Iwaki, Japan – November, 2024 – Tungaloy Corporation (President: Satoshi Kinoshita, Head Office: Iwaki City, Fukushima Prefecture) announces the expansion of its TungSpeed-Mill series, introducing small-diameter, extra close pitch cutters. The new lineup includes ø40 (z=8), ø50 (z=10), and ø63 (z=14) bore-type cutters with industry-leading tooth counts for enhanced productivity. Additionally, the lightweight ø100,125 steel body, featuring a unique design for strength and rigidity, enables compatibility with smaller machines like BT30, offering versatile and efficient machining solutions.
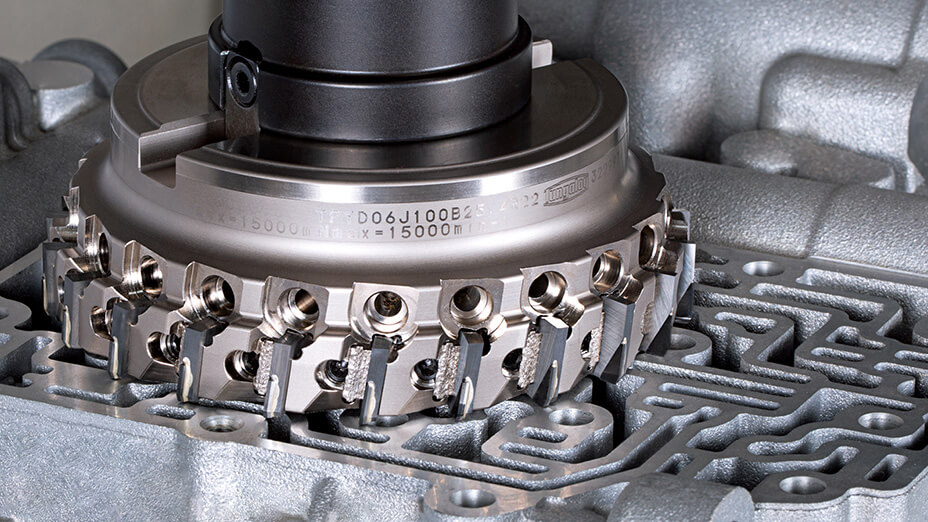
Challenges and Trends
In recent years, the automotive and general industrial machinery sectors have increasingly demanded higher machining speeds and precision. This is particularly important in the machining of valve bodies, aluminum alloy cases, and pneumatic equipment cases, where efficiency has become a key focus. However, conventional small-diameter cutters face the challenge of having fewer cutting edges, making it difficult to achieve high-efficiency machining. Additionally, when using BT30 machines, weight limitations on tools often prevent the use of large-diameter cutters, posing an additional challenge. Furthermore, lightweight cutters with aluminum bodies often lack the rigidity and strength of steel-bodied cutters. To address these challenges, there is growing demand for a cutter that combines greater efficiency, lightweight construction, and the necessary strength.
Product Overview
TungSpeed-Mill is a high-efficiency tool ideal for machining aluminum alloy components such as aircraft and automotive parts, as well as electronic enclosures. Available in diameters ranging from 40mm to 160mm, it features up to 34 cutting edges and enables cutting speeds exceeding 3,000 m/min for aluminum alloys and non-ferrous alloys.
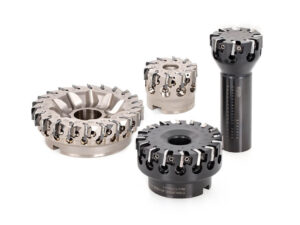
Benefits and Features
Feature 1: Industry-leading extra close pitch design for small-diameter cutters
- The extra close pitch design with ø40 (z=8), ø50 (z=10), and ø63 (z=14) significantly enhances machining efficiency.
- By utilizing an extra-close pitch cutter, machining time is reduced, leading to increased productivity.
- The large number of inserts distributes cutting resistance, enabling more stable machining.
Feature 2: Lightweight steel body
- The unique lightweight design maintains strength and rigidity while reducing weight compared to conventional cutters.
- The lightweight body allows for smooth operation even on smaller machines such as BT30, making it compatible with a wide range of equipment.
- A tooling weight (including arbor) of 3 kg or less was achieved, staying within the ATC limit for BT30 compact machines.
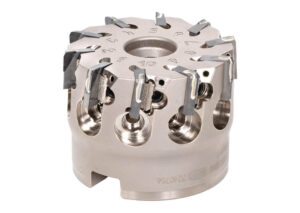
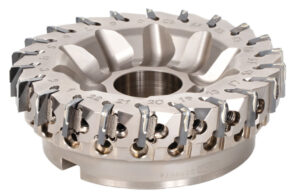
Success Stories
IMPROVED PRODUCTIVITY
TungSpeed-Mill achieved 1.5 times higher efficiency in roughing and 2.0 times higher efficiency in finishing through its multi-tooth design.
The competitor’s product started generating burrs at approximately 3,500 pieces, requiring manual deburring until reaching its set tool life of 27,400 pieces.
TungSpeed-Mill, even after processing 20,000 pieces, did not produce burrs, eliminating the need for manual deburring, an outcome that was well received.
Industry | Automotive |
---|---|
Component | Timing chain case |
Material ISO code | |
Work material | ADC12 |
Machine(spindle type) | Vertical Machining Center Small(#30,HSK40) |
Tool family | Milling |
Tool category | Face milling |
Product name | TungSpeed-Mill (TPYD, EPYD) |
TSR No. | 5066M |
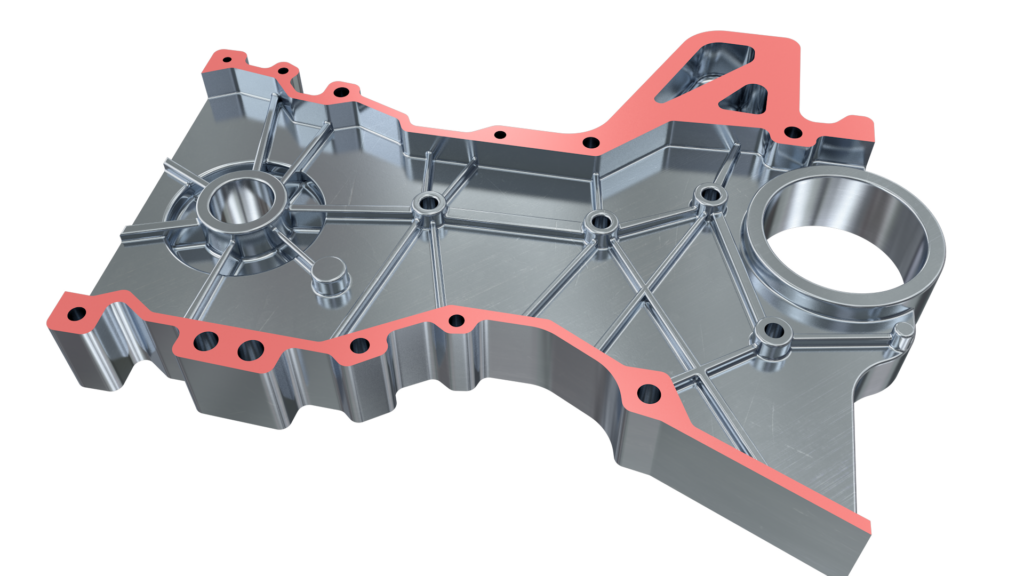