自動車や家電製品に使われている部品やそれらを製造する金型は、各種工作機械による加工でつくられています。工作機械による加工で最も代表的な手法は鋼や合金からなる工具で材料を切ったり、削ったり、穴を開けたりする切削加工です。この連載では全12回に渡って、加工に携わる若手技能者・技術者が、切削加工と工具に関する基礎知識を学べるように情報を整理しています。
各回とも加工とそれに用いられる切削工具に関する基礎について、平易な言葉と図を用いてわかりやすく説明するので、切削加工と工具の基礎知識を習得するきっかけとして役立ててください。また、後輩を持ち、指導する立場の中堅技術・技能者は自らの知識を確認するときに役立てていただければ幸いです。基礎・基本に立ち返ることで思わぬ新たな発見につながることもあります。切削加工の深さや面白さ、そこで得た気づき、ノウハウも若手に伝えていただければ、筆者としてこれに勝る喜びはありません。
切削加工とその方法
さて、まず具体的な話に入る前に「切削」という言葉の意味を少し考えてみましょう。切削とは「切る」(連結・結合しているものを刃物などで切り離す)、「削る」(少しずつ削いで取る、薄く削ぎ取る)の2つが合わさった言葉で、切り削ることを言います。身近なものでたとえると、リンゴの皮むきがイメージしやすいでしょう。包丁を用い、皮をそぎ形にしていく。これは切削加工と同様の作業です。ただ、リンゴは柔らかく、手で作業することができますが、金属は硬く手作業ができないため、工作機械を用いて切削加工が行われます。つまり、工業製品をつくる際の切削加工は金属・樹脂などの素材を硬い工具を用いて切削し、形にすることです(図1)。
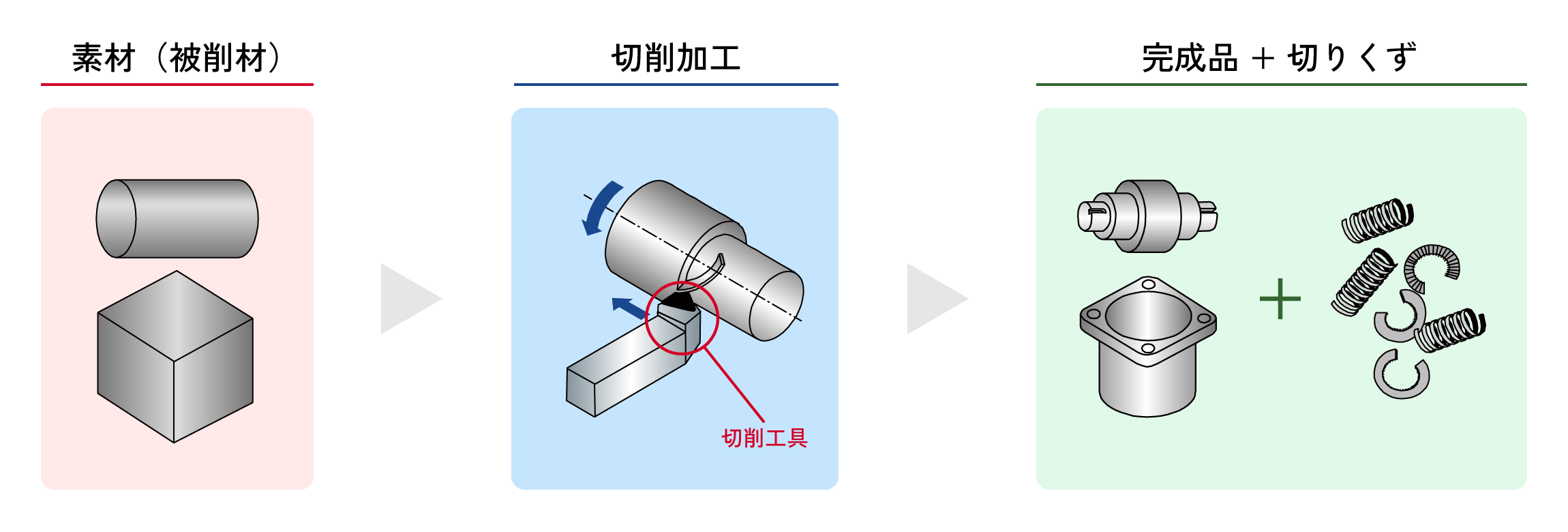
切削加工の主な形式は、下記の3つの加工方法となります。
-
旋削加工
旋削加工は材料(被削材)を回転させ、切削工具を移動することで切削する加工です(図2)。
使用する機械は、汎用旋盤やNC旋盤、自動盤などがあります。図2 旋盤加工の原理と汎用旋盤 -
転削加工
転削加工は材料(被削材)を固定し、切削工具を回転して移動することで切削する加工です(図3)。
使用する機械は、汎用フライス盤やマシニングセンタなどがあります。図3 フライスと溝入れ加工のイメージとそれらを行えるマシニングセンタ -
