Sustainable Precision: Balancing Tool Life and Environmental Impact in Modern Machining
As sustainability becomes a key focus in modern manufacturing, industry leaders are tasked with finding ways to reduce environmental impact without compromising on quality or efficiency. In this evolving landscape, Tungaloy stands out for its innovative approach to precision tooling, developing sustainable designs that extend tool life, reduce waste, and lower emissions. By emphasizing innovations like tool miniaturization and head-exchangeable systems, Tungaloy is helping manufacturers achieve their sustainability goals while delivering the precision and durability they need for complex machining.
The Challenge: Balancing Tool Life and Environmental Responsibility in Precision Machining
Precision machining requires high-quality tooling that can withstand demanding conditions and produce consistent results. Traditionally, the focus has been on durability and precision, but with increased pressure to reduce waste and emissions, companies are looking for tools that balance these needs with environmental considerations. Tool life directly impacts the waste generated in production: the longer a tool lasts, the fewer replacements needed, leading to reduced disposal and resource use. At the same time, certain sustainable practices, like minimizing tool size, can sometimes challenge tool life if not expertly engineered.
This is where Tungaloy’s expertise shines. By leveraging advanced tool miniaturization and head-exchangeable designs, Tungaloy helps customers maintain productivity while reducing waste and conserving resources. This approach not only supports sustainable manufacturing but also provides practical benefits in cost and efficiency, especially for industries requiring high-precision solutions, such as aerospace and automotive.
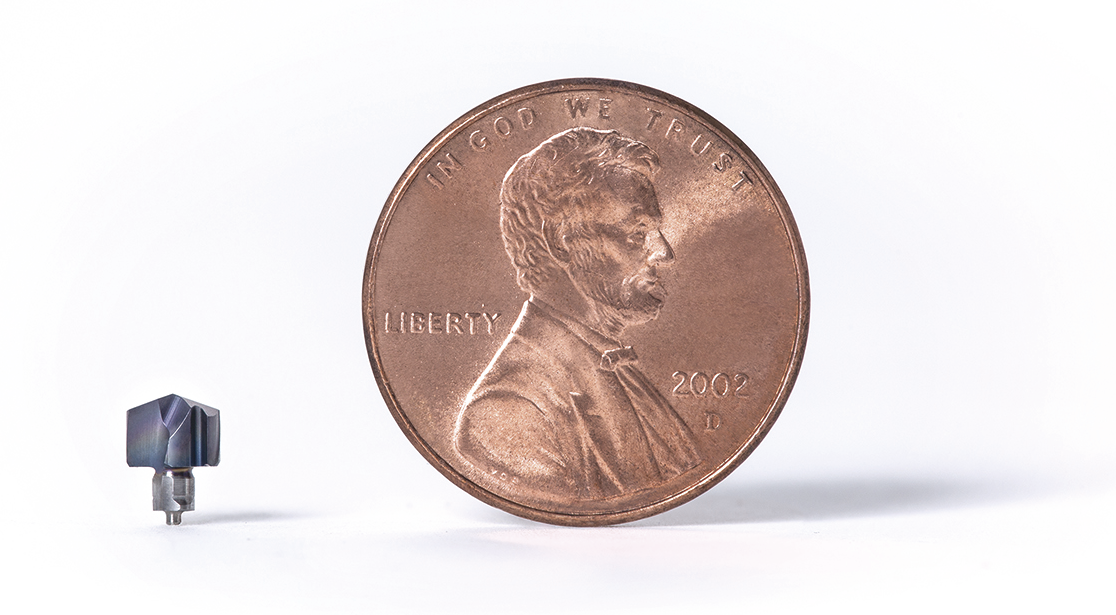
Miniaturization of Cutting Tools for Sustainable Machining
Tool miniaturization is a major part of Tungaloy’s green strategy. By designing smaller tools, Tungaloy reduces the amount of raw material used per tool, directly decreasing waste at the end of its life. For instance, Tungaloy’s VNMG1204 inserts (from the ISO-EcoTurn series) weigh around 47% less than standard ISO inserts, significantly reducing the material that needs to be discarded. Other solutions, such as the AddMeisterDrill and AddDoFeed, also align with this approach, offering sustainable designs that conserve resources and lower the carbon footprint associated with manufacturing, shipping, and disposal.
