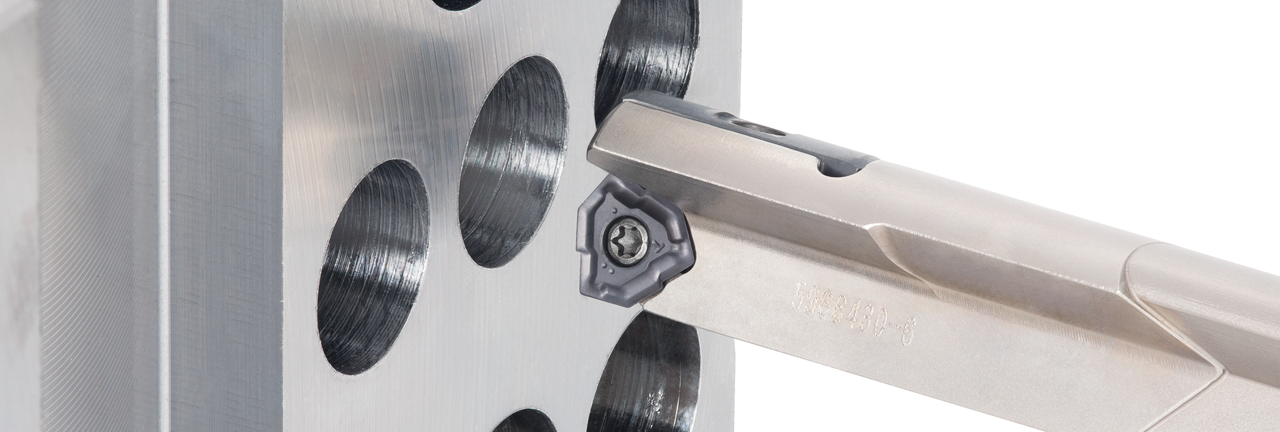
Achieving High-Quality Surface Finishes in Marine Engine Parts with Indexable Gun Drills and Head Exchange Drills for Cross Hole Machining
This article is a web-edited version of the one published in Machinery Technology May 2024 issue.
In the wake of the automotive industry’s shift towards electrification, the maritime sector is also setting sail towards decarbonization. Miyahara Manufacturing Co., Ltd., based in Tamano City, Okayama Prefecture, specializes in machining and assembling marine diesel engine parts. With an eye on reducing greenhouse gas emissions, they’ve partnered with Tungaloy, a leading tool manufacturer, from the outset of their mass production endeavors.
President
Hiroaki Miyahara Mr.
Manufacturing Department Deputy Manager
Shota Yamamoto Mr.
Machining Section Chief
Masayuki Shimada Mr.
Through this collaboration, Miyahara implemented Tungaloy’s indexable gun drill “DeepTri-Drill” and head exchange drill “DrillMeister”. These tools, along with expert guidance, enabled Miyahara to establish a machining method ensuring high surface quality and stable operations. Together, they’re steering the maritime industry towards a greener horizon, one cross hole at a time.
Marine Engine Focus
The company aims to lead in the marine engine sector, having shifted focus solely to this industry from machining parts for printing and machine tools. They serve core clients and seek opportunities with domestic and international marine engine manufacturers.
Their strength lies in a comprehensive system handling operations from machining to assembly. With in-house machining and diverse equipment across two factories, including approximately 40 NC machines, they produce components ranging from palm-sized to large parts. Additionally, they offer unique services like in-house hardening and chrome powder spraying for enhanced part durability.
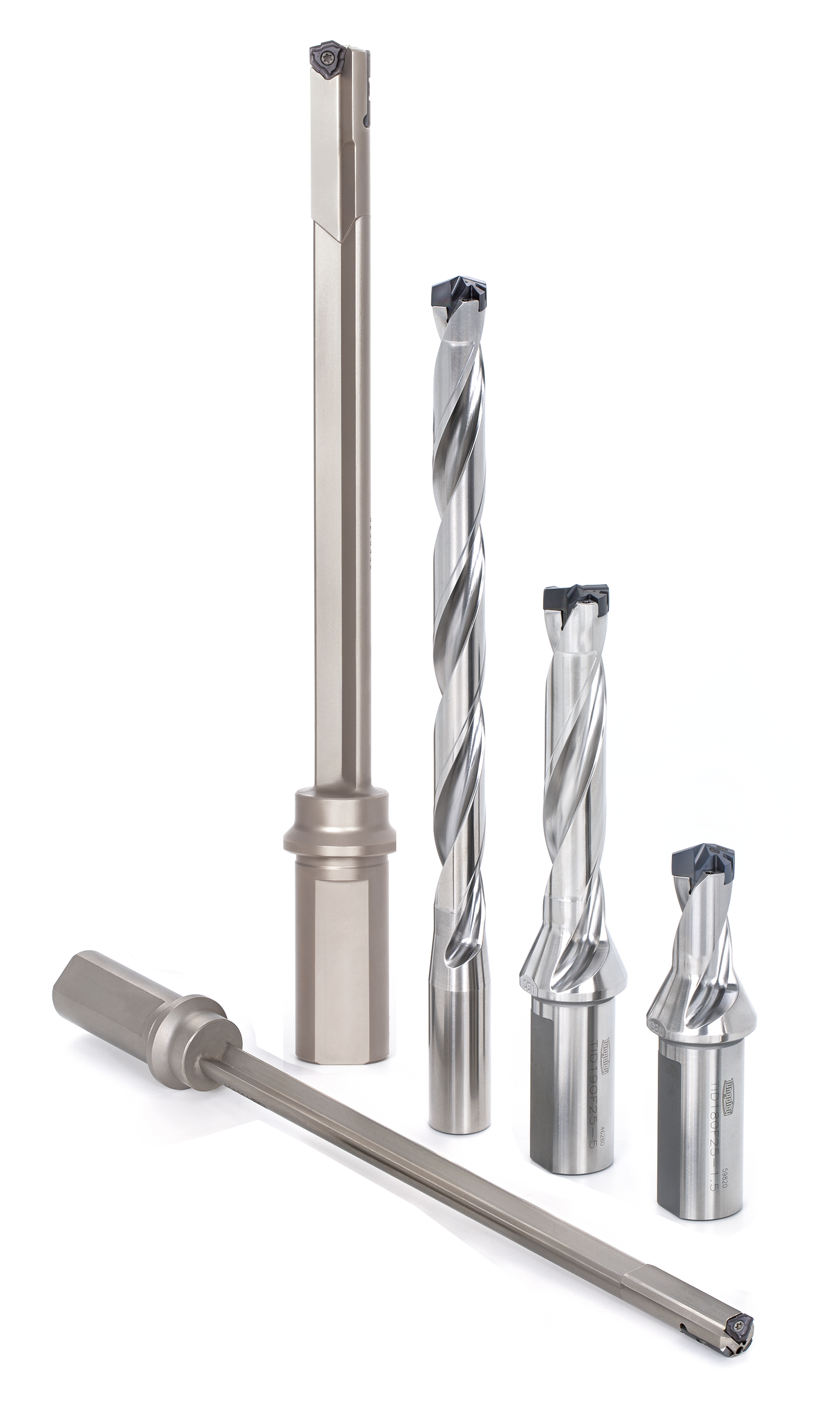
Collaboration with Tool Manufacturer
In response to the anticipated rise in demand for dual-fuel engines, the company refocused its efforts over the past 1-2 years towards manufacturing parts for this innovative technology. Dual-fuel engines utilize both conventional heavy oil and alternative fuels like natural gas, offering a significant reduction in greenhouse gas emissions. Mass production of these parts commenced in 2023 at the behest of a major client, marking a pivotal moment for the company. However, they encountered formidable challenges right from the outset.
The material at hand is S45C, and the block’s dimensions measure 400×300×200 mm, featuring an intricate network of holes ranging from ø4 to 80 mm in diameter. These holes, including the thickest ones intersected by oblique holes from multiple directions, presented a machining challenge of unprecedented complexity. With the need for precision machining of numerous cross holes and off-center holes, the company sought external expertise to ensure seamless mass production.
Recognizing the need for specialized drilling capabilities, the company turned to Tungaloy, renowned for its expertise in deep hole drilling.
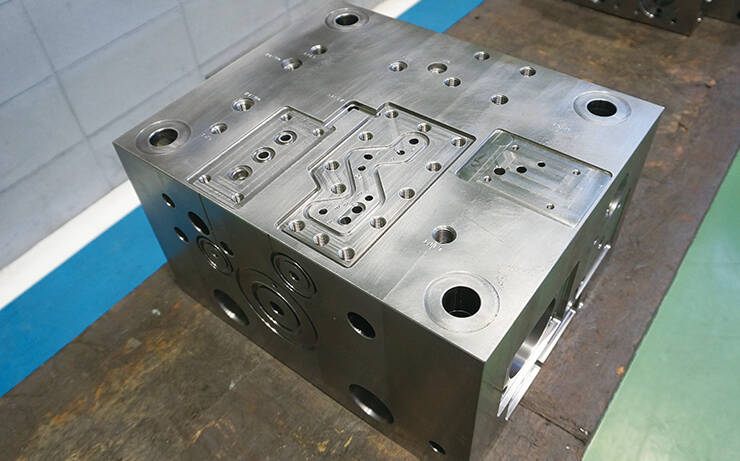
Dual-fuel marine diesel engine parts
Advanced Hole Machining Tools
Under the guidance of Tungaloy, Miyahara Manufacturing underwent a significant transformation in their approach to hole machining tools. Traditionally, they relied on HSS drills for deep hole machining due to their toughness and resistance to breakage, essential for stable operations. However, the slow machining speeds of HSS drills posed challenges in achieving smooth finishes, with surface roughness levels reaching Ra=3.2μm, and finer finishes of Ra=0.8μm or Ra=0.6μm proving elusive. To address this, they turned to carbide tools capable of balancing machining speed and surface quality.
