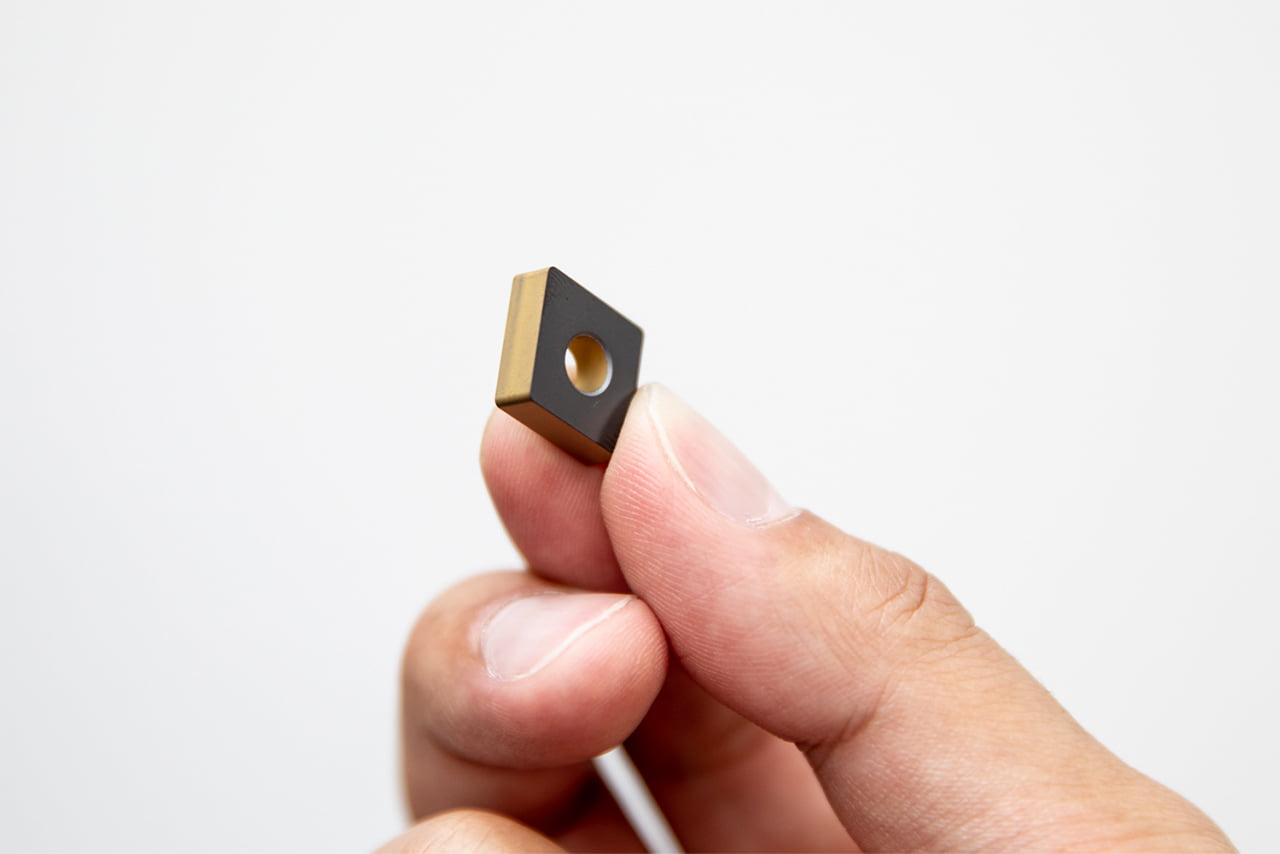
タンガロイ史上No.1を誇る
超厚膜CVD材種への挑戦
Members
-
技術本部材料開発部 CVD開発グループ
2015年入社 / 物理専攻 K・Iさん入社以来CVDコーティングに従事。これまでにない新しいコーティング材料の導入に挑戦してみたいと考えている。
-
マーケティング本部テックセンター
2016年入社 / 機械専攻 M・Aさんマシニングセンタのオペレーションを担当。開発試験やお客様のテスト加工などを行う。機械加工技能士2級の技術試験に向け勉強中。
-
生産本部生産技術部
2000年入社 / 物質系専攻 T・SさんPVD開発グループに9年ほど在籍した後、生産技術部に異動。PVDから始まり前後工程へと徐々に守備範囲を広げている。普段から新しい情報に目を光らせ、労力が少なく生産性の高い製造方法を模索している。
硬さと靭性。相反する性質をいかに両立するか
海外において特に重要視される高能率高速加工。同じ加工をするのであれば、1つの工具を1秒でも長く使い、1秒でも早く加工を終えることが価値につながる。つまりインサートのコーティングが担う役割は非常に大きいのだ。
そんな高能率高速加工を実現すべく立ち上げられたのが「高い耐摩耗性を備える鋳物用CVD材種の開発プロジェクト」である。
このプロジェクトの担当であるK・Iがまず取り掛かったのは、耐摩耗性のキーとなる膜厚の検討である。コーティングを厚膜にすればするほど耐摩耗性は高くなるが、その分耐欠損性が下がりインサートが欠けやすくなる。このバランスをどのようにとるのかが今回のプロジェクトの肝であり、最大の難所だった。
すぐに競合他社のデータを整理しつつベンチマークを設定、プロダクトグループのメンバーと相談しながら論理的に検討し、試作品の制作に取り掛かった。その試作品を基に、M.Aと共に複数の加工試験を行った。
その結果、ターゲットの性能を得るためには、従来のタンガロイ製品の膜厚を大きく上回る20μm以上の膜厚(従来の1.5倍)が必要であることが判明した。しかし、このような厚膜の切削工具は、非常に欠けやすく、実用上問題となることは明らであった。
ターゲット性能を得るためには、コーティングは薄くできない。厚いまま、欠損性を上げなければならない。そこでコーティング後の後処理を大幅に見直し、耐欠損性を向上させることにしたのである。アイデアはあったが、既存の処理設備では、そのアイデアを試すことができなかった。
相談を受けた生産技術部のT・Sは、「かなりハードルの高い開発だと思いましたね。」と笑う。耐摩耗性と耐欠損性という相反する性能を同時に叶える必要があるからだ。
K・Iのアイデアを実現すべく、T・Sは装置の仕様を検討した。これまでより精密かつ、強力な加工が必要となる。装置メーカーに相談しつつ、T・Sは装置の改造を実行した。新たに生まれ変わった後処理装置を使用し、K・IはT・Sと共に試作を重ね、ついに理想的な処理にこぎつけたのである。
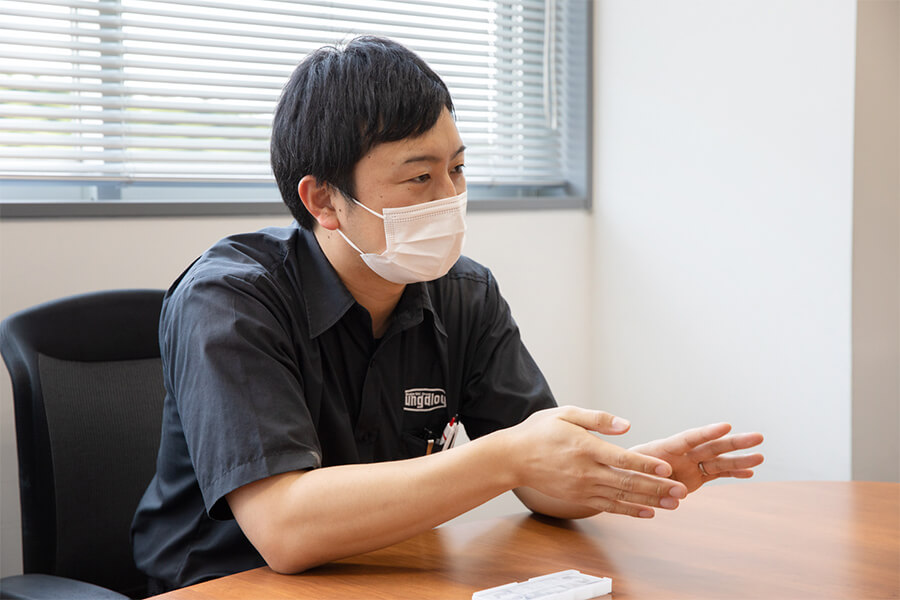
製品化への壁を超えろ
「すぐに狙いの性能は出ましたが、安定して製造できる条件を見つけ出すまでが大変でした」とK・Iは言う。
性能に影響するパラメーターは分かっていても、安定していなければ大量生産をすることはできない。そのためコーティングや後処理の条件を少しずつ変えながら、安定する製造条件を決めていく。この作業が非常に骨の折れるものであった。K・Iは数多くの試作を行い、その試作品をテックセンターに持ち込んだ。M・Aは、狙いの性能が得られているかを確認する加工試験を繰り返した。
試行錯誤はまだまだ続く。今回適用した後処理は、従来よりも威力の強いものだったため、インサート形状やサイズにより、インサートが処理中に動いてしまう、転んでしまうということが起きたのだ。これでは効果的な処理はできない。T・Sはインサートを乗せるトレーを見直すなど細かな改善を続けた。
さらにコスト面での障壁もあったという。
従来品よりも厚膜にするためには、コーティングにかける時間も延ばす必要がある。その分のコスト増加は、一度にコーティングできる工具の数を増やし、また製造プロセスを短縮し素材費を抑えた専用母材を開発することで調整した。
プロジェクト開始から2年。
数々の障壁を経て、タンガロイ史上最も厚い20μm以上のコーティング膜を採用した材種が誕生したのである。
完成したときの気持ちを教えてください
-
K・Iさん
かなり特徴的な材種であったので、不安でした。
社内試験では満足いく結果が得られても、実際にお客様が使用したときにどうなるかが分からないので。市場テストの時期がコロナ禍に重なってしまったこともあり、なかなか市場の声がいただけませんでした。
そんな中でもテストにご協力いただいたユーザーの皆様や、開発に協力いただいた皆様のおかげで何とか発売することができ、感謝しております。 -
T・Sさん
とりあえずは一区切りついてホッとしたというところでしょうか。
これからこの材種も様々な形状・サイズのインサートに展開していくことになりますから、今後も新インサートへの対応や効率改善などは継続する必要があります。 -
M・Aさん
新しく誕生する製品を試作の段階から加工に携われて、そして完成するというのは嬉しい気持ちとと遂にという待った気持ちがあります。
お互いのこんなところが良かった、という点を教えてください。
-
K・Iさん
開発にあたり無理難題を相談させていただきましたが、何事も前向きに検討していただいたことです。おかげ様で、新しい試みを達成することができました。ありがとうございます。
-
T・Sさん
私は途中からのプロジェクト参加でしたが、主担当である材料開発部のK・Iさんはプロジェクト開始よりテックセンターのM・Aさんと共に粘り強く様々な困難をクリアしてこられました。その分要求も多くなかなか諦めてくれませんが、時にアイデアを提案し、それがインサート飛散問題の解決の糸口になりました。今回一緒に仕事ができ、またそれが形となって嬉しく思います。
-
M・Aさん
K・IさんとT・Sさんには試験を円滑に行うため、念入りな準備と素早い対応をして頂きました。加工を行うにあたって、連携がしっかりととれることが重要なので、お二人には大変感謝しております。
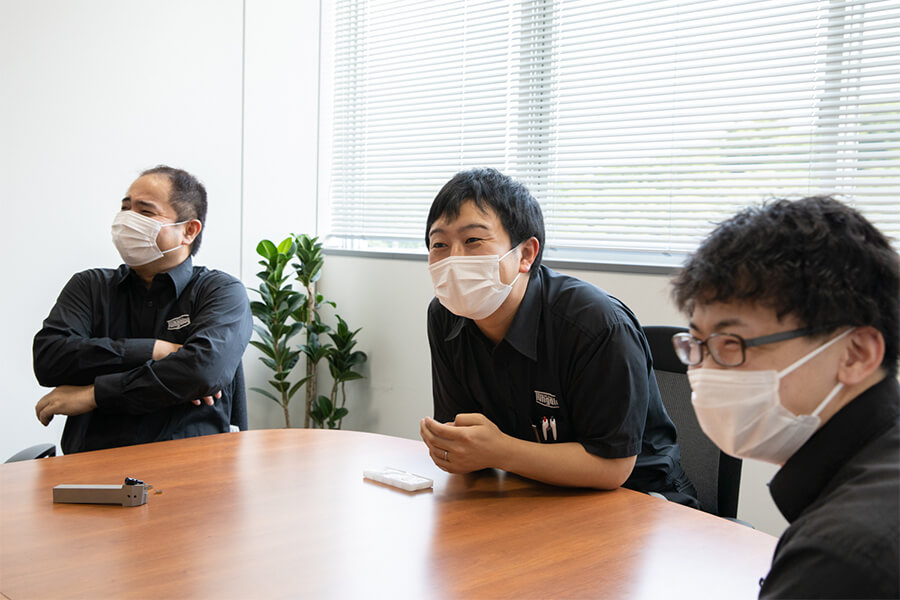