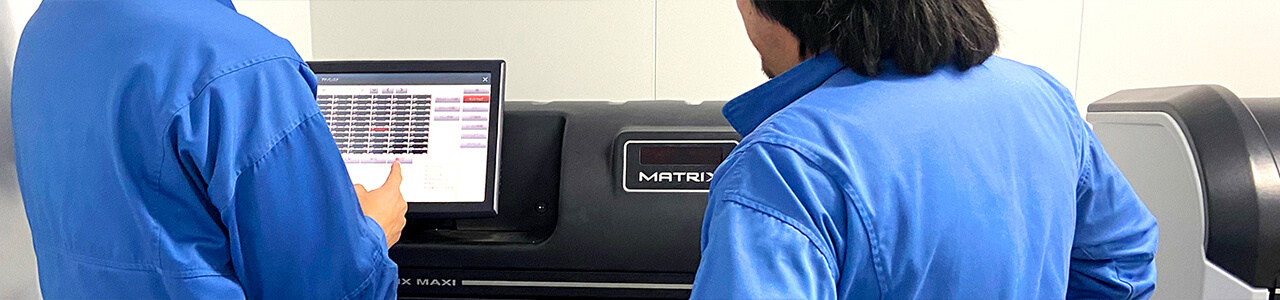
MATRIX encouraged us to take proactive initiatives for kaizen
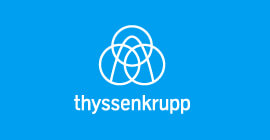
Before using MATRIX
Our tools were kept in traditional cabinets. When we take out a tool, we wrote down the quantity, date, and the user's name on the paper. Many times, the actual quantity didn't match the records because someone forgot to document it or wrote a wrong information. As for ordering, we set minimum stock level and asked our workers to place orders as needed, but they often forgot to contact the suppliers. We had no choice but to increase our inventory and reduce the frequency of our orders. Hoping to improve these situations, we started to consider installing MATRIX on our production floor.
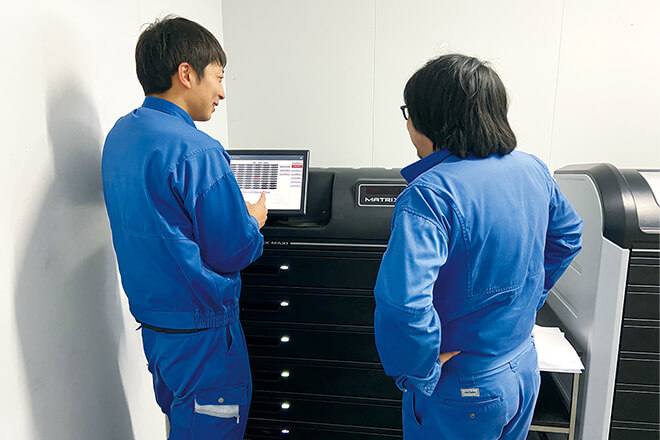
Benefits Brought by MATRIX
Now, anyone can easily take out the right tools, which greatly improved each person's workflow and significantly reduced the time spent on tool management. In addition, since we can check and analyze highly reliable, transparent data in real time, the awareness of tool management has increased throughout the company, and many employees proactively made efforts for "kaizen" (improvement).
Our internal communication has also accelerated, and we managed to reduce tool costs by eliminating shortages on our inventory as well as ordering unnecessary items. We are happy with the MATRIX's user-friendly, intuitive screen, which allowed us to start using it immediately without the need for extensive training. Its simple design is also popular among our employees as it fits in very well in our factory floor.
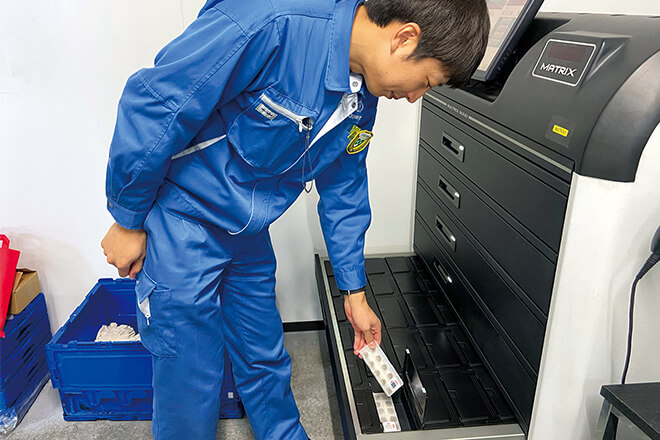
Our Unique Idea on Using MATRIX
Most workers use the search function to find the tools they need, so we put in-house names in the additional item code (where you can register a name different from the model number) to prevent mistakes during the issuing process. Also, as for toolholders, it's often hard to see the printed model number, so we prepared a separate document with the tool's model number, photo, and barcode. To take out a tool, we simply read this barcode with MATRIX.
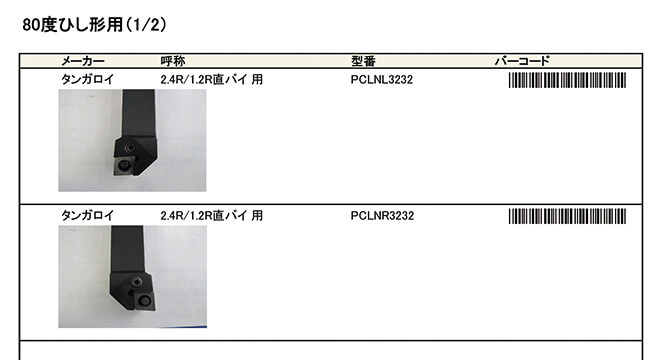