 8 – 10 | 10 – 12 | 12 – 15 | 15 – 18 | |
Prehardened steels NAK80, PX5, etc. |
SH725 | 40 – 140 | 6 – 8 | 8 – 10 | 10 – 12 | 12 – 15 | 15 – 18 | |
![]() |
Stainless steels SUS304, SUS316, etc. X5CrNi18-9, X5CrNiMo17-12-3, etc. |
SH725 | 40 – 140 | 8 | 10 | 12 | 15 | 18 |
![]() |
Grey cast irons FC250, FCD300, etc. GG25, 250, GG30, 300, etc. |
SH725 | 30 – 100 | 7 | 9 | 12 | 14 | 17 |
Ductile cast irons FC450, FCD600, etc. GGG60, 600-3, etc. |
SH725 | 30 – 100 | 7 | 9 | 12 | 14 | 17 | |
![]() |
Aluminium alloys, Copper alloys Si < 12% |
SH725 | 90 – 200 | 6 | 8 | 10 | 12 | 15 |
Internal grooving
ISO | Workpiece materials | Grade | Cutting speed Vc (m/min) |
Feed f (mm/rev) |
---|---|---|---|---|
![]() |
Low carbon steels S15C, S25C, etc. C15E, C15E4, etc. |
SH725 | 40 – 140 | 0.01 – 0.03 |
Carbon steels, Alloy steels S55C, SCM440, etc. C55, 42CrMo4, etc. |
SH725 | 40 – 140 | 0.01 – 0.03 | |
Prehardened steels NAK80, PX5, etc. |
SH725 | 40 – 140 | 0.01 – 0.03 | |
![]() |
Stainless steels SUS304, SUS316, etc. X5CrNi18-9, X5CrNiMo17-12-3, etc. |
SH725 | 40 – 140 | 0.01 – 0.03 |
![]() |
Grey cast irons FC250, FCD300, etc. GG25, 250, GG30, 300, etc. |
SH725 | 30 – 100 | 0.01 – 0.03 |
Ductile cast irons FC450, FCD600, etc. GGG60, 600-3, etc. |
SH725 | 30 – 100 | 0.01 – 0.03 | |
![]() |
Aluminium alloys, Copper alloys Si < 12% |
SH725 | 90 – 200 | 0.01 – 0.03 |
![]() |
Titanium alloys Ti-6AI-4V, etc. |
SH725 | 30 – 100 | 0.01 – 0.03 |
Superalloys Inconel718, etc. |
SH725 | 30 – 100 | 0.01 – 0.03 |
Face grooving
ISO | Workpiece materials | Grade | Cutting speed Vc (m/min) |
Feed f (mm/rev) |
---|---|---|---|---|
![]() |
Low carbon steels S15C, S25C, etc. C15E, C15E4, etc. |
SH725 | 40 – 140 | 0.01 – 0.05 |
Carbon steels, Alloy steels S55C, SCM440, etc. C55, 42CrMo4, etc. |
SH725 | 40 – 140 | 0.01 – 0.05 | |
Prehardened steels NAK80, PX5, etc. |
SH725 | 40 – 140 | 0.01 – 0.05 | |
![]() |
Stainless steels SUS304, SUS316, etc. X5CrNi18-9, X5CrNiMo17-12-3, etc. |
SH725 | 40 – 140 | 0.01 – 0.05 |
![]() |
Grey cast irons FC250, FCD300, etc. GG25, 250, GG30, 300, etc. |
SH725 | 30 – 100 | 0.01 – 0.05 |
Ductile cast irons FC450, FCD600, etc. GGG60, 600-3, etc. |
SH725 | 30 – 100 | 0.01 – 0.05 | |
![]() |
Aluminium alloys, Copper alloys Si < 12% |
SH725 | 90 – 200 | 0.01 – 0.05 |
![]() |
Titanium alloys Ti-6AI-4V, etc. |
SH725 | 30 – 100 | 0.01 – 0.05 |
Superalloys Inconel718, etc. |
SH725 | 30 – 100 | 0.01 – 0.05 |
For new indexable boring bar (EPG*04 / EPG*03 insert)
ISO | Workpiece material | Grade | Cutting speed Vc (m/min) |
---|---|---|---|
![]() |
Low carbon steels S15C, S25C, etc. C15E, C15E4, etc. Carbon steels S45C, S55C, etc. C45, C55, etc. Alloy steels SCM440, SCr420, etc. 42CrMo4, 20Cr4, etc. |
SH7025 | 10 – 200 |
SH725 | 10 – 200 | ||
SH730 | 10 – 150 | ||
J740 | 10 – 100 | ||
NS9530 | 150 – 300 | ||
GT9530 | 150 – 300 | ||
![]() |
Stainless steels SUS304, SUS316, etc. X5CrNi18-9, X5CrNiMo17-12-3, etc. |
SH7025 | 10 – 200 |
SH725 | 10 – 200 | ||
SH730 | 30 – 150 | ||
![]() |
Grey cast iron FC250, GG25, 250, etc. |
TH10 | 30 – 100 |
![]() |
Aluminium alloys Si < 12% |
TH10 | > 100 |
DX140 | > 500 | ||
Aluminium alloys Si > 12% |
TH10 | > 100 | |
DX140 | > 400 | ||
Copper alloys | TH10 | > 100 | |
DX140 | > 500 | ||
![]() |
Hardened materials | BX310 | 30 – 150 |
Powder metal | Sintered powder metals | BX470 | 100 – 300 |
For more information about this product, visit our online e-catalog or download the product report: