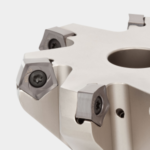
High-speed face milling with superior surface finish
Economical face milling cutter with high productivity for all materials
Applications & Features
Applications
Features
1. Economical pentagonal insert
• Double-sided insert with 10 cutting edges.
2. Low cutting force
3. Wide line-up of inserts for various machining
Inserts & Grades
Inserts
PN*U0905
- Maximum depth of cut = 6.4 mm (except -W)
- 10 corner inserts for face milling
- PNCU0905-W is wide wiper insert (2 corners)
Main Grades
AH3135
- High fracture resistance
- Suitable for machining steel and stainless steel under general cutting conditions
AH3225
- Good balance between wear and fracture resistance
- Suitable for steel and stainless steel
AH8015
- Good balance between wear and fracture resistance
- First choice for machining heat-resistant alloy under general cutting conditions
Cutter bodies
Practical examples
Example #1
General Engineering
Part: | Pump housing |
Material: | SKD11 |
Cutter: | TEN09R125M38.1-06 (ø125 mm, z = 6) |
Insert: | PNCU0905GNEN-ML |
Grade: | AH3135 |
Cutting conditions: | Vc = 120 (m/min) fz = 0.25 (mm/t) Vf = 458 (mm/min) ap = 3 (mm) ae = 60 (mm) Application: Face milling Coolant: Dry Machine: Horizontal M/C |
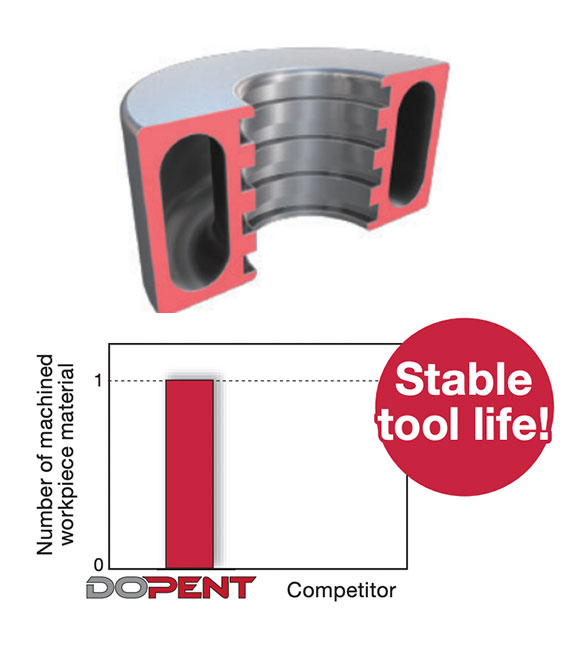
Example #2
General Engineering
Part: | Rolling die material |
Material: | Tool steel |
Cutter: | TEN09R160M50.8-12 (ø160 mm, z = 12) |
Insert: | PNMU0905GNEN-MJ |
Grade: | AH3225 |
Cutting conditions: | Vc = 300 (m/min) fz = 0.1 (mm/t) Vf = 716 (mm/min) ap = 0.8 (mm) ae = 50 (mm) Application: Face milling Coolant: Dry Machine: Horizontal M/C |
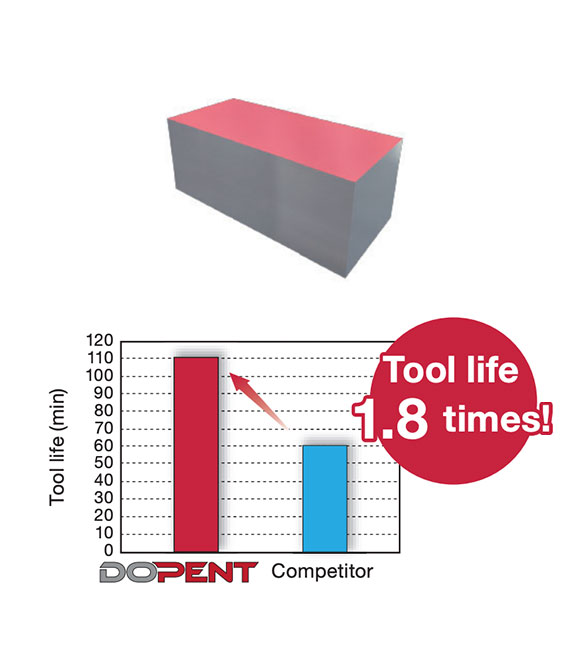
Example #3
General Engineering
Part: | EGR valve |
Material: | FC250 / 250 |
Cutter: | TEN09R125M38.1-06 (ø125 mm, z = 6) |
Insert: | PNCU0905GNEN-MJ |
Grade: | AH120 |
Cutting conditions: | Vc = 390 (m/min) fz = 0.15 (mm/t) Vf = 900 (mm/min) ap = 0.9 (mm) ae = 75 (mm) Application: Face milling Coolant: External supply Machine: Vertical M/C、6kW |
Process: | , |
Machine: |
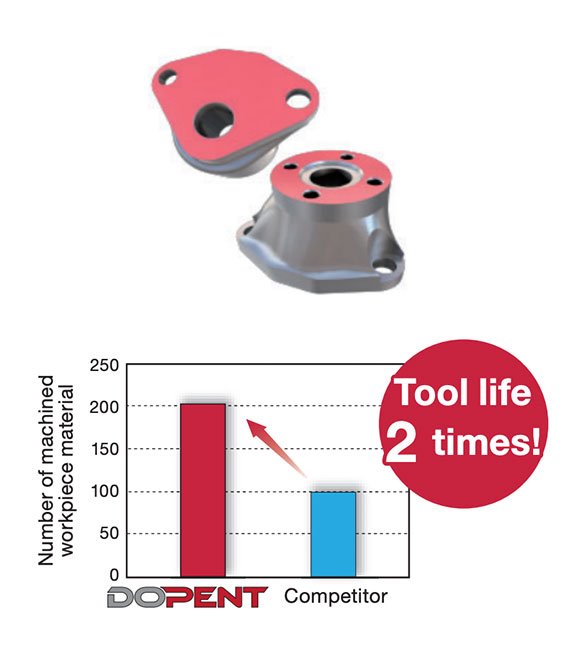
Standard cutting conditions
ISO | Workpiece materials | Hardness HB |
Selection criteria |
Recommended grade |
Chip- breaker |
Cutting speed Vc (m/min) |
Feed per tooth fz (mm/t) |
---|---|---|---|---|---|---|---|
![]() |
Low carbon steels S15C, C15E4, etc.S15C, C15E4, etc. C15, etc. |
200 – 300 HB | First choice | AH3225 | MJ | 100 – 250 | 0.1 – 0.4 |
200 – 300 HB | Low cutting force | AH3225 | ML | 100 – 250 | 0.1- 0.3 | ||
200 – 300 HB | Wear resistance | T3225 | MJ | 200 – 350 | 0.1- 0.3 | ||
200 – 300 HB | Surface quality | NS740 | MJ | 100 – 250 | 0.1- 0.3 | ||