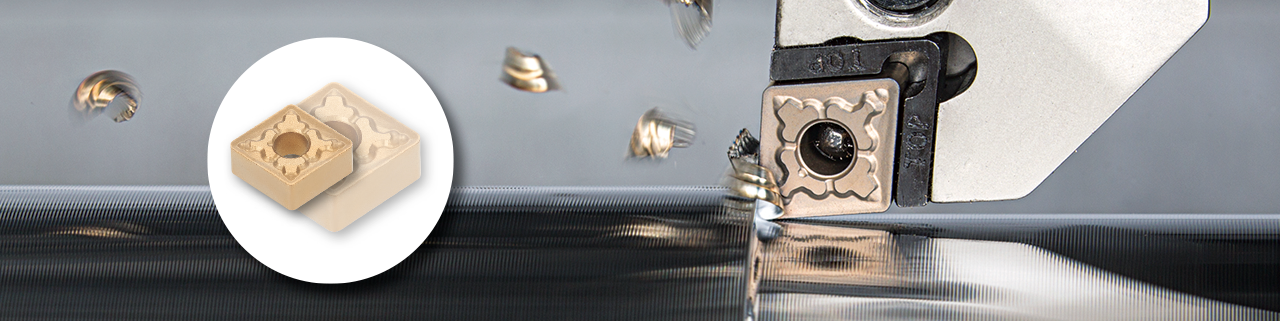
Beyond waste reduction, miniaturized tools offer operational efficiencies. Smaller inserts allow for increased production volume per batch, which reduces the overall emissions per unit of production. Additionally, miniaturized tools like the VNMG1204 require less energy during machining operations, aligning with energy efficiency goals in high-volume production. For manufacturers, this translates to a two-fold benefit: reduced disposal costs and enhanced machining efficiency, an ideal combination for companies prioritizing lean and sustainable manufacturing.
The Role of Head-Exchangeable Systems in Waste Reduction
A highlight of Tungaloy’s sustainable tooling lineup is the head-exchangeable system. Tools like DrillMeister and TungMeister feature replaceable heads, allowing manufacturers to replace only the worn cutting portion of the tool rather than discarding the entire unit. This innovation drastically reduces material waste, particularly in high-usage environments where tool turnover is high. For example, Tungaloy’s head-exchangeable reamers weigh just 16g compared to 207.19g for a conventional solid reamer—a reduction of over 92% in waste.
The benefits of head-exchangeable tools extend beyond waste reduction. These tools also contribute to reduced downtime, as changing the head is faster and requires less setup time than replacing an entire tool. In high-precision manufacturing, where machine uptime is essential, head-exchangeable systems save both time and money, making them a cost-effective and sustainable solution. Customers adopting these tools report decreased operational costs and enhanced productivity, demonstrating that sustainable tooling can deliver competitive advantages. For more insights, read about how to reduce setup time and optimize tool overhang for Swiss-type automatic lathes with head-exchangeable tools, click here.