穴あけ加工
切削工具を回転して加工する場合と材料(被削材)が回転して加工する場合の両方があります(図4)。
使用する機械は、NC旋盤やマシニングセンタなどがあります。加工の目的により、工作機械や切削工具、加工形式を使いわけ、製品をつくり上げます。図4 穴あけ加工
被削材の種類
切削加工する金属材料を、削られる材料という意味から「被削材」と呼びます。また、加工対象物を表す言葉で「ワーク」とも呼びます。被削材は、P(鋼)やM(ステンレス)、K(鋳鉄)、N(非鉄金属)、S(難削材)、H(高硬度材)の6種類に分類(ISO513による)されており、切削加工に使用する工具材種は、どの被削材に適応できるかをこの6種類の分類記号でカタログなどに表記しています。表1に分類記号と代表的な被削材料をまとめました。
表は横にスクロールしてご確認いただけます分類記号 | 被削材 | 代表的な材種 | 適用部品 |
---|---|---|---|
|
低炭素鋼 | SS400 S15C |
一般機械部品、製函部品、鋼管 |
炭素鋼 | SS45C S55C |
一般機械部品 | |
合金鋼 | SCr440 SCM440 |
一般機械部品、タービンハウジング | |
ダイス鋼 | SKDKD11 SKD61 |
金型 | |
|
ステンレス | SUSSUS304 SUS316 SUS630 |
高強度、耐食・耐熱性が必要な機械構造用部品、タービンブレード、ポンプ、シャフト、ノズル |
|
鋳鉄 | FC250 FCD600 |
自動車部品,デフケース,ディーゼル用エンジンブロック・ヘッド、ブレーキディスク,工作機械ベッド |
|
アルミニウム 銅合金 |
ADC12 AC4B-T6 A7075 |
シリンダーブロック・ヘッド,ミッションケース,バルブボディー、航空機部品 |
|
チタン インコネル |
Ti-6Al-4V Inconel718 |
航空機部品、ジェットエンジン燃焼室部品、発電用タービンブレード、人口関節 |
|
焼き入れ鋼 | 硬度 40HRC~ |
金型、自動車部品、シャフト、切削工具ボディ |
工具材種に求められる特性
切削加工では、被削材を削る際に切りくずが生成され、切りくずと工具接触面との摩擦により、工具刃先は高温かつ大きな負荷が掛かります。また、被削材中の硬質粒子により、工具の刃先は徐々に擦られ摩耗が進行していきます。工具材種に求められる特性は下記の4つです。
-
高硬度であること
被削材中の硬質粒子による摩耗を抑えるため硬度が必要です。一般的に工具の硬さは被削材硬さの約4倍が必要とされています。
-
高温硬度が高いこと
切削加工中に発生する切削温度は、炭素鋼などで700℃~1,000℃になります。材種は高温になればなるほど、軟化しますが軟化した材種は摩耗の進行が早まるため、高温でも硬度を保つことのできる材種が必要です。
-
高じん性であること
切削加工中に工具刃先に生じる負荷に耐えうる。
粘り強さ(じん性)を持った材種が必要です。じん性の低い材種は、切削加工中の負荷により、欠けてしまいます。じん性の指標として抗折力が用いられ、数値が大きいほど欠け難い材種を意味します。 -
化学的に安定していること
切りくずが工具表面を擦過する際、摩擦により高温となり、化学反応を起こし損傷が進行します。この化学反応を抑えることのできる材種が必要です。
代表的な工具材種とその特徴
現在、切削工具で使われる代表的な材種について説明します。図5は、各材種のじん性と硬さの相関図です。
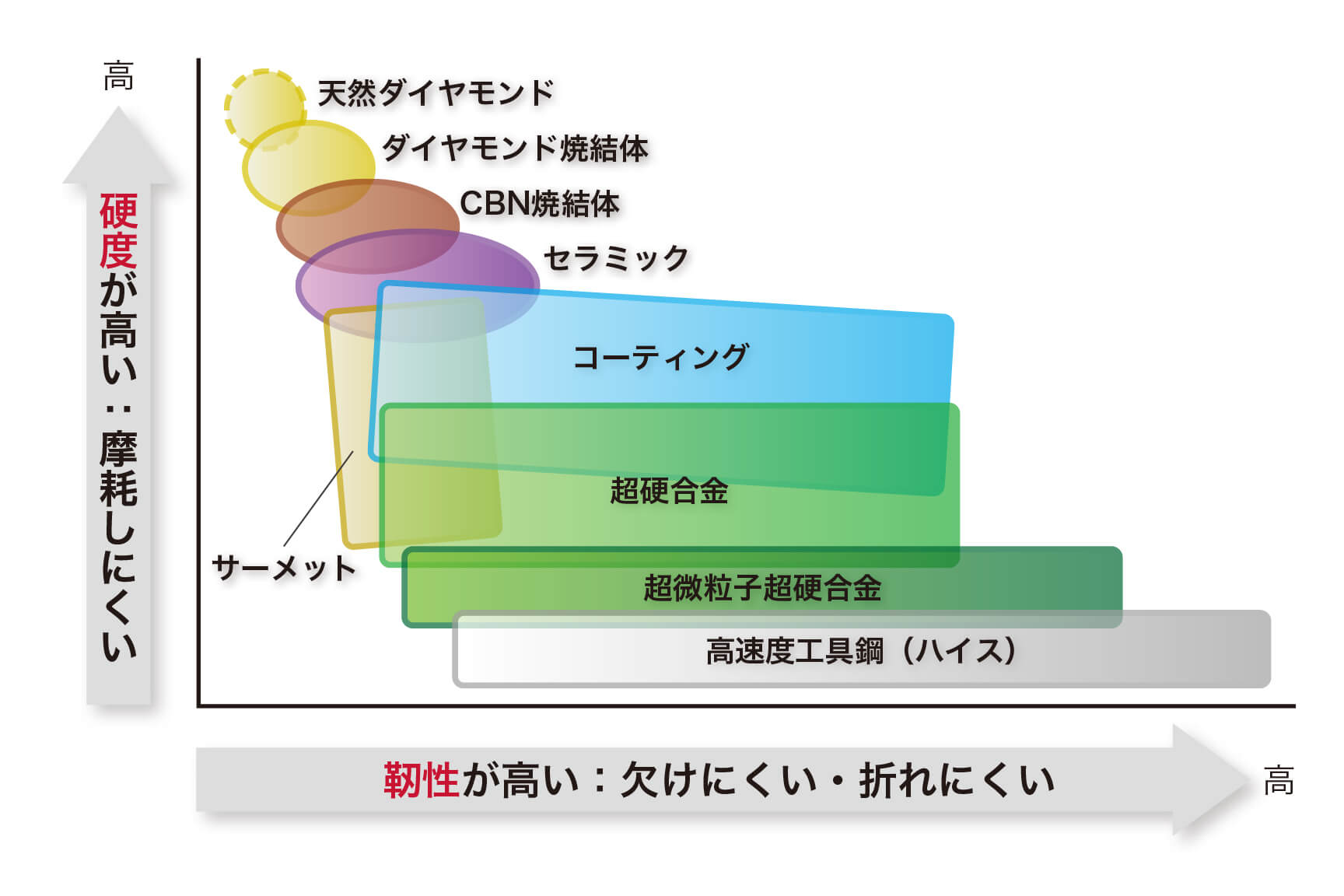
-
高速度鋼
高速度鋼はHigh Speed Steelの頭文字をとり、HSS(ハイス)と呼ばれています。じん性が高く、欠けや折れに強いため、ドリルやエンドミル、タップに使われます。図6は高温硬さを示しますが、600℃付近で硬度が低下するため、使われる切削速度域はVc=10m/min程度であり、切削温度の上がる高速切削には不向きです。
図6 高温硬さの比較 -
超硬合金
超硬合金は現在、切削工具に使用されている基本材種です。炭化タングステン(WC)を主成分とし結合剤のコバルト(Co)を配合した材料です。高温硬さがあり、シャープエッジが必要な非鉄金属用の工具やコーティング材種の母材に使われます。
-
超微粒子超硬合金
超硬合金と主成分は同じですが、WCの粒径が超硬合金は1~3μmに対し、超微粒子超硬合金は、1μm以下のものを使用しています(図7)。同じ硬さで比較すると、超微粒子の方がじん性は高く、欠けにくく折れにくい特性を持ち、刃立ち性にも優れます。仕上げ加工で使用されるエンドミルやドリルに使われます。