High carbon steels, alloyed steels S45C, SCM440, etc.S45C, SCM440, etc. C45, 42CrMo4, etc. |
150 – 300 HB | First choice | AH3225 | MJ | 100 – 250 | 0.1- 0.35 | |
150 – 300 HB | Low cutting force | AH3225 | ML | 100 – 250 | 0.1- 0.3 | ||
150 – 300 HB | Wear resistance | T3225 | MJ | 180 – 300 | 0.1- 0.3 | ||
150 – 300 HB | Surface quality | NS740 | MJ | 100 – 250 | 0.1- 0.3 | ||
Prehardened steels NAK80, PX5, etc. |
30 – 40 HRC | First choice | AH3225 | MJ | 100 – 200 | 0.1- 0.3 | |
30 – 40 HRC | Low cutting force | AH3225 | ML | 100 – 200 | 0.1- 0.25 | ||
30 – 40 HRC | Wear resistance | T3225 | MJ | 150 – 250 | 0.1- 0.25 | ||
![]() |
Stainless steels SUS304, etc.SUS304, etc. X5CrNi18-9, etc. |
– 200 HB | First choice | AH3135 | ML | 100 – 200 | 0.1 – 0.3 |
– 200 HB | Fracture resistance | AH3135 | MJ | 100 – 200 | 0.1 – 0.35 | ||
– 200 HB | Wear resistance | T3225 | MJ | 100 – 250 | 0.1 – 0.3 | ||
![]() |
Grey cast irons FCD400, etc.FCD400, etc. 250, etc. |
150 – 250 HB | First choice | T1215 | MJ | 100 – 300 | 0.1 – 0.35 |
150 – 250 HB | Fracture resistance | AH120 | MJ | 100 – 250 | 0.1 – 0.4 | ||
Ductile cast irons FCD400, etc.FCD400, etc. 400-15S, etc. |
150 – 250 HB | First choice | T1215 | MJ | 100 – 300 | 0.1 – 0.35 | |
150 – 250 HB | Fracture resistance | AH120 | MJ | 80 – 200 | 0.1 – 0.4 | ||
![]() |
Aluminium alloys Si < 13% |
– | First choice | KS05F | AJ | 500 – 1500 | 0.1 – 0.5 |
Aluminium alloys Si ≥ 13% |
– | First choice | KS05F | AJ | 150 – 500 | 0.1 – 0.5 | |
![]() |
Titanium alloys Ti-6Al-4V, etc. |
– 40 HRC | First choice | AH3135 | ML | 30 – 60 | 0.1 – 0.3 |
– 40 HRC | Fracture resistance | AH3135 | MJ | 30 – 60 | 0.1 – 0.3 | ||
Heat-resistant alloys Inconel 718, etc. |
– 40 HRC | First choice | AH725 | MJ | 10 – 40 | 0.04 – 0.1 | |
![]() |
Hardened materials SKD61, X40CrMoV5-1, etc. |
– 45 HRC | First choice | AH8015 | MJ | 80 – 150 | 0.05 – 0.15 |
– 45 HRC | Low cutting force | AH8015 | ML | 80 – 150 | 0.05 – 0.15 |
- Remove excessive chips with an air blast to prevent chip jamming.
- Use water-soluble coolant to avoid built-up edge in case extreme welding occurs on cutting edges. (ex. aluminium machining).
- For operations with a varied depth of cut (ex. casting skin) and machining of workpiece materials with interrupted surface, the feed (fz) should be set to the lower recommended value shown in the above table.
- Cutting conditions may be limited depending on machine power, workpiece rigidity,and spindle output. When the cutting width, depth or overhang length is large,
set Vc and fz to the lower recommended values and check the machine power and vibration.
For more information about this product, visit our online e-catalog or download the product report: