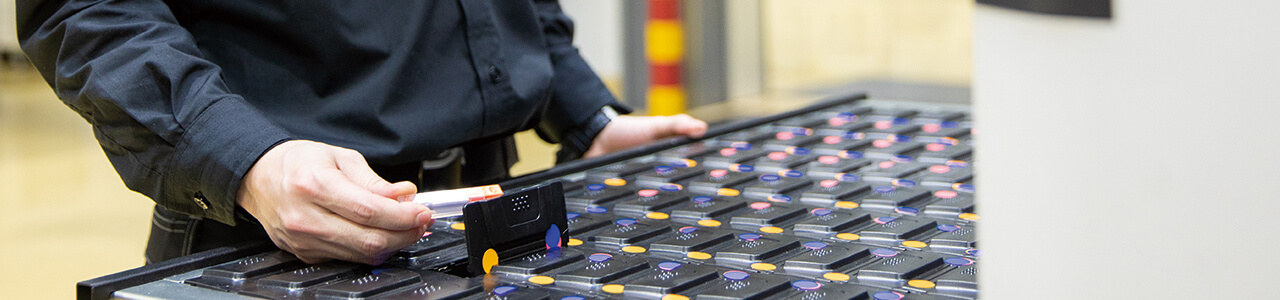
Tool costs reduced by 16.7%! Also contributes to training of human resources
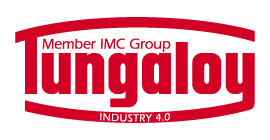
Before using MATRIX
Only 1 person handled inventory management of over 2,000 tools and devices. We often forgot to order necessary items and also found ourselves looking for missing tools. Furthermore, inventory discrepancies in our annual stock-taking amounted to millions of yen, which required extra days for recounting and adjusting. It was time to say goodbye to manual inventory management on our floor.
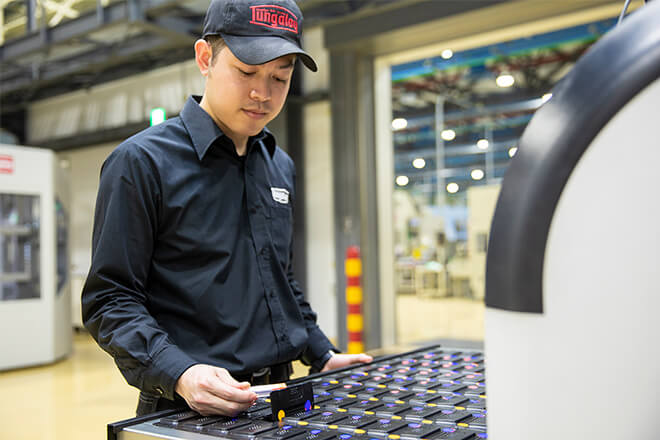
Benefits Brought by MATRIX
MATRIX helped us reduce 16.7% of our tool costs by eliminating the use of wrong tools for machining operations and stopping unnecessary orders for slow-moving items. MATRIX's analytical features also contributed to the development of our human resources on the production floor. There was a time when the total number of tools consumed in one production line amounted higher than another line that machined the same component. After reviewing the data from MATRIX, we learned that the difference in the tool usage came from the operators' skills and experiences. We quickly asked the high-skilled operator (who used less tools) to train the other operator for better tooling. The report that only took 1 minute to extract from MATRIX helped us improve our worker's machining skills, which added value to our production for many more years to come. MATRIX also reduced the problematic stock-taking discrepancies to 1/10 and reduced the time required for stock-taking by over 50%.
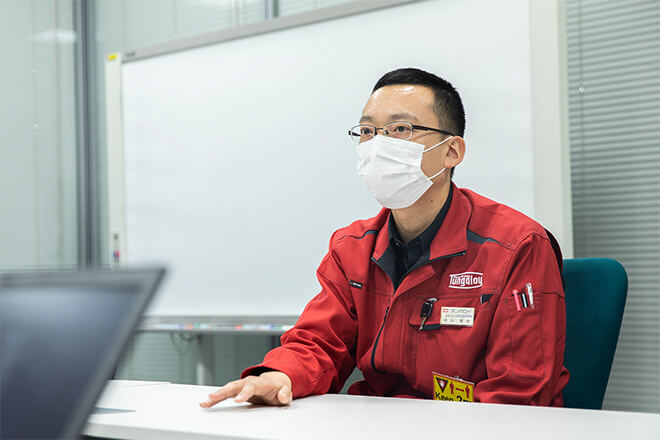
Our Unique Idea on Using MATRIX
We use MATRIX MAXI and DLS combined. We keep new tools in MAXI that has bins with lids, while we put used and reconditioned tools in DLS that have no lids. Since used tools are frequently taken in and out, we feel that the type without lids allow us to work more efficiently without a hassle.
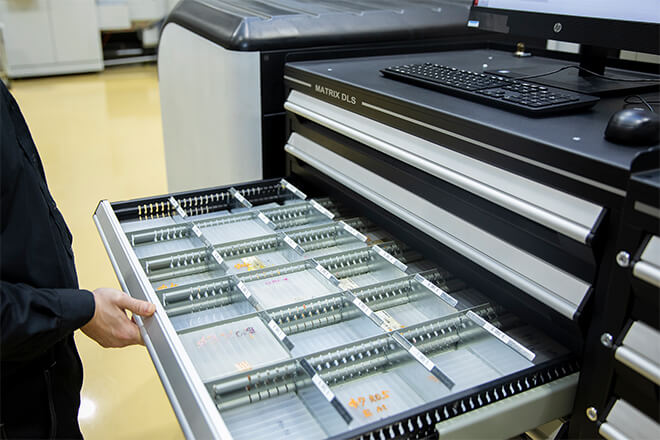