After rigorous prototyping using a newly introduced 5-axis machining center, Miyahara Manufacturing established a stable machining method. They adopted two key tools: the indexable gun drill “DeepTri-Drill” and the head exchange drill “DrillMeister.” The DeepTri-Drill excels in chip removal efficiency, machining rate, and precision, while the DrillMeister combines the cutting performance of a solid carbide drill with the convenience of one-touch head exchange. DeepTri-Drill handled deep hole and cross hole machining, while DrillMeister tackled other hole machining tasks, effectively addressing surface roughness issues and ensuring stable operations.
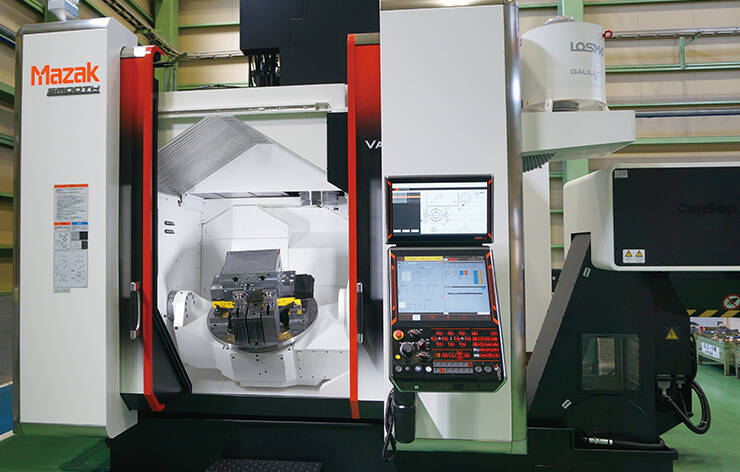
Utilizing specialized jigs to harness the capabilities of the 5-axis MC
Looking ahead, Miyahara Manufacturing plans to further optimize their processes. They aim to reduce setup times by utilizing specialized jigs and leveraging the capabilities of the 5-axis machining center to process multiple faces simultaneously. Additionally, they are exploring lateral expansion into other parts, recognizing the benefits of exchangeable tools in minimizing human errors and optimizing tool replacement timing through quantitative assessment of wear conditions.
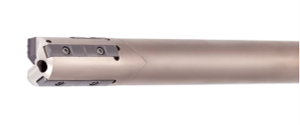
DeepTri-Drill for cross-hole machining with two guide pads connected
Cross-Hole Machining with DeepTri-Drill
Example of Machining Program for Cross-Hole Machining
Video provided by: DMG MORI Precision Boring CO.,LTD.
Encouraging Free Innovation
The success of this endeavor can be attributed to the early involvement of Tungaloy during the initial stages of mass production. Deputy Manager Yamamoto praised the invaluable advice and expertise provided by Tungaloy’s team through their sales representative. He expressed satisfaction with specialized products like the DeepTri-Drill, which enhanced guide pads for cross hole drilling.
In February 2024, as Miyahara Manufacturing celebrated its 100th anniversary under the banner “KEEP THE TOMORROW SHIP,” President Miyahara reaffirmed the company’s dedication to focusing on marine engines while embracing new challenges. Emphasizing a culture of open innovation, President Miyahara encourages all employees to freely explore their interests and pursue innovative ideas.
Miyahara Manufacturing has not only established machining techniques crucial for the decarbonization of the maritime industry but also aims to further invest in equipment to expand their newly acquired technologies. Additionally, they are keen on attracting new customers as they continue their journey towards shaping the future of marine engineering.
Curious about Tungaloy’s Hole Making lineup? Click here to learn more!
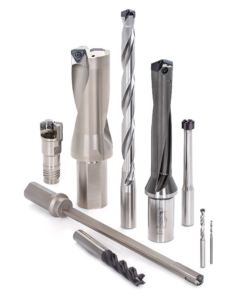