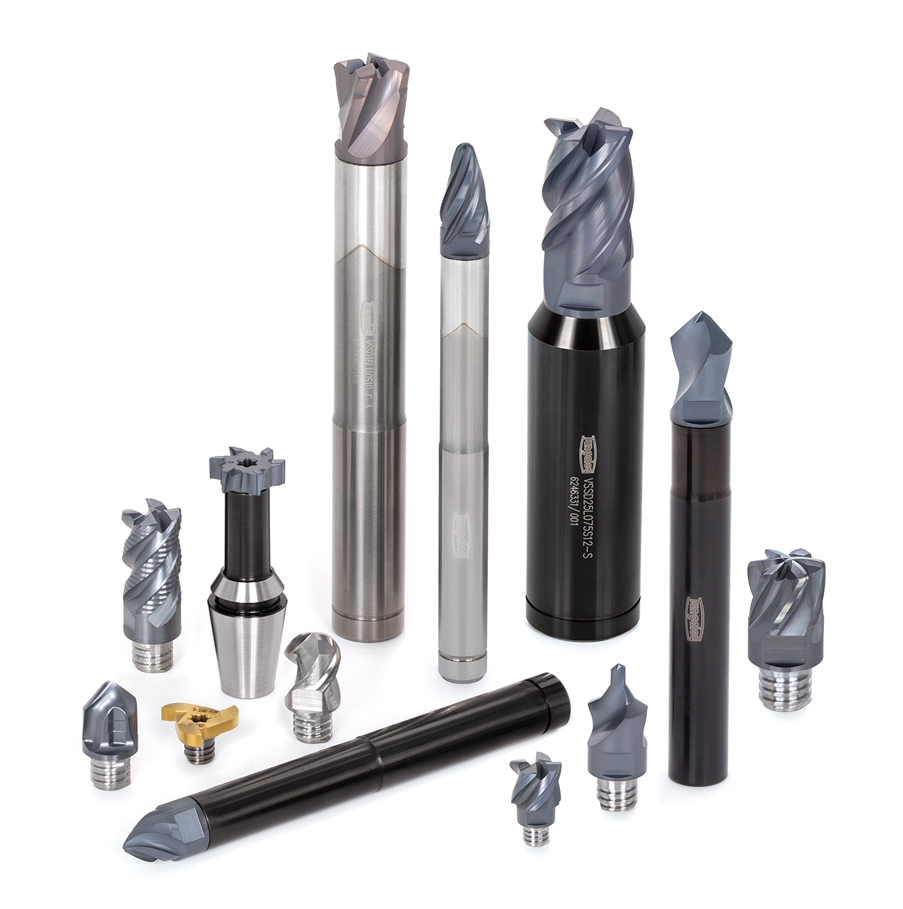
Additive Manufacturing for Sustainable Tool Design
Tungaloy also embraces Additive Manufacturing (AM) to further enhance sustainability. AM enables the creation of lightweight, optimized tool designs that consume less material during production while maintaining superior performance. In addition to reducing resource use, AM allows for innovative geometries that improve tool life and machining efficiency. This cutting-edge approach not only supports eco-friendly manufacturing but is also implemented in Tungaloy’s own production processes, reinforcing its commitment to sustainability and technological advancement. To read more how Tungaloy used Additive Manufacturing for its own production and what solutions Tungaloy brings for machining 3D printed components click here
Case Study: Sustainable Precision in Automotive Manufacturing
In one recent case, a high-volume automotive manufacturer turned to Tungaloy’s head-exchangeable drills and miniaturized inserts to reduce waste and meet strict sustainability targets. By implementing DrillMeister drills and ISO-EcoTurn, VNMG1204 inserts, the manufacturer achieved a 40% reduction in tool waste and lowered their CO₂ emissions by an estimated 25% over the course of a year. Furthermore, with the reduced downtime associated with head-exchangeable tools, the manufacturer saw an increase in machine uptime and output. This case demonstrates the tangible impact of sustainable tooling on productivity and environmental responsibility. By focusing on miniaturization and head-exchangeable designs, Tungaloy enabled the customer to achieve a balanced solution that supported both performance and sustainability—reinforcing the idea that eco-conscious practices can go hand-in-hand with operational excellence.
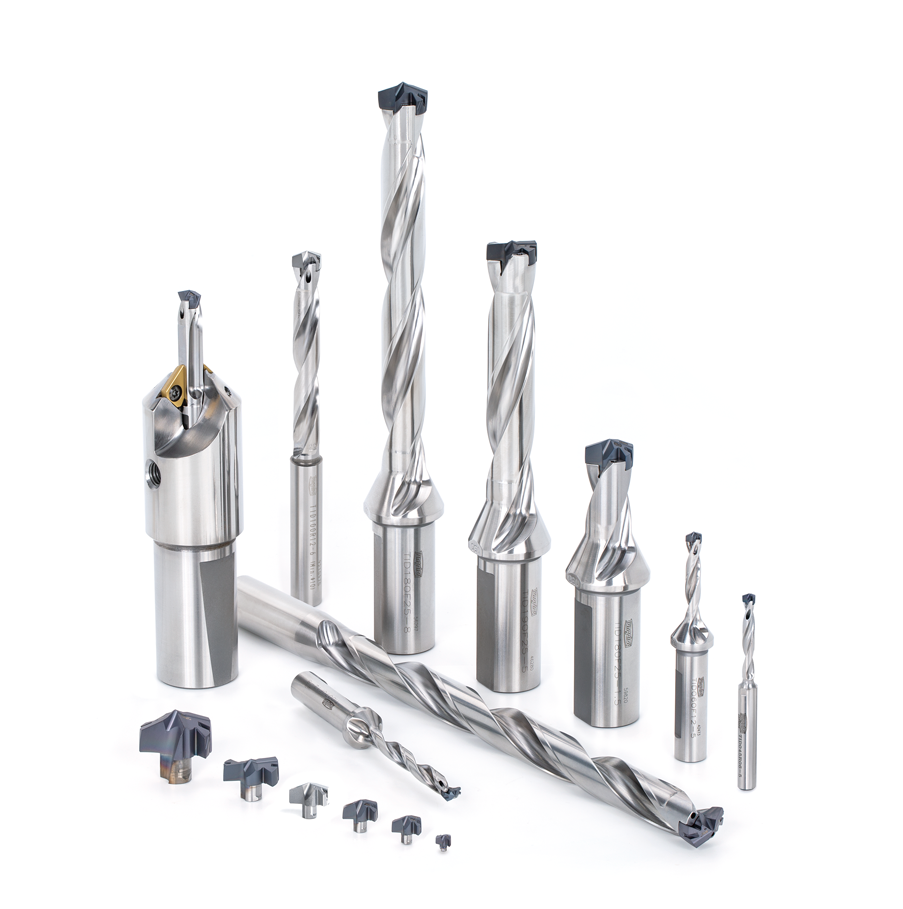
Sustainable Machining: A Competitive Edge in Precision Manufacturing
Tungaloy’s approach to sustainable tooling aligns with broader trends in the manufacturing industry, where companies are prioritizing carbon reduction and waste minimization in response to regulatory pressures and customer expectations. As environmental standards continue to rise, companies that adopt sustainable practices stand to gain a competitive edge, not only by meeting these standards but also by building a reputation as environmentally responsible manufacturers. With tools like the DrillMeister, TungMeister, and ISO-EcoTurn series, Tungaloy is at the forefront of this shift, providing solutions that meet stringent performance criteria while supporting sustainability goals. These tools are engineered to help manufacturers reduce waste, extend tool life, and lower their carbon footprint, addressing the twin priorities of precision and environmental responsibility.
Conclusion: Building a Greener Future with Tungaloy’s Sustainable Tooling Solutions
Tungaloy’s sustainable tooling innovations—rooted in miniaturization, head-exchangeable systems, and precision engineering—offer manufacturers a pathway to greener operations without sacrificing quality or efficiency. By focusing on waste reduction, resource conservation, and improved productivity, Tungaloy’s products empower companies to make a meaningful impact on their sustainability goals. Each tool selection is a step toward a more eco-friendly manufacturing process, making Tungaloy an ideal partner for businesses committed to sustainability. In a world where environmental responsibility is increasingly vital, Tungaloy’s approach demonstrates that precision and sustainability are not mutually exclusive but can coexist to benefit both businesses and the planet. Whether through tool miniaturization or head-exchangeable designs, Tungaloy invites manufacturers to embrace a greener future, one tool at a time.