図7 組織写真 -
コーティング材種
コーティング材種は超硬合金に硬質の物質を被覆した材種です。現在の切削加工で最も多く使用されています。超硬合金より硬い物質を被覆することで、被削材中の硬質粒子による摩耗を抑えます。また、鋼材との親和性が低いので、化学反応による摩耗にも優れています。旋削、転削、穴あけで使用される工具に広く使われます。
-
サーメット
サーメットは炭化チタン(TiC)や窒化チタン(TiN)を主成分とした材種です。超硬合金より硬く、高速域で切削加工が行えます。また、鋼材との親和性が低いため、切れ刃に切りくずが付きにくく、良好な仕上げ面が得られる特徴があります(図8)。
図8 加工面粗さの比較 -
セラミック
セラミックは酸化アルミニウム(Al2O3)や窒化ケイ素(Si3N4)を主成分とした材種です。超硬やサーメットに比べ高温での硬さに優れ、より高速域での加工が可能です。主に鋳鉄や高硬度材、難削材の加工に適しており、旋削工具と転削工具に使われます。
-
cBN焼結体
cBN焼結体は粉体の立方晶窒化ホウ素(cBN)を超高圧で焼結・固体化した材種です。ダイヤモンドに次ぐ硬さを持ち、鉄系材料との反応性が低い特徴があります。高温での硬さもほかの材種より高いため、鋳鉄や高硬度材、焼結金属などの高速域での加工に適しており、主に旋削工具に使用されます。
-
ダイヤモンド焼結体
ダイヤモンド焼結体は最も硬い工具材種です。しかし、700℃辺りから黒鉛化が始まり、極端に硬度は軟化してしまうため、切削温度の上がる鉄系金属の切削には適しません。主にアルミや銅合金など非鉄金属の加工に使われます。
工具材種は、相反するじん性と硬さを併せ持つことが理想です。中でもコーティング材種は、バランスの取れた材種であり、現在最も使用されている材種のゆえんとも言えます。
超硬合金の製造プロセスとコーティング方法
これまで説明しているコーティング材種は、超硬を母材とする超硬コーティング材種を指します。超硬合金の製法とコーティング方法について説明します。
図9は超硬合金の製造プロセスをまとめたものです。この製法は、粉末冶金法と言います。主成分のWCと結合材のCo、材種によっては複合炭化物の粉末を配合させ混合粉砕します。WCやCo、複合炭化物の配分量を変えることで、硬さやじん性、耐熱性など特性の異なった超硬合金をつくることができます。
乾燥造粒工程でパウダー状にした後、高圧プレス機にて成形させます。この時点ではまだ、硬度を持っておらず、手で簡単に割ることができます。約1,500℃で焼結することで、融点の低いCoは溶け始めWCの結合材となり、冷めた後、ここで硬度を持った超硬合金となります。
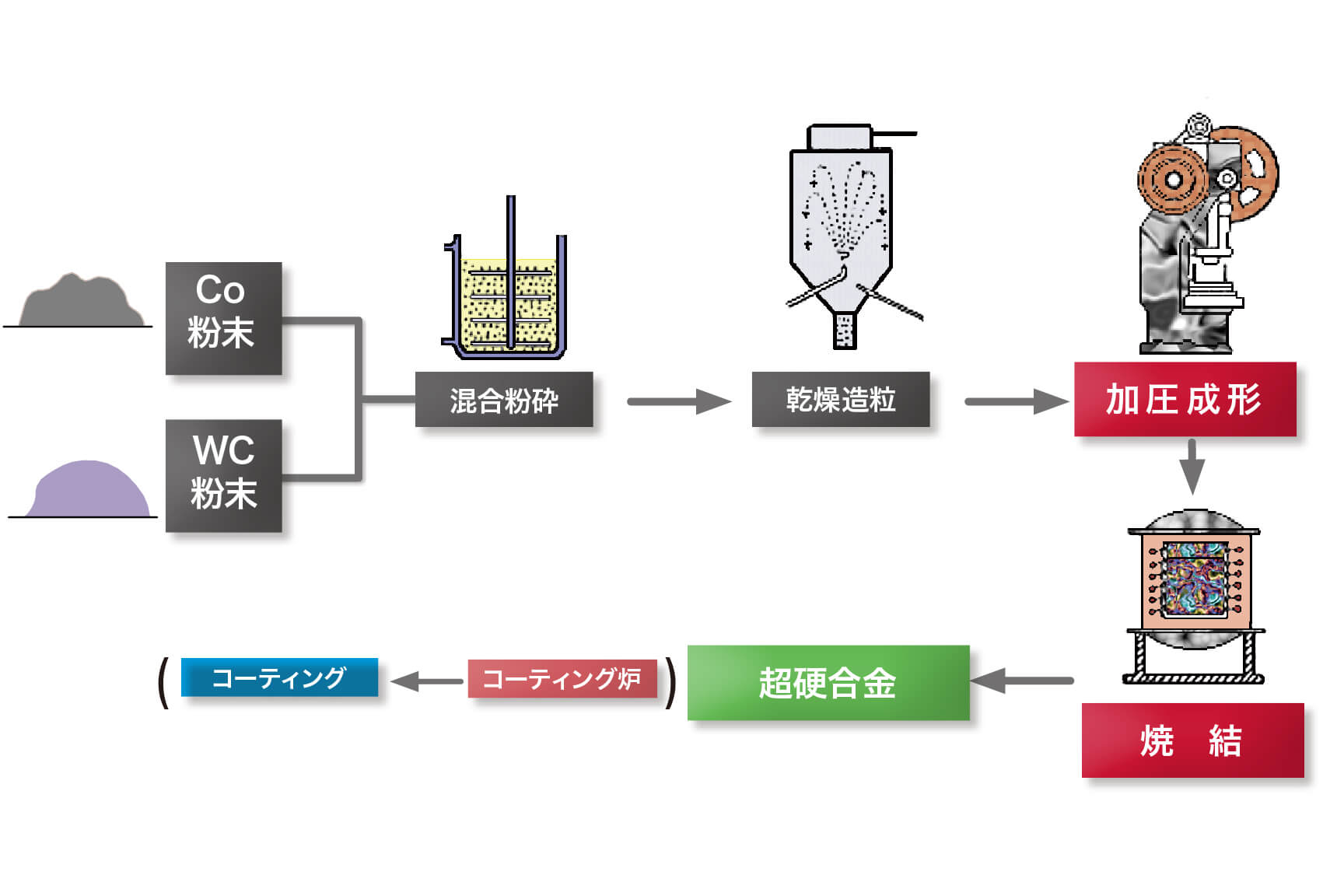
コーティングには、CVDとPVDの2つの製造方法があります。
-
CVD(化学的気相蒸着)
CVD(図10)は化学的気相蒸着のことで、加熱炉の中にガスを流し、化学反応により硬質物質を蒸着させる方法です。加熱炉内は約1,000℃まで上昇し、各種ガスを流すことで特性の異なった膜を多層に蒸着させることができます。代表的なコーティング層としてアルミナ(Al2O3)、窒化チタン(TiN)、炭窒化チタン(TiCN)、炭化チタン(TiC)などがあります。
図10 CVDの仕組み -
PVD(物理的気相蒸着)
VD(図11)は物理的気相蒸着とも言い、硬質物質をイオン化(+)して、電気的に母材(-)へ飛ばして蒸着させる方法です。PVD炉内は約500℃であり、CVDに比べ低温で被覆工程が行われます。代表的なコーティング層は、TiNやTiCN、現在は窒化チタンアルミ((Ti、Al)N)が主流です。表2にCVDとPVDの特徴をまとめました。
図11 PVDの仕組み
評価項目 | CVD | PVD | 特性 |
---|---|---|---|
膜と母材の密着性 | 高い | 低い | 密着性が高いと膜の剥離が少なく、耐摩耗性に優れる |
コーティング膜厚 | 一般的に厚い 15μm前後 |
一般に薄い 3μm前後 |
膜厚が厚いほど、耐摩耗性に優れる |
鋭角部へのコーティング | 困難 | 可能 | シャープエッジに適する 仕上げ用工具にも適用できる |
膜中の残留応力 | 引っ張り残留応力 | 圧縮残留応力 | 引っ張り残留応力:耐欠損性に劣る 圧縮残留応力:耐欠損性に優れる |
今回は切削加工の基礎と切削工具材種について解説しました。次回は旋削加工と工具について説明します。